Comparison of PP Hollow Building Formwork and Traditional Formwork
Architectural formwork is an important tool for the construction of concrete structures. Formwork technology directly affects the quality, cost and benefit of engineering construction. Architectural formwork technology is an important part of construction engineering construction technology.The construction volume of the concrete structure of this project is huge, and the formwork project will account for 20% to 30% of the cost of the concrete structure project, 30% to 40% of the engineering labor, and about 50% of the construction period. On the premise of ensuring the quality of the concrete project, it is a major problem faced by this project to choose what type of template material to achieve the most economical and reasonable.
At present, the commonly used template types in China are wood template, steel template, aluminum-plastic template, bamboo plywood template, wood plywood template, hollow plastic template, etc., among which wooden template, steel template, aluminum-plastic template, bamboo plywood template, wood plywood template It is replaced by a plastic template. The plastic template is a new type of building template. It is an energy-saving and environmentally friendly product. The promotion of the use of plastic templates can achieve the use of plastic for wood and plastic for steel. , Is an important measure to save resources, has broad development prospects, currently in construction projects
It has been widely used in Heqiao project and has achieved good results, but it has not been widely used in Shaanxi Province, and the construction experience is not perfect. Therefore, after research and analysis in this project, it was decided to select only 2 buildings, each with 36 floors and 11 #楼、12#Building is used as a pilot for plastic formwork. Polyurethane plastic formwork and new hollow plastic formwork are used for concrete structural engineering construction. Other buildings use plywood formwork and bamboo plywood formwork.
2: The characteristics of the plastic template used in this project
2.1 Advantages of plastic formwork
(1) The surface of the board is flat and smooth, which can be used for clear concrete, eliminating the second plastering of the wall, saving time, labor and materials.
(2) Light weight, the weight per square meter is about 9.5 kilograms, the supporting and disassembling molds are light, the construction operation and transportation are safe and reliable, and the construction is convenient.
(3) The turnover rate is high, the number of turnovers can be up to 40 to 50 times, the use cost is low, the life is long, and it can be recycled.
(4) Quick and easy demoulding, easy to clean and keep clean.
(5) No shrinkage, no swelling, no cracking, no deformation at temperatures from minus 20 degrees to minus 60 degrees.
(6) Good water resistance.
(7) Strong plasticity.
2.2 Two plastic templates used in this project
This project uses two types of plastic formwork: polyurethane plastic formwork and new hollow plastic building formwork. The same is a plastic template, its performance is different.
The polyurethane template has the advantages of small temperature deformation and easy assembly. Disadvantages are low strength, high cost, low temperature fragility, and less turnover.
The new hollow plastic building template has high strength, light weight, high turnover, installation and removal methods
Convenience and other advantages, and the best surface effect of concrete.
3 Problems and countermeasures of using plastic template
Plastic templates have weaknesses such as low strength and stiffness, poor heat resistance and aging resistance, and large coefficients of thermal expansion and contraction. In practical applications, we must take measures to avoid or weaken these defects.
(1) Problems and countermeasures with small strength and rigidity
Compared with steel formwork, wooden formwork, and bamboo formwork, plastic formwork has lower strength and rigidity. In order to solve this problem, the plastic formwork can mainly meet the construction requirements by appropriately controlling the secondary beam (flute) spacing.
The spacing of the secondary beams supported by the flat plastic formwork is determined according to the thickness of the plate. Under general construction conditions, the spacing between the secondary beams of the floor with a thickness of less than 150 is 250-300 mm. The spacing of secondary beams can be adjusted according to the thickness of the concrete slab. For the plastic formwork of the shear field, take the wall height of 2800mm and the thickness of 300mm as an example. Use 12
High-efficiency extruder to ensure uniform and stable plasticization of materials, and to provide guarantee for subsequent forming and output.
The unique mold design can produce two templates at the same time, truly achieving the effect of one mold and two outputs, high output and high efficiency.
The design of the three-level stereotyped plate ensures the template forming effect and template flatness during efficient extrusion.
The design of the combined tractor can make the template stable and flat during the molding process.
If you want to know more about it please do not hesitate to
contact me. WhatsApp:+86-15966835076.
