take you to learn what is single screw extruder
Single screw extruderThe single-screw extruder is mainly used to extrude thermoplastics such as soft and hard polyvinyl chloride, polyethylene, etc. It can process a variety of plastic products, such as blown film, extruded tube, platen, pulling ribbon, etc., and can also be used for melt granulation. The plastic extruder has advanced design, high quality, good plasticization and low energy consumption. It adopts involute gear transmission and has the characteristics of low noise, smooth operation, large bearing capacity and long life.
Chinese List of Screw Extruders Used for extruding soft and hard PVC. Actually used to process a variety of plastic products. Examples include film blowing, tube extrusion, platen, and ribbon pulling. The advantages are advanced design, high quality, and good plasticization.
table of Contents
1 Introduction
▪ Principle of single screw extruder
▪ Use of single screw extruder
2 Idea
3 Scope
4 Features
5 advantages and disadvantages
Introduction
Single screw extruder
Single screw extruder
As a common extruder equipment, single screw extruder is used in the plastics processing industry. What is the principle and structure? The following is an analysis of the principle of single screw extruder from the conveying section, compression section and metering section of the extruder.
The single-screw extruder is generally divided into three sections in terms of effective length. The effective length of the three sections is determined according to the screw diameter, pitch, and screw depth.
The high-efficiency single-screw extruder adopts a two-stage overall design, which strengthens the plasticizing function, ensuring high-speed and high-performance stable extrusion, and a special barrier comprehensive mixing design to ensure the mixing effect of the materials, high shear and low melting plasticizing temperature Ensure the high-performance low-temperature low-pressure metering extrusion of materials. Design concept and characteristics: high-speed, high-yield extrusion based on high straightness.
Single screw extruder principle
The last thread of the feed opening starts to be called the conveying section. The material here needs to be not plasticized, but it needs to be preheated and compressed by compression. In the past, the old extrusion theory believed that the material here was loose, and later it was proved that the material is actually solid. Plug, that is to say, the material is a solid like a plug after being squeezed, so as long as the conveying task is completed, it is its function.
The principle of the single screw extruder: when the second section is called the compression section, the volume of the screw groove is gradually reduced from large to large, and the temperature must reach the degree of plasticization of the material. The compression occurs here from the conveying section three, where it is compressed to one, this is called the screw The compression ratio is 3:1, and some machines are also changed. The plasticized material enters the third stage.
The principle of single-screw extruder: The third section is the metering section where the material maintains the plasticizing temperature, but it delivers the melt material accurately and quantitatively as the metering pump to supply the machine head. At this time, the temperature cannot be lower than the plasticizing temperature, generally Slightly higher.
The single-screw extruder is mainly used for extruding thermoplastics such as soft and hard polyvinyl chloride, polyethylene and other plastics. It can be used with various auxiliary machines (including forming heads) to process a variety of plastic products, such as films, tubes, Plates, ribbons, etc. can also be used for granulation.
The plastic extruder has advanced design, high quality, good plasticization and low energy consumption. It adopts involute gear transmission and has the characteristics of low noise, smooth operation, large bearing capacity and long life.
Single screw extruder uses
Pipe extrusion: suitable for PP-R pipes, PE gas pipes, PEX cross-linked pipes, aluminum-plastic composite pipes, ABS pipes, PVC pipes, HDPE silicon core pipes and various co-extruded composite pipes.
Sheet and sheet extrusion: suitable for the extrusion of PVC, PET, PS, PP, PC and other profiles and sheets. Extrusion of various other plastics such as silk, rods, etc.
Extrusion of profiles: adjusting the speed of the extruder and changing the structure of the extrusion screw can be applied to the production of various plastic profiles such as PVC and polyolefin. Modified granulation: suitable for blending, modifying and enhancing granulation of various plastics.
Idea editing
◎High-speed, high-yield extrusion based on high quality.
◎The design concept of low temperature plasticization ensures the extrusion of high-quality products.
◎ The two-step overall design strengthens the plasticizing function and ensures the adjustment of high-performance extrusion.
◎Special barrier, comprehensive mixing design to ensure the mixing effect of materials.
◎High torque output, extra large thrust bearing.
◎The gear and shaft are made of high-strength alloy steel, carburized and grinded.
◎High hardness, high finish and ultra-low noise.
◎PLC intelligent control can realize the linkage between the main and auxiliary machines.
◎Easy to monitor the man-machine interface, easy to understand the processing and machine status.
◎The control method (temperature control instrument) can be replaced as required.
