Structure and production process of new material lock SPC floor
Structure and production process of new material lock SPC floorSPC stone-plastic floor: European and American countries call this kind of floor RVP, rigid plastic floor. Lockable SPC stone-plastic flooring is in the stage of active promotion and rapid development in domestic and foreign markets.
The composition of the lock type SPC stone plastic floor:
Floor composition: PVC resin powder, stone powder, plasticizer, stabilizer, carbon black, the main components are polyvinyl chloride and stone powder.
Structure: From bottom to surface, it is composed of PVC base color film decorative paper and wear-resistant layer, and UV coating.
Lockable SPC stone-plastic flooring is a new type of environmentally friendly flooring developed based on high technology. It has the characteristics of zero formaldehyde, mildew, moisture, fire, insect and simple installation. SPC floor is extruder combined with T-shaped die to extrude PVC substrate, using three-roller or four-roller calender to separately apply PVC wear-resistant layer, PVC color film and PVC substrate, and heat and laminate at one time , The process is simple, the fit is done by heat, and no glue is needed.
The lock-type SPC stone-plastic floor material uses environmentally friendly formulas, does not contain heavy metals, phthalates, methanol and other harmful substances, and meets the standards of EN14372, EN649-2011, IEC62321, and GB4085-83. Widely popular in developed countries in Europe and America and the Asia-Pacific market.
