PVC granulator basic knowlege all we should learn
PVC granulatorThe main working mode of the PVC granulator is granule wet granulation. Through a certain amount of water or steam, the basic fertilizer is fully chemically reacted after adjusting the humidity in the cylinder. Under certain liquid phase conditions, with the help of the rotation of the cylinder, The squeezing force between the material particles is aggregated into a ball.
Chinese name PVC granulator output≤200-600Kg/h spindle speed 380/735r.p.m motor AC motor
table of Contents
1 Main features
2 Product introduction
▪ Technical parameters
▪ Upper-level machine
▪ Lower-level machine
▪ Machine model
3 Production process
4 matters needing attention
5 Troubleshooting
▪ Basic introduction
▪ Cause of failure
Main featuresedit
The main advantage lies in the use of steam heating to adjust humidity, increase the temperature of the granulated material itself, reduce the moisture of the granulation, reduce the load of the dryer, and improve the working efficiency. The pelletizing rate can be up to 70% by using the drum granulator, and the equipment is simple to operate, flexible and easy to maintain. The equipment is lined with ultra-high molecular weight polyethylene (UHMW-PE), which eliminates the sticking of materials, reduces the labor intensity of workers, and greatly extends the service life of the equipment.
Product introduction
200-elevation mixer-----500 type screw feeder----- twin-screw metering feeder——GLS-65 twin-screw——connecting body——∮GLD-150 single-screw extruder— —Integrated hydraulic plate type automatic screen changer — Air-cooled die surface hot-cutting granulation auxiliary machine — First-level cyclone separator --- Air-cooled vibrating screen (2.5m) --- Second-level cyclone separator - -——A set of wind blowing silo;
Technical Parameters
Yield................................................. ......... ≤200-600Kg/h
One-time feeding volume................................................ ..≤120Kg/h
Total volume/effective volume..............................300L/150L
Spindle speed.......................................... .....380/735r.pm
Speed mode............................................... ... change pole
way to heat up................................................ ..... self-friction
Material heating/heat mixing time..............................110℃/room temperature 10min
Discharging method...................................................... ......pneumatic
Discharge compressed air pressure..............................0.39~0.49MPa
electric motor................................................. .......AC Motor
Inner tube material................................................ .....stainless steel
Lid material.................................................. ..... cast aluminum Z102
Outlet material............................................. ...Cast aluminum Z102
Stirring material.................................stainless steel
Screw feeder................................................ ...500 screw feeder; the hopper is made of stainless steel;
Upper machine
Gearbox
1) The deceleration and torque distribution parts are integrated, and the structure is compact;
2) Needle roller bearings, radial bearings of the bearing deceleration torque distribution system;
3) The gears are made of high-quality alloy materials, and the precision is manufactured according to the accuracy of ISO1328-1995 cylindrical gears. All gears are made of carburized and hardened hard tooth surfaces. The gear profile is trimmed with special gear grinding software to ensure gear strength, uniform tooth load, high strength, low noise and low vibration.
Screw
1) The screw has a building block structure;
2) Mandrel material: 40CrNiMoA, threaded element and mandrel are involute connection; high strength, large load bearing, easy assembly and disassembly;
3) The threaded component material is high-quality high-speed tool steel W6MO5CR4V2, high temperature vacuum quenching heat treatment;
4) Overall hardness: HRC60-64;
5) The screw head and parallel cap connection are anti-tooth connection to ensure the connection is tight.
Barrel
1) Material: 45# steel is used as the base, and the inner hole of ∞ adopts high-quality double alloy bushing;
2) The first section cylinder is the feed cylinder, the sixth section cylinder is the natural exhaust cylinder, the ninth section cylinder is the vacuum cylinder, and the remaining cylinders are closed cylinders;
3) The cylinder is cooled by soft water;
4) Hexagon high-strength bolts are used for connection between cylinders;
5) Heating section: The feeding area is not heated, and the other uses high-quality cast aluminum heaters.
