Analysis of common problems in the production process of HDPE silicon core tube finished products
Analysis of common problems in the production process of HDPE silicon core tube finished productsThe production of HDPE silicon core tube finished products is the most important link in the production process of HDPE silicon core tube, and is also a link with more problems. HDPE silicon core tube professional manufacturer Hubei Liangcheng Plastic Industry has summarized many years of production experience and will The common problems and solutions are listed below. I hope to help my friends. If there are any problems, please invite experts and friends to criticize and advise. At the same time, we also welcome our colleagues to discuss and communicate with us, learn together, and seek common development.
Common problems in the production of HDPE silicon core tube finished products:
1. Extrusion is not smooth during the production process, and the product surface does not look smooth.
Solution: The main problem that causes this kind of phenomenon is that the temperature is too low, which can be gradually increased by 3-5 ° C to reach the required temperature.
2. In the normal production process, it is found that the surface of the produced product has slip marks.
Solution: There may be two reasons for this phenomenon of HDPE silicon core tube. One is that the output surface is caused by too wet raw materials. There are bubbles on the output surface and it is higher than the surface. When the sleeve is changed through setting, uniform scars will occur. To the scratch marks. To solve the sliding marks caused by such reasons, drying the raw materials or adding defoaming materials (up to 5% dosage) is sufficient. The second possibility is that the temperature is too high, as long as the temperature is appropriately lowered.
