Electric heat sink sharing detailed explanation of maintenance and cleaning steps of meltblown cloth equipment! Must be collected
Electric heat sink sharing detailed explanation of maintenance and cleaning steps of meltblown cloth equipment! Must be collectedWhat is the cleaning procedure of melt-blown cloth equipment? Today, I will introduce the cleaning procedure of melt-blown cloth equipment.
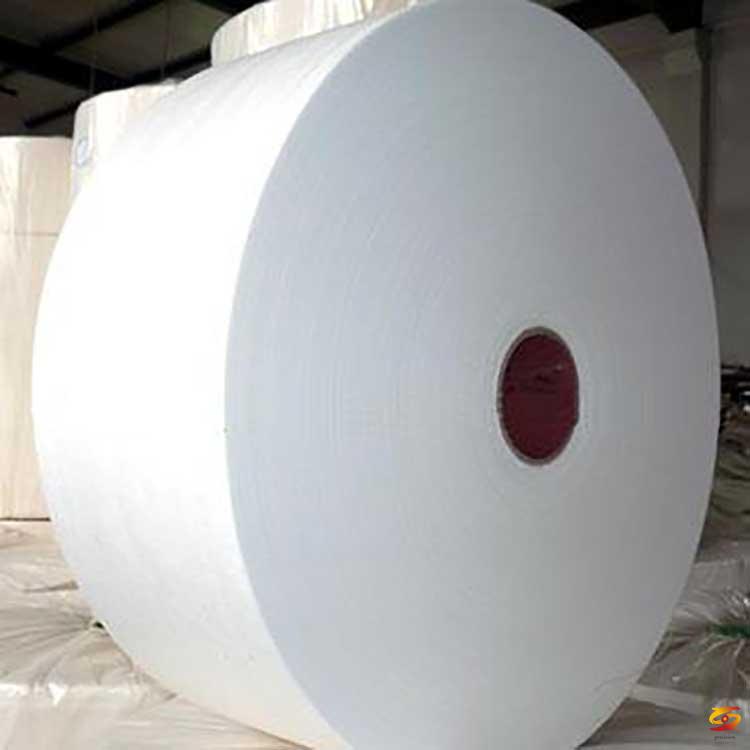
Cleaning procedure for cleaning and maintenance of spinning components of melt blowing system:
Decomposition of components-calcination-high pressure water cleaning-ultrasonic cleaning-compressed air drying-to be inspected-component assembly
1. Disassembly (Note: special tools are required for the disassembly and assembly process)
(1) Quickly clean the surface of the disassembled component, try to clean up the large pieces of slurry remaining on the surface of the component.
(2) Hang the component on the worktable, and place it properly with the spinning surface of the spinneret as the support.
(3) Use an Allen wrench to remove all 142 M12 bolts on the connecting plate, and then use an impact hammer to pull out four φ12 cylindrical pins.
(4) After suspending the connection board and putting it away, take out the distribution board and place it properly.
(5) Install four M10 eye bolts on both sides of the spinneret, turn the spinneret over, and place it with the outlet side of the spinneret facing up.
(6) Use an Allen wrench to remove 25 M12 bolts on one side of the blade first, then leave one fastening in each of the left, center, and right positions, and use the impact hammer to pull out 28 M16 set screws and 28 φ12 cylindrical pins.
(7) Install a T-shaped M16 handle in the threaded holes in the left, center and right positions of the knife plate, and three people respectively support them, and then remove the remaining three M12 bolts.
(8) Three people screw in the T-shaped handles separately. When the blade is lifted up and separated from the spinneret, the blade on this side can be moved to the workbench and placed.
(9) Use the same method to remove the blade on the other side.
