Twin screw technology development trend
Twin screw technology development trendTwin screw extruder technology development trend _ high speed, high efficiency, energy saving has been the main theme of the continuous improvement of international plastic machinery in recent years. High speed and high output enable investors to obtain high returns with lower investment. However, the high speed of screw speed brings a series of problems to be solved.
Technology Progress Trend of Twin Screw Extruder
High speed, high efficiency and energy saving have been the main melody of the continuous improvement of international plastic machinery in recent years. High speed and high output enable investors to obtain high returns with lower investment. However, the high speed of the screw speed brings a series of problems to be solved: if the material stays in the screw for a short time, it is easy to cause uneven mixing and plasticization of the material; too high shear may cause the material to heat up rapidly and thermal decomposition; may occur Extrusion stability problems; high-performance auxiliary machines and careful control systems are needed to match them; screw and barrel wear problems and reduction gearbox design problems, etc. Therefore, it is one of the important directions of technical innovation for twin-screw suppliers to provide solutions to the problems that high speed may bring.
The new twin-screw extruder-ZEUTX series launched by Berstorff (Germany), Germany, is distinguished by its excellent screw diameter/productivity ratio. The screw design has a maximum speed of 1200 rpm, a large torque, and an extrusion capacity of 100 to 3500 kg/h. The processes of material mixing, reaction and exhaust can be carried out at the same time. The barrel and screw adopt modular design, which can meet various special process requirements, have excellent processing flexibility, and are equipped with ZSEF side feeder, which can achieve high solid particle conveying rate, and the pelletizer can Match different yields and material processing.
In order to meet the needs of high speed and high output, this extruder has many improvements. Equipped with a barrel heater, it can complete the temperature rise of the extruder in a very short time, and the maximum heating temperature can reach 450 ℃; the design of the cooling channel truly realizes counter-flow cooling and optimizes the cooling system; it is equipped with a "bow clamp" Tightening device", the time for changing the barrel can be faster than the traditional bolt connection type; the barrel adopts a patented high-frequency quenching and hardening process, giving excellent wear resistance, thereby eliminating expensive wear bushings; In addition, it is also equipped with the company's advanced process control system.
If you want to know more about it please do not hesitate to
contact me. WhatsApp:+86-15966835076.
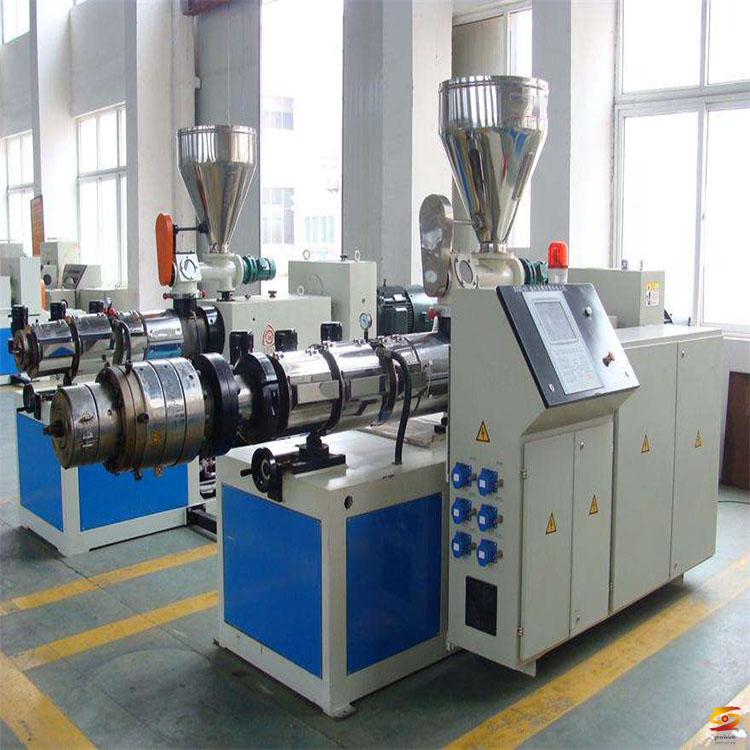
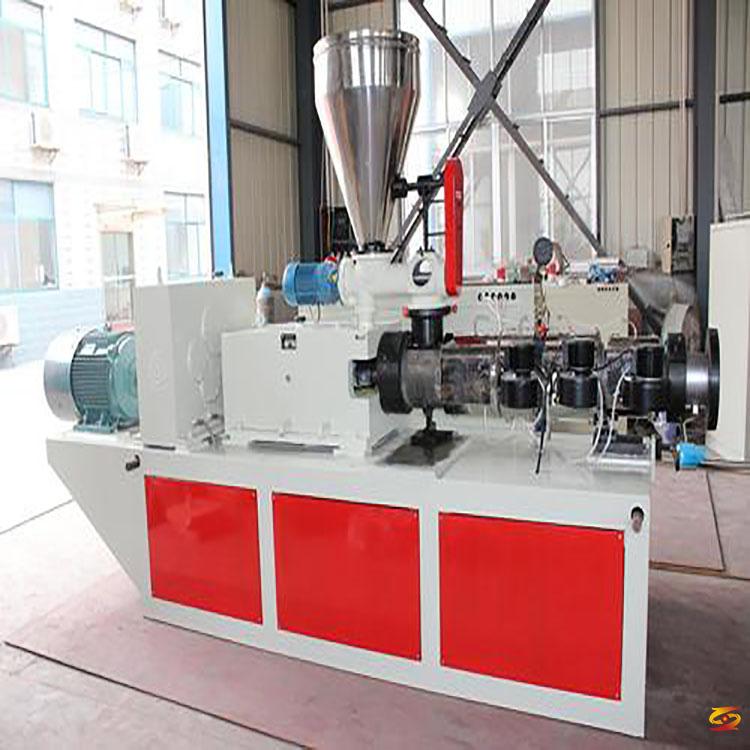
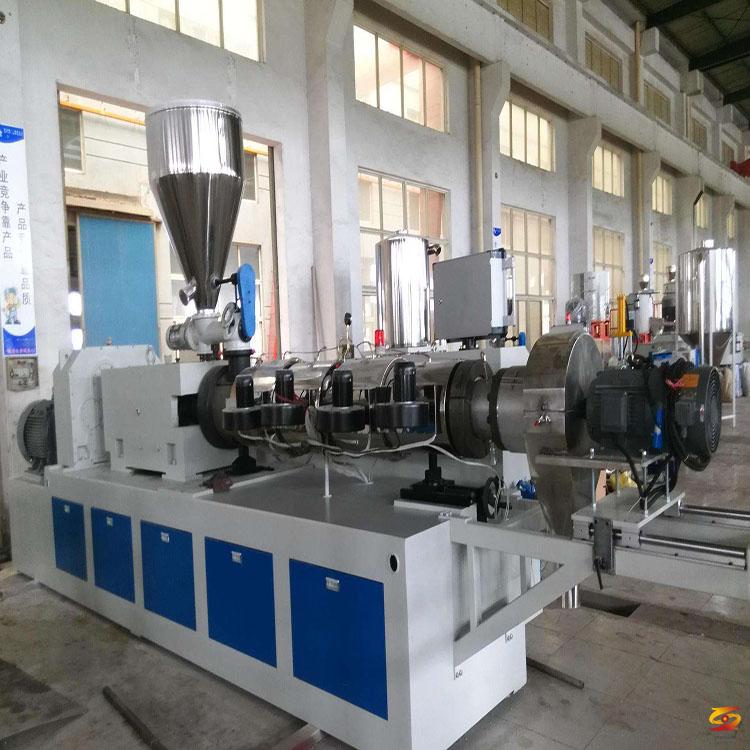