◎Material is 38CrMoAL/A nitriding treatment, wear-resistant.
◎Strict temperature control accuracy, combined with air cooling and water cooling.
◎Unique material inlet design, with perfect water cooling device.
◎The screw barrel with grooved feeding bottom sleeve has enhanced feeding function, which provides a guarantee for high-speed and high-yield extrusion.
Item
45/30
65/33
75/33
90/33
105/33
120/33
150/33
Screw diameter mm
Screw diameter (mm)
45
65
75
90
105
120
150
Screw/L:D
Screw L/D
30
33
33
33
33
33
33
Screw speed rpm
Screw rotation speed (rpm)
150
150
150
150
150
120
90
Driving power (kw)
Drive power (kw)
18.5-37
45-90
90-132
160-185
185-250
250-315
155-450
Number of heating and cooling sections
Headging cooling segments No.
5
6
6
6
6
6
6
Connection heating power
Connector heating power
1.7
2
3
4
4
5
6
Yield
Output
60-120
120-220
300-400
400-500
500-700
800-1100
1000-1400
HDPE/MDPE-granular material
HDPE/MDPE partices
100
260
380
600
700
950
1200
PERT-granular material
HDPE/MDPE particles
85
220
320
510
600
810
1020
PPRT-granular material
PPRT particles
80
210
300
480
560
760
960
PP-granular material
PP particles
75
195
285
450
525
710
900
PB-granular material
PB particles
70
180
270
420
490
60
840
Barrel heating power
Machine barrel heating power
10
19
twenty three
35
35
60
72
Single screw extruder is a type of plastic extrusion production line, its technical parameters and models are as follows:
1. Technical parameters of single screw extruder:
1) Extruder production capacity Q: the amount of plastic extruded per hour
2) The specific flow capacity of the extruder per revolution per hour per revolution
3) Nominal specific power Motor power required to process kg plastic per hour
4) Screw length to diameter ratio L/Db: the ratio of the length of the working part of the screw to the diameter of the screw
5) Screw diameter Db: refers to the large diameter, series of standards 20, 30, 45, 65, 90, 120, 150, 165, 200, 250, 300
6) Drive screw motor power P: KW
7) Screw speed range: nmin-nmax r/min
2. Model
150/20 means that the screw diameter is 150mm and the length to diameter ratio is 20:1 plastic extrusion
Scope editing
Scope of application: all thermoplastic extrusion molding, extrusion granulation.
Features Edit
Hardened gear box, AC or DC stepless speed regulation.
New screw structure, uniform melting and mixing, ensuring low melting temperature and high output
The screw barrel is made of nitrided steel 38CrMoAIA with nitriding treatment, and the surface alloy treatment has higher hardness.
The cast copper and cast aluminum heaters are air-cooled and water-cooled as required.
Advanced electrical control system
Pros and consedit
Advantages: Single screw extruder is simple in design and cheap in price, so it is widely used.
Disadvantages:
(1) The material transportation of the single screw extruder mainly relies on friction, which limits its feeding performance, and it is difficult to add powders, pastes, glass fibers and inorganic fillers.
(2) When the head pressure is high, the reverse flow increases, which reduces the productivity.
(3) The surface renewal effect of the material of the single screw exhaust extruder in the exhaust area is small, so the exhaust effect is poor.
(4) Single-screw extruder is not suitable for certain technological processes, such as polymer coloring, thermosetting powder processing, etc.
If you want to know more about it please do not hesitate to
contact me. WhatsApp:+86-15966835076.