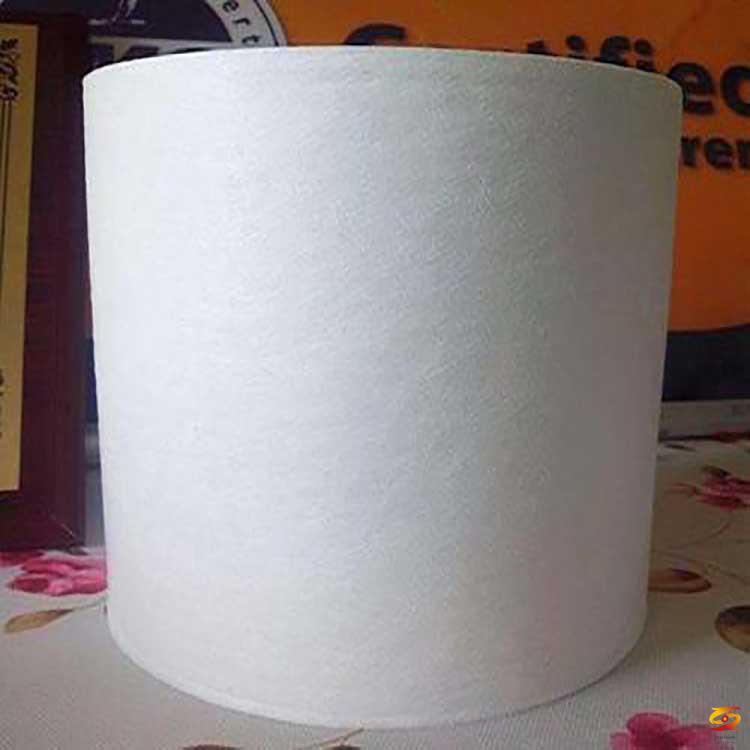
2. Calcination
(1) Put the decomposed spinneret and distribution board into the calcination furnace, and place the spinneret with the exit side of the spinneret facing up. Before calcining, make sure that the sealing strip has been removed.
(2) Select the working mode of the calciner at the "calcining" position. The operating mode is selected in the "automatic" operating position
(3) Setting parameters and operation
After setting the process parameters (temperature, time), start the equipment, and the calcination (cleaning) calciner will automatically run according to the set procedures and parameters, and process the components.
The first stage heats up; the set temperature is 290℃, the set processing time is 45 minutes and the heat preservation is 60 minutes
Second stage; set temperature 450℃, set processing time 45 minutes, keep heat 120 minutes
The third stage; the vacuum pump automatically starts, starts vacuuming for 150 minutes, and automatically stops;
The fourth stage of temperature reduction; after the end of the vacuum, the furnace temperature will automatically drop to 52 ℃, the total processing time is 7 hours.
(4) Install four M10 lifting rings on both sides of the module, hang out the workpiece according to the operating regulations, and carry out the work in the next step.
3. High pressure water cleaning spinneret
(1) Send the connection board, spinneret, distribution board and knife board to the cleaning site;
(2) After fixing the connection board and the distribution board separately, first wash the two board surfaces repeatedly with a high-pressure (160kg/cm2) flowering water gun.
(3) Use 160kg/cm2 to clean all the boards.
(4) Use the same method to clean the spinneret and blade, but the water pressure must be controlled within 30kg/cm2.
(5) Then use 1000-mesh metallographic sandpaper to polish the bevels on both sides of the spinneret, and the airway and exit surface of the knife plate.
(6) After the spinneret assembly cleaned with high-pressure water is returned to the cleaning room, if it is not immediately cleaned by ultrasound, the moisture should be dried in time and properly placed for use.
4. Ultrasonic cleaning
(1) After the spinneret cleaned with high-pressure water is transported back to the cleaning room, place it in the ultrasonic cleaning machine with the inlet hole down and the outlet hole up.
(2) Prepare the cleaning solution; inject a sufficient amount of desalinated water (or distilled water), and add a cleaning agent (wash clean).
(3) Wash for 60 minutes at a water temperature of 50-70°C.
(4) Replace the cleaning fluid and drain the water in the water tank of the washing machine; blow it off with compressed air.
(5) Secondary ultrasonic cleaning; inject clean water (demineralized water or distilled water), and wash for 60 minutes at a water temperature of 50-70°C.
(6) Dry the water; after cleaning, hang the spinneret and dry the water with compressed air, put it on a special platform, cover it with a clean cloth and wait for inspection.
