PVC wood plastic crust foam building template Project feasibility proposal
PVC wood plastic crust foam building template Project feasibility proposalFeasibility report of PVC foam board as building template
table of Contents
Preface
1. Introduction and market prospects of wood-plastic building formwork projects
2. Production process and flow chart of wood-plastic building template
3. Whole plant production equipment for wood-plastic building template
4. User-supplied projects and equipment installation and commissioning
5. Feasibility analysis of PVC wood-plastic building template project
Six, PVC wood plastic building template equipment supporting plan
7. Quality and Service Commitment
Preface
Our company is located in the beautiful coastal city of Jiaozhou City, Qingdao. It is a modern technology enterprise integrating science, industry and trade. The main products are SPC stone plastic floor equipment, various hollow product processing equipment, and plastic pipe sheet sheet profile extrusion production lines. All kinds of plastic machinery, molds and plastic products, the products are spread all over the country and more than 50 countries and regions in the world. For many years, the company has always followed the idea of customer first and quality first, providing users with high-quality plastic machinery and equipment and a full range of services, and enjoys a high reputation in the same industry at home and abroad.
Our company has developed wood-plastic machinery and equipment with international advanced level. The wood-plastic products produced make full use of abundant wood side materials, crop straws, plastic waste, etc. to realize "wood-plastic replacement" and protect limited forest resources. , Reducing "white pollution", is a national key promotion project. Used by users at home and abroad, it has won high praise and trust from customers.
1. Introduction and market prospects of PVC wood-plastic building template project
(1) Product background
Building template is an important tool for concrete structure engineering construction. In cast-in-place concrete structure engineering, formwork engineering generally accounts for 20%-30% of the concrete structure engineering cost, 30%-40% of the engineering labor cost, and about 50% of the construction period. Formwork technology directly affects the quality, cost and benefit of project construction, so it is an important content to promote the progress of my country's construction technology.
At present, the main formwork for construction in my country is wood formwork. According to the statistics in 2009, the market size of wood plywood formwork was 300 million square meters, its annual output was 77.3 million square meters, and the market size of bamboo plywood formwork was 122 million square meters. The annual output is 31.4 million square meters. At present, China's total timber demand is more than 100 million cubic meters, while the market supply is only more than 60 million cubic meters, with a gap of about 40 million cubic meters. The formwork alone requires more than 3 million cubic meters of wood. my country's timber resources are scarce, and importing timber will cost a lot of foreign exchange. At present, there are two ways to solve this problem: on the one hand, it is to encourage the import of wood; on the other hand, it is to seek wood substitutes through the research and development of new materials. Wood-plastic template has become the preferred substitute. Many foreign countries such as the United States and Canada have invested heavily in the development of wood-plastic projects.
The production scale of my country's construction formwork industry will maintain a growth rate of about 10% in 2010; the average annual growth rate of production scale of my country's construction formwork industry will be around 15% from 2011 to 2012; by the end of 2012, the output of my country's construction formwork industry will reach 220 million About square meters. The average annual total demand for construction formwork panels is conservatively calculated to be more than 200 billion yuan, and it is increasing at an average annual rate of 9-12%. In the next 2-3 years, wood-plastic building templates will occupy 30%-50% of the market share, and the output value will reach about 60-100 billion. The market prospect is very broad.
(2) Performance comparison of common building templates
1. The wooden formwork was the first to be used. Because a large amount of wood is consumed, and the disassembly formwork is easy to split, the loss rate is relatively high, and the general turnover is 4-6 times. For our country where forest resources are not abundant, we should seek alternative products.
2. Steel formwork: The advantage is that it can save a lot of wood, but it also has many unsatisfactory points:
(1) The cost is high, the average price is 280 yuan/square meter, which is much higher than the price of wood-plastic template;
(2) Bulky, inconvenient construction and lifting, and difficult to disassemble. The area of a single template is not large, and there are many splicing blocks in use, which is time-consuming and laborious;
(3) The steel formwork has a strong affinity with cement. When the formwork is removed, it is easy to peel off the surface of cement products such as columns or beams, which affects the quality;
(4) The steel template is easy to rust.
