Key points and precautions for tapping the screw thread of the twin screw extruder
Key points and precautions for tapping the screw thread of the twin screw extruderTwin-screw extruder threaded sleeves are usually used for angular threaded workpieces. In addition to machining, threads can also be obtained by tapping and threading in pliers machining methods. The twin-screw extruder thread tapping (also known as tapping) is to use taps to process the internal threads on the cylindrical surface of the workpiece; the threads (or ferrules, buckles) are to use the die to process the external threads on the cylindrical rod. .
Faucet and hinge 1 Each faucet has a working part and a handle. Working parts include cutting parts and calibration parts. There are several (usually three or four) chip pockets in the axial direction, correspondingly forming multiple fins (cutting edges) and rake angles. The cutting part (ie, the incomplete tooth part) is an important part of the cutting thread, and is often ground into a conical shape so that the cutting load is distributed over several teeth.
The nose cone has a smaller cone angle with 5-7 teeth; the second cone has a larger angle with 3-4 teeth. The calibration part has complete teeth for thread reduction and a guide tap for axial movement. The handle has a square head for matching hinges and transmitting torque.
Hinge Hinge is a tool used to fix the faucet. Adjustable hinges are usually used. Rotate the handle to adjust the size of the square hole to accommodate different sized faucets. The length of the hinge should be selected according to the size of the faucet to control the torque during tapping and prevent the faucet from being twisted due to improper force application.
Determine the diameter and depth of the drill hole and the diameter of the bottom hole before tapping and chamfering the opening of the screw sleeve of the twin screw extruder. During the tapping process, the cutting edge is mainly for cutting metal, as well as extrusion. The action of metal causes the metal to protrude and flow toward the tip of the tooth, so the hole diameter of the drill bit (that is, the bottom hole) should be larger than the inner diameter of the thread before tapping.
The diameter of the bottom hole can be found in the manual or according to the following empirical formula: brittle materials (cast iron, bronze, etc.): drilling diameter d0 = d (thread outside diameter)-1.1p (pitch) plastic materials (steel, copper, etc.): Drilling diameter d0 = d (thread outside diameter)-p (pitch) The drilling depth is determined when the blind hole thread (without through hole) is tapped. The drilling depth cannot be greater than the thread length. The blind hole depth can be based on the following formula Calculation: the depth of the hole = the depth of the required thread +-.7d The chamfer of the hole is chamfered at the hole of the hole before tapping to facilitate positioning and cutting the faucet. The depth of the chamfer is greater than the pitch of the thread.
The precautions and precautions for operating the threaded sleeve of the twin screw extruder are based on the specifications of the threaded holes on the workpiece. The tap is selected correctly, the first cone and the second cone are not reversed. When clamping the workpiece, make the center of the hole perpendicular to the jaws to prevent thread tapping. When tapping the thread with a cone, first screw in 1-2 turns and check whether the faucet is perpendicular to the end face of the hole (visible or perpendicular to two directions perpendicular to each other). When the cutting part cuts into the workpiece, it should be reversed by 1/4 turn and 1-2 turns to break the chip; at the same time, no pressure should be applied (that is, only rotate without pressing) to avoid knocking or Tap the tap. The thread teeth are thinner.
If you want to know more about it please do not hesitate to
contact me. WhatsApp:+86-15966835076.