Inferior machine
Reducer: Adopt ZLYJ series high-precision hard tooth surface with thrust seat gear transmission device specially designed for single-screw rubber-plastic extruder. Design adopts various technical specifications stipulated in JB/T8853-2001 "Cylinder Gear Reducer" The output shaft is made of high-strength 42CrMo, and other gears and shaft parts are made of high-strength 20CrMnTi materials; the gears are processed by carburizing, quenching and tooth grinding processes, and the gears have high precision and high hardness; the gear precision is GB10095-88, grade 6, teeth The surface hardness is HRC-54~62, and the thrust bearing is arranged at the front end of the hollow output shaft to withstand the axial thrust when the screw is working. The whole machine has small size, high bearing capacity, stable transmission, low noise and high efficiency. When the oil level is lower than the oil mark position, please add medium-load industrial gear oil L-CKC220 or L-CKC320 (oil products need to be purchased by the customer).
Screw
1) The material is 38CrMoALA nitriding treatment, nitriding HV950-1050, depth 0.6-0.75mm, brittleness is not more than grade II, the surface of the screw is hard chrome plated;
2) The core of the screw adopts water cooling
Barrel
1) The material is 38CrMoALA nitriding treatment, nitriding HV950-1050, depth 0.6-0.75mm, brittleness not more than grade II;
2) The screw cylinder adopts water cooling;
3) Slotted on the cylinder body, coiled copper pipe, through which cooling water is passed;
4) A protective cover is added to the screw barrel, which is made of stainless steel;
5) Heating section: using high-quality cast aluminum heater
6) The machine head is heated by a mold temperature machine
4. Eager auxiliary machine:
1) Air-cooled die-face hot-cutting granulator: 4-stage motor, one set of hot-cutting knife and one motor coupling, hot-cutting uses 4 blades to cut pellets
2) Speed control: adopt frequency conversion speed control;
3) Pelletizing hood: pair blown type, stainless steel material; one piece; push-pull structure; with brake device; there is enough space for separating the heat cutting hood from the machine head; easy to operate; the pair of blown type heat cutting hood is integrated with the bed
4) First-class cyclone separator: φ800mm, stainless steel material; one piece; using φ160mm stainless steel pipe connection;
5) Two-stage cyclone separator: φ800mm, stainless steel material; one piece; using φ130mm stainless steel pipe connection;
6) Lengthened vibrating screen: one set, L=2.5m, the motor adopts: special motor for vibration; the amount of vibration can be adjusted: two motor powers; the vibrating screen uses three layers of separated materials; the diameter of the large hole is φ8mm and the diameter of the small hole φ2.5mm, stainless steel material,
7) Wind blowing silo: one set, 1m3 silo one piece, stainless steel material; using φ130mm stainless steel pipe connection;
Machine model
model
Equipment series
Screw diameter
MM
Aspect ratio
Screw speed
(rpm)
main motor power
(KW)
Screw torque (N.M)
Torque level
GLS-52
A
50.5
32-64
500
45
405
5.1
B
600
55
415
5.2
C
500
75
565
7.1
D
600
90
680
8.5
GLD-100
100
9
86
37
1
1
GLS-65
A
62.4
32-64
500
55-75
680
4.8
B
600
75-90
680
4.8
C
500
110
830
5.9
D
600
160
1200
8.5
GLD-150
150
9
86
55
45
65
GLS-75
A
71
32-64
500
90-110
995
4.6
B
600
110-132
995
4.6
C
500
160
1200
5.5
D
600
250
1890
8.7
GLD-180
180
9
86
75
75
85
GLS-75B
A
71
32-64
500
90-110
995
4.6
B
600
110-132
995
4.6
C
500
160
1200
5.5
D
600
250
1890
8.7
GLD-200
200
9
86
90
2150
12.5
Production Process
PVC cable material is a general term for cable materials made of polyvinyl chloride (Polyvinylchloride, PVC). As a traditional cable material, it still occupies the most important market share in the current domestic market. Because its processing is relatively simple compared to other cable materials, and the amount is relatively large.