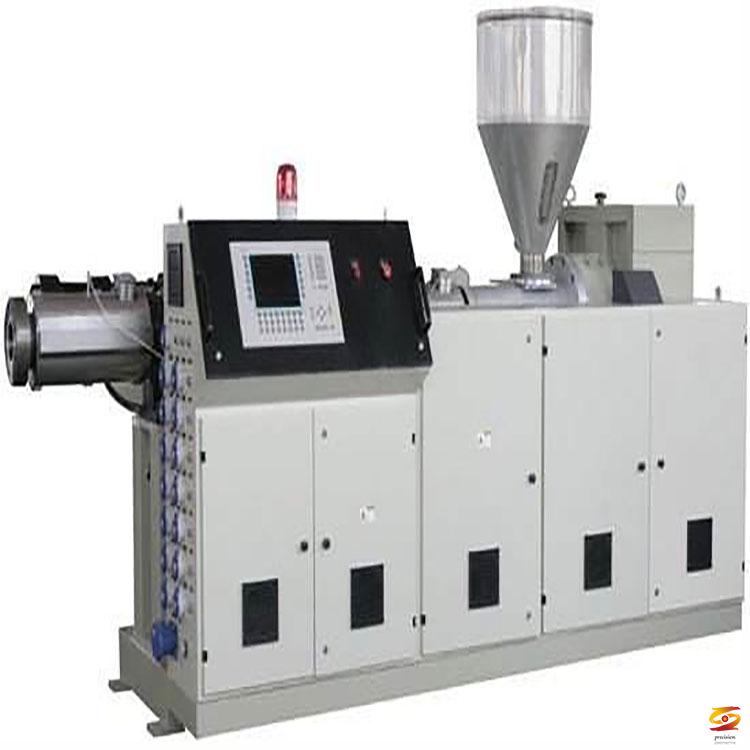
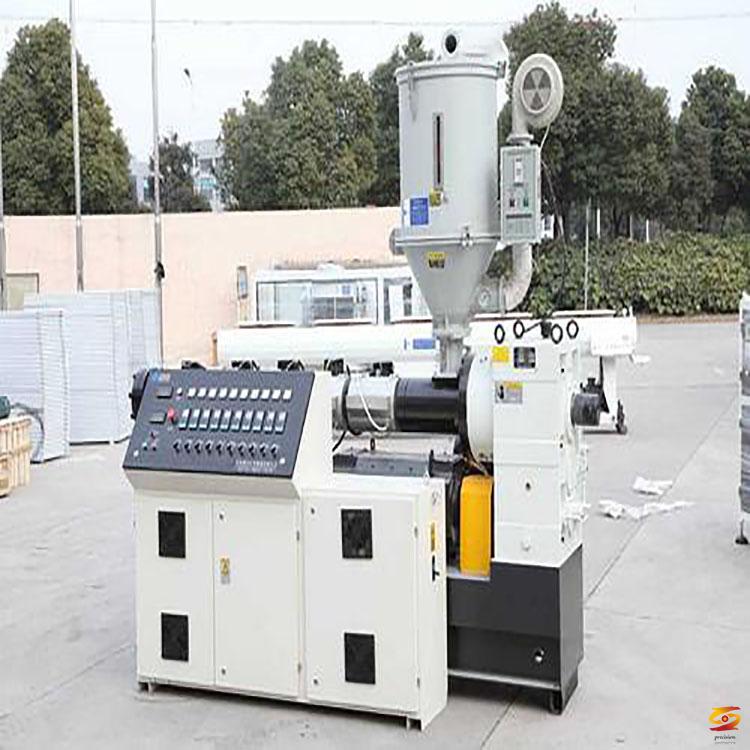
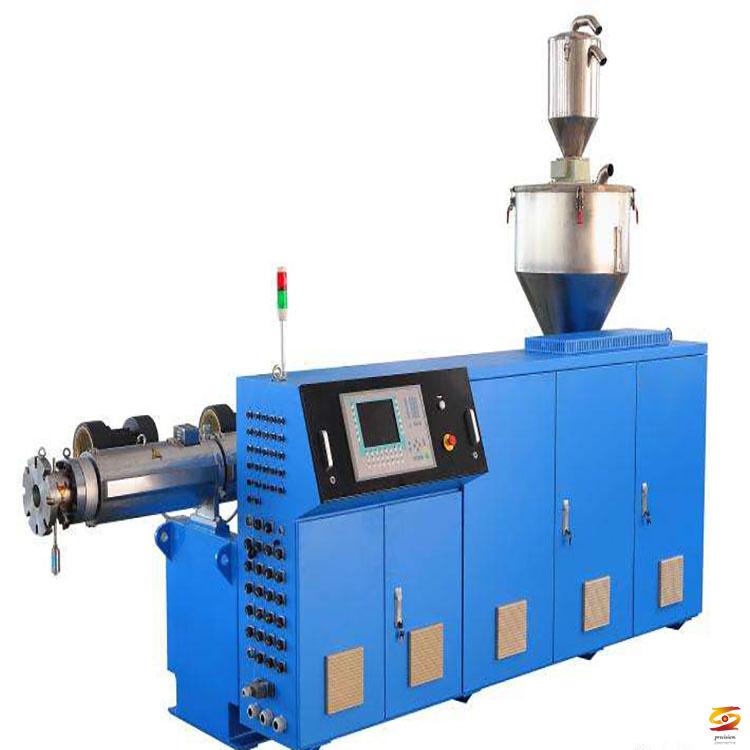