Waterproof membrane introduction
Waterproof membrane introductionWaterproof coiled material is mainly used in building walls, roofs, tunnels, highways, landfills, etc., to resist external rainwater and groundwater leakage. It is a flexible building material product that can be rolled into a roll shape as the engineering foundation There is no leakage connection with the building, which is the first waterproof barrier for the whole project and plays a vital role in the whole project.
The products mainly include asphalt waterproof membrane and polymer waterproof membrane.
Chinese name for waterproofing membranes, architectural walls, roofs, etc. Architectural brand classifications, waterproofing membranes, etc. Features strong impermeability, high tensile strength, synthetic rubber, synthetic resin, etc.
table of Contents
1 Classification
2 Performance
3 Standard model
4 Application Introduction
▪ Fixed system
▪ Economic analysis
5 Synthesis
6 products
7 Construction requirements
8 How to choose
Category Editor
The asphalt or polymer waterproof material is impregnated on the carcass to make the waterproof material product, which is provided in the form of coiled material, which is called waterproof coiled material. According to the different main materials, it is divided into asphalt waterproof membrane, polymer modified asphalt waterproof membrane and synthetic polymer waterproof membrane; according to the difference of the carcass, it is divided into non-carcass membrane, paper tire membrane, glass fiber Tire roll material, glass cloth tire roll material and polyethylene tire roll material.
Waterproof coiled materials require good water resistance, stability to temperature changes (no flow, no blistering, no confusion at high temperature; no brittleness at low temperature), certain mechanical strength, elongation and fracture resistance. It has certain flexibility and anti-aging properties. [1]
The waterproof membrane is a sheet-shaped waterproof material that can be rolled. It is one of the important varieties of waterproof materials in construction engineering.
According to its main waterproof composition materials, it can be divided into three categories: asphalt waterproof material, polymer modified waterproof membrane and synthetic polymer waterproof membrane (SBC120 polyethylene polypropylene composite membrane). There are PVC, EVA, PE, ECB and other waterproof membranes
Asphalt waterproof coiled material is a rollable sheet-shaped waterproof material made by dipping asphalt on a base tire (such as base paper and fiber fabric) and then spreading a powdery or sheet-like insulation material on the surface.
Performance editing
1. Water resistance
Water resistance refers to the fact that its performance is basically unchanged under the action of water and after being soaked in water. It has impermeability under the action of pressure water, and is usually expressed by indicators such as impermeability and water absorption.
2. Temperature stability
Temperature stability refers to the performance of not flowing, blistering, sliding at high temperature, and not brittle at low temperature, that is, the ability to maintain the original performance under certain temperature changes. Commonly used indicators such as heat resistance and heat resistance.
Aluminum foil
Aluminum foil surface (2 photos)
3. Mechanical strength, elongation and fracture resistance
It refers to the performance of waterproof coiled material under certain load, stress or under certain deformation conditions without breaking. Commonly used indicators such as tensile force, tensile strength and elongation at break.
4. Flexibility
Flexibility refers to the ability to maintain flexibility under low temperature conditions. It is very important to ensure easy construction and no brittleness. Commonly used indicators such as flexibility and low-temperature bendability.
5. Atmospheric stability
Atmospheric stability refers to the ability to resist erosion under the long-term comprehensive action of factors such as sunlight, heat, ozone, and other chemically aggressive media. Commonly used indicators such as aging resistance and heat aging retention rate.
Standard model editing
Asphalt composite flexible waterproof membrane KSF-515
Self-adhesive polymer modified asphalt waterproof membrane KSF-930
EPDM waterproof membrane KFS -CPE-173
Asphalt waterproof membrane
Asphalt waterproof membrane
Chlorinated polyethylene waterproofing membrane KSF-603
Elastomer modified asphalt waterproof membrane GB18242-2008 [2]
Plastomer modified asphalt waterproof membrane GB18243-2008
Petroleum asphalt fiberglass waterproof membrane GB/T14686-2008
Aluminum foil surface petroleum asphalt waterproof membrane JC/T504-2007
Asphalt composite tire flexible waterproof membrane JC/T690-2008
Self-adhesive rubber asphalt waterproof membrane JC840-1999
Modified asphalt polyethylene tire waterproof membrane GB18967-2003
Self-adhesive polymer modified asphalt polyester tire waterproof membrane JC898-2002