3. Advantages of PVC wood plastic building template:
①Can save a lot of wood;
②It has advantages in convenience and safety of construction;
③WPC does not require maintenance and can be recycled, so production costs can be greatly reduced, and many key problems in engineering can be solved.
(Three) PVC wood plastic template performance and advantages
Wood plastic formwork processing WPC formwork application
PVC wood-plastic template is a new type of environmental protection material compounded by plant fiber and PVC resin.
The annual output of plastic products in my country exceeds 40 million tons. Ranked second in the world, about 13.84 million tons of waste plastics are produced every year. The output of domestic agricultural plant fiber is tens of millions of tons, wood materials are more than 1 million tons, and other natural fibers are also 5-10 million tons, which provides a rich raw material foundation for the development of my country's PVC wood-plastic template.
1. Features of PVC wood-plastic composite materials:
(1) There are wide sources of materials and low value.
(2) Wood-plastic products are artificial overall synthetic products, and the product process and formula can be adjusted randomly according to the requirements of use, so as to produce materials with different properties and shapes, and the utilization rate of its profile is close to 100%.
(3) The wood/plastic base material of PVC wood plastic material and its commonly used additives are environmentally safe, non-toxic and harmless, and there will be no side effects during the production and processing process, so it does not pose any harm to the human body and the environment.
(4) The maintenance cost is extremely low, and the product life span is several times that of ordinary natural wood,
(5) Scrap products and recycled waste products of PVC wood plastic materials can be 100% recycled, and will not affect product performance.
2. Advantages of PVC wood plastic building template
(1) There are wide sources of raw materials, low overall cost, and certain competitiveness in the market;
(2) The basic performance is equivalent to that of wood, which can be sawn, nailed, and corrosion-resistant, and its products have better durability than wooden and bamboo building templates;
(3) The product assembly is flexible and can be changed according to the specific requirements of the market and users;
(4) High reuse rate and recyclable;
(5) Not afraid of insect bites, acid and alkali resistance, aging resistance, not easy to absorb water, and easy to peel off from concrete.
(4) Performance and price comparison between PVC wood plastic building template and mainstream template:
Performance item
Wood material
Steel material
All plastic material
Plastic wood composite
proportion:
G/cubic centimeter
0.8-1.1
7-8
0.9-1.1
0.6-0.7
Rigidity and load capacity
Higher
high
low
Higher than wood and
All plastic material
Machinability
easy
Not easy
not easy
easy
Durability
limited
(Easy to corrosion)
limited
(Easy to corrosion)
Higher
High (7-10 times
Wood material)
Water absorption
high
Does not absorb water
Does not absorb water
Does not absorb water
Solar aging resistance
it is good
it is good
difference
it is good
Acid and alkali resistance
difference
difference
excellent
excellent
Resistance to environmental pollution
Poor
better
it is good
it is good
Maintenance frequency
And difficulty
high
Convenience
Lower
Difficult to repair
Lower
Not repairable
low
Convenience
Recyclability
difference
difference
Recyclable but performance
Lower
100% renewable
Disposal of waste materials
Abandoned or
Payment recovery
Harder,
Payment recovery
Lower price entry
Waste plastic market
Can be traded in
Use safety
(Spiked wood thorns, etc.)
