Discussion on Production Technology and Formula of PVC Foam Advertising Board
Discussion on Production Technology and Formula of PVC Foam Advertising BoardDue to its excellent performance, PVC foam materials are widely used in construction, building materials, decoration, furniture, advertising, automotive and other industries, and have developed rapidly in recent years. PVC foam board is also called Andy board and Chevron board. It can be divided into two categories from product appearance, performance and production process: ① skinned foam board, which is produced by the principle of Celuka, with a hard layer on the surface, Smooth and flat, high hardness, good mechanical properties, high product accuracy, small thickness error, strict requirements for molds, formulas, materials, and production processes; ②free foamed sheet, the product surface is loose and no skin, and it is a fine uneven surface It is good for printing, spraying and veneering. It can be produced by using ordinary foaming molds, and the process is relatively easy to control.
1 Process and formula
At present, most of the domestic crust-foamed PVC sheet production lines are imported equipment, and the free-foamed PVC sheet production line mainly uses domestic equipment. The commonly used main machine is generally an 80-cone twin-screw extruder. The die differs greatly and the main production process is roughly the same.
1. 1 main formula
The main formula of PVC foam board is shown in Table 1.
1. 2 Craftsmanship
Weigh the raw materials accurately and feed them in the order required by the process. Determine the addition time of the blowing agent according to the type of blowing agent used, and reach the end point of kneading. When the temperature of the material reaches about 125 ℃, quickly put the material into a cold stirrer to cool, and reduce the temperature to about 50 ℃, in order to prevent agglomeration and premature decomposition of the foaming agent and affect the foaming ratio, resulting in an increase in product density. The process flow is shown in Figure 1.
1. 3 Extruder process parameters
Zone 1: 175 ~ 186 ℃, Zone 2: 180 ~ 186 ℃, Zone 3: 185~190 ℃, connector: 175~185 ℃, machine head: 190~200℃, host current: 50~70 A, screw speed : 14~22 r/ min.
2 Components of PVC foam sheet
2. 1 PVC resin
For the production of rigid PVC foamed products, PVC resin with a low K value is generally selected. P-700 type PVC resin is generally used for the production of PVC foamed sheet. The gelation speed is fast during processing, the processing temperature is relatively low, the product quality is stable, and the density is easy to control. In the production of skinned foamed PVC sheet, in order to improve product quality, strict control
For the fluctuation of product density and thickness, P-700 type vinyl PVC resin is mostly used. In the production of free-foaming PVC sheet, from the viewpoint of reducing production cost, many manufacturers have adopted calcium carbide method P-700 type PVC resin.
2. 2 stabilizer
In the production process of PVC foamed sheet, in order to fully plasticize the material, the temperature of the material is high; and the sheet mold has a wide cross-section and a long flow channel, especially the long setting section of the skinned foamed sheet mold; in addition, The foaming agent also generates heat of decomposition during the decomposition process. These factors require that the stabilizer must have sufficient thermal stability to ensure product quality and long-term stable production. Lead composite stabilizers with a mass fraction of lead oxide of about 60% are mostly used in the production of ordinary PVC foamed sheets; calcium-zinc composite stabilizers and organic tin composite stabilizers are mostly used in the production of exported foamed sheets and environmentally friendly decorative sheets and furniture Use plates. The lead oxide and metal salts of stearic acid in the lead-based composite stabilizer have an activation effect on the ADC foaming agent, which will broaden the decomposition temperature of the ADC foaming agent. Although the foaming temperature is lowered, attention should be paid to the stability of the molten material leaving the die to avoid local bursts and blistering. Lead-based composite stabilizers and calcium-zinc composite stabilizers mostly contain a certain amount of paraffin, stearic acid and metal salts of stearic acid. In the formulation system, these components have a good lubricating effect, and they should be considered comprehensively.
The role of body lubrication performance.
2. 3 ACR and foam regulator
ACR-401D is formed by copolymerization of methyl methacrylate, ethyl acrylate, butyl acrylate and styrene. Its molecular structure is core-shell structure. As a processing aid in the formulation system, it can effectively reduce the plasticization temperature and promote plasticity. Chemical effect, improve plasticizing efficiency, increase melt strength, reduce melt pulsation, prevent melt fracture, and significantly improve the surface smoothness of products. Foaming regulator is a high-quality polymer with multilayer structure made of multiple monomers of acrylic esters through multi-stage emulsion polymerization. Its composition and mechanism of action are similar to ACR, but in the formulation system, it focuses on regulating foam.孔结构。 Hole structure. During the extrusion process, the foaming regulator is wrapped around the PVC macromolecules in the form of molecules to form a network structure, which can not only promote the plasticization of PVC, but also significantly improve the strength and ductility of the foamed melt, making the hair The expansion of the foam melt is in a stable and controllable state, resulting in a PVC foam sheet with a uniform and fine cell structure and good independence. Whether in the production of skinned foamed sheet or free foamed sheet, ACR-401D and foaming regulator are usually used together. Because the core-shell structure and the network structure formed by ACR-401D and the foaming regulator itself have a significant effect on improving the impact strength of the product at normal and low temperatures, the impact modifier CPE is generally not added in the production process now. ACR-401D produced by Jinhong Rohm and Haas Chemical Co., Ltd. can be used in crust foamed sheet and free foamed sheet. The foaming regulators J HB-24 and J HB-26 produced by the company are mostly used to produce crust foaming boards, the general dosage is about 6 parts; J HB-42 and J HB-100 are mostly used for free foaming boards, generally The dosage is about 8 servings. With proper amount of foaming agent and lubricant, the density of the board can be controlled at 0.45~0.50g/cm3. However, some manufacturers only consider reducing costs, ignoring the effective ingredient content of ACR and foaming regulator, and the side effect of ineffective ingredients
The effect of use makes the product density difficult to control effectively, and even the production stability is poor, the defective rate is high, and the overall cost is greatly increased.