waterproof materials
waterproof materials
Modified asphalt waterproof membrane for road and bridge JC/T974-2005
PVC waterproof membrane GB12952-2011
Chlorinated polyethylene waterproof membrane GB12953-2003
Polymer waterproof material Part 1 Sheet GB18173.1-2006
Ternary rubber waterproof membrane JC/T645-1996
Chlorinated polyethylene-rubber blended waterproof membrane JC/T684-1997
Plastomer (APP) asphalt waterproof membrane for road and bridge JT/T536-2004
Asphalt waterproof membrane tensile properties GB/T328.8-2007
Polymer waterproof tensile properties coiled material GB/T328.9-2007
Tear performance (nail bar method) GB/T328.18-2007
The tearing performance of polymer waterproof membrane GB/T328.19-2007
Asphalt waterproof roll seam peeling performance material GB/T328.20-2007
Seam peeling performance of polymer waterproof membrane GB/T328.21-2007
Seam shear performance of asphalt waterproof membrane GB/T328.22-2007
Seam shear performance of polymer waterproof membrane GB/T328.23-2007
Application introduction
1. Petroleum asphalt paper tire linoleum (production and use are now prohibited).
2. Petroleum asphalt glass cloth linoleum.
3. Petroleum asphalt glass fiber tire linoleum.
4. Aluminum foil linoleum.
Compared with the traditional oxidized asphalt, the modified asphalt waterproof membrane has a greatly expanded use temperature range. The finished coil is smooth and soft, can be made into a thickness of 3--5mm, can be used in a single layer, has 15- -20 years of reliable waterproof effect.
It can be divided into: 1. Elastomer modified asphalt waterproof membrane (SBS membrane). 2. Plastomer modified asphalt waterproof membrane (APP membrane).
3. Self-adhesive polymer modified asphalt waterproof membrane (APF membrane). 4. Synthetic polymer waterproof membrane
5. SBC polyethylene polypropylene waterproof membrane
Elastomer modified asphalt waterproof membrane KSF-SBS
This product is suitable for waterproofing and dampproofing of industrial and civil building roofs, basements, toilets, etc., as well as waterproofing of bridges, parking lots, swimming pools, tunnels, cisterns and other buildings. This product adopts the torch hot melt method for construction, which is easy to operate, safe, and has high construction efficiency. It can be constructed all year round. The aluminum foil rolls have a reflective cooling effect. The modified asphalt such as SBS used in this product has high elasticity, good flexibility at low temperature, and is suitable for temperature difference and resistance to deformation.
Construction requirements [3]
Construction must be carried out in strict accordance with GB5027-2002 (Roof Engineering Quality Acceptance Code) and design regulations. The base layer should have a certain strength, should not be shelled, loose, uneven, dust and foreign objects on the roof and the joints of the warehouse must be removed. The grassroots needs to be dry, with a moisture content of less than 8%. Generally, the base layer is whitish without obvious water marks or a 1m×1m linoleum is laid flat on the clean flat surface for 3-4h. If the color of the surface of the base layer covered with linoleum is still the same as the surrounding uncovered parts, and there is no obvious watermark, the moisture content has reached the requirement. Method Use a hot melt spray gun to bake the adhesive surface of the coil. The coiled material and the base layer can be fully bonded, and can also be point or strip. The area is determined by the slope size. When the minimum bonding, the surface of the shale should be baked until the asphalt is melted and the shale sheet is covered. Laminated rolls. It should be baked and compacted. There must be excess bitumen squeezed out at the overlapping edges. The long edge of the coil is lapped, the full adhesion method is not less than 70mm, the point adhesion and the strip adhesion are not less than 100mm; the short edge lap, the full adhesion is not less than 100mm, and the empty paving, point adhesion and strip adhesion are not less than 150mm. When adopting the double-layer method, the upper and lower layers of the coiled material should be staggered by 1/3 or 1/2 width and different seams. In the yin and yang corners of the roof, there are no wrinkles, hollows, edge warping, delamination and slipping in the gutters, rainwater outlets, roof ridges, laps and closing nodes. Can also be used for cold stick construction. Observe and inspect the construction quality by yourself after the construction is completed. Do not wear spikes for operation. If the construction materials are flammable, fire safety should be noted, and fire extinguishing equipment should be provided. The coiled material should be erected in a ventilated place, and avoid direct sunlight or contact with heat sources.
Product specifications
Specification (nominal thickness) mm
2
3
3
4
Materials on the table
PE
S
AL
PE
S
M
AL
PE
S
M
AL
PE
S
M
AL
Area ㎡/roll
Nominal area
15
10
10
7.5
deviation
±0.15
±0.10
±0.10
±0.10
Minimum roll weight, ㎏/roll
33
37.5
33
32
35
40
32
42
45
50
42
31.5
33
37.5
32
Thickness (mm)
Average ≥
2.0
3.0
3.2
3.0
4.0
4.2
4.0
4.0
4.2
4.0
Fixed system
1. Mechanical fixing system
The mechanically fixed coiled material waterproof roofing system is divided into a light steel roofing mechanical fixing system and a concrete roofing mechanical fixing system.
The system has the characteristics of excellent waterproof, ultra-light weight, little influence by the weather, easy maintenance, rich and beautiful colors, environmental protection and so on.
The structure is simple, and there are only three levels of vapor barrier, insulation board and waterproof coiled material (complex backing). The system has low cost and wide versatility.