With its excellent stability and durability, the stone-plastic flooring not only solves the problem of moisture and deformation of the solid wood floor, but also solves the formaldehyde problem of other decoration materials. It has a wide selection of flower patterns and is suitable for indoor decoration, hotels, hospitals, shopping malls and other public places.
Technological process for producing lock-type SPC stone-plastic floor:
Process 1: Mixing
Automatic metering according to the ratio of raw materials → hot mixing with high-speed mixer (hot mixing temperature: 125°C, the function is to make all kinds of materials mix evenly and eliminate the moisture in the materials) → enter cold mixing (cool the material, prevent caking and discoloration, Cold mixing temperature: 55°C) → Mix uniform materials by cooling;
Process 2: Extrusion
Join the twin-screw extruder to carry out heating extrusion → enter the sheet die head for extrusion molding, the formed piece
The material passes through a four-roll calender, and the base material is set to a thickness → pasted with color film → pasted with a wear-resistant layer → cooled → cut;
Process 3: UV tempering
Surface UV→tempering (tempering hot water temperature: 80~120℃; cold water temperature: 10℃)
Process 4: slitting and grooving
Slitting → slotting, trimming, chamfering → inspection → packaging
If you want to know more about it please do not hesitate to
contact me. WhatsApp:+86-15966835076.
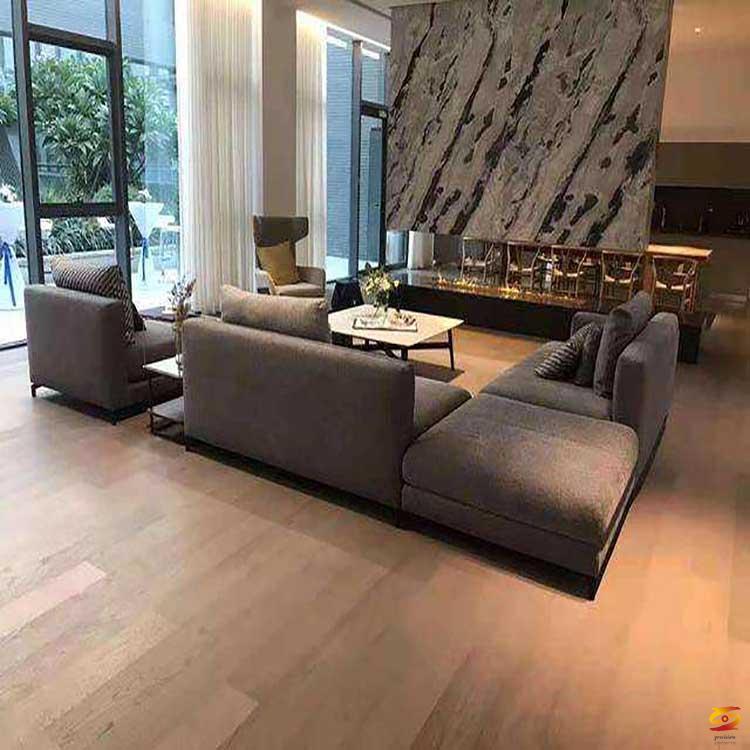
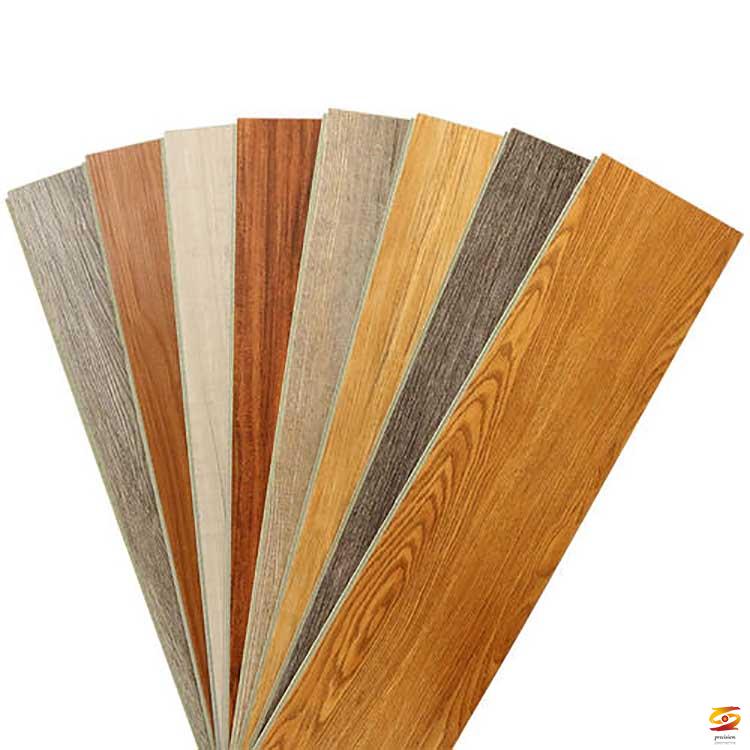
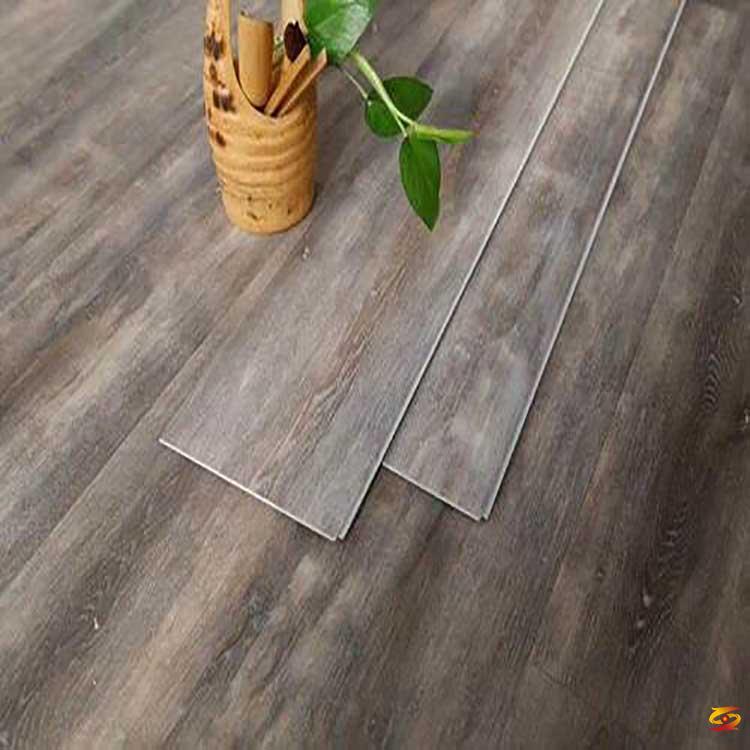
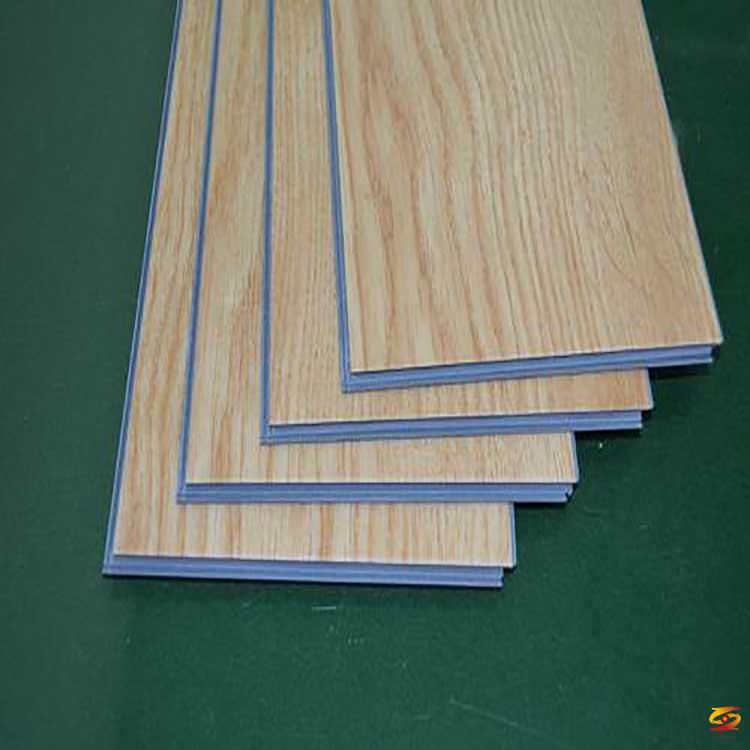