Operation process of EPE foaming machine
Operation process of EPE foaming machine8.1 Check whether butane, monoglyceride and nitrogen are sufficient. Butane must be pressurized with nitrogen to be injected into the extruder by the butane pump. The pressure of nitrogen is generally set at 1.3-1.4Mpa. If the pressure value of nitrogen drops to 2Mpa, new nitrogen should be replaced.
8.3 Change the network. According to the thickness of the sheet to be produced, install the corresponding filter on the filter board. For the selection of the filter, please refer to the following table:

8.4 Warm-up
8.4.1 Turn on the power switch of the main electrical cabinet and turn on the shunt switch. Check whether the temperature controller in each zone is displayed normally. Find anomalies and resolve them immediately. Adjust the number of each temperature controller to the required temperature, the initial set temperature value can refer to the following table:

8.4.2 Turn on the heating switch of each zone and check whether the ammeter value of each zone is normal. If the current value is less than the rated value, it means that the heater in this area may be damaged and should be checked and replaced immediately.
8.4.3 When the temperature of each zone reaches the set value, keep the temperature for about half an hour to make the temperature inside and outside the barrel screw sufficiently uniform to ensure that the raw materials in the barrel melt sufficiently.
8.4.4 Check whether the monoglyceride in the pot is sufficient.
8.5 Ready to start
8.5.1 After the preheating is completed, open the nitrogen bottles of the butane system, each butane gas cylinder, pressure relief tank, and each valve of the one-way valve. The pressure value of the nitrogen meter is adjusted to 1.3-1.4Mpa, and check for There is no leakage, if there is any leakage, immediate measures should be taken to solve it. Check the flow rate of the butane pump. If the butane pump is frequency-controlled, check whether the FM knob is in the low-frequency position; if it is not frequency-controlled, check whether the flow control valve is in the low-flow position (generally 16%).
8.5.2 Check whether the flow regulating valve of the single glycol pump is in the low flow position. It is generally the position of scale 6.
8.5.3 Turn on the water pump switch and check whether the water pump works normally.
8.5.4 Two paper winding shafts of the winding machine are covered with paper tubes and fastened.
8.6 Power on
EPE foaming machine
8.6.1 Set the cooling temperature.
Modify the temperature values of the first, sixth, seventh, eighth, screen changer and machine head to the cooling temperature. Generally, the first zone is set to 130 C °, and the sixth, seventh and eighth zones are set according to the actual data during the test.
8.6.2 The host starts.
Press the start button of the host, and after the variable frequency speed regulator display is stable, adjust the frequency modulation knob to 8Hz, at this time the host has been started.
Note: It is strictly forbidden to turn on when the temperature is below! ! Otherwise, there is a danger of twisting the screw.
8.6.3 Start the butane pump and single glycol pump.
Press the start button of the butane pump and single glycol pump, and observe whether the indications of the butane pressure gauge and single glycol pressure gauge are normal. If it is abnormal, measures should be taken to solve it. For specific measures, please refer to the fault analysis table.
8.6.4 Start the cooling system.
8.6.4.1 Cooling part of the barrel.
Open the three, six, and eight water valves and adjust the flow of water in each valve. To cool the three areas, pay attention to the proper water flow. If it is too small, the temperature will be slow, and the cooling time will be too long. Because the thermocouple needs a certain response time in the sensing process, the water flow is too large, it is easy to produce stiff material, squeeze 636f707962616964757a686964616f31333431356634, the sheet foaming, serious holes, or even cracked into a ray of strip Therefore, during the cooling process, the temperature of each cooling zone should be observed, and the size of the water flow should be adjusted accordingly.
8.6.4.2 Screen changer and head part.
Turn off the heating knobs of the machine head and the screen changer to stop the heating. Dip the cloth in the water or pour it directly in a small stream of water with a hose to cool the screen changer and the machine head. The cooling of the water should be intermittent to prevent cooling. Too fast, stiff material is generated at the screen changer and the machine head. Note: Before spraying water on the machine head and screen changer, be sure to turn off the heating power to prevent electric shock.