2. Adhesive fixing system
Adhesive fixed coiled material waterproof roof system is divided into light steel roof adhesive fixing system and concrete roof adhesive fixing system. The system uses polymer PVC/TPO waterproof membrane with adhesive or glue as the roof covering.
It has the characteristics of excellent waterproof, super light weight, good thermal insulation performance, no cold bridge, no damage to the base, easy maintenance, rich and beautiful colors, environmental protection and so on. The structure is simple, and there are only three levels: vapor barrier, insulation board, waterproof membrane (composite self-adhesive).
3. Empty paving weight system
The empty paving weight (loose paving weight) fixed roofing system used cobblestones, concrete slabs, earth bricks and mortar, paving slabs and supports to weight the coiled material to resist wind loads. It has the characteristics of simple and fast construction, low system cost, protection of the waterproof layer, and delaying the aging of the waterproof layer. It is widely used in parking lot roofs, underground roofs, and mans roofs.
4. Color coiled roof system
Sloping roof systems can be applied to concrete, light steel, and wood base. The system has the characteristics of excellent waterproof, ultra-light weight, fast construction, easy maintenance, rich and beautiful colors, environmental protection and so on.
The structure is simple, with only insulation board, waterproof membrane (complex backing) vapor barrier and three levels. It can be constructed by mechanical fixing method or adhesive fixing method.
In short, the above is mainly used for building roofing and underground waterproofing projects. It is generally not recommended for waterproofing in multi-node, small area applications, such as toilets.
Economic Analysis
In general, the properties of synthetic polymer waterproof membranes are better than polymer modified asphalt waterproof membranes, so the service life is relatively long, but the cost of one-off engineering is also relatively high.
Policy-oriented
In the announcement of the “Eleventh Five-Year Plan” for the promotion and application of the construction industry and the restrictions on the use of prohibited technologies (the first batch) issued by the Ministry of Construction, long-fiber polyester felt, alkali-free glass fiber felt tire-based SBS, APP modified asphalt waterproof membrane (Type II), EPDM (vulcanized type) waterproof membrane, PVC waterproof membrane (Type II), self-adhesive modified asphalt waterproof membrane (including tireless base and polyester tire base), High-density polyethylene self-adhesive film waterproofing membrane and pre-laid anti-sticking technology, bentonite waterproof blanket application technology are listed as popularized and applied products (first batch); paper tire and composite tire asphalt waterproofing membrane, polyethylene film thickness Polyethylene polypropylene and other composite waterproof membranes below 0.5㎜ are listed as restricted applications; S-type polyvinyl chloride waterproof membranes, polyethylene polypropylene and other composite waterproof membranes produced by secondary heating composite molding process or recycled raw materials are prohibited Used for waterproofing of house construction.
Composite editor
1. Synthesis
Synthetic refers to a rollable sheet-like waterproof roll made of synthetic rubber, synthetic resin, or a blend of the two as a base material, adding an appropriate amount of chemical additives and fillers, and processed through a certain process. This coil has high tensile strength, high tear strength, large elongation at break, good heat resistance, low temperature flexibility, corrosion resistance, aging resistance, and cold construction.
Can be divided into: 1, rubber-based waterproof membrane. 2. Plastic waterproof membrane. 3. Rubber-plastic blended waterproof membrane.
The choice of waterproof membrane has a great influence on the quality and durability of the waterproof layer. Proper selection and rational use of waterproof membrane are one of the keys to the success or failure of roof waterproof design. There are many types of waterproof membranes and different performances.
1. According to the characteristics of polymer modified asphalt waterproof coiled material, its construction methods are (A. hot melt method B. cold bonding method C. self-bonding method).
2. Waterproof vapor-permeable membrane
Waterproof vapor-permeable membrane is a new type of polymer vapor-permeable waterproof material. In terms of manufacturing process, the technical requirements of waterproof vapor-permeable membranes are much higher than that of ordinary waterproof materials. At the same time, from the perspective of quality, waterproof vapor-permeable membranes also have functional characteristics that other waterproof materials do not have. The waterproof vapor-permeable membrane enhances the air-tightness and water-tightness of the building. At the same time, its unique vapor-permeability performance can quickly discharge the water vapor inside the structure, avoid the growth of mold in the structure, protect the value of the property, and perfectly solve the moisture-proof and human health; Water vapor is quickly discharged to protect and maintain the thermal performance of the structure. It is a healthy and environmentally friendly new energy-saving material.
Product Editor
SBC120 series
Polymer reinforced composite waterproof membrane (SBC120 series
waterproof material
waterproof material
) It is made of polyethylene, polypropylene non-woven fabric, EVA, anti-aging agent and other high-molecular raw materials after physical and chemical changes are compounded by automated production line and processed. Its structure is that the middle layer is a waterproof layer and an anti-aging layer, and the upper and lower sides are reinforced adhesive layers. The product is a high-molecular multi-layer compound at one time, and its surface is irregular cross mesh. It is characterized by high tensile strength, strong waterproof and impermeability, and simple construction. It is the newest waterproof material with the most development potential and the fastest development.
