What is the technological process of the degradable lunch box production line?
The production line of disposable degradable lunch boxes is more environmentally friendly and healthier. It is everyone's responsibility to reduce the use of white garbage, reduce damage to the environment, and make society greener. The PLA degradable lunch box production line uses polylactic acid as raw material, which can be degraded into carbon dioxide and water in a short time after being landfilled. It is an environmentally friendly product. The food packaging products such as lunch boxes are healthier and consumers can use it more at ease. It is an ideal choice for investment projects.The main raw material of PLA degradable lunch box is polylactic acid. Polylactic acid (PLA) is a new type of biodegradable material made of starch from renewable plant resources (such as corn). The starch raw material is saccharified to obtain glucose, and then fermented by glucose and certain strains to produce high-purity lactic acid, and then chemically synthesized to synthesize polylactic acid with a certain molecular weight. It has good biodegradability. After use, it can be completely degraded by microorganisms in nature to generate carbon dioxide and water without polluting the environment. This is very beneficial to environmental protection and is an environmentally friendly material.
Based on global carbon dioxide emissions in 2030, the temperature will rise to 60°C. Ordinary plastics are still treated by incineration and cremation, causing a large amount of greenhouse gases to be emitted into the air, while polylactic acid plastics are buried in the soil to degrade, and the carbon dioxide produced is directly organic matter in the soil or absorbed by plants and will not be discharged into the air. Will not cause the greenhouse effect.
Description of the production process of the degradable lunch box production line: First, mix the polylactic acid raw materials and other auxiliary materials into the mixer uniformly, put them into the hopper of the first-level extruder, and use the screw designed by CAD professional design software to make the resin uniformly melt and plasticize. At the same time, the foaming agent is injected into the molten resin under high pressure and mixed uniformly. After kneading, it is sent to the secondary extruder for further mixing and cooling, and then extruded into a cylindrical shape through a die, cooling the sizing sleeve, and forming, splitting and flattening. After being pulled by the tractor, it is sent to the coiler and coiled into PLA foamed sheet products.
If you want to know more about it please do not hesitate to
contact me. WhatsApp:+86-15966835076.
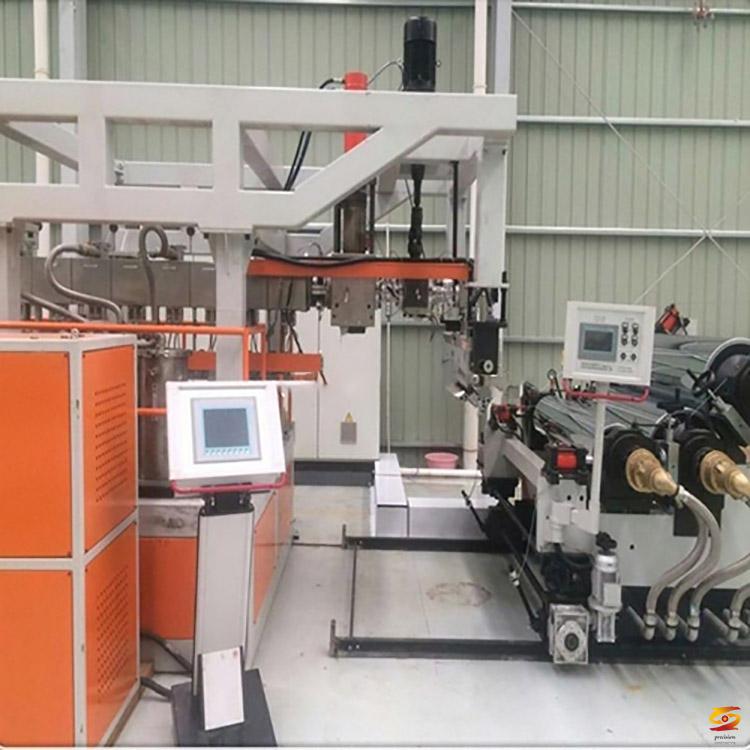
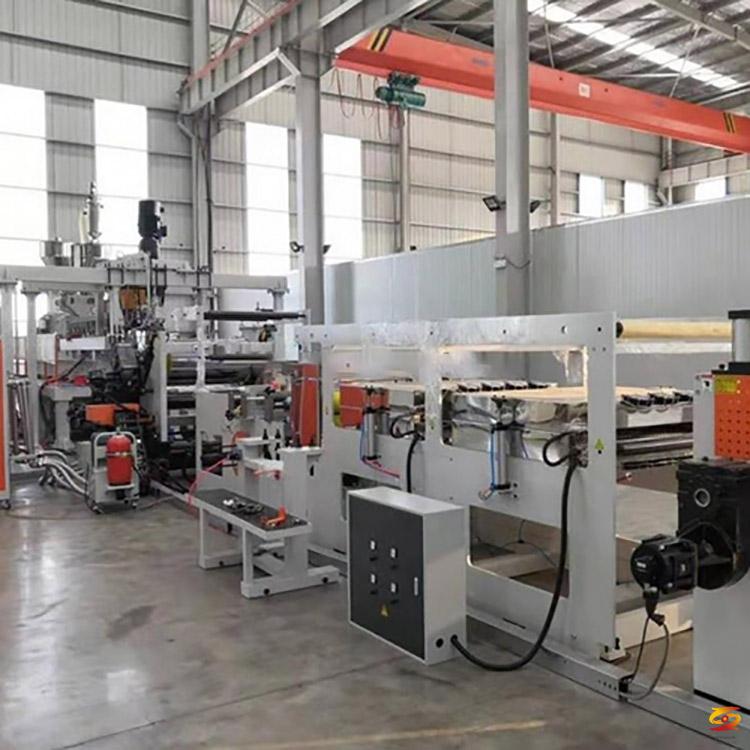
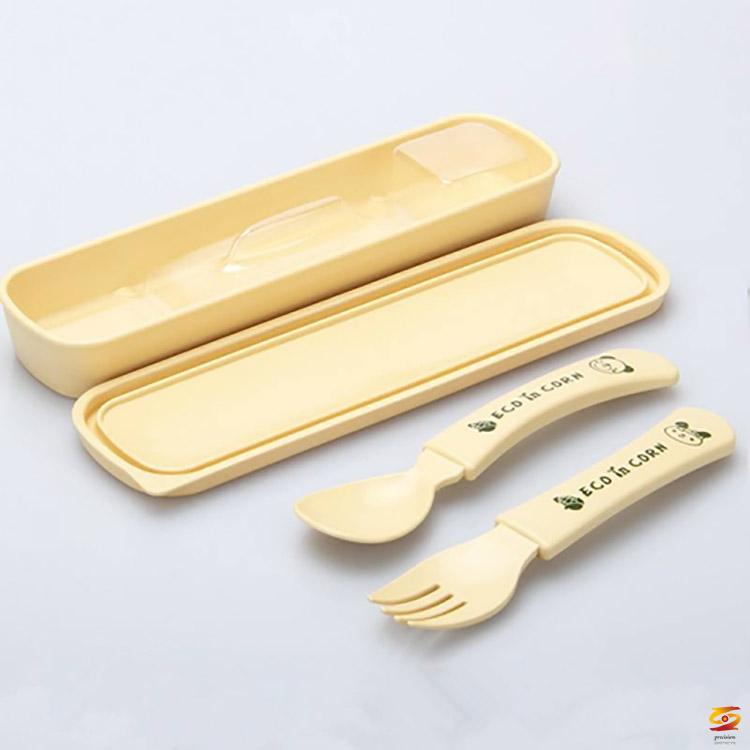
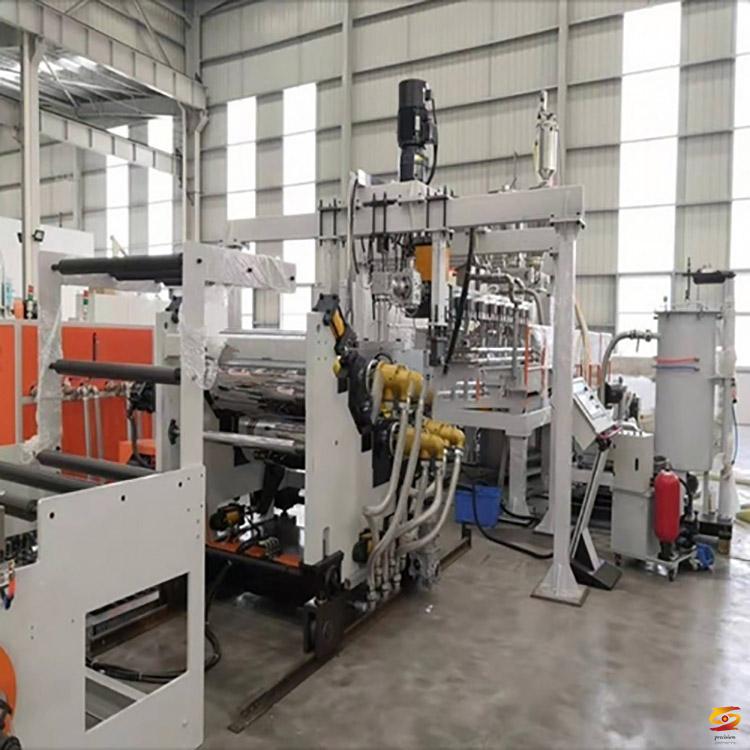