Common problems, causes and solutions of PVC production and processing (summary)
Common problems, causes and solutions of PVC production and processing (summary)(1) Common problems, causes and solutions of pipes
Common problems Possible cause Solution
There are lumps in the tube wall (like bubbles). The moisture of the material is too high. Properly increase the mixing temperature and extend the mixing time
Impurities mixed in materials Check the source of impurities and remove impurities
Poor plasticization Appropriately reduce external lubricant and increase plasticization
The inner wall of the pipe is rough, and the plasticization is poor.
The inner wall of the pipe has irregular depressions. There are impurities in the material. Check the source of the impurities and remove the impurities
Poor plasticization Appropriately reduce external lubricant and increase plasticization
The surface of the tube wall is matte, half of the light is bright, and half of the dark is poor.
The particle size of CaCO3 is too large or too wide. Replace the appropriate calcium carbonate
Precipitates stick to the inner wall of the die Remove the precipitates and improve the formula
The external lubricant content is too low. While ensuring plasticization, increase the external lubricant appropriately
Uneven thickness of tube wall Poor uniformity of plasticizing Adjust the formula to improve the uniformity of plasticizing
Partial decomposition of materials
Black streaks or color points on the surface of the pipe Carbon black, uneven dispersion of pigments and stabilizers Improve the mixing process and improve the dispersibility
Poor fluidity Improve the formula and increase the amount of internal and external lubricants
The surface of the pipe is discolored or has coke particles. The stability of the material is insufficient. Replace the PVC or the stabilizer and increase the amount of stabilizer.
Material shear friction is too large Increase the amount of internal and external lubricants
There are small pores in the cross section of the pipe. There are volatiles in the formula. Adjust the formula to remove the volatile raw materials.
Insufficient material stability Replace PVC or stabilizer, increase stabilizer dosage
The friction between the material and the equipment is too large Increase the amount of external lubricant
The pipe is too soft, excessive plasticization, adjust the proportion of lubricant, increase the amount of external lubricant
Excessive dosage of impact modifier Reduce impact modifier
The pipe is brittle or broken. Poor plasticization. Reduce the amount of external lubricant and increase the plasticization.
Impurities mixed in materials Check the source of impurities and remove impurities
Poor uniformity of plasticization Adjust the formula to improve the uniformity of plasticization
1. The color of the extruded product is yellow
problem analysis:
The yellowing of the pipe is caused by the decomposition of PVC. When PVC decomposes, a dehydrochlorination reaction occurs to form a conjugated polyolefin series, which is yellow. The decomposition of PVC is mostly due to many reasons such as formula, process or equipment.
1. Equipment problem (suddenly turns yellow)
(1) Check whether the thermocouples in each area of the barrel are working properly and the fans in each area are operating normally. If there is a problem with the thermocouple or fan, it will cause the overheating of the screw barrel and cause the product to yellow.
(2) Check whether the heat transfer oil of the screw is sufficient, whether the oil pump is working properly, and whether the oil pipe is blocked. If the oil passage is blocked, the friction heat of the screw cannot be effectively discharged, which will cause the material to decompose and turn yellow due to overheating of the screw.
(3) Check and adjust the screw clearance or replace the screw. In the case of serious screw wear, the gap between the screw and the barrel becomes larger, and the screw's ability to push the material becomes worse, which will cause the material to return in the barrel, so the heating time of the material inside the barrel will become longer, resulting in yellowing . (This situation is generally manifested in equipment where the screw is used for a long time, the feed ratio is slightly increased, and the feed port is fed.)
(4) Check the mixing device, whether the mixing time is normal, whether the cooling water circulation is normal, and whether the cooling water temperature is normal. If the hot mixing time is too long or the cold mixing cannot cool the material to the normal temperature, the material will consume the stabilizer in the formula during the mixing or storage process. When used, the effectiveness of the stabilizer will be reduced, resulting in yellowing of the product during the production process.
Second, the process problem (generally yellowing after a certain start-up), PVC is heated and sheared by the screw and the barrel during the extrusion process. Improper process settings will cause PVC decomposition to a certain extent.
If you want to know more about it please do not hesitate to
contact me. WhatsApp:+86-15966835076.
(1) Appropriately lowering the temperature of the barrel can improve the yellowing phenomenon.
(2) Reduce the rotation speed of the host within an appropriate range and increase the feeding ratio, which can reduce the shear, and make the material in the screw groove more uniformly mixed, the stabilizer fully exerts its effect, thereby reducing yellowing.
(3) Improper startup method will also cause the product to turn yellow. Restarting may solve this problem.
Third, the formula problem
It usually appears after the batch or manufacturer of a certain auxiliary agent is changed. Generally adjust the formula according to the actual situation from the following aspects.
(1) Increase the content of stabilizer.
(2) Adjust the balance of internal and external lubricants.
(3) Solve yellowing by complementing pigments or increasing the proportion of fluorescent whitening agent.
2. Air bubbles appear on the cross section of the product, and the inner wall is not smooth.
Bubbles appearing on the cross-section of the product are due to the evaporation of moisture and small molecules during processing. There are generally the following solutions:
(1) Ensure that the raw materials are dry and free of moisture.
(2) Check whether the vacuum pump is malfunctioning and whether the vacuum pipeline is blocked.
(3) Increase the ratio of stabilizer or lubrication content, depending on the specific situation.