difference
Poor
it is good
it is good
Structural size flexibility
high
low
low
highest
Handling with existing logistics
Equipment adaptability
high
Difficult
Difficult
high
Automated logistics handling
Equipment adaptability
difficult
it is good
difficult
it is good
2. Production process and flow chart of wood-plastic building template
(1) Production process route
Wood flour+PVC resin+auxiliary---extrusion--sizing--cutting--packing
(2) Production process flow chart
raw material
↓
→ mix
↓
Put into the hopper ↓
Melt plasticization
↓
Extrusion through the die
↓
Shape cooling
↓
Traction
↓
Cut to length
↓
Shattering and recycling of defective products ← Qualified products are put into storage
(3) Production process description
First, put PVC, wood flour, filler and other functional additives into the high-speed mixer, mix evenly and put them into the hopper of the extruder through the screw automatic feeder. At the same time, the temperature of the extruder is preset and kept warm. Exit the machine to melt and plasticize the raw materials. Ruijie people extrude into the shaping device through a special die to cool and shape, and pull it out by traction, enter the automatic cutting machine to automatically cut to the stacking rack according to the preset length, and store qualified products, defective products and leftovers Reuse after crushing and grinding.
(4) Main raw materials
1. PVC
2. Wood flour
3. Filler
4. Functional additives
3. Whole plant production equipment for wood-plastic building template
(1) Equipment composition
1. SRL-500/1000 plastic heating and cooling mixing unit
2. SJFB-Z80X22 PVC wood plastic crust foaming building formwork unit
3. SWP-500 plastic crusher
4. SMP-400 high-speed vortex mill
(2) Detailed technical parameters
1. SRL-500/1000 plastic hot-cold mixing unit, feeder
The plastic hot-cold mixing unit is mainly used for the mixing, drying and coloring of raw materials. The pot body is welded by stainless steel. There are heating jackets and electric heaters on the surface of the pot.
Model SRL-500/1000
Total volume of hot mixing 500L
Effective volume 370L
Each feeding amount 150-200kg/pot
Mixing time 6-15 minutes
Hot mixing paddle speed 860r/min
Thermal mixing motor power 55/67KW two-speed motor
Heating method Electric heating, self-friction
Temperature control method Digital display intelligent temperature control instrument
Total volume of cold mix 1000L
Effective volume of cold mix 650L
Cold mixing motor power 11KW
Rotating speed of cold mixing slurry ≤60r/min
Blade material Stainless steel integral casting structure
Lid opening control Pneumatic control
Discharging method Pneumatic valve discharge
2. SJFB-Z80X22 PVC wood plastic crust foaming building formwork unit
a. Automatic feeding machine
b.SJ-Z80X22 special conical twin screw extruder for wood plastic
SJ-Z80 wood-plastic conical twin-screw extruder is an efficient wood-plastic extrusion equipment developed by Qingdao Ruijie. Segmented fault alarm for easy detection. The high-performance deceleration torque distribution system ensures the reliable operation of the equipment. The optimized design and carefully made screw barrel has excellent plasticizing effect. The host is equipped with a PID intelligent temperature control system and automatic temperature control. Equipped with vacuum exhaust, forced feeding mechanism and other devices.
Screw material 38CrMoAl high-quality alloy steel is nitrided twice, and the front end is treated with bimetal
Screw diameter Φ80/156mm
Effective length 1800mm
Quantity 2
Speed 1-36.9 r/min
Nitriding depth 0.5-0.7mm
Barrel material 38CrMoAl high-quality alloy steel is nitrided, and the inner wall is drawn groove sprayed with bimetallic treatment
Heating method: cast aluminum electric heating
Heating zone 5 zone
Heating power about 28KW
Temperature control method Imported brand temperature control instrument, PID intelligent automatic control
Cooling method Fan cooling
Cooling power 4×0.55KW
Host drive power 75KW
Motor speed regulation method
Gear box form Gear material adopts 20CrMoTi grinding and nitriding treatment
Distribution box form Gear material adopts 38CrMoAlA gear grinding and nitriding treatment
The connecting shaft is made of 40Cr, and the bearing is imported
Feeding method: screw automatic quantitative feeding
Screw speed 0-34r/min
Motor power 1.5KW
Speed regulation mode Inverter speed regulation
Vacuum pump form Water ring vacuum pump
Motor power 4KW
Vacuum degree -0.06Mpa
c. Extrusion die
Form Clothes hanger mould
Die material is made of high-quality stainless steel forgings and the inner runner surface is polished
Mold cavity Polished to a bright mirror surface
Die lip with adjustable bolt
Heating method adopts stainless steel electric heating rod to heat
Mold width 1320mm
Product width 1220mm
Product thickness 3~20mm
Temperature measuring element Thermocouple
Mould trolley, bracket type, with walking wheels
d. Foam board forming machine
Vacuum shaping cooling mold size: 1500mm×600mm
Number of vacuum shaping cooling molds: 4 groups (8 pieces)
Upper shaping cooling mold lifting method: pneumatic
Cooling method: water cooling
Shape thickness adjustment: 3-20mm adjustable
Front and rear walking unit Worm gear drives rack and pinion
e. Roller supporting cooling device
Roller diameter X effective length: 80X1400mm
Number of rollers: 20
Vertical arrangement length: 5000mm
f. Edge trimming device
Cutting method: electric saw blade type and blade type two structures.