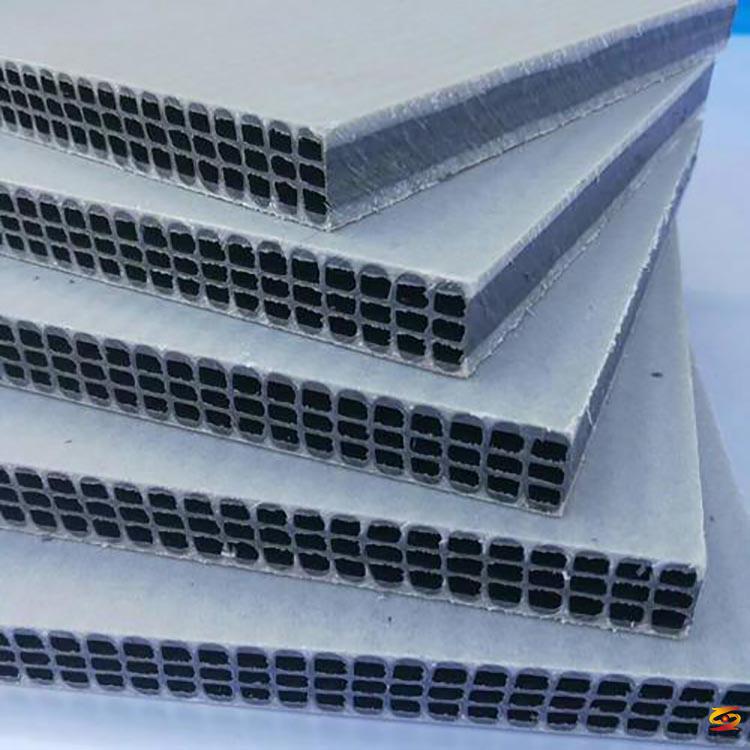
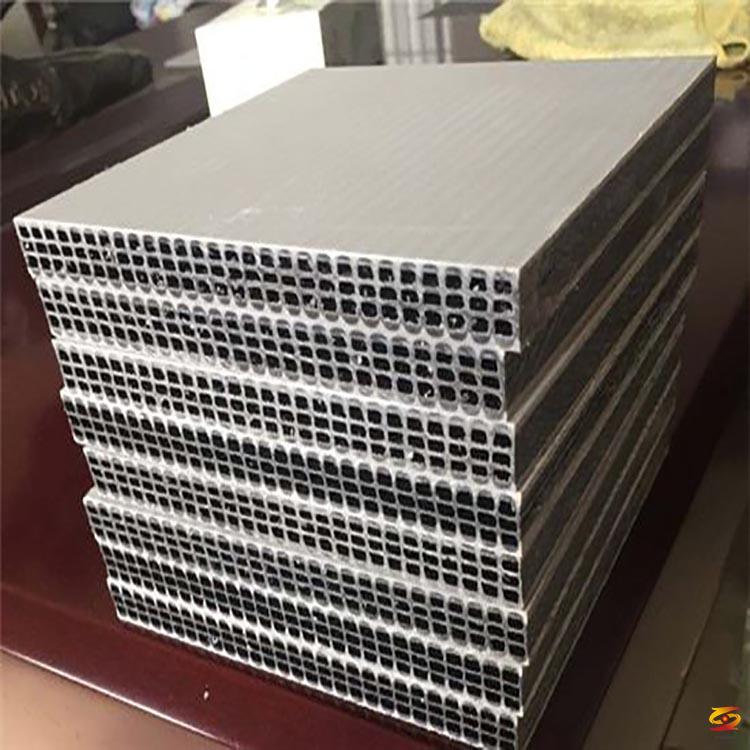
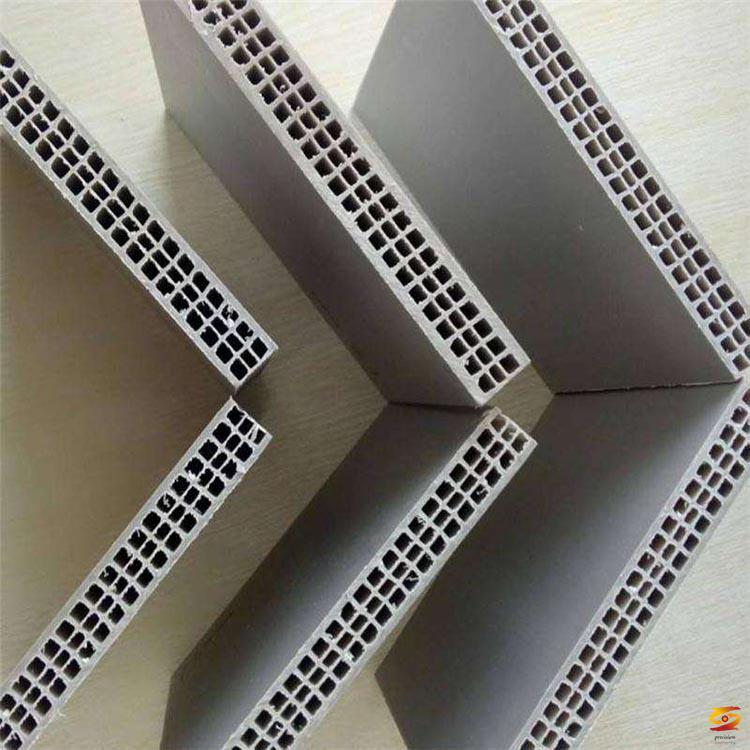
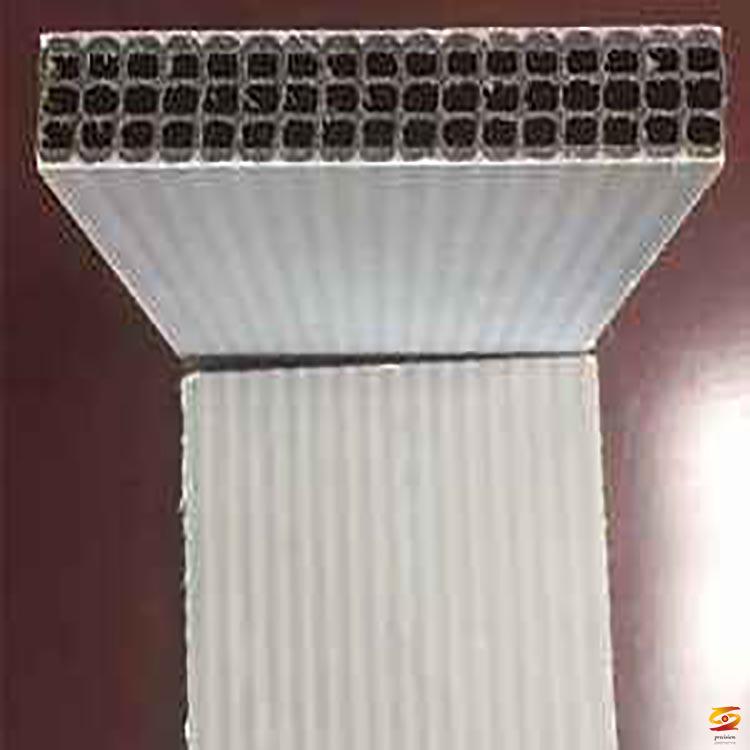