(4) Increase the temperature in the first and second zones, lower the three and four zones, and reduce the speed of the host.
3. The surface of the product is rough, with protrusions or bubbles.
(1) There is too much water in the material, and the material is stirred back and dried again.
(2) The temperature in the third and fourth regions is too high, and excessive plasticization is not conducive to the vacuum removal of water and small molecular substances, and the temperature in the third and fourth regions is appropriately lowered.
(3) The melt strength is not enough, appropriately reduce the extrusion speed or increase the ACR ratio.
4. Poor gloss of products.
(1) The plasticization of the material is not good, and the processing temperature and the speed of the host are appropriately increased.
(2) The temperature of the die is too high or too low, the inner wall of the die is not smooth, and it is adjusted according to the actual situation.
(3) There are precipitates on the mold, the vacuum airway of the mold is blocked, and other reasons should be cleaned and dredged in time.
(4) Insufficient external slip in the formula. Appropriately increase the external slip, but too much increase may delay plasticization, and precipitation will seriously block the die.
(5) The combination of ultramarine and fluorescent brightener in the formula is reasonable.
(6) Choose good quality stabilizer and calcium powder.
5. There are yellow or black lines on the surface of the product
(1) The black line is mostly due to the decomposition of the material due to the excessive friction between the extruder screw and the barrel. Usually the axial gap between the screw and the screw is too small or the coaxial gap between the screw and the barrel is not uniform. Check the adjustment screw fit.
(2) The yellow line is the decomposed material brought out by the dead corner of the die or confluence core. Check the die and confluence core.
The above two problems can also obtain a certain effect by adjusting the lubrication and stabilizer.
6. Black spots on the surface of the product
(1) There are impurities in the material, check whether there are impurities in the raw materials.
(2) There is stagnation in the vacuum port. Check and clean up.
(3) Check whether there is any material with longer adhesion time on the inner wall of the hot mixing pot.
(2) Common problems, causes and solutions of plates
Common problems Possible cause Solution
Uneven surface, rough, poor gloss, poor plasticization, reduce the amount of external lubricant, increase plasticization
The raw material moisture is too high. Properly increase the mixing temperature and extend the mixing time.
Impurities mixed in materials Check the source of impurities and remove impurities
There are scratches on the surface There are foreign objects in the die Remove the foreign objects
The surface becomes yellowish or there are char particles. The stability of the material is insufficient. Replace the PVC or the stabilizer and increase the amount of stabilizer.
Material shear friction is too large Increase the amount of internal and external lubricants
There are precipitates on the surface of matt sticks. Clean the roller and adjust the formula to reduce the precipitates.
Decomposition products remain in the machine head
There are bubbles on the surface. The content of moisture or volatiles in the material is large. Fully dry or reduce the amount of low melting point lubricant
The viscosity of the melt is too high. Improve the formula and increase the amount of internal and external lubricants
The head material is too large, the amount of foaming agent is too large, reduce the amount of foaming agent appropriately
The apparent density is too high, the material is not foaming well, adjust the formula or increase the amount of foaming agent
Partially brittle or broken, poor plasticization, reduce the amount of external lubricant, increase plasticization
Impurities mixed in materials Check the source of impurities and remove impurities
Poor uniformity of plasticization Adjust the formula to improve the uniformity of plasticization
(3) Common problems, causes and solutions of injection molding
Common problems Possible cause Solution
Insufficient injection, insufficient product Poor raw material flowability Adjust the formula to improve the flowability
Poor plasticization Appropriately reduce external lubricant and increase plasticization
There are impurities at the nozzle or runner. Clean the die and check to remove impurities
Decomposition at the nozzle or runner is blocked. Clean the die, replace the stabilizer or increase its dosage
Lack of material Adjust the feeding amount and increase the feeding amount appropriately
Overflow, flash material flow is too good Adjust the formula to reduce the fluidity
Too much feeding amount Adjust the feeding amount and reduce the feeding amount appropriately
There are bubbles and voids. The content of moisture or volatiles in the material is large. Fully dry or reduce the amount of low melting point lubricant
The viscosity of the melt is too high. Improve the formula and increase the amount of internal and external lubricants
Partial depression caused by shrinkage Insufficient fluidity of the material Improve the formula and increase the amount of internal and external lubricants
Poor plasticization Appropriate reduction of external lubricant to enhance plasticization
Insufficient feeding amount Adjust the feeding amount and increase the feeding amount appropriately
There is peeling phenomenon Poor plasticization Appropriate reduction of external lubricant to enhance plasticization
Too much lubricant
There are cold spots, poor plasticization, appropriate reduction of external lubricant, enhance plasticization
The surface is rough and the gloss is poor. The material has insufficient fluidity. Improve the formula and increase the amount of internal and external lubricants.
Poor plasticization Appropriate reduction of external lubricant to enhance plasticization
There is more incorporation of regrind to reduce the amount of regrind added
There are small pores on the surface, that is, silver spots. The content of moisture or volatiles in the material is large. Fully dry or reduce the amount of low melting point lubricant
Insufficient material flowability Improve the formula and increase the amount of internal and external lubricants
There is more incorporation of regrind to reduce the amount of regrind added
The product has cracks. The material has insufficient fluidity. Improve the formula and increase the amount of internal and external lubricants.