Sawing motor power: 1.1KWX2 sets
Trimming width: adjustable
Vacuum cleaner motor power: 1.5KW
g. Tractor
Traction roller diameter X effective length: 220X1400mm
Number of traction rollers: 16
Hauling speed: 0-2m/min
Drive motor power: 11Kw
Speed regulation method: frequency conversion speed regulation
Maximum traction: 100KN
h. Cutting machine
Maximum cutting width: 1400mm
Maximum cutting thickness: 20mm
Cutting motor work
Rate: 3Kw
Action: Linkage with length counting device, automatic cutting according to set length, automatic control.
Vacuum cleaner motor power: 1.5KW
i. Material accumulation platform
Vertical length: 3000mm
3. SWP-500 plastic crusher
Number of rotating knives: 9 pieces
Number of fixed knives: 2 pieces
Rotary knife fixed knife material: 9SiCr
Sieve plate aperture: 5-12mm
Feeding port size: 530mmx400mm
Broken size: 3-12mm
Output: 150-300Kg/h
Drive motor power: 15Kw
4. SMP-650 high-speed vortex mill
Grinding chamber diameter: 390mm
Spindle speed: 3000r/min
Drive motor power: 55Kw
Output: 400-600Kg/h
4. User-supplied projects and equipment installation and commissioning
(1) User-provided items
1. Public facilities
A. Power facilities
Power 380V×50HZ ×3 phase
Total installed capacity 250KW
B. Air source
Air pressure 0.7Mpa 0.5-1.0m3/min
C. Water source
Circulating water 10m3/h 15℃
2. Civil works such as plant and equipment foundation
3. Installation tools, including lifting tools, spirit level, etc.
(2) Installation and commissioning
1. The unit should be placed in a good place with a ground concrete foundation greater than 30cm.
2. The extruder can be fixed with M16 metal expansion bolts, and the rest are laid flat on the ground and not fixed.
3. Place each part of the equipment according to the layout drawing of the production line and calibrate the centerline and level of the unit. The distance between auxiliary machines can be adjusted appropriately according to the workshop site conditions. Auxiliary equipment such as electric control box and mixer shall be placed in a convenient place for operation and maintenance according to actual conditions.
4. The electrical appliances of the unit must have good grounding protection.
5. After the installation is completed, connect the electricity, water and gas pipelines.
6. Check whether the parts are loose or falling off.
7. Check whether the rotation of each transmission component is normal.
8. Debug each part of the equipment separately, and then enter the whole machine debugging after the operation is normal.