2. 4 blowing agent
The basic requirements for preparing foamed products are: the molten material cannot foam before leaving the die lip; the decomposition temperature of the foaming agent should match the melting temperature range of PVC, and the residual amount of the foaming agent should be as small as possible to ensure melting The foaming agent is completely decomposed between the material leaving the die and the shaping die. The melt expanded evenly after the pressure was released. Even in the case of high-speed extrusion, the expansion of the melt remained at a gentle rate, and the phenomenon of localized bubble accumulation and continuous blistering could not occur on the surface. The commonly used ADC foaming agent has many advantages, but after it is activated, the decomposition temperature is too wide. After leaving the die, it is easy to produce local blistering phenomenon, leaving scars on the surface of the product and increasing the defective rate. . It should also be mentioned that because the ADC blowing agent contains azo groups, the decomposition residue will affect the detection of the product's environmental performance, and it should pay more attention to export products.
The environmental protection type PVC rigid foaming product special foaming agent produced by Yuzhou Zhongkai Auxiliary Factory in Henan Province has good processing performance, its technical indicators: the appearance is white fine powder, the working temperature is 180~200 ℃, hair The gas volume is 180 mL/g, the effective content is> 98%, and the water content is <0.5%. The product is easy to disperse in the material, the cells are fine and uniform, and the product density can be effectively controlled at 0.45 to 0.50g/cm3. The fine characteristics of the cells and the closed-cell structure are conducive to the formation of a dense and smooth surface. When the density requirements are met, the surface is hard
The degree can reach about 80 Shore D hardness. The foaming agent is an endothermic reaction, which can avoid the phenomenon of degradation and yellowing caused by overheating of the core layer, and is particularly important in thick-walled products. It is confirmed in production practice that the use of this foaming agent can make the production stable and controllable. When the extrusion rate is increased by 30%, the molten material leaves the die and maintains a gentle expansion rate.The production stability and product stereotypes are good. Effectively reduce the dimensional deviation of products.
2. 5 Lubricants
In the design of the formula, the initial lubricity of the system must be fully considered for the PVC foam sheet to reduce the shear heat and friction heat; the lubricity at the later stage must also be considered, so that the molten material still has good external lubricating properties at high temperatures. There is no precipitation or scaling during long-term stable production. Honeywell China's PE wax A-C 6A has good initial lubrication and improves the surface finish of the product; A-C316A has good late lubrication and promotes plasticization of the material. Its main properties are shown in Table 2.
2. 6 filler
In the formulation system, the amount of light calcium carbonate is generally 10 to 40 parts. In addition to being used as a foaming nucleating agent, it can also reduce material costs. However, if the amount is too large, the uniformity of the cells becomes worse, affecting the appearance quality, and the product density is difficult to control, resulting in an increase in overall cost.
3 Performance of PVC foamed sheet
The performance index of PVC foamed board produced by this formula is shown in Table 3.
4 Conclusion
When designing the formula of PVC foamed board, we should fully understand the content of the active ingredients of various additives and the side effects of the ineffective ingredients to ensure product quality and improve product quality. At the same time, the relationship between formula cost and comprehensive cost should also be mastered to achieve the best economic benefit.
If you want to know more about it please do not hesitate to
contact me. WhatsApp:+86-15966835076.

