Five factors that affect the quality of PVC foam board and six common problems, causes and solutions worth learning
Five factors that affect the quality of PVC foam board and six common problems, causes and solutions1. Five factors affecting quality
In the extrusion process of PVC foam board, the problems encountered can be basically classified into five categories. One is stability problems; the other is melt strength problems; the third is lubrication problems; and the fourth is dispersion problems. These five types of problems, especially the first three types of problems, will be mutually restrictive and cross-influential. From the surface, it is sometimes difficult to distinguish them immediately. It is necessary to observe and analyze the situation and find the root cause of the problem before it can be solved.
1. Insufficient stability will affect the whole board surface, the board surface is yellow, and the foamed sheet is brittle
2. Insufficient melt strength will cause foaming sheet to have large cells and long longitudinal section.
The most direct way to judge whether the melt strength is insufficient is to press the plate wrapped on the middle roll with your fingers after the three rolls. When the melt strength is good, you can feel the elasticity. If it is difficult to pop up after pressing, it indicates that the melt strength is poor. Because the screw structure and cooling method are quite different, it is difficult to judge whether the temperature is reasonable. Generally speaking, within the allowable load of the extruder, the temperature in zone 3-5 is better. In order to obtain foamed uniform products in foamed pipes, it is also necessary to ensure that PVC materials have good melt strength. Therefore, the quality and type of the foaming regulator is of utmost importance. Of course, the yellow and white foaming agent should be matched well.
3. Lubricant
Lubricants are divided into external lubricants and internal lubricants. The external slip is good for demoulding, which is good for the surface finish of the sheet. The external slip is too little. The temperature in the 5 zone of the extruder is not easy to control and easy to heat up, which will cause the confluence core High temperature, large bubbles in the middle of the plate, stringing, yellowing, etc., and the surface of the plate is not smooth; too much slippage, precipitation will become serious, the structure shown in the mold and the precipitation of the slide surface of the plate will also show Some individual phenomena move back and forth from time to time on the board. Inner slip is good for plasticization and melt fluidity. Insufficient inner slip is difficult to control the thickness of the board surface, which is shown as the middle thickness of the plate is thin on both sides. The more inner slip, the higher the temperature of the confluent core.
4. Poor dispersion will cause the surface of the board not smooth
Process temperature control problem: The four problems mentioned above are fundamental problems, they are the foundation and the deep problems. Compared with the above four problems, process temperature control is much more intuitive and is a surface problem, but poor temperature control will induce the emergence of fundamental problems. Increasing the processing temperature, the material stability time will be reduced, and stability problems will occur; the original lubrication balance will be broken, generally manifested as insufficient external lubrication, especially in the later period of external lubrication, the need to increase the amount of external lubrication; temperature increase will also lead to The melt strength is reduced, the foaming sheet foam cells are increased, the number of cells is reduced, the sheet is brittle and easy to break; increasing the temperature reduces the melt strength and also reduces the melt viscosity, the viscosity is reduced, the shear dispersion ability is reduced, the dispersion In the case of a screw with a weak capacity, uneven dispersion sometimes occurs.
5. The more foaming agent, the better the foaming, the lower the density, the lighter?
In the actual production, we met many customers of PVC foam products. The products showed large cells or the weight could not be reduced. I asked various experts and friends and got an answer that convinced them: This is the addition of foaming agent. If it is not initiated, more foaming agent will be added, so it is naturally initiated. The situation was even worse, so they discussed another way together to increase the amount of foaming regulator, and the results improved somewhat until the amount of regulator added was sufficient without any problems.
The yellow foaming agent AC is the most used in PVC products. When AC is added to the product, it will decompose under heat and generate a lot of heat. The product expands and the melt strength decreases until the small bubbles generated by the decomposition of the AC foaming agent cannot be covered. , A large number of small bubbles will merge into large bubbles, and the decrease in density is hindered. To this end, we must add a foaming regulator to reinforce, to increase the melt strength, so that the bubbles are evenly distributed to reduce the density.
Speaking of some people here, it’s not the same as the first paragraph. No, here we introduce a concept, specific surface area, refers to the total area of the material per unit mass. There are two types of external surface area and internal surface area. For a substance of the same volume, the larger the specific surface area, the lower the density and the lighter the mass.