Production Process:
Raw materials and various additives are added according to a certain proportion and added according to the process sequence -----200-elevating mixer -----500-type screw feeder--twin screw metering feeder- -65 twin screw-connecting body-∮-150 single screw extruder-integrated hydraulic plate type automatic screen change-air-cooled die surface hot cutting granulation auxiliary machine-first-level cyclone separator-wind Cold vibrating screen (2.5m)----- Two-stage cyclone separator---a set of wind blowing silo
Formula of PVC cable material
70H-PVC cable material formula such as PVC type 75PHR--active calcium carbonate 35PHR---DOP (plasticizer) 25PHR---epoxy soybean oil soybean oil 3PHR--chlorinated paraffin 20PHR--stabilizer 2.8PHR- -Hard acid 0.6PHR - CPE 9PHR --- Paraffin 1PHR
(1) Preparation: Stabilizer, filler and colorant are sieved through an 80-mesh sieve, and then added with plasticizers respectively and saturated with a three-roll mill or colloid mill. Reserve after weighing. After the plasticizer is mixed evenly, preheat it at 90℃ for use;
(2) High-mixing machine: Put in PVC resin, then add plasticizer and stir for a while. After the resin basically absorbs the plasticizer, add stabilizer, and increase the temperature of the material to about 90℃ by frictional heat, then add filler, Colorant, when the material temperature rises to 110 ℃, discharge the material to the cooling mixer to cool down, and discharge the material to below 45~50 ℃.
(3) Stable setting of PVC granulator:
1) Upper-stage twin screw temperature setting: between 140 and 160 degrees; different temperature settings according to different materials;
Temperature table
Temperature table
2) Stable setting of lower single screw: between 125 and 145 degrees; different temperature settings according to different materials;
3) The setting on the temperature control table (see the picture on the right) is good. Only after the actual temperature reaches the set temperature, keep it for 40 minutes before starting production. This is to ensure that there are materials left in the previous day in the equipment, so that the previous day can be saved The material left behind is softened so that it does not hurt the equipment.
(4) Production:
1) After the PVC material of the high-mixer is put into the hopper of the screw feeder, the powdered material is put into the upper parallel twin screw extruder through the screw feeder
2) The upper-stage parallel twin-screw extruder mixes the materials uniformly, and completes the plasticization and kneading under the state of the temperature of 140-160°C, and fully disperses them evenly. Finally, the extruded mixture becomes a melt (temperature is 130-140°C) and falls directly into a large-diameter lower-stage single-screw extruder.
3) The lower-stage single-screw extruder completes the extrusion and granulation of the melt at 120°C under low speed, high pressure and cooling. During extrusion, the temperature has dropped to 120-140°C. At this time, the air-cooled die surface can be hot cut, and the grain is not sticky during the cutting process.
4) The particles eagerly cut by the air-cooled die surface are cooled by the secondary air-cooled cyclone separator, and the particle temperature is reduced to 35-40 ℃, and then the air-cooled lengthened vibrating screen is used to reduce the particle temperature to room temperature for feeding into the finished product. Silos for packaging.
Range of use
Cable material processing and granulation PVC processing and granulation PVC cable material processing and granulation
Precautions
1. The main motor and the oil pump motor are electrically interlocked, that is, the oil pump motor does not start, the main motor cannot start; the main motor does not stop, the oil pump motor cannot stop.
2. The main motor and the feeding motor are electrically interlocked, that is, the main motor does not start, and the feeding motor cannot start; the main motor of the feeding motor does not stop, and the main motor cannot stop.
3. The main motor control cabinet has overcurrent protection, in addition, it also has a mechanical protection device, generally a nylon shear pin type safety coupling. When the design torque is exceeded, the shear pin is cut off and the transmission box stops working.
