Detailed explanation of PVC wood plastic formula raw material technology
Detailed explanation of PVC wood plastic formula raw material technologyThe materials of PVC wood plastic are mainly PVC resin powder, PVC recycled materials, wood powder, stone powder and some modifiers. PVC wood plastic products can be divided into three methods: vacuum forming, cold push method and three-roller suppression. PVC wood-plastic products are light in weight, good in toughness, moderate in hardness, and widely used. PVC wood plastic products are mainly used for interior decoration materials, such as doors, floors, door covers, etc. The application of wood-plastic features will not introduce too much, and enter the topic! !
The raw material composition and performance of PVC wood plastic
PVC resin plus wood fiber and inorganic filler (wood powder, calcium carbonate), lubricant, stabilizer, foaming agent, foaming regulator, toner and other related additives (plasticizer, toughener, coupling Agent) and other components.
Resin
Don't introduce too much resin, you can Baidu small knowledge, wood plastic domestic mainly use SG-7 resin, SG-7 resin good fluidity is conducive to foaming.
filling
Filled with fiber wood powder (usually about 80-120 mesh wood powder and more poplar wood powder), calcium carbonate according to different quality requirements, different production processes, you can use 2.4 sink light calcium carbonate or 400-1250 Heavy calcium, some wood-plastic floors are processed with coarse powder heavy calcium.
Additive details
PVC wood plastic
Because wood powder has strong water absorption and strong polarity, most thermoplastics are non-polar and have hydrophobicity, so the compatibility between the two is poor, and the adhesion of the interface is very small It is often necessary to use appropriate additives to modify the surface of the polymer and wood powder to improve the affinity of the interface between the wood powder and the resin. Moreover, the high filling wood powder has a poor dispersion effect in the molten thermoplastic, and often exists in a certain state of aggregation, which makes the melt fluidity poor and the extrusion molding process difficult. It is necessary to add a surface treatment agent to improve the fluidity to facilitate Extrusion. At the same time, the plastic matrix also needs to add various additives to improve its processing performance and the performance of the finished product, improve the binding force between wood powder and polymer and the mechanical properties of the composite material. Commonly used additives include the following categories:
stabilizer
Stabilizers used in PVC production include composite lead salt stabilizers, organic tin, calcium zinc stabilizers, etc. The domestic stabilizers generally used for wood plastics are composite lead salt stabilizers, which have the advantages of cheap price and good thermal stability. . The disadvantage is that it is toxic and not environmentally friendly. However, the proportion of compound lead salt stabilizer lubricants is basically about 50%. If the lubricants added are all low melting point lubricants, the performance of the product will also be affected.
Plasticizer
For some resins with high glass transition temperature and high melt flow viscosity, such as PVC, it is difficult to process when compounding with wood powder, and it is often necessary to add plasticizers to improve its processing performance. The plasticizer molecular structure contains both polar and non-polar genes. Under the action of high temperature shear, it can enter the polymer molecular chain, and the polar genes attract each other to form a uniform and stable system. The insertion of polar molecules reduces the mutual attraction of the polymer molecules, making the processing easier. Plasticizers often added to wood-plastic composite materials are dibutyl phthalate (DOS) and the like. For example, in PVC wood powder composite materials, the addition of plasticizer DOP can reduce the processing temperature, reduce wood powder decomposition and fuming, and improve with the increase in the content of the plasticizer DOP, the tensile strength of the composite material decreases and the elongation at break increases .
Commonly used for PVC eco-wood plasticizers are DOP and epoxy soybean oil. DOP can reduce the force between resin molecules and improve fluidity, and has a certain lubricity to facilitate production and processing. But it can reduce the product's Vicat, one kilogram of DOP can reduce Vicat by 3 degrees. The plasticizing effect of soybean oil is not as good as DOP and has a certain thermal stability, which will also reduce the Vicat of the product.
Lubricant
Wood-plastic composite materials often need to add lubricants to improve the fluidity of the melt and the surface quality of the extruded products. The lubricants used are divided into internal and external lubricants. The choice of internal lubricant is related to the matrix resin used. It must have good compatibility with the resin at high temperatures and produce a certain plasticizing effect, reduce the cohesive energy between the molecules in the resin, and weaken the mutual interaction Friction to reduce the melt viscosity of the resin and improve the melt fluidity.