When a certain amount of AC and foaming agent are added, innumerable small bubbles of uniform size are formed, and the cells are fine and uniform. At this time, the specific surface area is the largest. When the amount of AC exceeds the enhanced melt strength range of the foaming regulator, small bubbles will bubble up, and many small bubbles form a large bubble. At this time, the specific surface area will decrease and the density will naturally increase. There are even bubbles in the cross section, and even more, the middle and the two sides are layered.
So how do we adjust for problems such as cells? I think that after carefully reading the above text, there is already an answer. First of all, increase the amount of foaming regulator or reduce the amount of foaming agent. One of them is to facilitate the search for the reason. Of course, the cost consideration is of course the latter is the best policy, which is to reduce foaming. If the dosage of AC is improved, continue to decrease to normal. Therefore, it is of course wrong to increase the amount of blowing agent in the first stage.
In addition, in order to obtain more superior products in the production process, it is recommended to add a white endothermic foaming agent to offset the excess heat released during the AC decomposition process.
In actual production, there are often more reasons for the occurrence of cells. There are reasons for the process. We cooperate with a good process and adjust the formula, and we can quickly make products with uniform foaming, light weight and good mechanical properties. Specific problems also require specific analysis.
Two, six common problems, causes and solutions
1. The board surface turns yellow. If the extrusion temperature is too high or the stability is insufficient, the solution is to reduce the processing temperature. If the improvement does not occur, the formulation can be adjusted, and the stabilizer and lubricant can be added appropriately. It can be changed one by one. It is easy to find the problem quickly and solve the problem at the fastest speed ;
2. Yellowing in the middle of the board. The main reason is that the temperature of the core of the barrel is high and the temperature of the mold is also related to the amount of lubricant. Once again, it has a certain relationship with the white foaming agent;
3. The board surface is bent. Uneven material flow or inadequate cooling, the factors causing uneven material flow are generally large traction fluctuations or unbalanced internal and external lubrication in the formula. The factors of the machine are easy to eliminate. Formula adjustment generally adjusts internal lubrication under the premise of as little external lubrication as possible Very good results, while ensuring that the cooling is evenly in place.
4. Foam cells or bubble delamination appear on the cross section. The reason can be attributed to one point, that is, the melt strength is not enough, the reasons for the insufficient melt strength are: 1. excessive foaming agent or insufficient foaming regulator or inconsistent ratio of the two, or quality problems of the foaming regulator 2. plasticization Bad, low processing temperature or excessive lubrication
The foam plastic sheet section has two factors that break the bubble or break through the bubble:
A. Because the local strength of the melt itself is too low, the bubble breaking is formed from outside to inside;
B. Because the pressure around the melt is too small, local cell expansion occurs, the strength is weakened, and the bubble breaking is formed from the inside out. In the production practice, there is no obvious difference between the two functions, which may exist at the same time. Most of the broken holes are caused by the uneven expansion of the local cells and the decrease in melt strength. The strength of the melt itself is too low and the pressure around the melt is too small. In summary, there are mainly the following aspects.
5. Uneven thickness of the board surface. Uneven material output, adjustable die lip opening, if the flow rate is too large, the choke bar can be adjusted, the formulation is adjusted, generally the inner lubrication has more middle thickness, and the outer lubrication has more feeding on both sides.
6. Changes in plate thickness and lines that are likely to occur during handover. The main reason is related to the mixing. After the last shift, the interval between the mixing is long after the next shift. The mixing barrel is cooled well. The first pot is pre-plasticized, which is the same as the previous mixing. Differences are formed, and when other conditions remain unchanged, fluctuations are likely to occur, which can be adjusted by adjusting the traction, processing temperature, or through management.
PVC foam board product testing methods:
(1) The side of the board: the cut is smooth, the pores are fine, there are no pinholes, no large holes, the powder is not serious, there is no bee holes, and the cutting fibers fall off automatically and do not jump. Note: Please pay attention to the above situation.
(2) Board surface: smooth and smooth feel, no obvious mechanical texture, no color difference on the surface, milky white, no stain on the surface, no obvious pits, no pinholes, no large holes, cracks. Note: The non-milky foamed board infiltrates the recycled waste board, which is not an environmental protection board. The environmental protection board does not contain lead (the content is less than European and American standards).
