Discussion on co-rotating twin screw extruder technology
Discussion on co-rotating twin screw extruder technologyIn recent years, the co-rotating twin-screw extruder has developed rapidly, its output, torque and speed have been greatly improved, and its application has become increasingly widespread. Improving the production efficiency of co-rotating twin-screw extruders, improving product quality, and realizing multi-functional equipment are the basic requirements for achieving high performance, and the difficulty in research and development.
Increase productivity
Improving production efficiency is one of the important goals for the development of a new co-rotating twin-screw extruder. It can be achieved by increasing the screw speed, enhancing plasticization and mixing capabilities.
At the same screw speed, increasing the depth of the screw groove can greatly increase the delivery volume. Correspondingly, the plasticizing and mixing ability of the screw is also increased, which requires the screw to withstand greater torque. At high screw speeds, the residence time of the materials in the extruder is reduced, which may make the materials plasticized, melted, and mixed insufficiently. For this reason, it is necessary to increase the screw length appropriately, which in turn inevitably leads to an increase in the actual load torque and power of the twin screw extruder.
Increasing the free volume of the screw groove is also an important factor. In the feeding section and devolatilization section, it is very necessary for the screw element to have a large free volume. For bulk materials, increasing the free volume of the feeding section and the degree of filling of the material in the screw groove can greatly increase the production of the extruder ability.
To increase the torque and speed, the deceleration distribution box needs to be carefully designed. To greatly increase the torque index of the equipment, higher requirements will be placed on the design and manufacturing level of the transmission box. The higher the torque, the higher the design, manufacturing accuracy, material strength and heat treatment requirements of the gears, output shafts, bearings and other parts in the transmission box. At the same time, the design and manufacturing accuracy requirements of the screw mandrel, threaded components and kneading discs are also required higher. Because the free volume of the threaded element needs to be increased, the center distance between the two screws will decrease when the outer diameter of the screw is unchanged, which will make the problem of insufficient installation space for the matching gear and thrust bearing become more prominent.
improve product quality
To obtain high product quality, the design of the plasticizing system, the core component of the extruder, is of great importance.
The plasticizing system mainly includes a screw and a barrel. In order to adapt to various processing requirements, the screw and the barrel are usually designed as a modular combination structure. According to the function of each section, the screw can be divided into feeding section, plasticizing section, mixing section, exhaust section and extrusion section. These sections have different functions in the extrusion process, their structures are different, and the corresponding geometric parameters of the screw elements are also different, so how to determine the geometric parameters of the screw elements becomes the key to the design of the plasticizing system.
For co-rotating twin screws, there is a certain relationship between the diameter ratio (that is, the ratio of the center distance of the two screws to the radius of the screw), the number of thread heads, and the apex angle of the thread. It cannot be arbitrarily designed, otherwise it will occur between the two screws put one's oar in. To solve this problem, the author obtained the theoretical end surface curve of the screw according to the trajectory of the two screws. Using the three-dimensional solid modeling function of the large-scale computer-aided design (CAD) software, the twin-screw geometric modeling program was compiled to realize the three-dimensional solid graphics of the twin screw. It shows that the geometric parameters of various types of self-cleaning thread elements are obtained, and the meshing of the two screws is checked. In addition, combined with engineering practice, with the help of a computer, the three-dimensional solid model of the twin-screw with clearance is completed, which can be used to check whether the gap between the two screws is uniform, so that the material has no dead angle in the movement of the screw, that is, the screw has a strong The cleaning ability can effectively prevent the material from staying in the machine for too long and degrading, which undoubtedly provides a good processing method for manufacturing high-end and high-quality plastic products.
Due to the increase in screw speed, the residence time of the materials in the extruder is shortened. In order to make the materials more fully plasticized and mixed, and the temperature rise of the materials can be eased, to obtain high-quality products, in addition to the need for In addition to the optimized combination of screw elements, the length-diameter ratio of the screw also needs to be increased. However, the increase in L/D increases the requirements for the manufacturing accuracy and driving power of the machine and the bearing torque of the screw mandrel, and requires a higher level in manufacturing technology and structural design.
In addition, the optimized combination of threaded components in the exhaust section, the establishment of pressure-building components in front of the exhaust port, and the use of large-lead threaded components can improve the efficiency of devolatilization; in addition, the use of melt gears between the head and the extruder The pump builds pressure, which reduces the pressure at the end of the metering section of the extruder, shortens the effective full length of the screw, and lengthens the effective exhaust length, and can also improve the exhaust effect to a certain extent.