Features
1.1 Product structure characteristics
Polyethylene-polypropylene composite waterproofing membrane is made of polyethylene resin as the main waterproof layer, and double-surface composite polypropylene filament non-woven fabric is used as the reinforcement layer. The hot-melt direct pressure process is used for one-time composite molding (low-grade products use the second composite molding process ).
The main waterproof layer polyethylene film is made of linear low-scale polyethylene (LLDPE) resin with good puncture resistance. At the same time, auxiliary materials are added to improve the flexibility and adhesion of the main waterproof layer of the coil. Carbon black and antioxidant are added. To improve the aging resistance of the main waterproof layer of the coil.
The surface reinforcement layer adopts a new type of polypropylene filament hot-rolled spunbond non-woven fabric. Its main functions are as follows: First, it increases the overall tensile strength of the core layer (main waterproof layer), so that the thickness of the core layer is relatively reduced; The roughness of the surface makes the core layer play a protective role; the third is to provide a network void structure that can be bonded.
Non-woven fabric structure as the surface reinforcement layer of the composite coil, about 40% of the thickness and the water-impermeable layer of polyethylene resin are bonded by hot melt to ensure that the surface layer and the water-impermeable layer are firmly combined; about 60% of the thickness provides the main body of the coil The bonding of the layer and the structural adhesive layer ensures that the adhesive is fully bonded to the water-impermeable layer, making the waterproof structure tangentially impermeable to water.
1.2 Product performance characteristics
The selection and structural characteristics of polyethylene polypropylene fiber composite waterproof membrane make it have strong impermeability, high tensile strength, low temperature flexibility, small linear expansion coefficient, easy bonding, large friction coefficient, good stability, non-toxic, Strong deformation adaptability, wide temperature range and service life
Good comprehensive technical performance such as longevity. Polyethylene and polypropylene (polypropylene) are resistant to chemical stability, corrosion, mildew and ozone, and polypropylene has good mechanical properties. Under the condition of complete isolation from ultraviolet light, the proven life of polyethylene and polypropylene is greater than 50 years.
It should be noted that the polyethylene-polypropylene composite waterproof membrane discussed here refers to the products produced by regular enterprises whose main waterproof layer reaches the prescribed thickness, adopts a composite molding process, and has guaranteed quality.
1.3 Product application technical characteristics
The application technology of polyethylene-polypropylene composite waterproofing membrane product is the system waterproofing technology. The comprehensive use of superior materials assumes the decomposition function of the waterproofing system to form a waterproof system with good and stable overall performance.
System waterproof structure:
The polyethylene polypropylene fiber composite waterproof membrane is composed of a protective layer, an upper structural adhesive layer, a coil main body layer, a lower structural adhesive layer, and a base layer. The main layer of the coiled material is a polyethylene-polypropylene composite waterproof coiled material, which is composed of an upper reinforcing layer, a water-impermeable layer, and a lower reinforcing layer.
1.3.1 Functional characteristics of each part:
1) Protective layer: bear the functions of preventing mechanical damage, ultraviolet light irradiation, and blocking water flow.
2) Upper adhesive layer: It is responsible for the adhesion of the protective layer and the main layer of the coil, and the function of blocking the leakage water flow (consisting of a polymer-containing waterproof cement slurry).
3) The main layer of the coiled material: it bears the function of preventing water penetration and providing the bonding structure layer, and has the functions of preventing thermal aging and ozone aging.
4) Lower adhesive layer: It is responsible for the bonding of the main body layer of the coil and the base layer, blocking the lateral leakage of the leakage water flow, and making up for the defects of the base layer (consisting of polymer adhesive).
5) Base layer: bear the function of providing bearing matrix (mainly composed of building masonry or concrete structure).
1.3.2 System waterproof structure characteristics
The waterproof structure of the polyethylene polypropylene composite waterproof membrane system can meet the requirements of the waterproof engineering design for the waterproof system:
1) Structural stability: This is achieved by direct solidification and bonding between the web structure of the coil surface and the cement structure.
2) Water impermeability: This is achieved by means of a coiled polyethylene core layer and a laterally impermeable stable bonding interface structure.
3) Atmospheric aging resistance: This is achieved by the good anti-oxidation and ozone resistance of polyethylene and polypropylene, and the cement structure which is stably combined with the coil and completely cut off the ultraviolet light.
4) Mechanical protection: rely on the surface reinforcement layer and the cement material protective layer with stable performance.
5) Ultraviolet light protection: the protective layer of cement material shall bear, and the coiled material after construction is completely isolated from ultraviolet light.