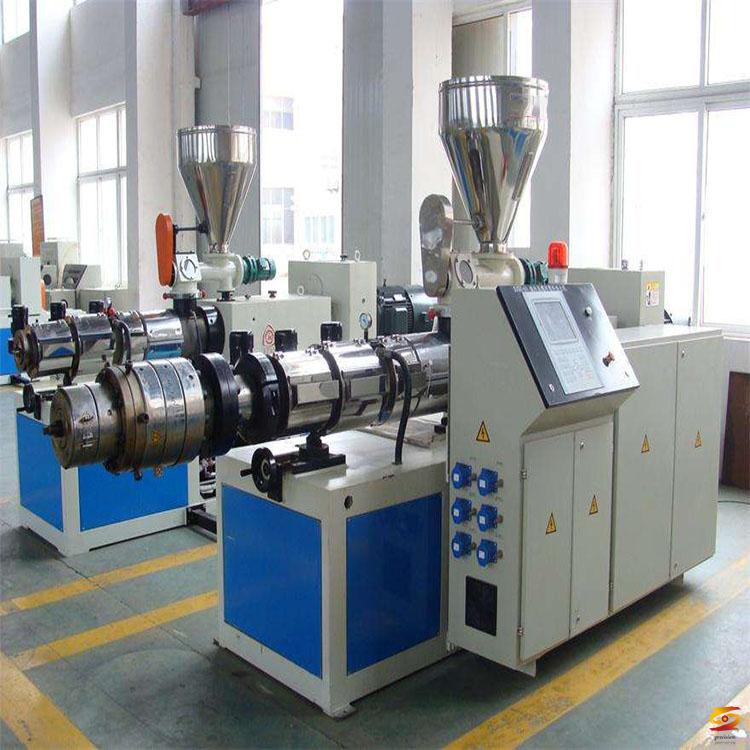
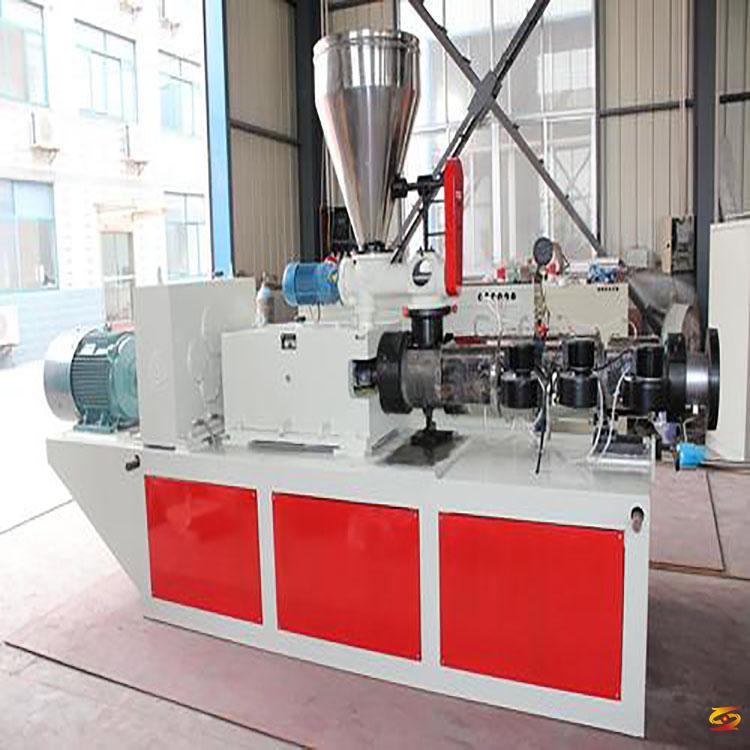
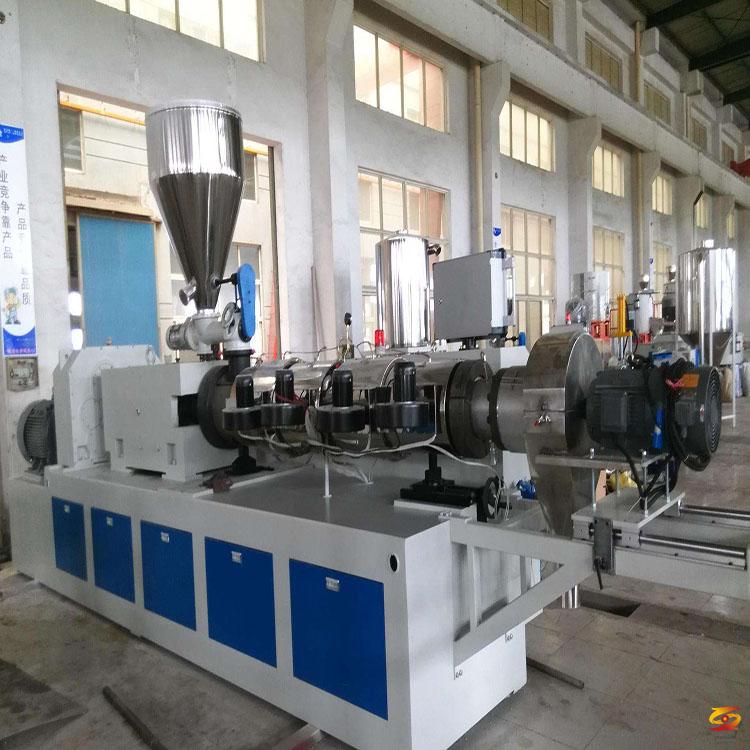