Poor plasticization Appropriate reduction of external lubricant to enhance plasticization
There are focal spots, yellowing and black lines. The thermal stability of the material is insufficient. Replace the PVC or stabilizer and increase the amount of stabilizer.
Insufficient material flowability Improve the formula and increase the amount of internal and external lubricants
The plasticization of the material is too fast Adjust the proportion of lubricant and increase the amount of external lubricant
Welding marks are obvious. The content of moisture or volatiles in the material is large. Fully dry or reduce the amount of low melting point lubricant.
Too much lubricant
Poor plasticization Appropriate reduction of external lubricant to enhance plasticization
Flash
(1) The mold is not tightly sealed. The mold should be repaired.
(2) The cooling rate is too slow. The cooling efficiency should be improved and the cooling speed should be increased. It is better to pass cooling water to the bottom mold for better cooling effect.
(3) Too much injection volume and feed. Should be appropriately reduced.
(4) Improper coordination of plasticizing time and injection pressure. After measuring the relationship curve between pressure and foaming time, adjust the injection pressure and foaming time reasonably.
(5) Warping deformation of the inner liner of the mold. The inner liner should be repaired or replaced.
(6) The leakage of hydraulic system causes insufficient clamping force. The hydraulic system should be repaired.
(7) The spring on the pin mold hook is too loose. The spring should be replaced to increase the pulling force of the hook.
(8) The setting time is not enough, the surface layer of the product has not been fully penetrated, and the hot material in the middle broke through the surface layer and overflowed during the first mold opening. The first mold opening time should be properly extended.
Blisters
(1) The particle size of the blowing agent is too coarse, and the dispersion is uneven. Generally, the foaming agent needs to be grinded by three rollers, and it is grinded in the barrel for 2 to 4 times, which is used after grinding.
(2) The processing temperature during kneading and granulation is too high, the foaming agent decomposes prematurely, and the particles have a foaming phenomenon. The temperature of kneading and granulation should be properly reduced, and the extruded particles should not have small bubbles when cut.
(3) The residence time of the melt in the barrel is too long or the processing temperature is too high. Rapid pre-molding should be used, the plasticized melt should be injected at one time, and one machine and multi-mode production should be used as much as possible.
(4) The back pressure of the screw is too small, and the molten material expands by heating in the barrel. The back pressure should be increased so that the foaming agent contained in the melt will not undergo pre-expansion after thermal decomposition.
(5) The material at the end of the barrel leaks, forming a low-pressure area at the outlet of the end, causing the melt to expand at the outlet to form bubbles. The temperature of the discharge port should be properly reduced, and it is best to use a throttle valve structure at the discharge port to seal the end outlet.
(6) Improper reuse ratio of recycled materials. The amount should be reduced appropriately.
Foaming ratio is too large
(1) The amount of foaming agent is too much, which leads to excessive gas generation. The amount of gas generated should be measured and the material should be accurately fed.
(2) Too much plasticizer. Should be appropriately reduced.
(3) The starting temperature is too high. The mold should be cooled down.
(4) The holding time is too short. It should be ensured that the product is completely shaped and released from the mold.
Insufficient expansion ratio
(1) The amount of blowing agent is too small, resulting in insufficient gas generation. The amount of gas generated should be measured and the material should be accurately fed.
(2) Too little plasticizer. The amount of feed should be increased appropriately.
(3) When the product is processed for the second time, the second expansion time is too short. The cooking foaming time during processing should be properly extended, and the time interval between the first and second foaming cannot exceed 12 hours.
(4) When the surface of the product has a paint-baking pattern, it indicates that the first mold expansion and foaming is too slow. The first mold opening time should be shortened appropriately.
(5) When small bubbles bulge on the surface of the product, it indicates that the injection temperature is too low. The injection temperature should be increased appropriately. However, if foaming does not occur even after the molding temperature is increased, the first mold opening time should be further shortened.
Uneven pore size
(1) The particle size of the foaming agent is inconsistent and the dispersion is not good. The foaming agent should be used after grinding.
(2) If the injection pressure is too low or the injection speed is too slow, the melt will expand during the filling process, forming cells of different sizes. The injection speed should be properly accelerated to increase the injection pressure.
(3) The molding temperature is too high. Should be properly reduced.
(4) Too much material remains in the barrel. Should try to reduce the stock through a multi-cavity and other methods.
(5) The back pressure of the screw is insufficient. Should be appropriately improved.
Solid depression
(1) The product is too thin, and the molten material is subject to a large flow resistance when filling the mold, resulting in insufficient pressure in some parts and insufficient filling. The thickness of the product should be designed reasonably. Generally, the unfoamed thickness is above 6mm, and the thickness should be as uniform as possible.
(2) The cooling is uneven, and some parts cool too quickly, making foaming difficult. The product should be cooled uniformly, and the cooling system of the mold must be set reasonably according to the physical characteristics of the product.
Gate depression
(1) The gate section size is too large. Should be appropriately reduced.
(2) The pressure holding time is too short, and the mold release is too fast. The pressure holding time should be properly extended.
(3) The molding temperature is too high or too low. Should be adjusted appropriately.
(4) The hydraulic system of the molding machine fails and the injection pressure is insufficient. The hydraulic system should be repaired to increase the injection pressure.
Flow mark
(1) The molding temperature is too low or the temperature difference between the heating areas is too large. Should appropriately increase the molding temperature, and adjust the heating temperature of each part.
(2) The injection speed is too slow. Should be properly accelerated.