4. When the pressure of the machine head exceeds the set alarm value, the material pressure alarm signal light will turn on and stop automatically.
5. The raw materials produced by users are strictly prohibited to bring any metal debris.
6. When the machine is running, it is strictly forbidden to use metal objects to clean the materials at the opening of the cylinder.
7. Assembly and disassembly of pressure sensor and material temperature thermocouple. When there is material in the machine head, it must be heated, and installation and disassembly can only be carried out after the material softens.
8. For the circulating water of the cylinder cooling system, please use demineralized water or distilled water.
9. The screw is only allowed to start at low speed (≤20r/min), and the idling time does not exceed 2 minutes. After feeding, the standby head die hole is discharged to gradually increase the speed.
Troubleshooting
basic introduction
The extrusion granulation unit integrates machine, electricity and instrument highly, and the level of automation control is high. Therefore, in actual operation, there will be more failures that are difficult to diagnose, resulting in a long processing time, which affects the normal operation of the entire polypropylene plant and greatly reduces the economic benefits of production. The author combines the theoretical knowledge of the extrusion granulation production process and the actual production and operation of more than ten years
Management experience, analysis and judgment of the common causes of failure of the unit during operation, and formulated corresponding solutions and treatment methods to ensure its long-term stable operation.
Dalian Petrochemical ZSK250 extrusion granulation unit in a 70,000-ton/year polypropylene plant
cause of issue
In the extrusion granulation unit, the friction clutch disengages during the operation of the extrusion granulation unit, and the reasons for the interlocking of the unit can be divided into four categories:
Main motor system failure
1. The torque of the main motor is too high or too low;
2. The speed of the main motor is too low;
3. The temperature of the main motor bearing is too high;
4. The temperature of the main motor winding is too high;
5. The temperature at the entrance and exit of the main motor water-cooled cooler is too high;
6. The outlet flow of the main motor bearing lubricating oil pump is too low;
7. The outlet pressure of the main motor bearing lubricating oil pump is too low;
8. The water leakage of the main motor water-cooled cooler is too high.
Transmission system failure
1. The gearbox shift lever is out of position;
2. The instrument wind pressure of the friction clutch is too high;
3. The friction clutch speed difference is too large;
4. The outlet pressure of the gearbox lube pump is too low;
5. The oil temperature of the gear box lubricating oil pump is too high;
6. Internal failure of the friction clutch, etc.
Failure of screw process section of extrusion granulator
1. The melt pressure before and after the throttle valve is too high;
2. The melt pressure of the machine head is too high;
3. The pressure difference of the melt before and after the screen changer is too large;
4. The turning failure of the driving valve, etc.
Underwater pelletizing system failure
1. The winding temperature of the pelletizing motor is too high;
2. The speed of the pelletizer is too low;
3. The torque of the pelletizer is too high;
4. Automatic switching failure of the bypass of granular water;
5. The particle water pressure is too high or too low;
6. The flow of particle water is too low;
7. The clamping bolt of the pelletizer is not tight;
8. The bypass water valve of the pelletizing room is not closed;
9. The hydraulic clamping pressure of the pelletizer is too low;
10. Failure of pelletizing motor;
11. The axial feed pressure of the hydraulic cutter is too low.
Among the causes of the above failures, the most frequent ones are: the main motor torque of the main motor system is too high or too low; the friction clutch of the transmission system is faulty; the melt pressure of the screw process section system of the extrusion granulator is high; the underwater cutting Granulator system failure, etc. The following will analyze these common fault causes in detail and give corresponding solutions.
