Production technology and application of PVC building template (1)
Production technology and application of PVC building template (1)At present, my country's construction industry consumes 166 million m3 of high-quality wood every year, accounting for about one-third of the country's total consumption, and the dependence of wood imports has exceeded 50%. The National "Thirteenth Five-Year Plan for Forestry Development" clearly states that the commercial logging of natural forests will be completely stopped by 2017, which will inevitably have a certain impact on the use of wood and further aggravate the contradiction between supply and demand of wood resources. my country's plastic resources are abundant, especially the current PVC production capacity is relatively surplus, and the technology is mature. Under the background of the country's advocating the application of green building materials, it is timely to promote the work of "plasting wood with plastic". As a major consumables in the construction industry, vigorously promoting the use of plastic formwork can not only reduce the consumption of high-quality wood resources, but also help to play the technical advantages of my country's plastics industry and resolve the problem of excess PVC production capacity.
"Made in China 2025" puts green development in a prominent position. "Thirteenth Five-Year Plan for Industrial Green Development" and "Action Plan for Promoting the Production and Utilization of Green Building Materials" will speed up the implementation of green renovation and upgrading of building materials and promote the efficient recycling of resources Use as a key task will have a positive role in promoting the production and application of plastic formwork. "Replacing wood with plastics" is an inevitable way of environmental protection. In the product design and development stage, comprehensive consideration should be given to the selection of raw materials, manufacturing, sales, use, and recycling to achieve the goals of scientific resource utilization and environmental protection. Therefore, the development of PVC building templates is of great significance for the protection of forest resources.
1 Performance characteristics of PVC building templates
PVC wood-plastic building templates are plastic products extruded with PVC resin and various additives. The physical properties are in line with the national standard GB/T 29500-2013. The PVC construction template can replace the existing wood glue board, bamboo glue board and steel formwork with the following advantages.
(1) High comprehensive utilization rate and low use cost. The PVC wood-plastic building template has a long service life and can be used for more than 20 turnovers. After being scrapped, it can be recycled and reused twice, which reduces the cost and protects the environment.
(2) The quality of the project is good, the demoulding performance is good, and no secondary plastering is required. The surface of PVC wood-plastic building template is smooth and smooth, and there is no need to apply mold release agent to the contact surface with concrete. After the concrete is solidified, the formwork will automatically detach from the poured concrete, the demoulding is quick and easy, the effect is excellent, the cleaning and maintenance costs are reduced, the removal is convenient, the damage is less, and the labor intensity is reduced. After demoulding, the concrete surface is clean and flat, and the flatness error can be controlled within 4 mm. The thickness of the shear wall of the general high-rise residence is 200 mm, and the aerated block can be customized to 170 mm thick. After plastering, it is the same thickness as the shear wall. (The structural design of the junction between the reinforced concrete wall and the aerated block is reduced to 170 mm thick, and the steel wall is hanged with the aerated block wall to plaster). Since the concrete wall is not plastered, labor for plastering is saved ( 12 yuan/m2), which saves the plastering sand material (90 squares of sand, 300 tons of cement), and shortens the construction period, thus ensuring the quality of the project. Wall cracks are a serious disadvantage in the fine decoration of houses, and most of the wall cracks are cracks in the plastering layer. There is no wall cracking when the concrete wall formed by the wood-plastic formwork support is not plastered.
(3) Waterproof and fireproof. Good water resistance, long-term immersion in water, no layering, no foaming, no cracking, stable plate size. Because the wood-plastic formwork does not absorb moisture, it can save the moisture of the concrete surface, suppress the cracks on the concrete surface, which is conducive to the early maintenance of the concrete, and presents a good look on the formed concrete surface, such as full slurry, smooth and smooth; If the formwork does not absorb moisture, there will be no warping, bulging, etc. of the wooden formwork under the condition of alternating dry and wet conditions. When the formwork is supported, it can better contact with the keel and ensure the forming quality of the concrete. High fire resistance, PVC wood-plastic building template can effectively flame retardant, fire rating reaches B1 level, self-extinguish in case of fire, does not produce toxic gas, high safety factor. No worries about fire on the construction site.