The external lubricant actually plays the role of interface lubrication between the resin and the filler in the plastic molding process, and its main function is to promote the sliding of the resin particles. Usually a lubricant often has both internal and external lubrication properties. Lubricants have a certain influence on the service life of molds, barrels and screws, the production capacity of extruders, the energy consumption in the production process, the surface finish of products and the low-temperature impact performance of profiles. Commonly used lubricants are: zinc stearate, ethylene bis fatty acid amide, polyester wax, stearic acid, lead stearate, polyethylene wax, paraffin wax, oxidized polyethylene wax, etc.
Stearic acid, paraffin wax, PE wax, calcium stearate, etc. are generally used to form a wood-plastic lubricant system in the required ratio. Stearic acid and paraffin are cheap and have good lubricating properties. The disadvantage is that the melting point is too low (more than 50 degrees). The lubricant with low melting point also acts as a plasticizer while giving lubricity, which affects the rigidity of the product The low temperature of Vicat and heat deformation makes the product easy to deform with increasing temperature, and it is very easy to precipitate to affect production. If the PE wax is produced from new PE materials and is 100% pure, the melting point can reach more than 80 degrees, which will not reduce the Vicat of the product. If PE wax manufacturers use recycled PE materials in order to reduce costs and add a certain proportion of stearic acid and paraffin wax, this is not a real PE wax and will also affect the performance of the product.
Colorant
During the use of wood-plastic composite materials, the solvent substances in the wood powder easily migrate to the surface of the product, discoloring the product, and eventually turning gray. Different products may produce black spots or rust spots under certain usage environments. Therefore, colorants are also widely used in the production of wood-plastic composite materials. It can make the product have a uniform and stable color, and the decolorization is slow.
The toner suitable for ecological wood is generally yellow, red, black, titanium dioxide, etc. The yellow and red toners are inorganic and organic. The advantage of inorganic toner is that it is superior to organic toner in weather resistance, migration resistance and high temperature resistance. The disadvantage is that the amount of addition is large, and it is not suitable for brighter colors, but the price is cheap. Organic toner is the opposite. Ecological wood is generally used with organic and inorganic toners. There are two types of titanium dioxide: R titanium and anatase. R titanium has better hiding power and weather resistance than anatase, so ecological wood generally uses R titanium titanium dioxide.
Blowing agent
Wood-plastic composite materials have many advantages, but due to the composite of resin and wood powder, its ductility and impact resistance are reduced, the material is brittle, and the density is nearly twice that of traditional wood products, which limits its widespread use. Since the foamed wood-plastic composite material has a good cell structure, it can passivate the crack tip and effectively prevent the expansion of the crack, thereby significantly improving the impact resistance and ductility of the material, and greatly reducing the density of the product . There are many types of foaming agents, and there are two main types commonly used: endothermic foaming agents (such as sodium bicarbonate NaHCO3) and exothermic foaming agents (azodicarbonamide AC), which have different thermal decomposition behaviors. The viscoelasticity of the melt and the foaming form have different effects, so the appropriate foaming agent should be selected according to the use requirements of the product.
Generally, AC foaming agent and baking soda are used together, and AC foaming agent and sodium bicarbonate are also used. AC foaming agent has the advantages of large gas generation and small dosage. The disadvantage is that incomplete decomposition will leave a small part in the product. This will affect the appearance of the product during use, and the foaming agent will migrate to the surface of the product to produce spots and shadows. The weather resistance of the product accelerates the aging of the product.
UV stabilizer and others
The application of UV stabilizers has also developed rapidly with the improvement of the quality and durability requirements of wood-plastic composite materials. It can prevent the polymer in the composite material from degrading or reducing the mechanical properties. Commonly used are hindered amine light stabilizers and ultraviolet absorbers. In addition, in order to maintain a good appearance and perfect performance of the composite material, it is often necessary to add an antibacterial agent. The selection of the antibacterial agent should consider the type of wood powder, the amount of addition, the fungi in the environment of the composite material, and the content of the product. Various factors such as water volume. Such as zinc borate can be antiseptic but not algae.
If you want to know more about it please do not hesitate to
contact me. WhatsApp:+86-15966835076.
