Control Production Process of COD Bundle Tube on Expressway
Control Production Process of COD Bundle Tube on ExpresswayHow to set the pressure during production? How good is it? The pressure in the production process of the cluster tube is mainly that the vacuum pressure is generally controlled between 0.3-0.4Mpa, so as to maintain a certain water level. The steel tube or tube box is used to protect the cluster tube crossing the bridge, and the steel tube or tube box is fixed on the outside of the bridge guardrail. All the elevation gradient sections outside the upper and lower bridge guardrails are also protected by steel pipes. The two ends of the steel pipe at both ends of the bridge should protrude from the bridge slab to the roadbed, with a length of 1-2 meters, and extend to the depth of the communication pipeline to prevent shearing caused by the sinking of the side where the beam and pavement meet. Act directly on the cluster tube. The cluster pipes laid on the same day should be backfilled with 10-15 cm of fine sand to minimize the cluster pipes to prevent damage and the occurrence of them. During and after construction, the pipe mouth should be sealed to prevent water, soil and other debris from entering the cluster pipe. When backfilling pipe trenches, 10-15 cm thick fine sand should be filled first. It is strictly forbidden to directly fill large amounts of stones, bricks, and concrete into the trench.
The small-diameter pipes of each pressure zone of the cluster tube are specified as: 0.6Mpa pipe diameter is 63mm, 0.8Mpa pipe diameter is 50mm, 1.0Mpa pipe diameter is 40mm, 1.25Mpa pipe diameter is 32mm, 1.6Mpa pipe The caliber is 20mm and 25mm. Cluster tube connection is reliable: the polyethylene pipeline system is connected by electrothermal fusion, and the strength of the joint is higher than the strength of the pipeline body. The low temperature impact resistance of the cluster tube: the low temperature embrittlement temperature of polyethylene is extremely low, and it can be safely used in the temperature range of -60-60 ℃. During winter construction, due to the good impact resistance of the material, brittle cracking of the pipe will not occur. The cluster tube has good resistance to stress cracking: HDPE has low notch sensitivity, high shear strength and excellent scratch resistance, and environmental stress cracking resistance is also very prominent. The cluster pipe has good chemical resistance: HDPE pipes can withstand a variety of chemical media.
The materials and equipment must be produced by a professional manufacturer with a production license, with valid quality certification documents, and their quality should comply with the relevant national standards, and unqualified products must not be used. It is obviously not enough to have perfect temperature control for the production of high-quality communication collecting tubes. Combining years of production experience, it is concluded that in addition to temperature, the following points are also very important in the production process of collecting tubes. When the inner and outer layers of the polyethylene bundling tube and the color marking line are molded with HDP resin, the melt flow rate of the selected materials should be close to or the same. The flow rates of the three extruders for extruding the melt should be the same, which is conducive to the mixing of the three melts at the contact interface of the three extruders that are extruded into the composite pipe die at the same time. The working surface of the melt channel cavity in the compound tube forming mold should be smooth and tidy, with no assembly bosses or flat joint warps between the parts; the manufacturing and assembly precision of each part requires high. In order to ensure the smoothness of the inner wall of the collecting tube. Ensure a low friction coefficient on the inner surface of the product.
The chemicals present in the soil will not cause any degradation of the pipeline. Polyethylene is an electrical insulator. The cluster tube is resistant to aging and has a long service life: polyethylene pipes containing 2-2.5% uniformly distributed carbon black can be stored outdoors or used for 50 years without being damaged by ultraviolet radiation. The wear resistance of the cluster tube is good: the comparison test of the wear resistance of the HDPE pipe and the steel pipe shows that the wear resistance of the HDPE pipe is 4 times that of the steel pipe. In the field of mud transportation, HDPE pipes have better wear resistance than steel pipes, which means that HDPE pipes have a longer service life and better economy. The flexibility of the cluster tube is good: the flexibility of the HDPE pipeline makes it easy to bend. In engineering, it can bypass the obstacle by changing the direction of the pipeline. In many occasions, the flexibility of the pipeline can reduce the amount of pipe fittings and reduce the installation cost. The flow resistance of the cluster tube is small: HDPE pipes have a smooth inner surface.
In addition to the traditional excavation method, a variety of new non-excavation techniques such as pipe jacking, directional drilling, liner pipe, and split pipe can also be used for construction. This is for some places where excavation is not allowed. , Is a good choice, so HDPE pipeline applications are more extensive. Good hygienic performance of the cluster tube: no heavy metal salt stabilizer is added during the processing of the PE tube, and there is no scale layer, which solves the secondary pollution of urban drinking water. Long service life of the cluster tube: PE pipes can be safely used for more than 50 years under rated temperature and pressure conditions. Good impact resistance of the cluster tube: PE tube has good toughness and high impact resistance, and heavy objects directly press the pipeline without causing the pipeline to break. Reliable connection performance of the cluster tube: the strength of the PE tube hot melt or electric fusion interface is higher than that of the pipe body, and the joint will not be broken due to soil movement or live load. Good construction performance of the cluster tube: the pipe is light in weight, the welding process is simple, and the construction is convenient.