3. During the production process, the product naturally increases and there is foaming.
Solution: The main reason for the natural increase of the produced products is that the temperature is too high, and the temperature can be reduced. Wait until the adjusted temperature reaches the desired temperature and re-extrude. The main reason for the phenomenon of foaming is that the raw materials are too moist. Drying the raw materials or adding defoaming materials (up to 5% of the amount) is sufficient.
4. How should the wall thickness be controlled during the HDPE silicon core tube production process? Especially the wall thickness of non-standard products
Solution: The wall thickness of the HDPE silicon core tube is generally determined by the speed of the host and the traction speed. The speed of the main unit is inversely proportional to the traction speed, that is, the main unit is fast and the traction speed is slow, so the thickness is thicker. If the host speed is a fixed value, the faster the traction speed, the thinner the wall thickness. When producing non-standard products with thicker ends and thinner middle thicknesses, the speed can be set according to the formula: traction speed = original wall thickness × original traction speed / desired thickness
5. How to set the pressure during the production process? How much is best?
Solution: The pressure in the production process of HDPE silicon core tube is mainly that the vacuum pressure is generally controlled between 0.3-0.4Mpa, and it is best to maintain a certain water level.
If you want to know more about it please do not hesitate to
contact me. WhatsApp:+86-15966835076.
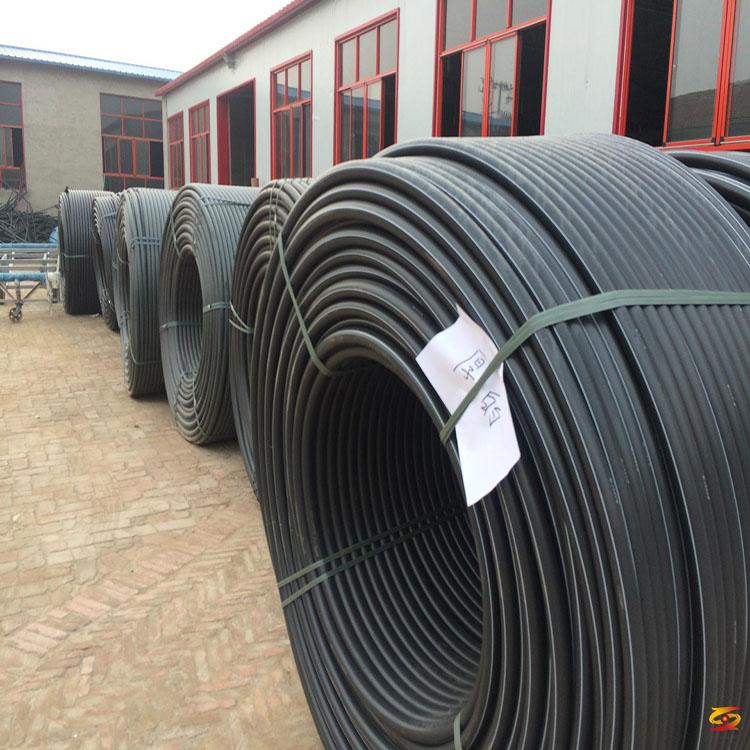
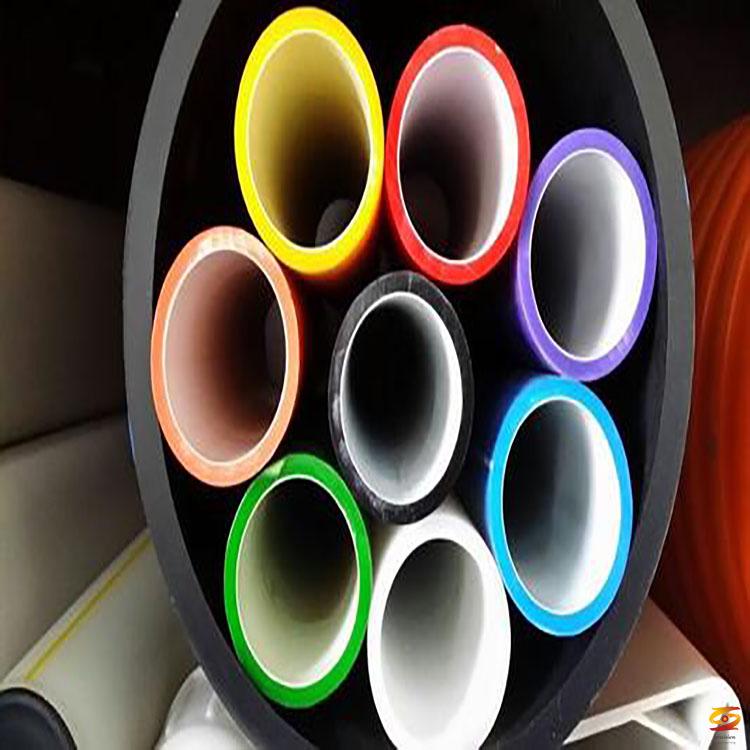
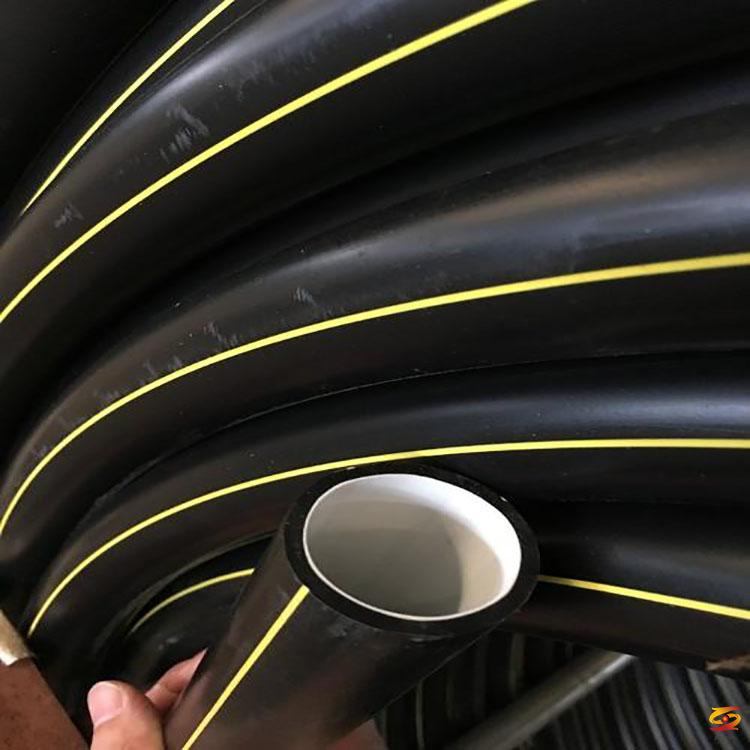
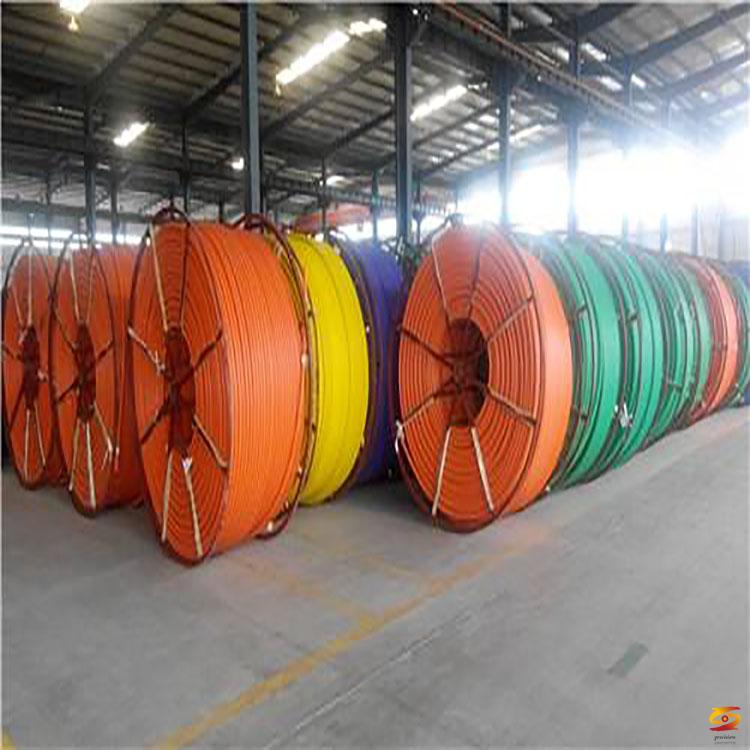