(3) Insufficient supply. The amount of feed should be increased appropriately.
Poor gloss
(1) The viscosity of the resin is too high, and the absorption of the plasticizer is uneven. Resin should be used reasonably.
(2) Bubbles shrink to form uneven pitted surface. The cause of the large bubble should be detected and the fault of the large bubble should be eliminated.
(3) The mold temperature is too low. The molding temperature should be appropriately increased.
(4) The surface finish of the mold cavity is poor or corroded. The surface finish of the mold should be improved.
(5) There are residues on the surface of the mold cavity. The mold cavity should be cleaned.
(6) Because the foaming agent on the surface of the molten material decomposes and foams during the filling process, some cells are torn during the flow process, forming a paint-baking pattern and affecting the gloss of the product surface. For this, auxiliary methods such as color spraying and glazing can be used to improve the surface light Ze.
Uneven color
(1) The color is not accurate. It should be accurately weighed.
(2) The color material is unevenly dispersed. A grinder should be used to grind and squeeze the color.
(3) The color quality is poor, the color is volatile, and the coloring power is not strong. Pigments with better coloring properties should be used.
(4) The local plasticization temperature is too high, causing discoloration. Check the heating system and reduce the local temperature.
(5) The surface has lacquer-like patterns, forming color difference. The first mold opening time should be shortened appropriately.
Raw material
(1) The molding temperature is not enough and the plasticization is poor. The heating system should be checked to increase the molding temperature.
(2) The raw material formula is unreasonable. The formula should be adjusted.
Layered
(1) Too much foaming agent. Should be appropriately reduced.
(2) The molding temperature is too high. Should be properly reduced.
(3) The setting time is too short. The cooling setting time should be properly extended.
Deformation
(1) The foaming magnifications of the bottom and top of the product are inconsistent or the local foaming magnification is too high. The heat transfer of the mold should be checked, the thickness ratio of the mold must be appropriate, and the temperature must be uniform.
(2) The cooling setting time is too short. The cooling setting time should be properly extended.
(3) The stress distribution of the condensation layer of the product is uneven. The temperature distribution of the mold should be checked to adjust the condensation stress of the melt.
(4) Improper mold release time control, or mold release too early, overheating mold release; or mold release too late, too cold mold release. The mold release time should be reasonably controlled.
Unstable size
(1) The foaming limit control varies. The foaming limit should be strictly controlled.
(2) During the production of a single batch of single mold, or the molding temperature and qualitative time are controlled differently. The consistency of the process conditions should be strictly controlled, and a multi-cavity method can also be used to improve the consistency of the products.
(3) The error of the mold exceeds the error of the expansion ratio. The mold should be trimmed to reduce mold errors.
(4) Uneven mold filling or long-term deformation of the mold. The structure size of the mold pouring system should be adjusted, and the mold should be trimmed to reduce errors.
(5) Mold leakage. The mold should be trimmed.
(6) Inconsistent product cooling. The mold heating and cooling system should be checked to ensure that the mold surface temperature is uniform.
(7) The clamping force is not enough. The tension of the hook spring should be adjusted to properly increase the clamping force.
(4) Common problems, causes and solutions of profiles
1. Uneven wall thickness
1. Poor positioning of the mouth template
Due to the inaccurate positioning of the template in the die head, the gap between the die and the die is uneven, and the degree of the Barrass effect is different. After cooling, the wall thickness of the product is eventually uneven.
Countermeasure: Correct the positioning pins between the templates and adjust the die gap.
2. The molding length of the die is short
The determination of the forming length of the die is the key to the design of the profile extrusion head. For different products, the molding length is different, the resistance of the thick wall part is small, and the flow velocity is fast; the resistance of the thin wall is large, and the flow velocity is slow. The forming length of thick-walled products should be longer than that of thin-walled products. Use the forming length to adjust the speed to make the material flow at the outlet even. Otherwise, the product will have uneven thickness and wrinkles
Countermeasure: Refer to relevant manuals to increase the molding length of the die appropriately.
3. Uneven heating of the die head
Due to the uneven heating temperature of the die head heating plate or heating ring, the viscosity of the polymer melt in the die head is not uniform, and after cooling and shrinking, an uneven wall thickness is generated.
Countermeasure: Adjust the temperature of the heating plate or heating ring.
4. The die wear is uneven
The die is a part on the surface of the profiled profile, which is in direct contact with the material, and wear and corrosion will occur. The uneven wear of the die is caused by the difference in material flow rate, flow rate, wall pressure, and resistance of different parts of the inner wall of the die and the diverter cone. Plastic can get a certain shape and size after passing through the die. Therefore, die wear will directly cause uneven thickness.
Countermeasure: adopt the method of "throttling and open source" to repair the gap of the opening template or the angle of the diverter cone.
5. The material contains impurities to block the flow channel
The blockage of the flow channel makes the flow velocity at the exit of the die not uniform, and the material is not stable, thus causing uneven wall thickness of the product.
Countermeasure: Pay attention to the cleanliness of raw materials and clean up the impurities in the die head flow channel.
Second, the bend
1. Uneven wall thickness
Uneven wall thickness naturally causes the product to bend after cooling. The causes and countermeasures of uneven wall thickness are shown in 1 above.