6) Construction feasibility: It is achieved by directly solidifying and bonding the mesh-like void structure provided by the surface reinforcement layer of the coiled material and the cement material. In the waterproof system, cement material is used for the bonding of the waterproof membrane and the main structure of the building and the protective layer. Therefore, the structural stability is good and does not weaken with time. At the same time, the construction does not require a low water content of the main body of the building.
7) Environmental protection feasibility: the product is non-toxic and pollution-free, and does not pollute the environment during construction.
8) Seepage blocking when the waterproof layer is accidentally damaged: The application system of polyethylene polypropylene composite waterproof membrane product focuses on the overall waterproof performance of the structure, and does not emphasize the ability of the waterproof membrane body material to prevent water penetration alone. In the entire waterproofing system, the layered structure plays a role in blocking the leakage of water; when the main material of the coil material is accidentally damaged, the total seepage flow of the leakage point of the main material of the coil material is controlled so that it does not form a clear water flow, thereby reaching the project The overall effect of waterproofing.
1.3.3 Splicing technology
The splicing of polyethylene polypropylene composite waterproof membrane adopts two methods of coagulative adhesive bonding and hot melt bonding, both of which have long-term physical and chemical stability.
1) Bonding with solidifying adhesive
Curable adhesives mainly refer to polyurethane adhesives, polymer modified cement coatings, etc. After the set adhesive is dried, it is riveted and bonded to the non-woven fabric on the surface of the coil.
Adhesive mechanism: The surface of the linear low-density polyethylene (main waterproof layer) composite non-woven fabric is roughened, and a mesh-like void structure is formed on the surface of the coiled material, so that it has adhesive properties. When the non-woven fabric on the surface of the coil is in contact with the bonding liquid, the tangential arrangement of the non-woven fabric fibers makes the bonding easy to immerse. The bonding liquid immerses into the non-woven mesh pores to form a mechanical riveting effect, so that the coil and the coil Or the base is firmly bonded together.
2) Hot melt bonding
Hot melt bonding mainly refers to hot wedge welding, with better bonding effect.
Adhesive mechanism: The polyethylene resin is thermally melted, and the polypropylene can be extruded under pressure or fusion bonded with polypropylene, and its adhesive strength is reliable, up to 40N/cm.
1.3.4 Engineering application advantages
Polyethylene polypropylene composite waterproof membrane has some unique advantages in the project:
1) Solve the problem that most organic waterproof membranes cannot be directly laid with cement materials;
2) There is no limitation that the construction of most organic waterproof membrane products requires low water content (<9%) of the building base;
3) Solved the problem that the waterproof material of the main body of the organic waterproof membrane product is easily damaged and aging when exposed to use;
4) There is no problem of open flame construction and environmental pollution of certain waterproof coiled materials;
5) The waterproof system gets rid of the method of solely relying on waterproof materials to assume all waterproof functions, reduces the consumption of organic materials and engineering costs, and improves the waterproof effect.
System supporting materials
Polyethylene polypropylene composite waterproofing membrane waterproofing system performs waterproof construction according to the design requirements of the project, and requires corresponding supporting materials, including supporting adhesives, thermal softening equipment, and predetermined materials.
2.1 Adhesive bonding construction
The bonding characteristics of polyethylene polypropylene composite waterproof membrane and the system waterproof structure determine the choice of bonding materials.
Polyurethane can be used as the adhesive for the seam of the coil. The polyether or asphalt-based polyurethane adhesive that is specially formulated and has no swelling effect on the waterproof coil is mainly selected to ensure that the coil is not deformed.
The upper and lower adhesive layers of the coiled material can be modified with non-resolvable polymer adhesive cement material, that is, special cement is added to the cement slurry. This type of material has a more suitable initial adhesion, better water retention, non-resolubility and swelling water resistance. The role of the polymer adhesive is to swell with water, block the penetration of water, maintain the workability of the cement slurry, and retain moisture to facilitate the hydration and solidification of the cement in the adhesive layer.
Cement slurry material can be used for the lower structural adhesive layer, which can be connected to the base layer with a moisture content greater than 9%. Of course, when the water content is high, the evaporation of water should be avoided to form empty drums. The upper structural adhesive layer can also be made of cement, which can be applied directly on the upper surface of the waterproof membrane, followed by the protective layer construction.
2.2 Hot melt bonding construction
When the polyethylene polypropylene composite waterproof membrane is constructed by hot-melt bonding, the fusion bonding of the polyethylene film should be ensured. The main construction equipment includes double-wedge automatic crawling gun, hot-air welding gun, press-out welding gun, etc.
The degree of softness of polyethylene polypropylene composite waterproof membrane varies greatly according to its specifications. Thinner coils are more flexible and easy to lay, and thicker coils are relatively stiff. Before laying, supporting thermal softening equipment (hot air, heat radiation) is required to make the coils soft and compliant, and adapt to the grassroots. Among them, the hot air is suitable for the corners with large curvature, and the heat radiation is suitable for the corners with small curvature. Temporary fixing method is required for the bonding and laying of complex parts, and supporting materials and quick-stick adhesive fixing technology can also be used.