(3) Density algorithm: density = weight (g)/length*width*thickness (cm).
(4) Board weight algorithm: weight (g) = length * width * thickness (cm) * density.
(5) Thickness measurement: When the caliper is placed on the surface, the contact is tight and seamless, and the left and right thicknesses are uniform. The left and middle and right measurements are made. Whether the deviation is large, and the thickness deviation is plus or minus 0.2MM is normal.
Practical recipe sharing
Advertising version Density 0.3 (Kg/m³)
Name Weight (Kg)
PVC 75
Calcium 50
Return 40
Stabilizer 3.4
60 0.42
PE 0.28
0A6 0.4
White foam 1.4
Yellow foam 0.4
Ultramarine 0.018
Brightener 0.08
Titanium dioxide 1.5
Conditioner 10
If you want to know more about it please do not hesitate to
contact me. WhatsApp:+86-15966835076.
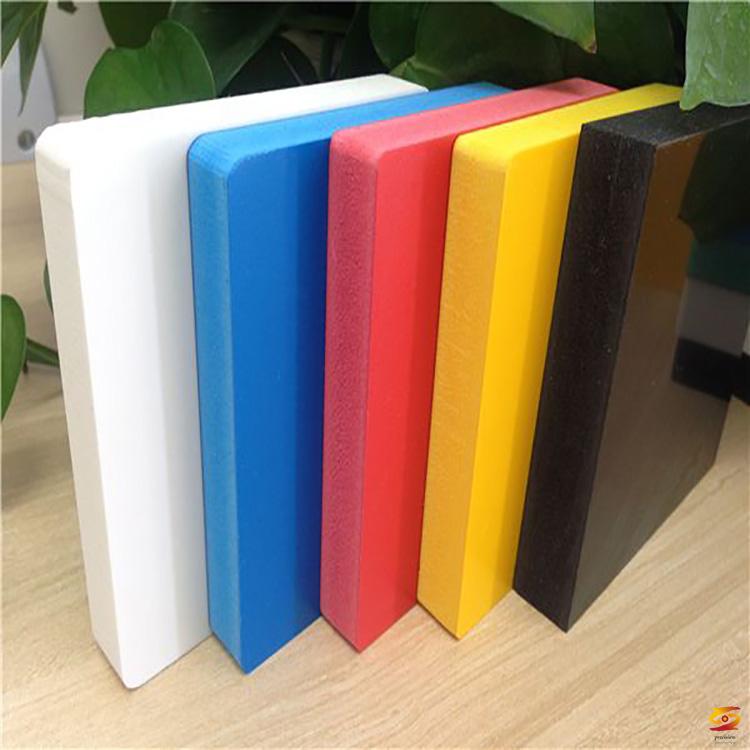
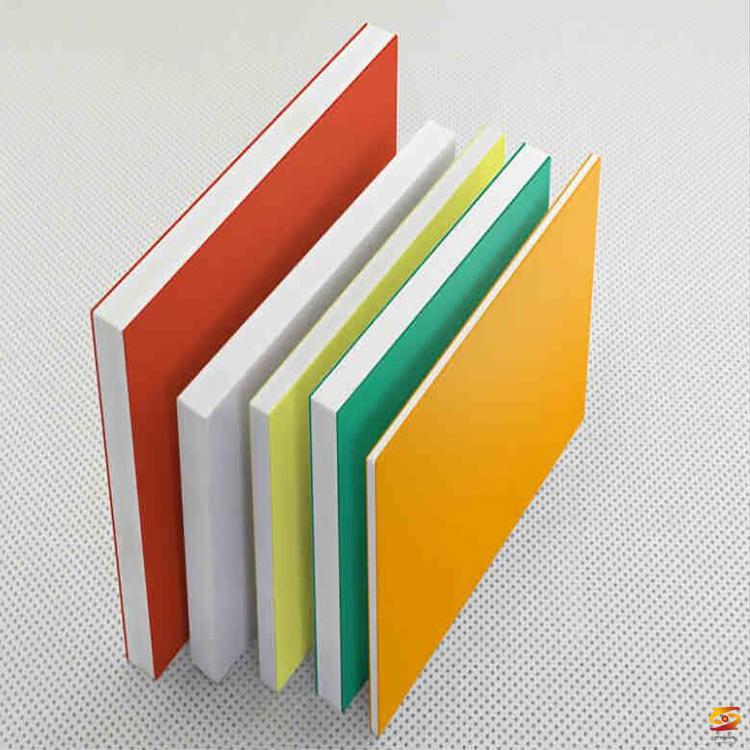
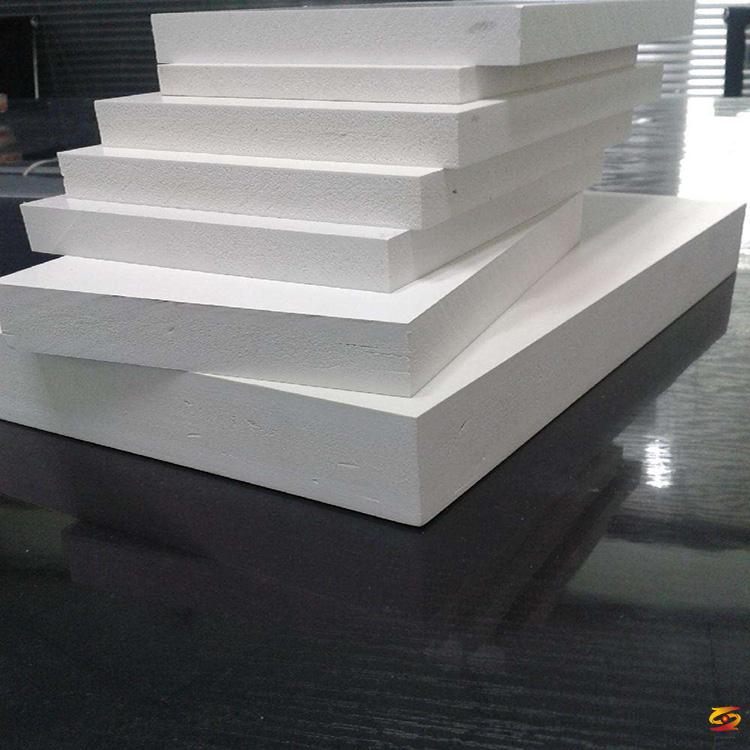
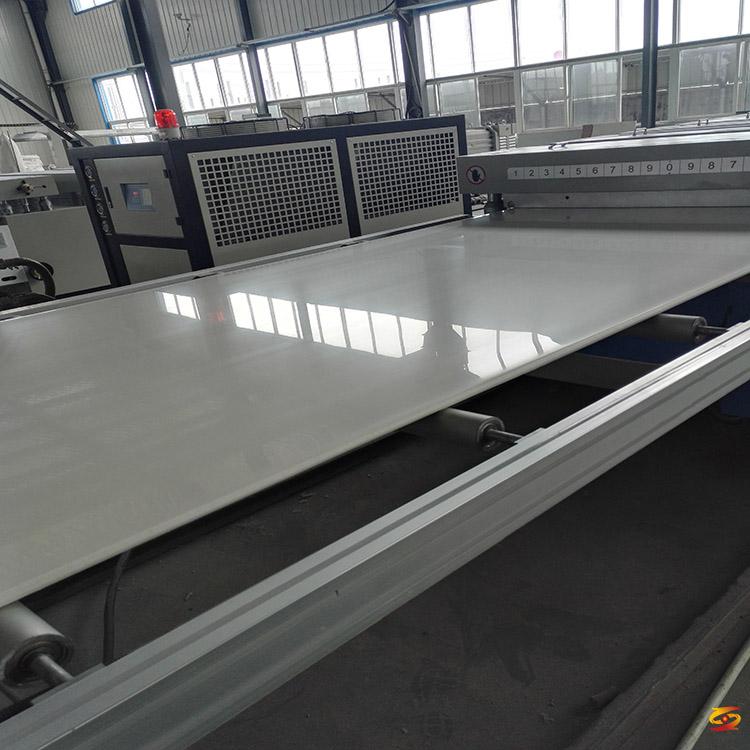