Uneven cooling or insufficient cooling
The molten stream extruded from the die is heat-exchanged and cooled by cooling and vacuum adsorption in the setting die. If the cooling of the various parts of the profile is inconsistent, then the cooling and shrinking of the various parts will cause the profile to bend; After the setting die and the setting water tank, the local temperature is still high and not completely cooled. When the cooling is continued, the partial contraction of the profile will still cause the profile to bend.
Countermeasures: Reduce the temperature of the cooling water, check whether the cooling water path is smooth, adjust the flow of cooling water, increase or block the water holes.
2. Uneven distribution of the resistance of the shaping die
The molten material will have a certain resistance due to cooling shrinkage in the setting mold. If the resistance distribution is quite different, the profile will be inconsistent in the setting mold due to the local resistance.
Countermeasure: Repair the shaping die to increase or decrease the resistance.
3. The traction speed is not constant
The unsynchronized and unsteady speed of the traction machine makes the thickness of the molten material uneven, which causes bending after cooling and shrinking.
Countermeasures: Overhaul the traction machine and adjust the traction speed.
3. Uneven surface
1. Insufficient cooling
Due to inadequate cooling of each part of the profile, the cooling rate of each part is inconsistent, and some parts are generated after the shaping, which causes the uneven surface of the product.
Countermeasures: dredge the water channel, increase the water hole, and increase the flow.
2. The vacuum is not enough
The geometric shape and dimensional accuracy of the plastic products are controlled by the mold. After the profile leaves the die head, the deformation is quite serious under the action of its own weight. After entering the shaping die, it can be matched with the shaping cavity under the action of vacuum adsorption. If the vacuum is not enough, the material does not completely match the cavity, which will cause the surface of the product to be uneven.
Countermeasures: Check the tightness, clear the airway, and increase the vacuum.
3. Towing speed is too fast
Too fast traction speed is inconsistent with the extrusion speed, the parison draw ratio is too large, and the surface is uneven after cooling.
Countermeasure: Adjust the traction speed appropriately.
4. Surface scratches
The shaping die is one of the important components of the extrusion die, which directly determines the final size, geometry and surface roughness of the plastic product.
1. The roughness of the mold is not enough
Countermeasure: Polish the inner cavity of the mold.
2. The indirect seams of each template of the setting die are not smooth
Countermeasure: Polish the plates of the stereotypes.
Five, profile vibration
1. Excessive traction
Countermeasure: Estimate the traction force by the above formula and adjust the traction force until the vibration is eliminated.
2. Unreasonable profile formula
The plastic formula contains a certain amount of plastic additives. According to their functions, plastic additives can be divided into plasticizers, stabilizers (including heat stabilizers, light stabilizers, antioxidants), modifiers (including fillers, reinforcing agents) , Tougheners, coupling agents), processing aids (lubricants, release agents, processing modifiers), other additives (including flame retardants, antistatic agents, foaming agents, crosslinking agents). Among them, the role of lubricant is more important. It not only improves the lubricity of the polymer, but also avoids degradation, improves the toughness of the product, reduces the energy consumption of processing, and increases the processing rate. Proper proportion of plastic formula will bring many benefits; if the proportion is not suitable, it will reduce the performance of the product, cause the product to warp, and cause profile vibration.
Countermeasure: Adjust the formula to properly increase the content of lubricants (such as hard fatty acids, hard fatty soaps, stearates, etc.).
Sixth, there are decomposition lines on the surface
1. The die structure is unreasonable and there are dead angles in the nose
The material flow channel of the machine head should be streamlined, and there should be no dead corners and areas that cause material stagnation at the joints of components. If the flow path in the machine head is not gradual, and expands or shrinks sharply, there are "dead spots" and steps, and the behavior of material flow is not observed, so that the polymer degrades there, and a decomposition line is generated during molding.
Countermeasure: trim the mold polishing channel to eliminate dead corners and reduce the time the material stays here.
2. Poor thermal stability of raw materials
In order to prevent PVC from degrading during processing, appropriate heat stabilizers should be selected. It must have two major functions: ①It must prevent the occurrence of HCl removal reaction in the early stage of processing, ②It must be able to react with HCl quickly in the case of HCl removal reaction to slow down the autocatalytic effect of HCl on further degradation of PVC.
Countermeasure: Check the plastic formula and increase the proportion of stabilizer appropriately.
The failure of the plastic profile extrusion die is not necessarily single. It may be that several defects exist at the same time, and should be comprehensively analyzed and considered as a unified whole.
Friendly reminder: rubber and plastic raw materials need to be tailored according to local conditions in the production of finished products. According to different equipment, different products and different recipes, their processing and equipment and temperature and other multi-party processes are adjusted. parameter.
Causes and countermeasures of defects in extruded products
Problems
Causes and countermeasures
Surface welding marks
1. Poor die design
(1) When setting the flow channel in the die, the flow rate of the melt should be uniform.
(2) The pressure at the front end of the die should be appropriately increased.
(3) The length of the die shaping section should be appropriately increased.
(4) A molten pool should be set behind the mold core support.
(5) The channel cross-section at the die population should be increased appropriately.
(6) The abrupt die of the plate runner should be used.
2. Material selection is inconsistent with molding conditions
(1) Raw materials with low melt viscosity and poor flow properties should be selected.
(2) The temperature of the barrel should be properly increased and the die temperature should be reduced.