5. Feasibility analysis of PVC wood-plastic building template project
(1) Basic composition of raw material formula and raw material cost analysis:
1. Analysis of basic composition of raw material formula:
Name Percentage Reference Price
PVC resin powder 10% 6300 yuan/ton
Wood flour 5% 700 yuan/ton
CaCO3 25% 900 yuan/ton
Functional additives 10% 15,000 yuan/ton
Recycled material 50% 3500 yuan/ton
Total raw material cost: 4140 yuan/ton
2. Analysis of processing cost: electricity fee + labor + water consumption + other = about 600 yuan/ton
3. Total cost: 4140 yuan/ton+600 yuan/ton=4740 yuan/ton=4.74 yuan/kg
4. The cost of a single board (take 1830×915×15mm board as an example, weight 16.5 kg): 4.74 yuan/Kg×16.5Kg/piece=78.21 yuan/piece
(2) According to the profitability analysis of a production line, the number of employees and the tax paid to the state:
1. Output value: calculated at 500 sheets/day
Annual output: calculated on the basis of 300 days of annual production, an annual output of 150,000 sheets
Annual production value: 150000×120 yuan/sheet = 18000000 yuan (calculated based on the current market price of 120 yuan/sheet)
2. Annual profit: 150,000 sheets × (120 yuan / sheet-78.21 yuan / sheet) = 6,268,500 yuan
3. Number of labors: 4 workers are employed per shift, and production is divided into 2 shifts every day, totaling 8 workers
(3) According to the normal business scale of the company, five production lines are needed to meet the market demand of a county. If the sales channels radiate to surrounding counties and cities, the business scale of the company will need to be expanded accordingly. Calculated according to the company's operating scale of 5 production lines:
1. Annual production value: 18 million yuan × 5 production lines = 90 million yuan
2. Annual profit: 6,268,500 yuan × 5 production lines = 3,1342,500 yuan
3. Number of employees: a total of 52 jobs can be provided for the society
Production workers: 8 people × 5 production lines = 40 people
Sales staff: 5