Main motor torque is too high
Cause Analysis:
Failure of the oil lubrication system, poor alignment of the main motor output shaft and the gearbox access shaft, motor and clutch vibration will damage the main motor bearings, resulting in excessive torque. In addition, excessive feeding load or poor material fusion will also cause the main motor torque to be too high.
solution:
Regularly check and clean the lubricating oil system, measure the main motor bearings with a vibration measuring instrument and infrared thermometer and form a trend chart. If the trend value is exceeded, determine whether the main motor idling current value or power value exceeds the specified value, and determine whether the bearing should be replaced. Regularly check the alignment between the output shaft of the main motor and the input shaft of the gearbox. The alignment must be checked after running for three months after the first drive or bearing replacement. Conduct electrical test inspection to determine the cause of rotor imbalance; perform vibration speed test on the clutch, and if it exceeds the specified value, the dynamic balance should be readjusted. Regularly check the cylinder heating and cooling system to ensure that the material is heated and melted evenly. If the power curve of the main motor and the melt pressure curve increase instantaneously when the extruder starts, it indicates that the feeding amount of the feeding system is too large instantaneously, and the feeding amount should be reduced.
Main motor torque is too low
Cause Analysis:
Failure of the feeding system to cause the twin screw to idle will cause the main motor torque to be too low.
solution:
Check to see if the additive system or the main material unloading system is faulty, and clear the clogged points.
Friction clutch failure
Cause Analysis:
The instantaneous starting voltage of the main motor is too low, the friction disk and the friction plate are overheated, the friction disk and the friction plate are aging, and the air pressure of the friction disk is too low. The clutch can be disengaged.
solution:
When the main motor is started, the peak power consumption should be avoided, and the feeding load should be reduced. The minimum restart interval is 30 minutes; in summer, when the main motor is started more than twice, the interval should be extended or forced by a fan. Cool down. Use the instrument wind to blow and wipe the ash marks on the surface of the friction plate and friction disk with a rag. If the wear is heavy or the phenomenon of "vitrification" occurs on the surface, the friction disk and friction plate should be replaced. Confirm whether the air pressure value can make the friction disc and the friction plate fit together.
High melt pressure
Cause Analysis:
High filter mesh number, low polypropylene powder melt index and large feeding amount, low barrel temperature of each section makes the material not completely melted, low template opening rate makes the extrusion of the head material blocked and other reasons can cause melt pressure Too high.
solution:
When producing low melt index products, a low-mesh filter should be used to increase the opening of the throttle valve to reduce back pressure; the filter should be replaced in time to monitor the quality of various additives and the ash content in the polypropylene powder. Reduce the feeding load. Without affecting the quality of the extruded product, increase the temperature of the cylinders in each section to increase the temperature of the polypropylene melt and increase the fluidity of the material. After the extruder stops, increase the temperature of the machine head and keep it at a constant temperature for a period of time, then thoroughly rinse and clean the template.
Underwater pelletizing system failure
Cause Analysis:
Excessive cutter wear or cutter edge damage, particle water flow is too low, granulator vibration is too large, cutter and template are not tightly attached, material melt index fluctuates greatly, resulting in inconsistent discharge flow rate, particle water temperature is too high, etc. Can cause the underwater pelletizing system to stop and cause the entire unit to interlock and stop.
solution:
After parking, visually inspect the cutter blades for excessive wear or damage, and if so, replace the cutters completely. Check and confirm whether the particle water is leaking, whether the filter and cooler of the particle water tank are blocked. If the blockage should be cleaned manually, check whether the inlet and outlet pressure of the particle water pump is normal. If it is abnormal, the valve on the particle water pump and the pump pipeline should be repaired. Check whether the alignment between the cutter shaft and the pelletizing motor is out of tolerance, whether the bearing assembly of the cutter shaft is damaged, and whether the dynamic balance of the cutter rotor is unbalanced. During operation, check whether there is any gap between the four moving wheels of the pelletizing trolley and the guide rail. Control the volatile content of polypropylene powder to eliminate the vibration of the cutter and cutter shaft when flowing through the template hole. Reduce the temperature of hot oil at the template, check the temperature distribution of the cylinder and the template, whether the flow rate, pressure and temperature of the cooling water of the cylinder are normal; confirm the time setting of "water, knife, material" reaching the template to prevent premature particle water Reaching the template freezes the template hole. After closing the head, the pelletizer should quickly increase the feeding amount to the set load of the extruder.