It can well protect the transmission material inside. The cluster tube is a new type of composite pipeline. The silicone solid lubricant is attached to the inner wall for lubrication and a certain sealing effect. Stable performance and corrosion resistance. In the optical cable communication network system of highways and railways, this kind of pipeline is often used to increase the speed of communication and ensure the safety of roads. In fact, as long as it is used in the optical cable communication network system, this kind of pipeline is mostly used. When the polyethylene tube is extruded, the temperature of the plasticizing process of the extruded raw materials of the three extruders will be different due to the different materials of the composite tube. The material of the outer layer of the cluster tube and the color marking line is high-density polyethylene, and the temperature control of each section of the extruder barrel for extruding these two raw materials is the same as that of the ordinary high-density polyethylene tube. Since the inner liner of the polyethylene manifold is mixed with silane lubricant, the control of the process temperature of each section of the extruder machine is different. The temperature of the feed section of the machine is 100-125 ℃.
The three major elements of machinery: temperature, speed, current, and pressure. The first temperature must clearly understand the temperature required for the raw materials. The temperature of HDPE is 200 ℃ -240 ℃, the temperature of LDPE is 180 ℃ -250 ℃, and the temperature of LLDPE is 180 ℃ -240 ℃. In order to improve the stress cracking resistance and low temperature impact resistance of the product and increase the% of elongation at break, HDPE raw materials can be added 10-20% LDPE and LLDPE to ensure the drop hammer impact performance test results. Practical conclusions summarized in normal work: If generally viewed from the surface of the product, if it is not smooth, the extrusion is not smooth, the temperature is too low, and it can be gradually increased by 3-5 ℃ to reach the required temperature. If the product is naturally enlarged and there is foaming phenomenon, it is that the temperature is too high, you can lower the temperature at any time, wait until the adjusted temperature reaches the required temperature and re-extrude it, and the product surface is found to have slip marks during normal work. .
If you want to know more about it please do not hesitate to
contact me. WhatsApp:+86-15966835076.
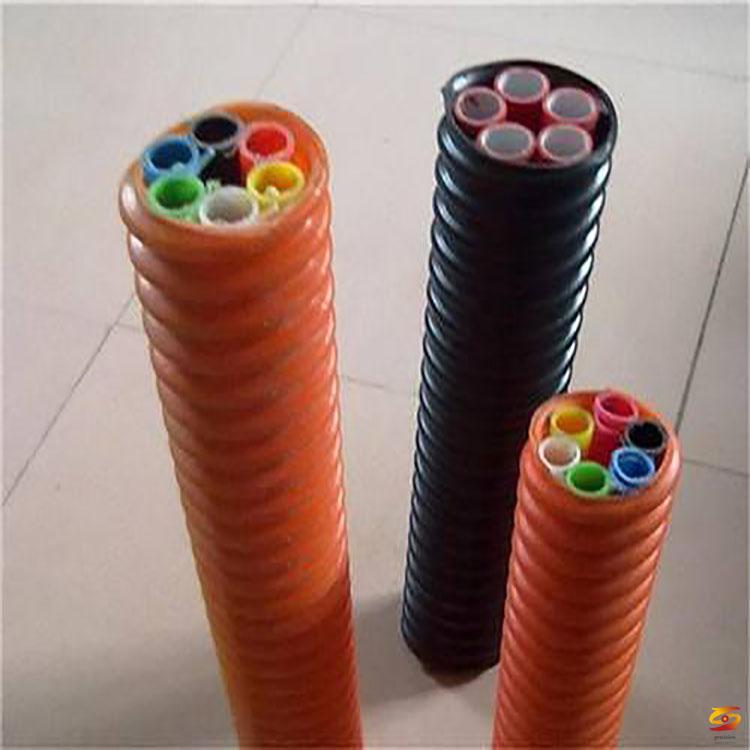
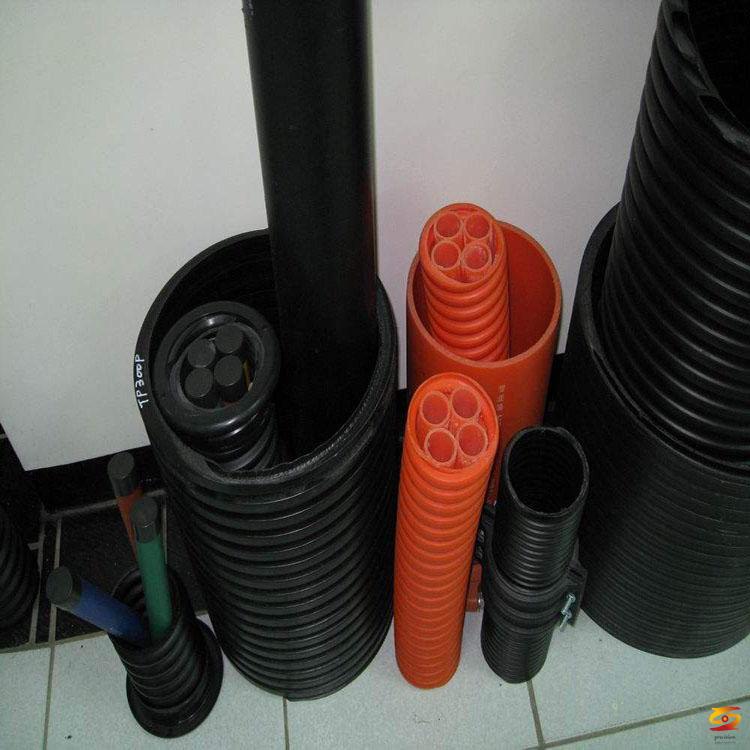
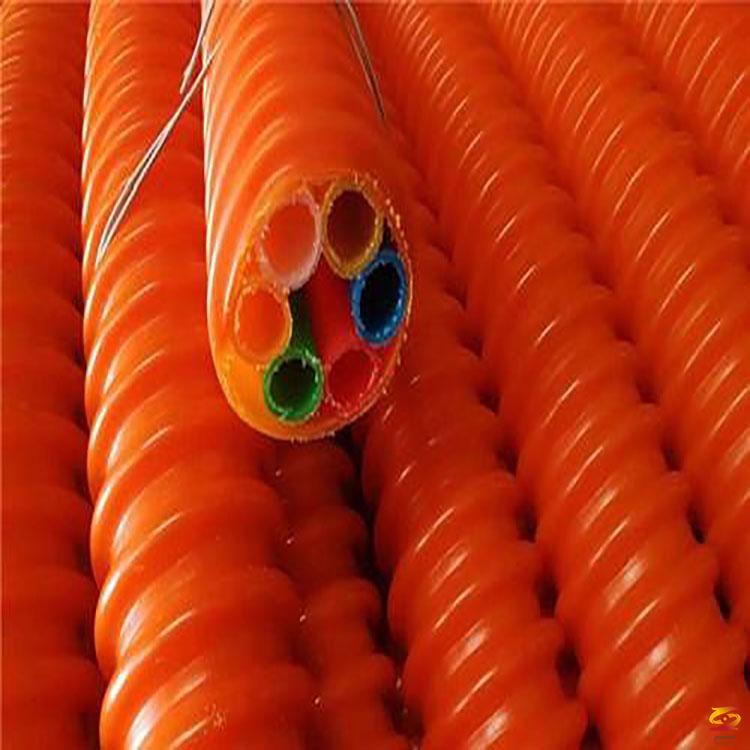
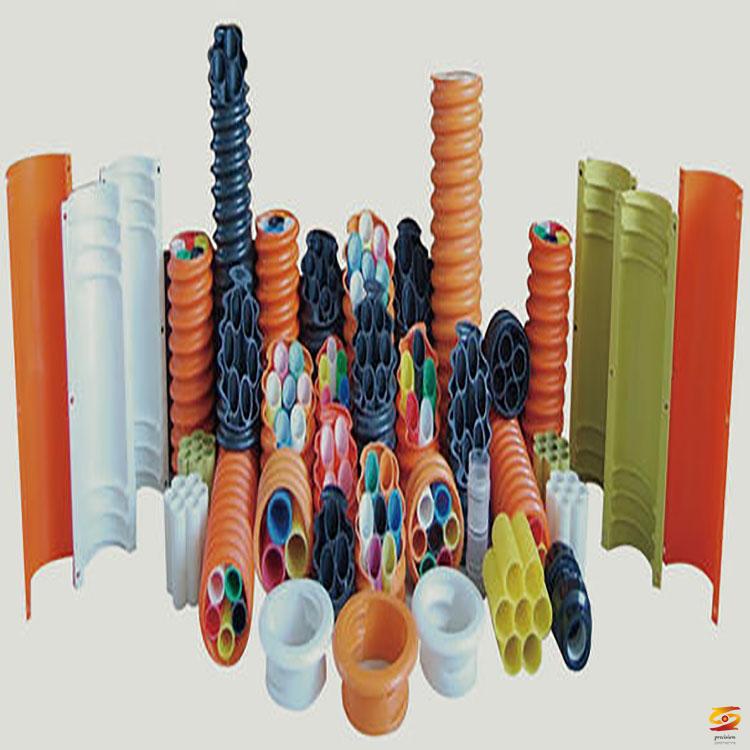