8.6.5 Operation during cooling.
8.6.5.1 Adjust the die gap.
The head adjustment nut of the rotary machine of the pearl cotton foaming machine makes the gap between the inner and outer die of the machine head about 0.1-0.2mm. Properly closing the gap of the small die can reduce the waste of materials. Check the thickness of the extruded material around the die opening and adjust the position of the inner die to make it even with the jacking screw. If the material extruded from the die cracks, it means that there is something dirty in the gap of the die, loosen the adjusting nut, and then go back tightly to release the dirty thing. Note: The gap between the molds should be adjusted properly, too small materials are easy to crack, and too loose materials will have a deflation sound.
8.6.5.2 Control of host frequency, temperature, butane and monoglyceride.
When the temperature in any of the cooling zones of 6, 7, and 8 has basically dropped to the set temperature value, the frequency of the main machine should be adjusted to the frequency required for normal production according to the thickness of the sheet to be produced, and then the flow of butane and monoglycerin should be increased To the corresponding value (each value is based on the value determined during the test). Note that if the flow rate of butane is too large, the head is prone to air jet phenomenon; if the flow rate is too small, the foaming of the material is not good and the pressure in the barrel is too high. If the flow rate of monoglyceride is too large, it will be easy to spray at the machine head; if it is too small, the material will easily stick to the surface of the die, and the extruded sheet will shrink easily. You can immerse the freshly picked material in water and observe whether there are foam bubbles on the surface. If there is any, it indicates that there is monoglyceride in the material.
8.6.5.3 Observe the material extruded from the machine head to determine the degree of cooling. When the edges of the extruded sheet no longer stick to each other, roughly adjust the size of the die gap according to the thickness of the sheet to be produced, and use the inner die to adjust The top thread makes the thickness of the extruded sheet uniform. At the same time, clean up the adhering materials around the die. If the edges of the sheet are stuck, check whether the temperature of the screen changer and the machine head has fallen to the set temperature value. If the temperature is too high, continue to cool down. If it falls to the set value, it may be the temperature of the inside and outside molds. High, wipe the inner and outer die with a damp cloth until the edges are no longer sticking.
8.6.6 Start the sizing blower, wind fan and cutting motor.
8.6.7 Start the tractor and winder and estimate their speed.
8.6.8 Separate the cylindrical foam sheet sprayed from the machine head, move the sizing drum to align the machine head, two people cooperate to put the foam sheet over the sizing drum, and tear off the end defective products while pulling, After flattening the frame to the tractor, and then to the winder, it is quickly wound around the paper tube of the winding shaft. Adjust the speed of the tractor and the speed of the winding shaft to match the extrusion speed of the sheet.
8.6.9 After the sheet material passes over the sizing cylinder, move the wind ring to the front end of the sizing drum. Note that the wind of the wind ring cannot blow the machine head.
8.6.10 Confirm that the head temperature is not higher than the set temperature, and turn on the screen changer and the head heating switch.
8.6.11 Check the sheet thickness. If it is close to the requirement, the traction speed can be adjusted appropriately to make the sheet meet the requirements; if there is a large difference, the die gap is adjusted first, and then the traction speed is adjusted until the requirement is reached.
8.6.12 According to the quality requirements, check the size of the cell, the height of the ribs, the width and the shrinkage of the sheet, and determine whether the flow rate and temperature of talc, butane, and monoglycerin are appropriate.
8.6.13 When rewinding to about half a roll, pat the sheet roll by hand along the axial direction, the feel should be basically uniform everywhere, otherwise the loose place means the sheet is thin, the tight place means the sheet is thick, then The top wire of the inner die should be adjusted slightly to eliminate this phenomenon.
8.6.14 If the equipment is turned on for the first time after installation, the height and position of the flattening frame, as well as the position of the tractor and winder should be adjusted to ensure that the winding is smooth and tidy.