(3) The extrusion speed should be properly reduced
Surface stripes and moire
1. Raw materials do not meet molding requirements
(1) For PVC raw materials, the flow properties of the melt should be appropriately reduced.
(2) Avoid mixing resins of different colors.
(3) Avoid mixing resins with different melt flow rates or grades.
2. Incorrect screw type selection and improper die structure design
(1) A screw with good mixing and mixing performance should be selected.
(2) A molten material pool or branch pipe should be set in the die.
(3) The catastrophic die of the plate runner should be used as much as possible.
(4) The number of filters should be appropriately increased
Poor surface gloss and longitudinal stripes
1. Improper molding conditions and raw material handling
(1) The temperature of the screw should be properly reduced to prevent it from overheating.
(2) The temperature of the barrel should be properly reduced to prevent the molten material from overheating.
(3) The amount of barium (Ba) metal soap and calcium (Ca) metal soap with strong electropositivity should be appropriately reduced.
(4) The raw materials should be pre-dried.
(5) The flowability of the melt should be appropriately improved.
(6) The extrusion speed should be appropriately reduced.
2. Unreasonable design of die structure
(1) The pressure at the front end of the die should be appropriately increased.
(2) The leading part of the flow material of the die shaping section should be properly enlarged.
(3) The shaping section of the die should be kept smooth.
(4) 0.2R fillet should be provided at the nozzle outlet
There are longitudinal ribs at the exit of the mold
1. Precipitate adhesion and accumulation
(1) The melt temperature should be properly reduced.
(2) The blank material should be cooled by the blower before entering the shaping die.
(3) No gap should be left between the inner surface of the mold and the parison.
(4) The sliding surface of the mold should be treated with fluorine-containing materials.
2. Improper design and operation of the mold structure
(1) Rounded corners should be provided at the corners of the really fixed attraction or gap.
(2) The cooling effect of the sliding surface of the mold should be improved.
(3) It should be checked whether the setting mold is too long, and whether the setting molds are concentric.
(4) The pores of the mold should be cleaned.
(5) The rust spots on the sliding surface of the mold should be removed
Surface spots and fish eyes
1. Raw materials do not meet molding requirements
(1) It should be prevented to mix polyvinyl chloride raw materials with different degrees of polymerization.
(2) Avoid mixing resins with different melt viscosities.
(3) The blending ratio and mixing process of recycled materials should be controlled.
2. Improper control of molding conditions
(1) Appropriate screw type should be selected and the screw should be prevented from overheating.
(2) During the extrusion process, foreign substances and impurities should be strictly controlled.
(3) The metal mesh should be used to filter the melt, while increasing the melt pressure
Melt decomposes in the die
1. The melt is overheated in the barrel
(1) The compression ratio of the screw should be properly reduced.
(2) Gradient screws should be used to avoid sharp compression.
(3) The screw speed should be reduced appropriately.
(4) Compressed air should be used to cool the screw, and the temperature of the screw should be appropriately reduced.
2. Unreasonable design of die structure
(1) The guide part of the flow material of the die should be appropriately increased, and the pressure at the front of the die should be increased.
(2) The stagnation angle in the die should be eliminated as much as possible.
(3) The length of the die should be shortened as much as possible to reduce the residence time of the melt at the die
The overall shrinkage of the profile is too large
1. The traction contraction rate is too large
(1) The traction shrinkage of the die should be minimized.
(2) When the traction shrinkage is too large, the melt temperature should be increased as much as possible.
2. Insufficient cooling
(1) After the profile is solidified and set, it should still be cooled sufficiently to below room temperature.
(2) The temperature of the cooling water should be reduced appropriately.
(3) For hollow profiles and thick-walled parts, the cooling length should be appropriately increased.
(4) The extrusion and traction speed should be appropriately reduced
The ribs contract too much
1. The melt flow in the rib groove of the die is too slow, the rib groove is stretched
(1) The gap of the ribs should not be increased, and the population of molten material should be enlarged to increase the flow speed of the molten material in the rib groove.
(2) The flow speed of the melt at the end of the rib groove should be increased as much as possible.
2. Most of the melt in the groove
(1) A baffle should be set in the die groove of the die to shunt the melt.
(2) The traction should be speeded up, and the slipping mold should be adopted.
(3) Vacuum setting die should be used to stretch and cool the rib.
3. Molding speed is too fast
(1) The tensile shrinkage of the die should be minimized.
(2) The length of the end shaping section should be reduced
Cracked or jagged end
1. The melt flow rate at the end of the die is too slow
(1) The population of the fixed section of the end should be appropriately increased.
(2) The length of the end shaping section should be reduced.
2. Improper temperature control of die lip
(1) The lip temperature should be properly increased.
(2) A cylindrical heater should be inserted near the end of the nozzle of the die.
(3) The temperature of the barrel should be properly reduced to increase the viscosity of the melt
Unstable feed
1. Resin slips in the feed section of the extruder
(1) A hopper should be used to heat the raw material.
(2) The temperature at the bottom of the hopper and the feeding section of the extruder should be increased.
(3) The length of the feed section of the screw should be increased appropriately, especially when extruding polyamide and cellulose resin.
(4) The barrel of the feed section of the extruder should be grooved.
2. Resin feeding at the hopper is unstable
(1) Resin raw materials with uniform particle size should be selected.
(2) The temperature of raw materials should be kept uniform.
(3) The raw materials sent to the hopper should maintain a relatively stable supply.
