Market characteristics and development direction of XPS extruded board
Market characteristics and development direction of XPS extruded board1. Features of the extruded board market
XPS flame-retardant extruded board production enterprises, mainly in the production of recycled materials. When the PS material with poor quality is melted many times, the molecular weight decreases greatly. It is difficult to form bubbles under higher pressure, which leads to a high opening rate, and the product is not easy to form or the quality is reduced.
The xps extruded board production machinery is designed for HCFC-22 and 142B. After the new foaming agent is used, the equipment screw and injection equipment need to be modified. Higher requirements are placed on equipment manufacturers.
The management level of Tangshan extruded board production enterprises is low, such as the use of flammable hydrocarbon blowing agents, such as the absence of renovation of ventilation and explosion-proof facilities. Very likely to cause fire.
2. Some directions of China XPS extruded board foam replacement technology
1. Add chain extender to increase the molecular weight of recycled materials.
2. Add inorganic fillers, such as nano-powder, etc. to improve the strength of PS melt
3. Add other polymers with high solution strength.
4. Lower the polymer melt temperature.
5. Through physical cross-linking or chemical cross-linking, the PS molecular chain can be cross-linked or branched.
The best case is to produce a bimodal distribution of molecular weight
6. Increase the amount of first-level screw advancement, preferably twin-screw advancement.
7. Replace the common plunger pump with a diaphragm pump.
8. Renovate the workshop and production equipment, and add fire prevention, explosion prevention, and ventilation facilities.
3. Difficulties and defects of XPS flame retardant extruded board foam replacement technology
1. High product density, especially when using carbon dioxide foaming technology.
2. Poor production stability. Especially the stability of carbon dioxide injection system is difficult to control.
3. The product has high thermal conductivity. Especially when using pure carbon dioxide foaming.
4. Poor flame retardancy. Especially when foaming with dimethyl ether.
5. Poor chemical stability. Especially when foaming water is used, the water reacts with hexabromododecane to release strong acids and corrode the screw.
6. The thickness of the product is limited. Especially carbon dioxide foam, the thickness is generally not more than six centimeters
7. Poor safety. Many companies have already started fires due to the use of hydrocarbon blowing agents.
If you want to know more about it please do not hesitate to
contact me. WhatsApp:+86-15966835076.
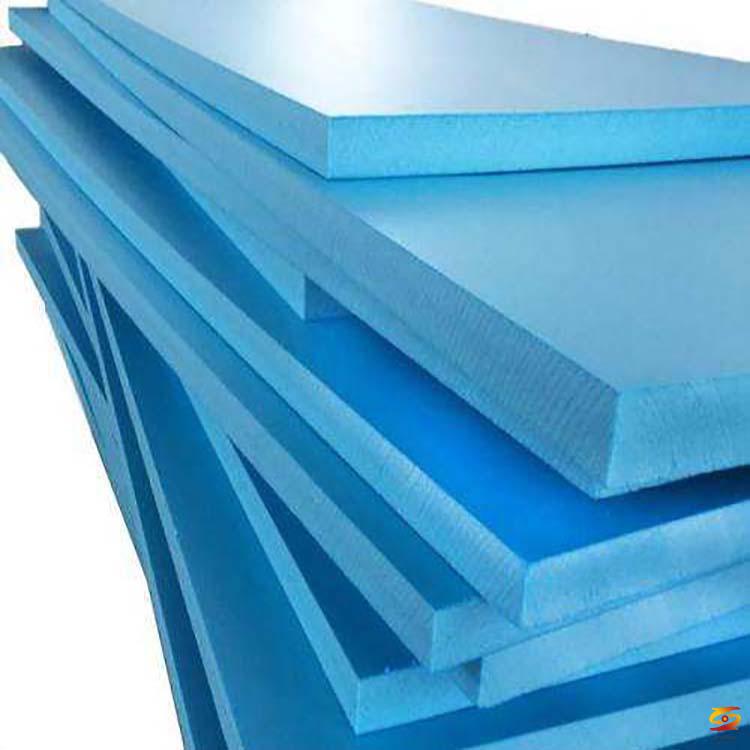
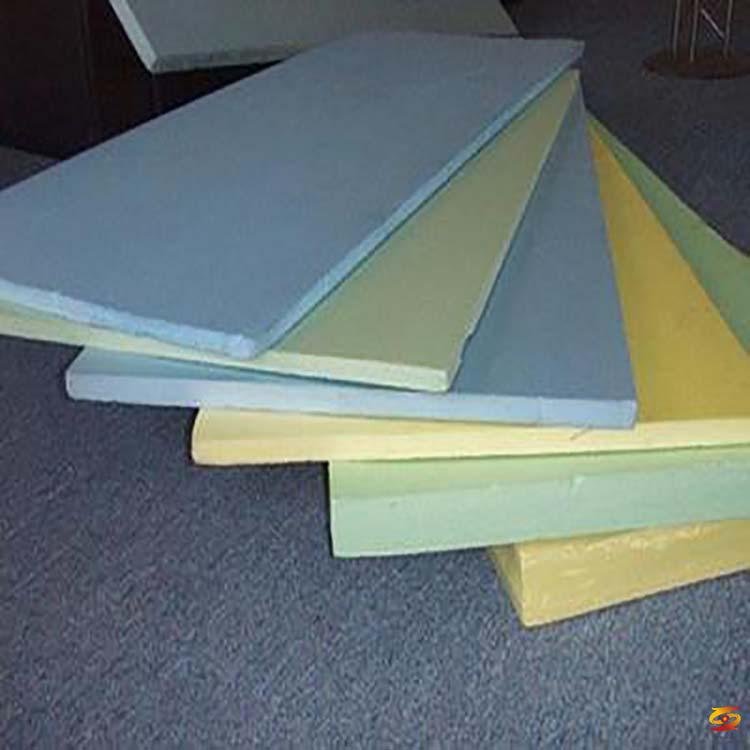
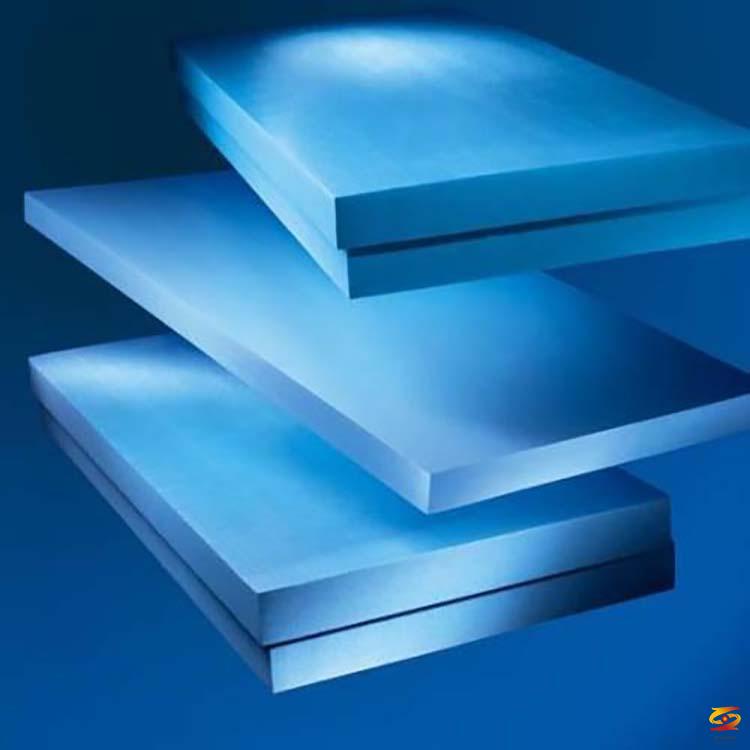