Other supporting construction tools include scrapers, mixing equipment, plastic containers, scissors, cutters, cleaning tools, weighing tools, putty knives, brushes, etc.
Product application range
The characteristics of polyethylene polypropylene composite waterproof membrane products can be applied in the cold northeast and northwest regions, as well as in the hot and humid southern regions.
The technical application fields of polyethylene polypropylene composite waterproofing membrane products are also wider: roofing, underground, indoor, subway, bearing table, cavern, storage, reservoir and other projects can be used. With the research and development of the special properties of this type of product, this type of material is marching into a wider range of applications. For example, through the study of the product's ability to withstand alternating loads, the composite coil will be used in road and bridge pavement waterproofing projects; through the study of the product's negative water pressure peeling performance, the composite coil will be available in underground waterproofing projects application.
Polyethylene-polypropylene composite waterproofing membrane waterproofing system is used in roofing waterproofing projects, mainly designed on the base layer; used in underground waterproofing projects, mainly designed on the basement facing the water side; used in indoor moisture-proof projects mainly designed on the basement and decoration Between the surface layers; applied in the bearing surface waterproofing project, mainly designed between the base layer and the bearing surface layer; used in the underground lining waterproofing project, mainly designed between the outer lining and the inner lining; applied in the cave waterproofing project It is mainly designed outside the inner lining; it is mainly used between the base and the tile lining in slope tile roof waterproof engineering.
Self-adhesive rubber asphalt waterproof membrane
Self-adhesive rubber asphalt waterproof membrane is based on polymer resin, high-quality asphalt as the base material, polyethylene film, aluminum foil as the surface material, and a self-adhesive waterproof membrane with a separate adhesive layer. The product is polyester-based tire and non-curable. The product has extremely strong adhesive properties and self-healing properties, suitable for construction in high and low temperature environments.
Features
1. No adhesive, no heating and baking until melting, only need to tear off the isolation layer, it can be firmly bonded to the base layer. The construction is convenient and the construction speed is extremely fast.
2. It has the elasticity of rubber, excellent elongation, and adapts well to the deformation and cracking of the base layer.
3. It has excellent adhesive force to the base layer, and the adhesive force is often greater than its shear force (breaking outside the adhesive surface) to ensure that the lap is tight and reliable, and it is seamless.
4. The very unique "self-healing function" can heal small puncture damage on its own. When encountering puncture or hard object embedding, it will automatically integrate with these objects to maintain good waterproof performance.
5. In addition to the main material, the surface material polyethylene film also has excellent water resistance and high strength (polyethylene polypropylene coil is only waterproof with this film), so waterproof has double insurance.
6. Corrosion resistance: The coil has good acid resistance, alkali resistance, chemical resistance, and excellent aging resistance in various environments.
Product application range
It is suitable for roofing, basement, indoor, municipal engineering and reservoir, swimming pool and subway tunnel of industrial and civil buildings. It is also suitable for the waterproofing project of wood structure and metal structure roof. It is especially suitable for re-waterproof projects such as military installations requiring cold construction and petroleum depots, chemical plants, textile mills, grain depots, etc. where open flames are not suitable.
For roof gardens, it can also play a role of root puncture resistance. It is also suitable for the construction of highway waterproof base. It is a national promotion product.
Construction requirements edit
The base layer (leveling layer) of the waterproof membrane must be cleaned and watered to ensure that the base layer is warm. (Note: the roof waterproof leveling layer should meet the requirements of GB 50345-2012 "Roof Engineering Technical Specifications", the underground waterproof leveling layer should comply with GBJ208 -83 "Code for Construction and Acceptance of Underground Waterproof Engineering").
Prepare the cement slurry binder with polyvinyl alcohol glue containing 10%-15% cement by weight. Stirring must be uniform, no precipitation, no clotting, no segregation phenomenon can be used.
Before the construction of the main waterproof layer on the roof, you should first seal the drainage and concentrated structural details and the coil used in the additional layer is the same as the material of the main waterproof layer.
The sealing material is polyether polyurethane. If other sealing materials are used, they should be free of mineral oil, petrolatum and other chemicals that affect the performance of polyethylene.
Corners should be covered with additional layers; Yin and Yang corners are made into R=20mm arc.
Waterproof rolls should be paved with a full spread method. The adhesive should be applied evenly on the base layer, without showing the bottom and not piled up. After the adhesive is applied, the rolls should be spread immediately to prevent the bonding quality from being affected for too long.
Paste waterproof rolls must not be wrinkled or stretched. The spreading of the rolls should eliminate the air and excess adhesive under the rolls to ensure that the rolls are tightly bonded to the base layer and each layer of rolls.