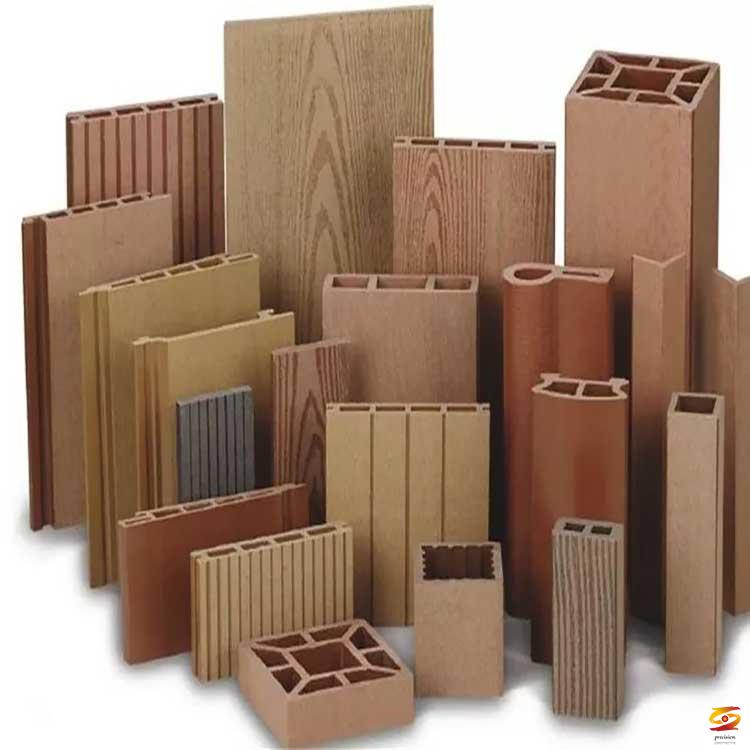
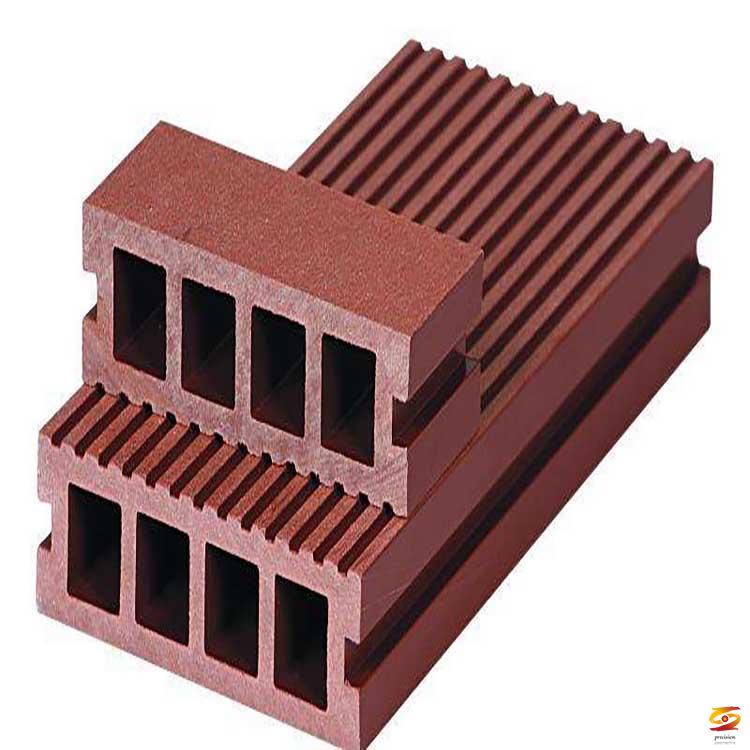