(4) Agitators should be installed in the hopper to prevent bridges.
(5) Recycled materials must be blended quantitatively
Unstable size
1. Unstable feed
The process conditions of the feed section and hopper of the extruder should be adjusted appropriately.
2. Mechanical failure of traction device
(1) The motor speed of the tractor is too low. Should be appropriately improved.
(2) The belt or transmission slips. Should be repaired.
(3) The profile slips on the traction roller or traction track. The clamping force should be adjusted appropriately.
3. Improper design or adjustment of die structure and shaping device
(1) The traction shrinkage of the die should be appropriately reduced.
(2) Air cooling should be carried out before setting the mold population.
(3) It should be fully cooled under the condition that the setting die is not overheated.
(4) Separate setting die should be used
The parison slips badly in the setting die
1. Unstable discharge speed at the die lip
(1) The length of the shaped section of the die or the population of the shaped section should be corrected, and the discharge rate at the nozzle of the die should be adjusted.
(2) A cylindrical heater should be inserted at the end of the die to locally adjust the flow of melt.
2. Poor cooling of the mold
(1) Brass with a larger thermal conductivity should be used to make the mold to improve its cooling efficiency.
(2) The temperature of the cooling water should be reduced.
(3) Separate molds should be used.
(4) During dry vacuum setting, a small amount of water should be added to the shape mold to improve the slip performance.
3. The melt temperature is too high
(1) The temperature of the barrel should be properly reduced.
(2) Cooling water or cold air should be passed into the screw to appropriately reduce the screw temperature
Profile bending deformation
1. Uneven discharge of die
(1) The die should be modified to make the extrusion speed of the melt at the exit of the die uniform, and the length of the shaped section of the die can be increased and the flow block can be added.
(2) The shrinkage rate should be reduced.