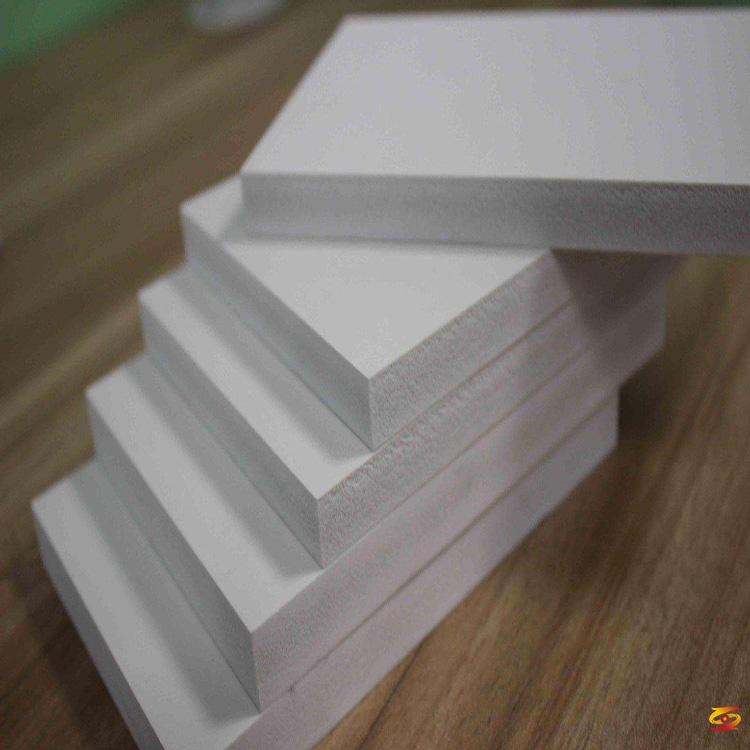
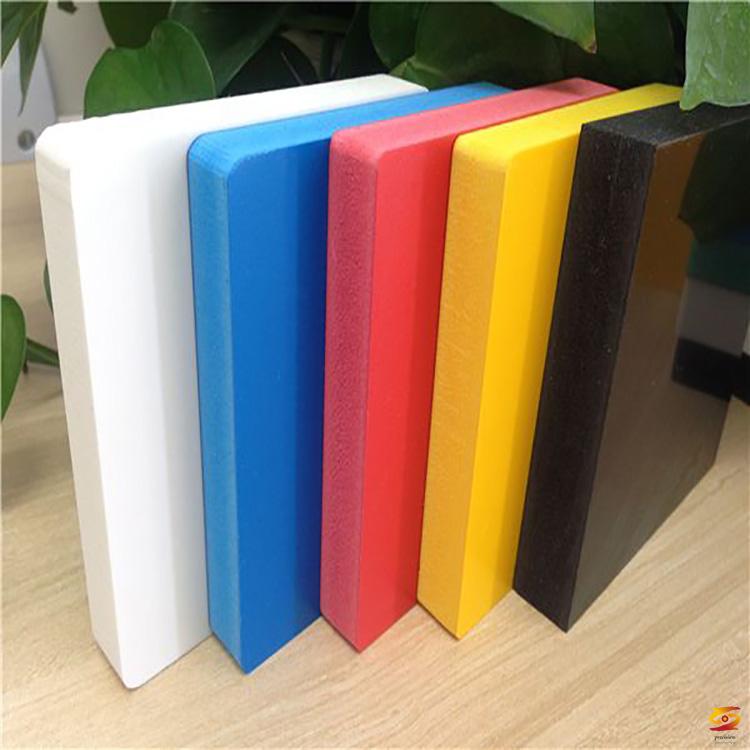
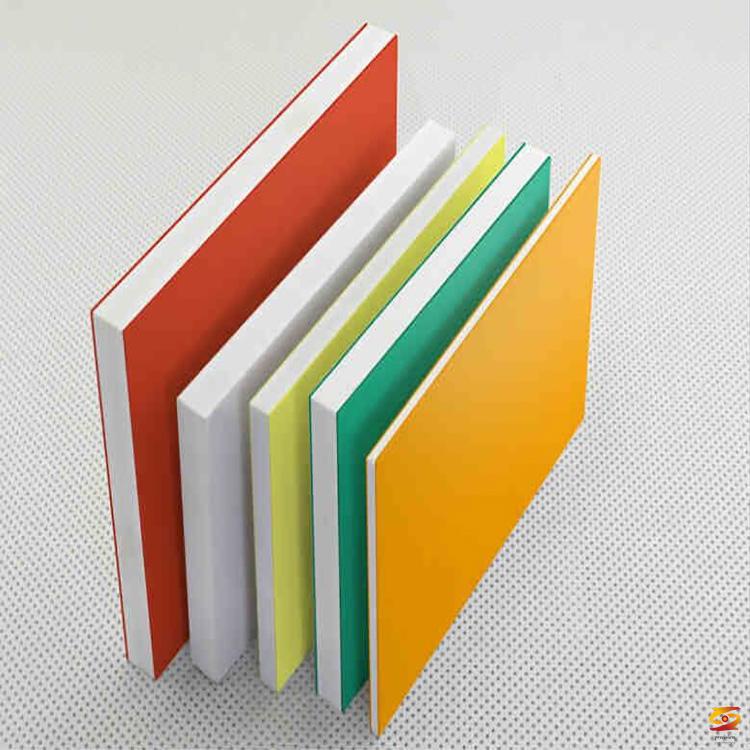