(4) The performance comparison of PVC wood-plastic building templates and other templates is shown in Table 1.
2 PVC building template production technology and process
2.1 Production principle and technological process
PVC building template is based on PVC-SG5 or SG7 type resin, with heat stabilizer, impact modifier, processing modifier, foaming agent, foaming regulator, lubricant, filler and other auxiliary materials, after extrusion It produces low-foaming PVC plastic products formed by molding, cooling and shaping.
The process flow is as follows:
PVC, additives, wood powder, high-speed mixing ---- low mixing cooling --- twin screw extruder --- head - cooling and shaping - traction - cutting - inspection One package and one finished product are put into storage.
2.2 Device configuration
2.4 Main process control points
2.4.1 Importance of PVC compounding quality
In the process of PVC plastic processing and forming, after the formula is determined, the effect of compounding quality on the performance of plastic products becomes very important. PVC mixing is an important one-step process. Good compound can make up for the adverse effects caused by poor performance extrusion equipment, and even the best extrusion equipment can not make up for the effects of bad compound. PVC mixture is divided into two parts: high-speed hot mixing and low-speed cold mixing. The main purpose of the mixture is to pre-plasticize the material so that various additives can be fully absorbed by the PVC powder, and at the same time, low molecular volatiles are discharged. High-speed thermal mixing is not a simple physical mixing, but a kneading process. Kneading is a special form of mixing. It is a mixing operation that relies on shear action to reduce and homogenize the aggregate size of the components.
The compounding process needs to pay attention to: the high-speed hot mixing discharge temperature must be timely and accurate, and can not exceed the temperature requirements of the process index. The high mixing temperature is generally controlled at 120-125 oC, and the high stirring time is generally controlled at 7 to 10 min. If the temperature still does not reach 110°C in 10 min, it indicates that the blades of the high agitator are seriously worn and needs to be replaced, because the materials cannot be heated for a long time; the cold mixing time of the low speed cold mixing is best controlled at 5-10 rain, and the discharge temperature is generally controlled Below 45℃. When the temperature of the cold mixing material is too high, the material will produce sintered agglomerates, which affects the quality of the compound. In addition, if the high agitator is a continuous mixture, even the scientifically designed high agitating blades should be replaced at least half a year to avoid the worn blades changing the flow behavior of the mixture and affecting the quality of the compound. The mixed PVC mixture is best used after aging for 24 hours.
2.4.2 Processing technology control points
(1) The extrusion molding process includes control of parameters such as process temperature, screw speed and traction speed. The temperature setting of each extruder is different, and it should be based on the actual situation of the extruded material, not mechanically copied. Whether the extrusion temperature is set reasonable or not will directly affect the product quality. If the temperature of the barrel is too low, the material will be poorly plasticized, the product cannot be formed, the head pressure is too large, and the equipment is overloaded; the high extrusion temperature will cause the foaming and decomposition of the material, the strength is low, and it may not even be formed at all. Severe sticky material at the mold, causing mold paste and poor product stability. Therefore, formulating a reasonable process temperature is the prerequisite for ensuring the normal production of extrusion.
(2) Set the temperature of the equipment barrel.
After the production formula is determined, at a certain extrusion speed, the plasticization and melt temperature of the material are determined. Melt temperature has a great influence on bubble structure, product density, and product quality. When the melt temperature is low, the melt viscosity is high, it is difficult to plasticize, and the foaming is incomplete; when the melt temperature is too high, the melt viscosity is low, the foaming advances, it is easy to produce large bubbles, the density of the product is small, and the performance is reduced. The best barrel temperature is to observe that the material in the mouth is okara
At this time, if the material at the observation port contains powder, the barrel temperature setting is low and the temperature should be increased; if the material is in the form of a band, the barrel temperature setting is too high and the temperature should be reduced. Barrel actual temperature control and set temperature deviation
The difference should be controlled within ± 2 ℃. Generally, the temperature in the barrel 4 zone is more difficult to control. The fan cooling alone can not meet the requirements. It is necessary to customize the special steel barrel screw with forced water cooling in the 4 zone. Paste affects normal production.