Logistics management staff: 6
Technical staff: 1
Six, PVC wood plastic building template equipment supporting plan
Serial number
Equipment name
unit
Quantity
unit price
(Ten thousand yuan)
use
1
SRL-500/1000 Plastic Heating and Cooling Mixing Unit
station
1
Plastic wood powder mixing, drying, coloring, etc.
2
SJFB-Z80X156 PVC wood plastic crust foaming building formwork unit
station
1
Production width 1220mm wood plastic board
3
SWP-500 plastic crusher
SMP-650 High Speed Eddy Current Mill
station
Each 1
Crushing and recycling scraps
PVC wood-plastic foam board production line equipment can also produce current net mahogany wood veneers, furniture boards and advertising lettering boards.
If you want to know more about it please do not hesitate to
contact me. WhatsApp:+86-15966835076.
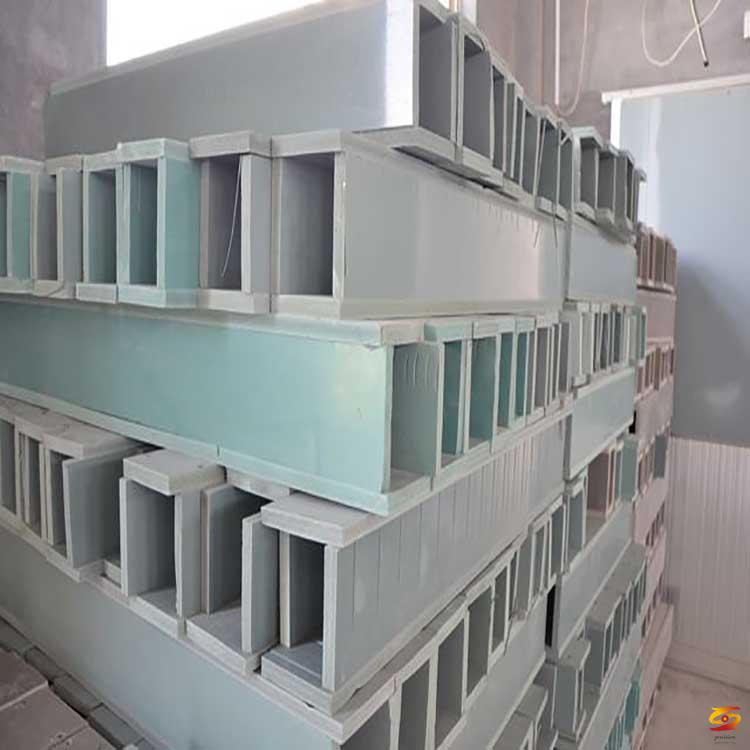
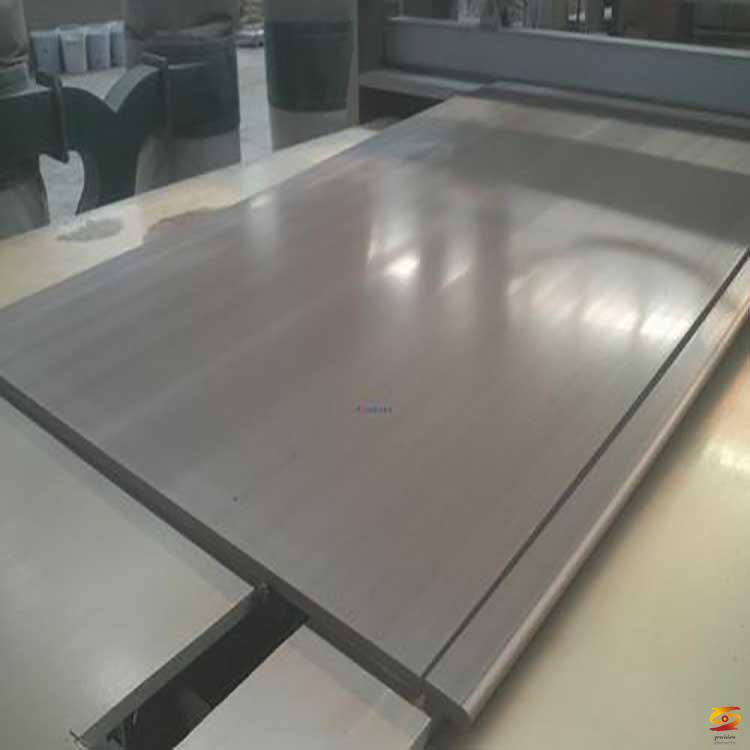
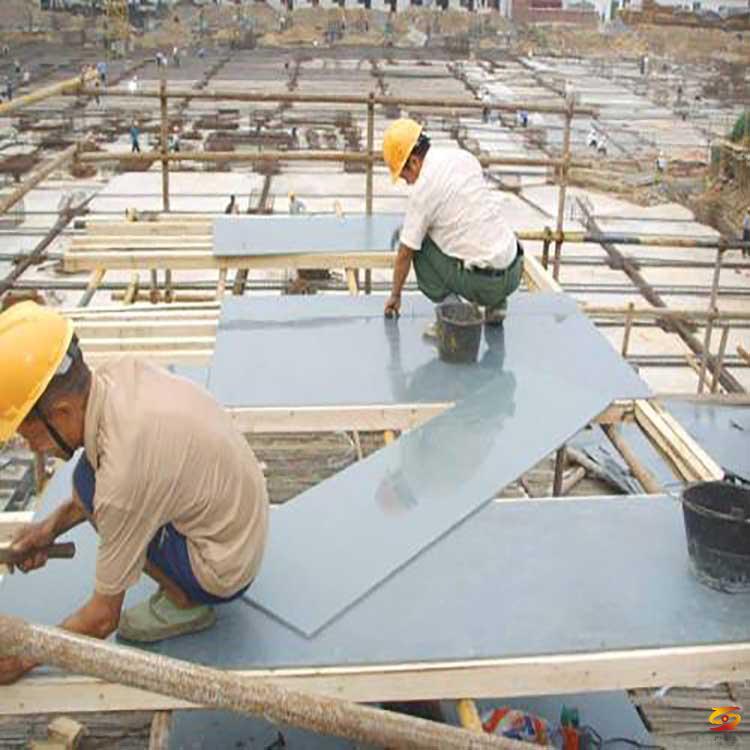
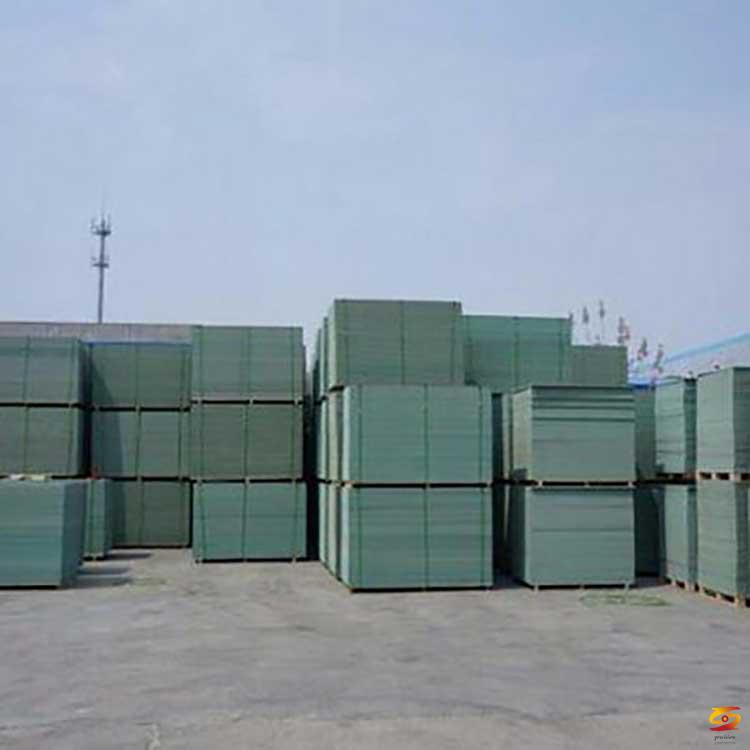
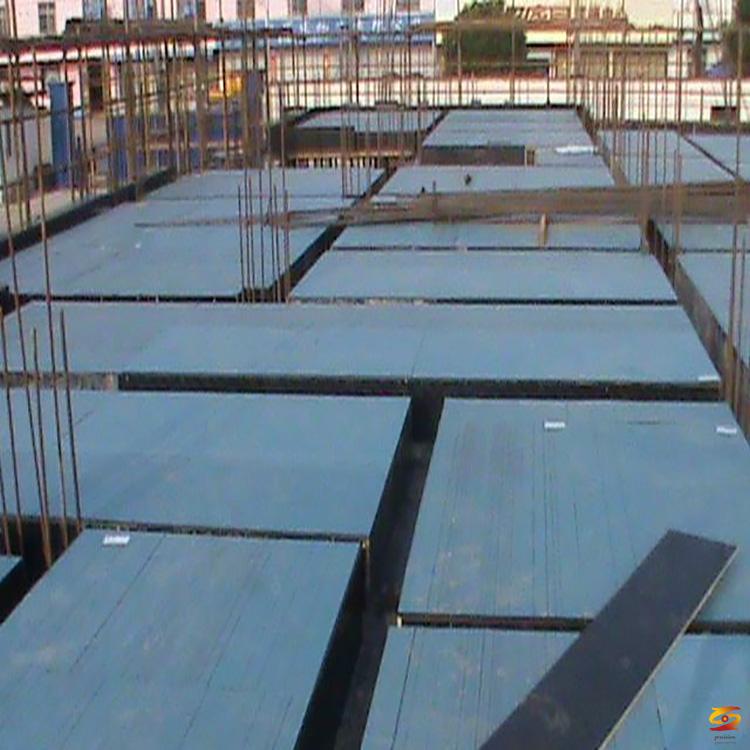