If the above fault cause points and the logical relationship of interlocking can be combined to compile fault diagnosis software, it can provide quick and intuitive reference and help for the operation, maintenance and management of the unit.
If you want to know more about it please do not hesitate to
contact me. WhatsApp:+86-15966835076.
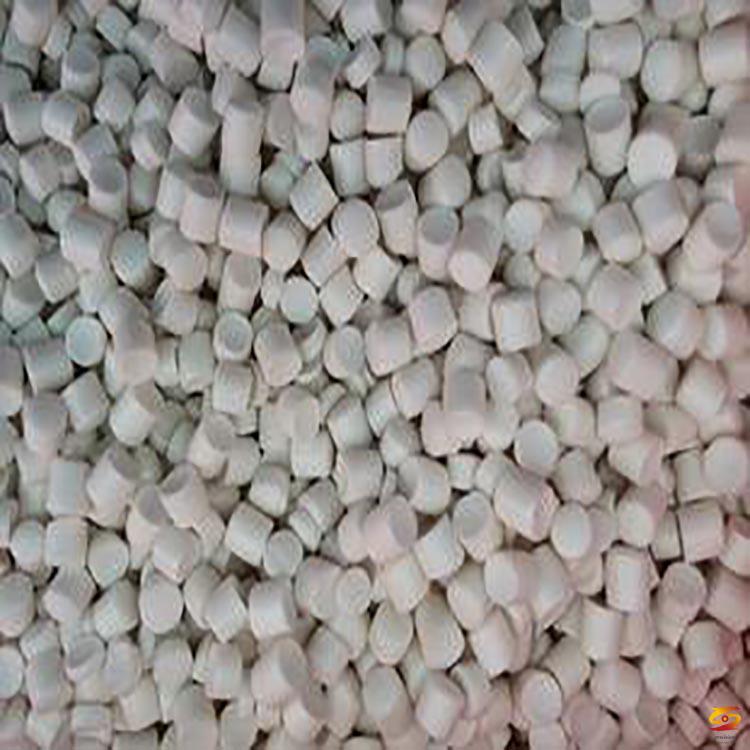
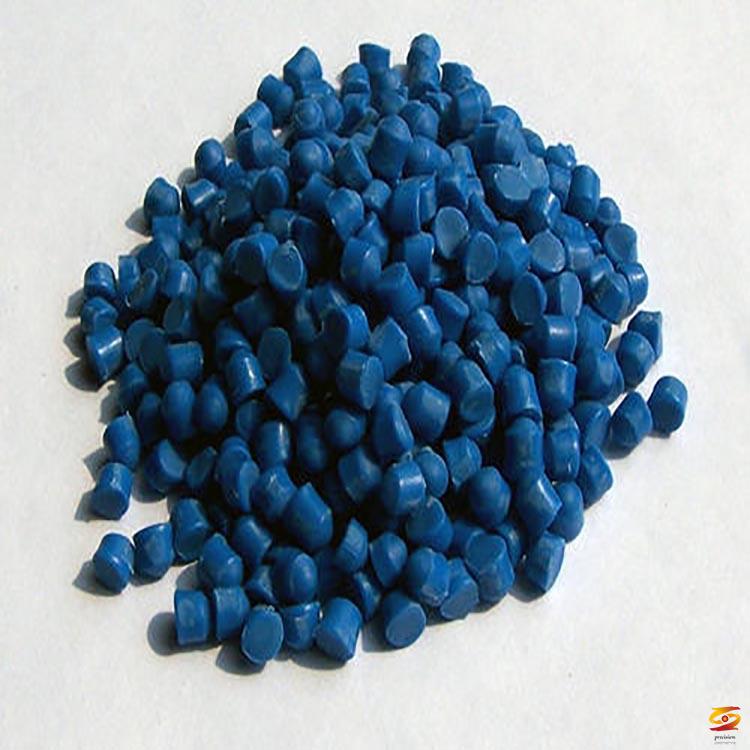
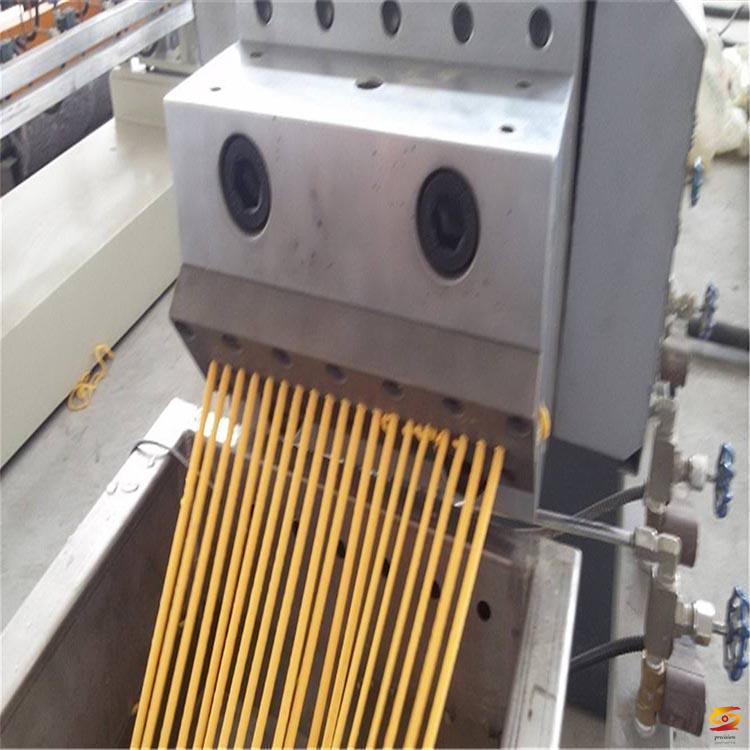
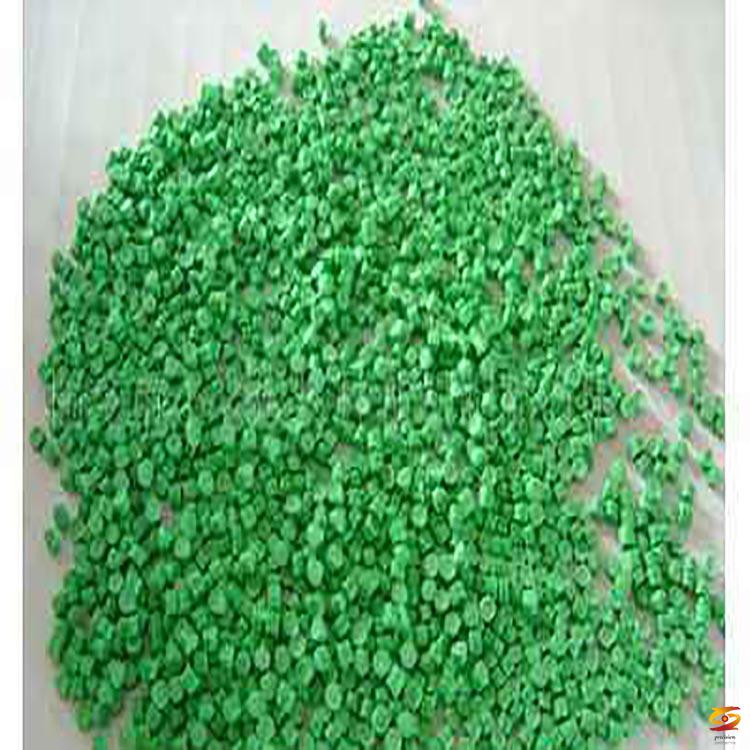