(3) Temperature setting of the machine head.
The temperature of the machine head directly affects the degree and quality of foaming, and is generally slightly higher than the AC foaming point temperature. The temperature of the side plates on both sides is relatively high to supplement the heat loss and facilitate the flow of materials
If you want to know more about it please do not hesitate to
contact me. WhatsApp:+86-15966835076.

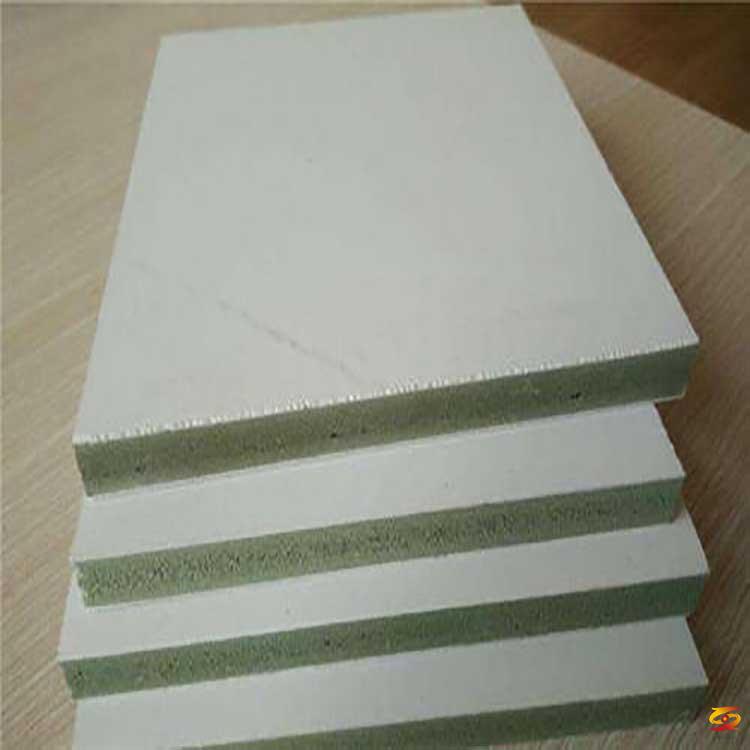

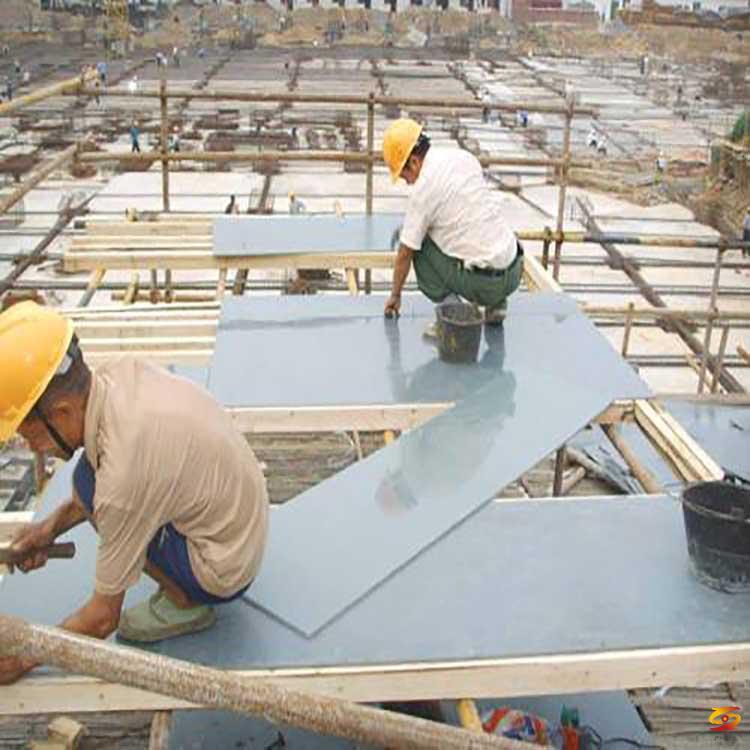