8.6.15 When the sheet reaches the set length, the device automatically turns over and replaces the station, and at the same time issues an alarm bell to prompt the operator to cut the sheet and wind it onto another winding shaft to enter the next winding cycle.
Note: During the production process, you should always check the consumption of nitrogen, butane, monoglyceride, and whether there is leakage.
8.7 Shutdown
8.7.1 Turn off the host part.
8.7.1.1 Press the stop button on the down-converter governor operator to return the FM knob to 0 (turn counterclockwise to the end).
If you want to know more about it please do not hesitate to
contact me. WhatsApp:+86-15966835076.
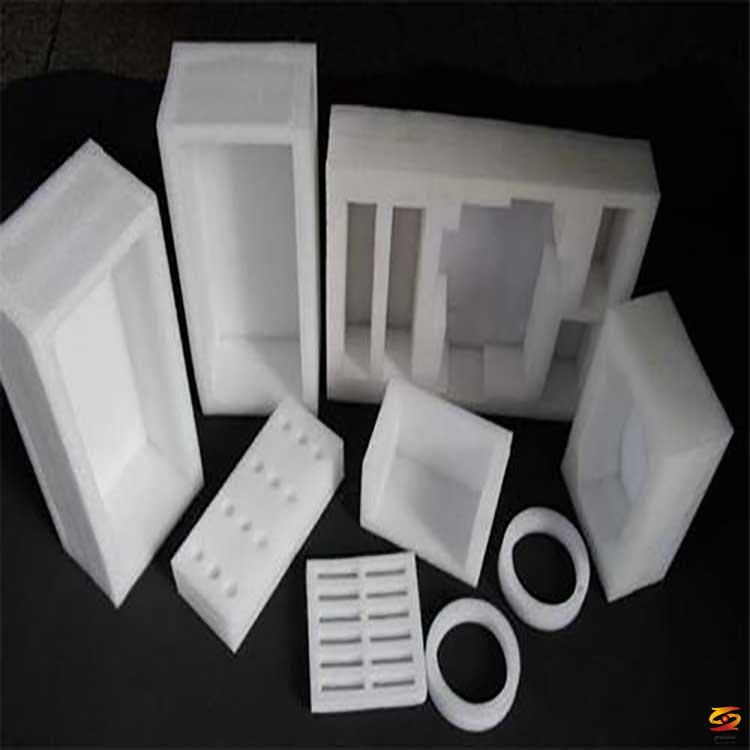
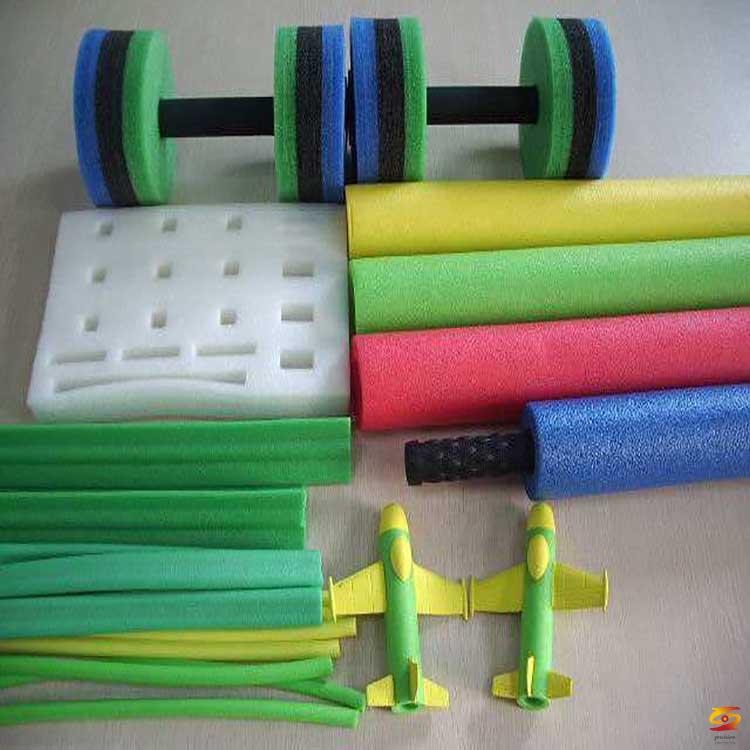
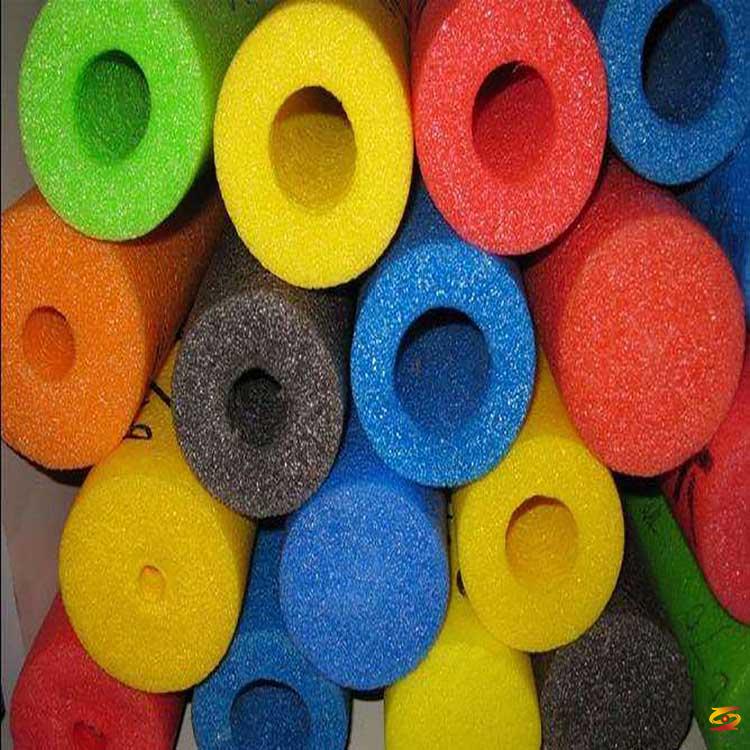
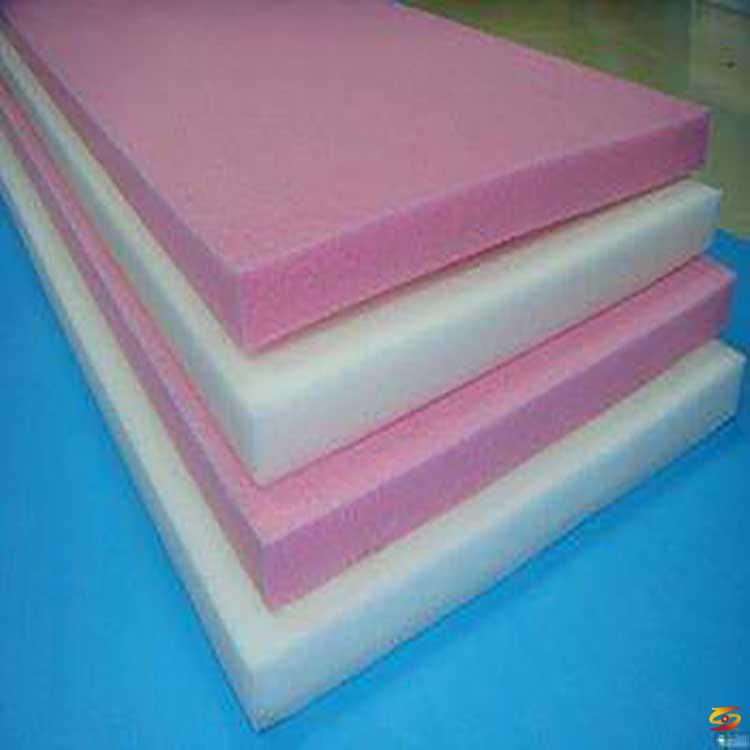