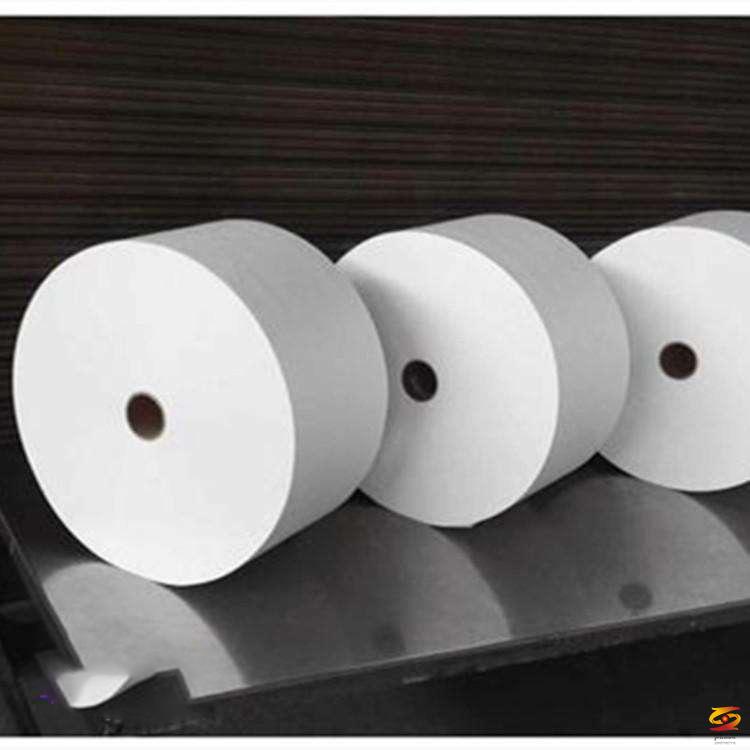
Ultrasonic cleaning distribution board and connecting board
(1) Install a lifting ring on the connecting plate, hang it in the ultrasonic cleaning machine, and directly put the distribution plate into the cleaning machine by hand;
(2) Fill with cleaning solution; inject sufficient amount of clean water until the workpiece is submerged by 40mm;
(3) Wash for 60 minutes at 50-70°C water temperature.
(4) Blow dry the water; hang out the distribution board, dry it with compressed air, put it on a special platform, cover it with a clean cloth and wait for use.
Ultrasonic cleaning blade
(1) Using the T-shaped handle, carefully place the two blades into the ultrasonic cleaner.
(2) Clean in the same way as cleaning the distribution board.
If you want to know more about it please do not hesitate to
contact me. WhatsApp:+86-15966835076.
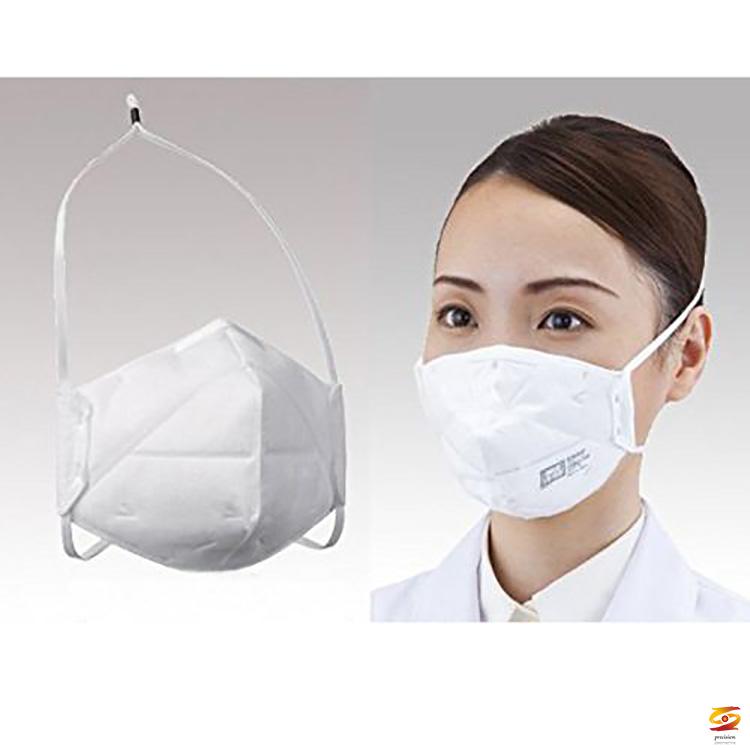