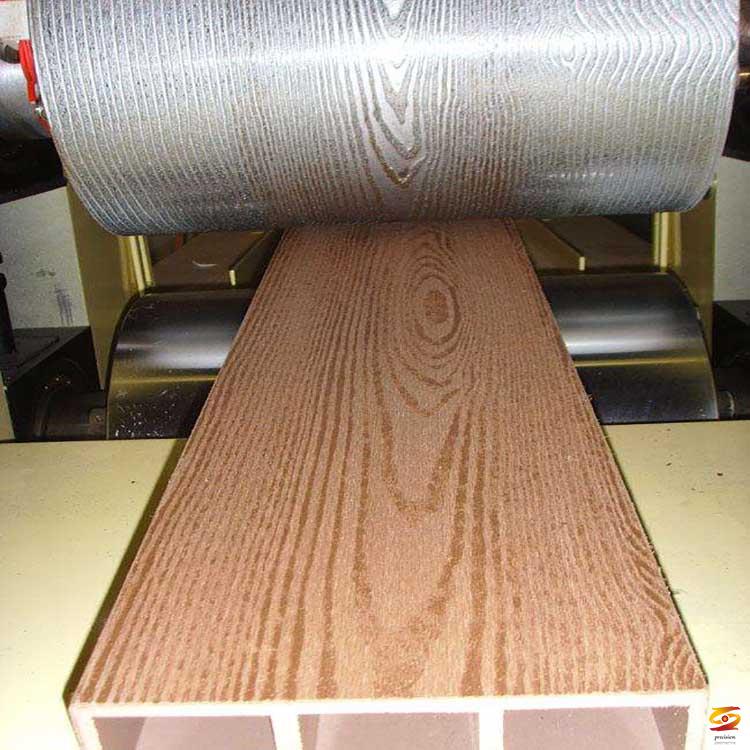
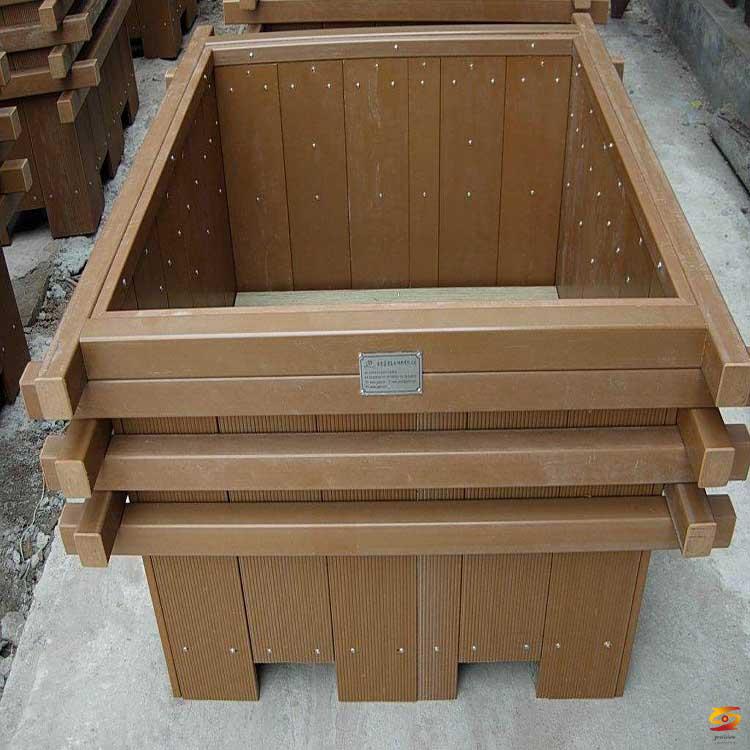
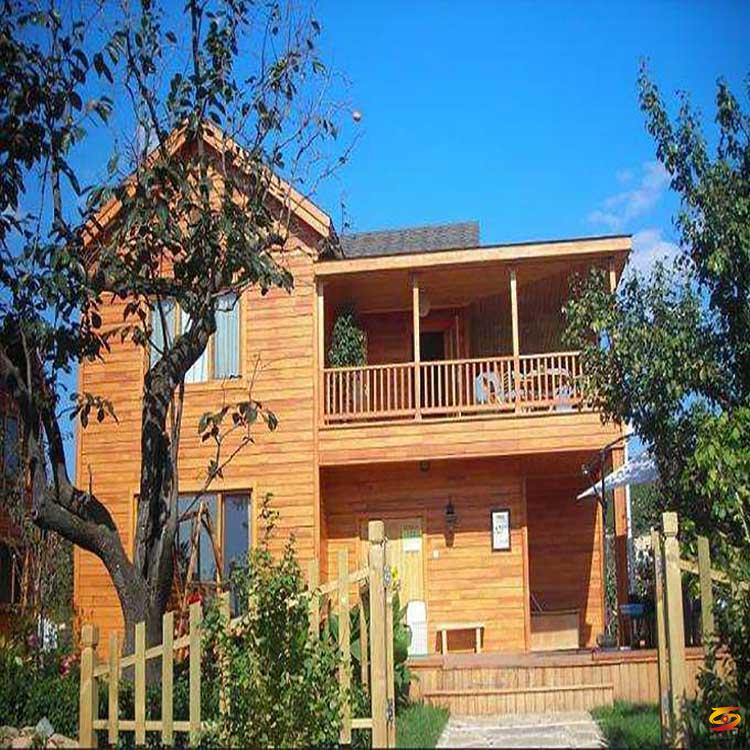