The overlapping width of the waterproof membrane shall not be less than 100mm.
The seam of the upper and lower two layers and the adjacent two webs should be staggered by one third. [4]
How to choose to edit
1. Pay attention to the product name and packaging logo
According to the product standard, the product packaging should be marked with the company name, product mark, production date or batch number, production license number, storage and transportation precautions, and product labeling should be strictly in accordance with the standard, consistent with the product name, and must not be ambiguous Incomplete words or marks and no production marks. When selecting these products, users must pay attention to the product mark and recognize the product name, because the mark represents the identity of the product. Example: Coil made of polyester-cotton nonwoven fabric-grid composite tire can only be named as asphalt composite tire flexible waterproof membrane or composite tire membrane, but not SBS membrane, and its product mark is also It can only be marked according to the standard of composite tires.
Second, identify the quality of the coil material from the tire base
Generally, visual inspection is carried out from the cross-section of the product. The specific method can tear the purchased product by hand to observe the tire-based fibers exposed on the cross-section. After the composite tire is torn, the ribs of the mesh cloth are exposed. It can be concluded that the product must be a composite tire roll, and what kind of composite tire roll is required to observe the bare tire base by means of physical property test-soluble content test. However, only the polyester or glass fiber fibers are exposed in the cross section after the web material of the simple polyester tire and the glass fiber tire is torn.