2. Improper cooling method
(1) The cooling efficiency at the thick wall should be improved to speed up the solidification.
(2) The cooling amount at the thin wall should be reduced or heated with hot air to slow down the curing speed.
(3) The cooling water should maintain a certain temperature.
(4) The center position of the shaping die and the pulling roller should be correct.
3. Bad structural design of profile
(1) The wall thickness around the profile should be as symmetric and uniform as possible.
(2) A small area of hollow should be provided in the thick-walled section.
(3) The disparity in wall thickness cannot be too large.
4. Unreasonable formula design
(1) Improper selection of resin grade and low molecular weight. New materials should be used instead.
(2) Improper amount of recycled materials. The blending amount of reclaimed materials and fillers should be appropriately reduced.
(3) Too much plasticizer. Should be appropriately reduced.
(4) The amount of modifier is too small. Should be appropriately increased
Reduced strength and elongation of products
1. Improper selection of process and conditions
(1) The flowability of the melt should be appropriately reduced.
(2) Full mixing and kneading should be carried out.
(3) Vacuum degassing should be performed in the mixer.
2. Improper selection of molding equipment and conditions
(1) The screw type with good mixing performance should be selected.
(2) The selected extruder should be mixed evenly.
(3) Large extruders with die and pressure should be used as much as possible.
(4) The molding conditions should be adjusted appropriately to allow sufficient exhaust.
3. Improper design of die structure and setting device
(1) A die with front end pressure should be used.
(2) The traction contraction rate should be appropriately reduced.
(3) The sizing device should adopt slow cooling method, and don't quench it.
(4) There should not be too much friction between the parison and the mold
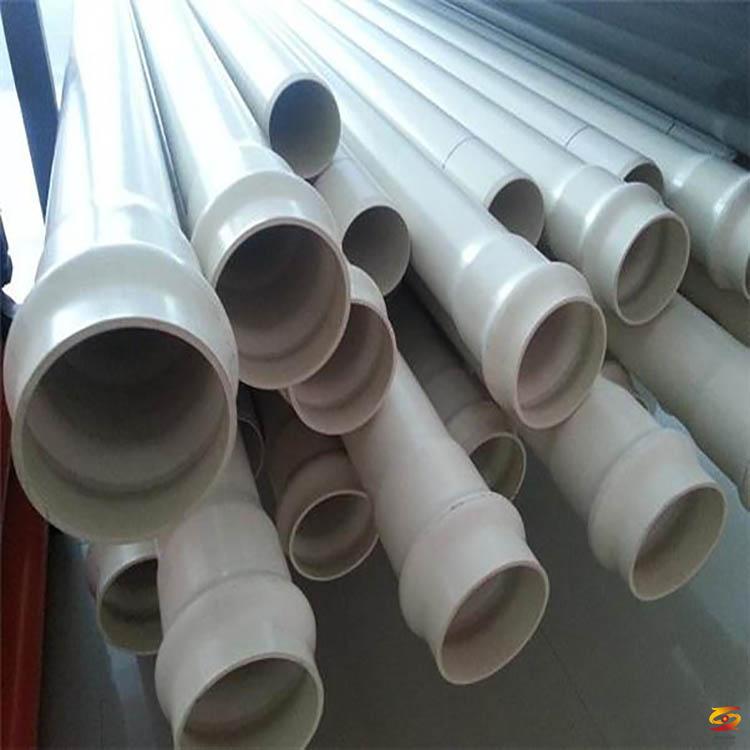
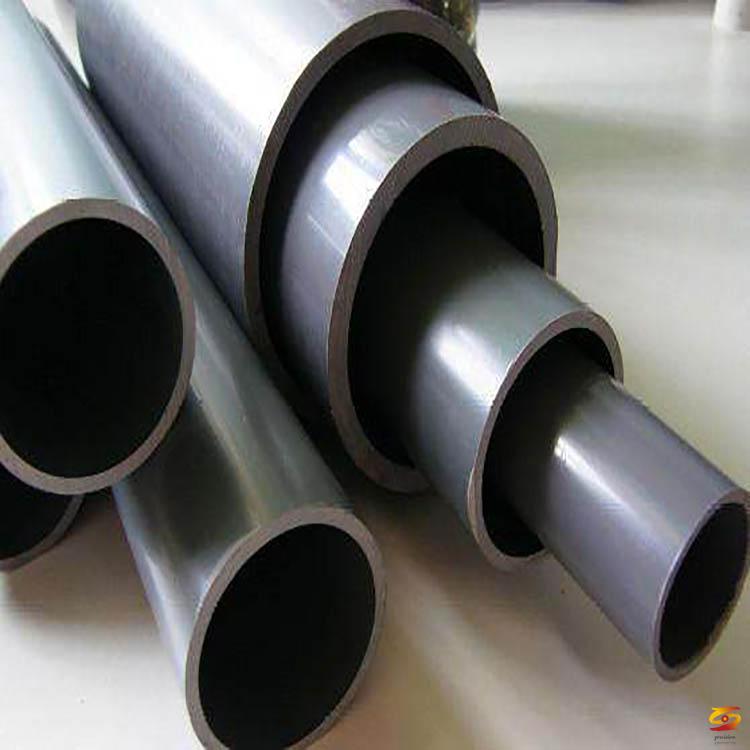
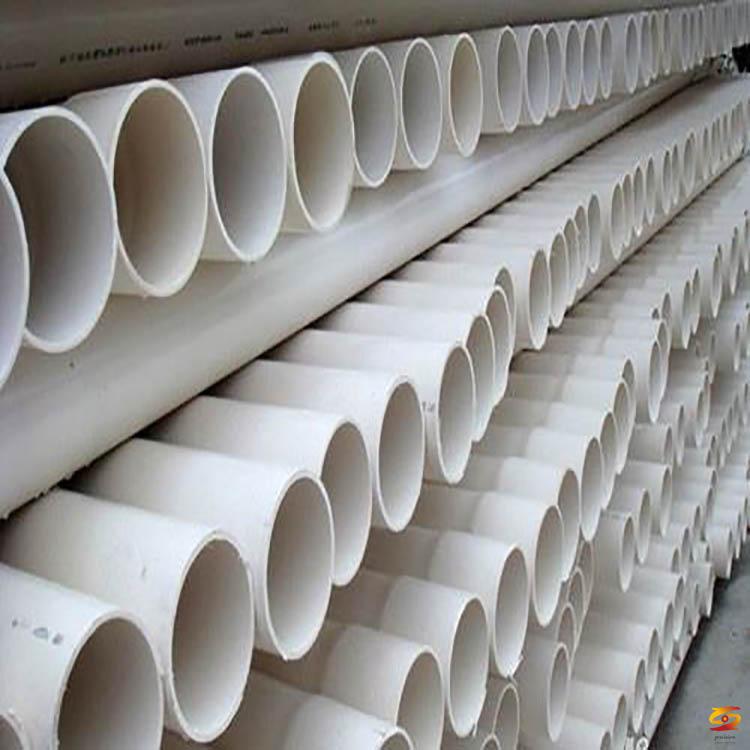
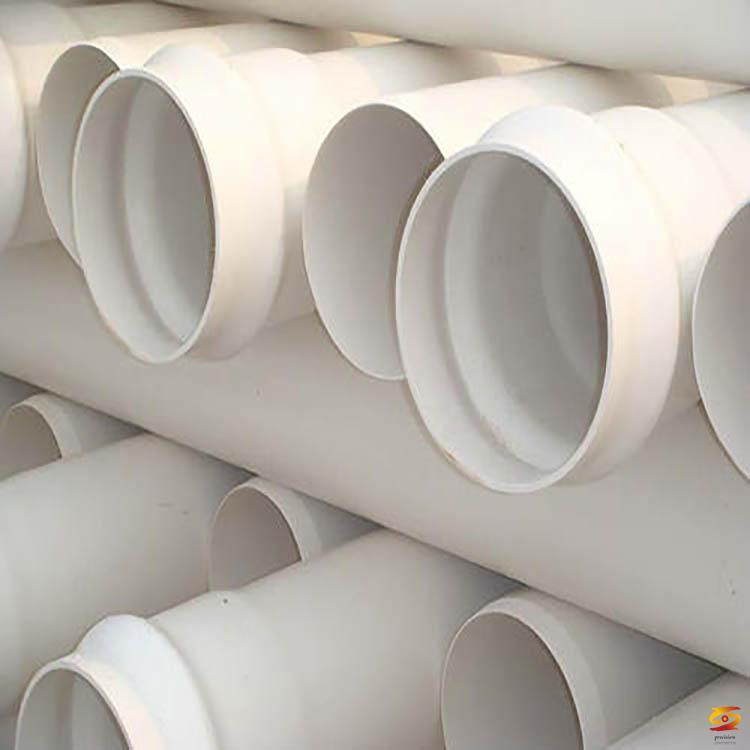