Multifunctional
As the process uses of twin-screw extruders become more and more extensive, in addition to the general processes of feeding, conveying, compressing, plasticizing, mixing, venting, homogenizing, etc. in the extruder, it is often required to complete Various processes such as dehydration, drying, degradation, reactive extrusion, etc., and require twin-screw extruders with multi-feed and multi-stage exhaust functions. In order to meet the user's different processes and requirements for rapid product updates, the design of the plasticizing system should focus on the development of different threaded components, barrels, and feeding systems. In addition to the development of four types of screw components for different combinations, different types of barrels need to be designed. In addition to the general closed barrels used in the plasticizing, melting and homogenization sections, there are also feeding barrels with upper openings , Side feeding barrel with side opening, glass fiber and vacuum barrel.
The feeder barrel is designed in the form of a wedge-shaped gap in the feed port. A wedge-shaped gap is formed on the side wall of the feed port and the screw surface up to the center of the bottom of the feed port, so that the material can be smoothly brought into the extruder by rotation. The side feeder barrel is designed to add materials that are difficult to add, such as carbon black, or easily decomposed additives that should not stay in the screw for too long, while the auxiliary feeder barrel is designed to add additives such as glass fiber. On the exhaust barrel, the exhaust port is vertically upward, and the center line of the exhaust port is offset by a certain distance from the center line of the barrel along the rotation direction of the screw, thereby reducing the rotation of the screw due to the centrifugal force from the exhaust port Out of possibility.
Design of self-cleaning, high-volume co-rotating twin-screw quantitative feeder, which cooperates with the liquid feeder of the side feeder, which can be premixed by conventional agitators, and then added to the base material through the main feed port. The process of twin-screw extruder has better mixing quality and can increase the output to a certain extent.
Multiple exhaust devices, such as natural exhaust and vacuum exhaust systems, can also be designed to exhaust volatile components during the mixing process. A large number of volatiles can be discharged through the multi-stage exhaust port, the intermediate steps of polymerization and mixing can be saved, and the production efficiency can be improved.
For the extruder with multi-path feeding and multi-stage exhaust, the length-to-diameter ratio is larger, which is 36-48, and can be adjusted freely according to the user's processing requirements.
The barrel and screw are required to have high wear resistance. Threaded components and kneading components need to be made of high wear-resistant cemented carbide. When used for glass fiber reinforced processing, the life span is 6-8 times longer than that of commonly used nitrided steel. The barrel adopts bimetal bushing to improve wear resistance and extend the life of the barrel. Bimetal bushing is a layer of SL100 high wear-resistant alloy with a thickness of 1.5-2.0mm, which is made of ordinary steel or low-alloy steel, and then processed by special machining. The hardness of the alloy layer is HRC58-64.
If you want to know more about it please do not hesitate to
contact me. WhatsApp:+86-15966835076.
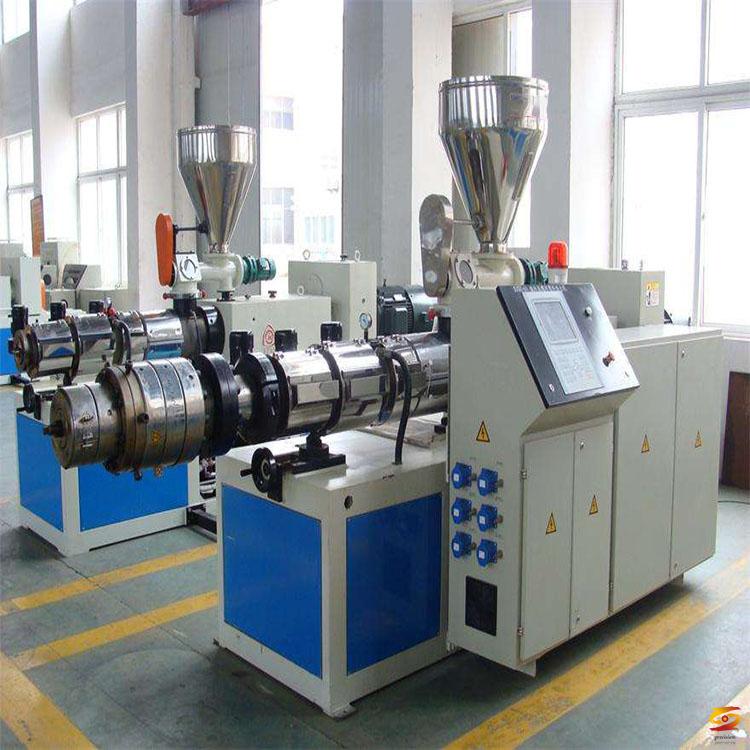