Third, strictly control the quality from the physical properties
The visual inspection can only distinguish the composite tire roll material, but it cannot solve whether the selected product meets the quality requirements. This requires the user to go to a technical institution with inspection capabilities to carry out the content of soluble matter according to the corresponding product standard. Examination of physical properties of ex-factory items. The content of solubles is used to control the amount of asphalt and modifiers contained in the product. At the same time, it can also reveal the true appearance of the tire base used in the product. It can be determined whether it is consistent with the product mark.
4. Product price comparison
The competition of waterproof membrane products is fierce, and fakes are rampant. Taking the production of SBS modified asphalt waterproof membrane with the largest market volume as an example, the best profit of the company is also no more than 15%. A variety of ultra-low-cost SBS modified asphalt waterproofing membranes appearing on the market have little SBS content, and even do not add SBS, they are replaced by waste rubber powder. Therefore, pay attention when purchasing, and try to avoid choosing products that are significantly lower than the market price.
If you want to know more about it please do not hesitate to
contact me. WhatsApp:+86-15966835076.
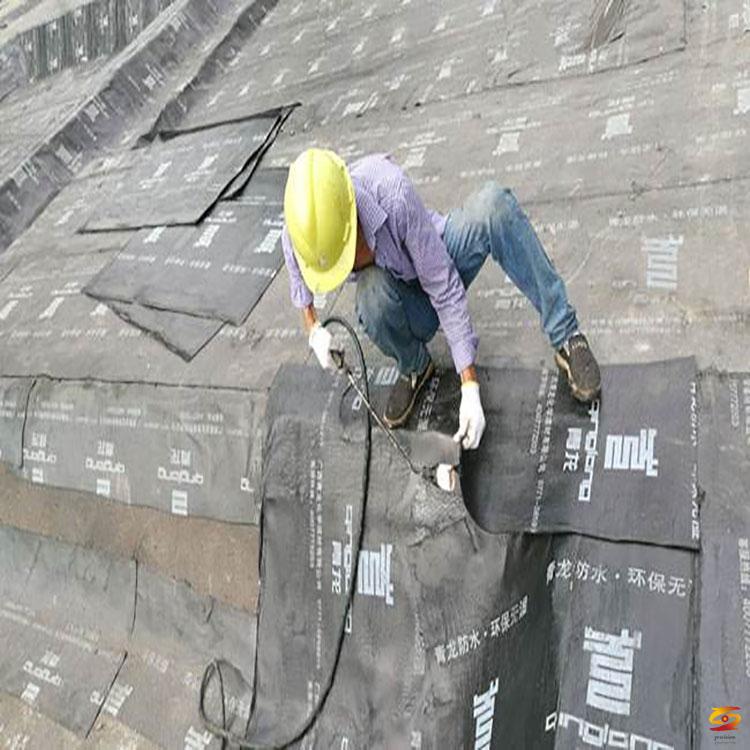
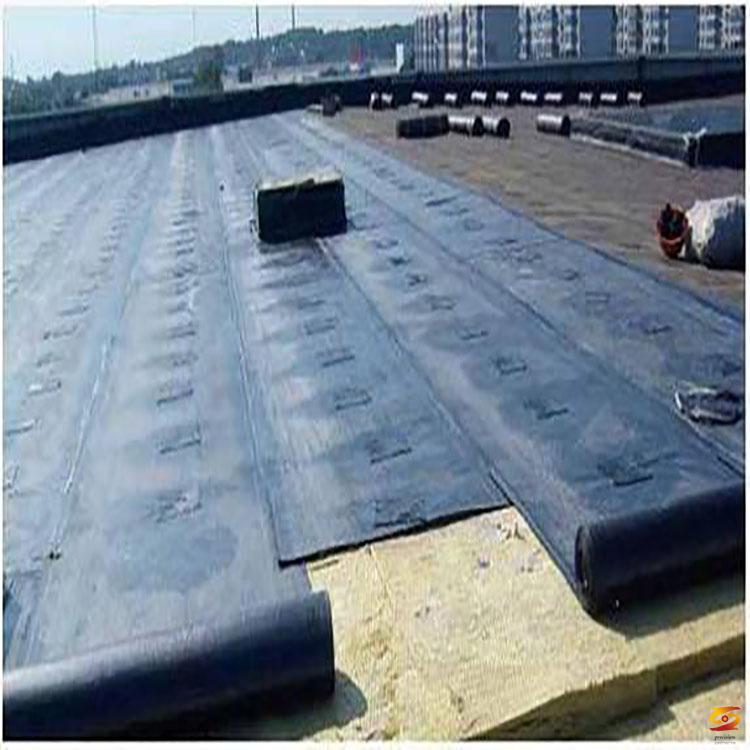
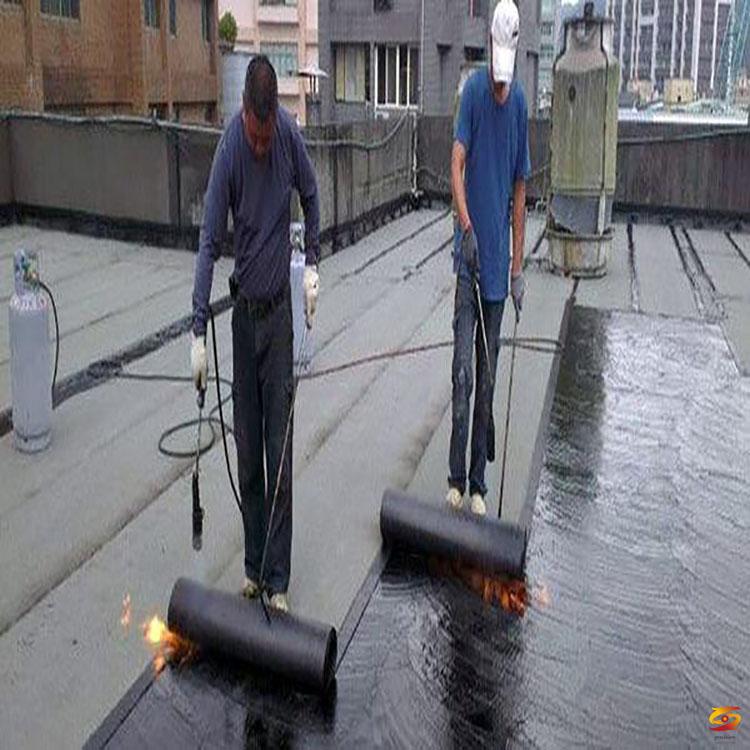
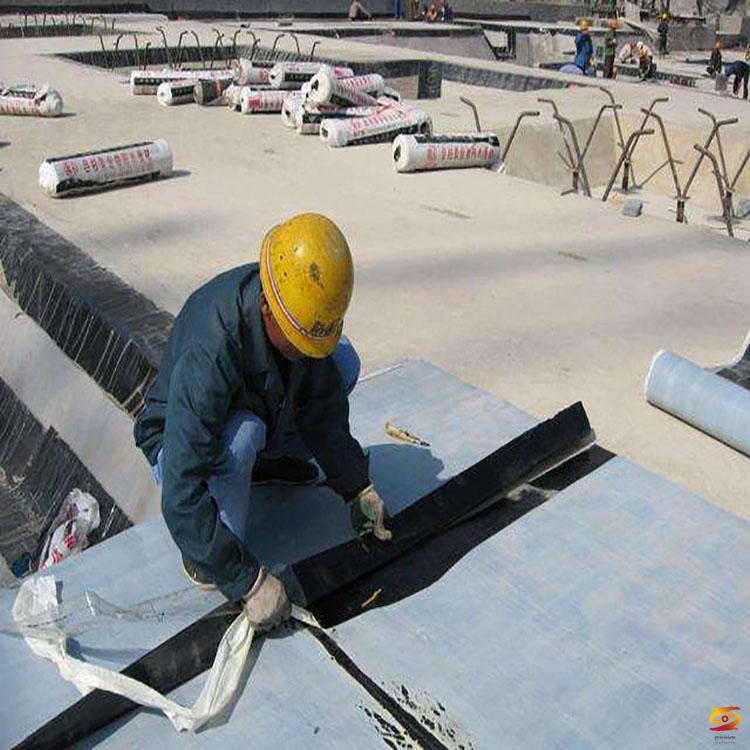