How to produce qualified meltblown cloth, experience sharing.
How to produce qualified meltblown cloth, experience sharing.What does it take to produce N95? One machine, the second master, the third process, and the fourth melt-blown material.
However, the current market models are quite confusing, and the artillery machine is flying all over the sky. Many friends have consulted. Can the artillery machine improve the quality of the meltblown cloth to reach 90 or 95 standard meltblown cloth?
In fact, whether it can produce 95 standards, not the size of the machine, mainly depends on whether it can resist profiteering, whether it can strictly use materials, and strictly rigorous production technology.
In addition to the different raw materials, the production of qualified melt-blown cloth differs on the machine. The parameters of the melt-blown cloth die, melting temperature, air volume and wind speed, and static electret are all different.
In addition to the machine, if you have the master of the cow X. The following are years of experience sharing, collection, and forwarding of the first-line sizing machine masters from major melt-blown fabric manufacturers!
1. How to make N95 with small machine and earth gun machine
1. Small machines are generally defined by the screw diameter, and large machines are defined by the width (width) of the cloth, which is the effective width of the spinneret.
2. There is no pressure sensor for the earth machine, and there is no non-stop screen change. The material pressure increases, the friction of the screw heats up, the actual melt material temperature far exceeds the set temperature, and the cloth will be brittle.
3. The heating system of the small machine is controlled by the AC contactor. The heating plates are output and stopped at full power. The temperature of the heating plates is actually very high. The barrel wall of the screw is thin and the material close to the barrel wall is It's actually overheated. But the temperature inside the material is not enough. Therefore, the setting temperature is not high, but the cloth is relatively brittle.
4. The sadness of the small machine, the material is too good, the liquidity is too good. When the hot air is large, the melt is not drawn into silk, but blown off directly, forming small liquid beads, which hit the cloth.
5. The small machine uses the material with a lower melting finger, because when the small machine uses the material with a higher melting finger, because the material flow rate is too fast, the thermal compensation, wind compensation, and air pressure compensation of the small machine are too late to keep up.
5. The artillery machine process is unstable, the machine is unstable, and the accessories can also be used on the spot.
Second, how to adjust the temperature of the melt blower
1. If the compound stays at high temperature and high pressure for a long time, it is easy to sinter and carbonize.
2. The temperature must first be determined when adjusting the machine, not the displayed temperature on the machine, but the actual temperature of the barrel and mold. In many small devices, the sensor has not been calibrated, and the displayed temperature will differ greatly from the actual temperature.
3. The temperature of the melt finger 1500 is set to be above 270℃, which is a little high.
3. What to do if the meltblown fabric becomes brittle and hard
1. Uneven spinning and insufficient air flow from the cooler, resulting in uneven heat dissipation and internal stress, resulting in brittleness. It can be improved by adjusting the melt volume of the extruder, adjusting the temperature of the hot air fan, and increasing the air volume of the cold air fan.
2. From the perspective of raw materials, it may be that a low-melting grease spinneret is used, which is relatively thick. After 24 to 48 hours of complete crystallization, it will cause the meltblown fabric to become brittle and hard. The melt-blown 1500 meltblown material is thin, soft, and evenly distributed, and the meltblown fabric is soft.
3. It has a relationship with the raw materials and the processing temperature is too high. After the fiber is produced, there is a secondary crystallization rearrangement process inside the PP, which is actually seriously heated inside the screw, which has caused severe thermal degradation. If the initiator of the melt-blown peroxide process is not well controlled, such problems are prone to occur.
The most important thing in the peroxide process is how to complete the molecular chain break before the screw is extruded in time to prevent secondary residues from entering the non-woven screw to continue the reaction. This is a test of the screw equipment combination and formulation control.
4. The temperature of the melt-blown cloth just produced, especially for the cloth-spraying machine with large drums, may not have a fan, and the temperature of the melt-blown cloth is high after winding. Plastics have greater flexibility and toughness in high temperature environments and become brittle after cooling.
5. Add proper amount (2%) of toughening agent
4. What to do if the filtering effect of meltblown cloth is poor
1. Increase the hot air flow or temperature (increasing the fineness of the fiber, reducing the porosity, improving the capture ability, but the resistance increases);
2. Increase the electrostatic voltage (current) (polarized fiber, increase the electrostatic field energy of the fiber and improve its adsorption capacity);
3. Add powder or other electrets to the raw materials (improve the fiber's power receiving capacity and storage time, and allow the fiber to carry more charge and charge time);
4. Increase the suction of the bottom of the net (increasing the density of the fiber and improving the ability to catch the fiber. The large grammage is obvious and not commonly used);
5. Properly reduce the output (under the same process, the amount of extrusion becomes smaller, the fiber becomes thinner, and the resistance increases);
6. Raise the working temperature of the die head (die tip) and other areas (melt fluidity becomes better, fibers become thinner);
7. Increase the spinning ambient temperature (fiber becomes thinner, generally when the room temperature rises, the resistance increases more obviously, and other physical indicators decrease);
8. Properly increase the amount of powder added.
5. How to improve the strength of meltblown cloth
1. Increase the flow of hot air (fine fibers, many winding nodes, uniform fiber stress, increased strength, but it will decrease after a certain degree);
2. Raise the temperature of the hot air (same as above);
3. Increase the weight of the product appropriately (within the range of internal control);
4. Raise the temperature of the die head (die tip) and other areas (same as 1);
5. Properly reduce the output;
6. Properly reduce the receiving distance of the meltblown cloth (not too small, but the brittle strength of the cloth will decrease, combined with other other parameters);
7. Increase the suction at the bottom of the net (large grammage is more obvious);
8. Use the raw material with lower melting index.
6. How to increase the elongation of meltblown cloth
1. Appropriately reduce the hot air flow or temperature (the slippage path of the node becomes larger and the feel becomes harder);
2. Reduce the working temperature of the die head (die tip) (same as above);
3. Properly reduce the output;
4. Increase the receiving distance of meltblown cloth (the effect is more obvious when used with 1 or 2);
5. Reduce the ambient temperature (spinning ambient temperature);
6. Increase the suction of the bottom of the net (the effect is not obvious, the large grammage is better);
7. Change the fiber angle by 6 degrees (change the structure of the fiber mesh, not commonly used)
8. Properly increase the output (this method will cause the reduction of other physical indicators, not commonly used).
7. How to reduce resistance
1. Reduce the hot air flow or temperature (fiber becomes thicker, the porosity is large, the resistance is small, and the efficiency becomes poor);
2. Increase the melt-blown cloth receiving distance (increasing the bulkiness of the fiber, the porosity is large, and the efficiency becomes poor);
3. Reduce the spinning ambient temperature (fiber cooling is sufficient, the structure is fluffy, the porosity is increased, and the hot air can achieve the purpose of reducing resistance and improving efficiency);
4. Reduce the suction at the bottom of the mesh (the fiber changes from dense to fluffy, the porosity becomes larger, and the large grammage is more obvious);
5. Reduce the working temperature of the heating area such as the die head (die tip) (the fiber becomes thicker and the porosity becomes larger);
6. Increase the metering pump (the extrusion volume becomes larger, the fiber becomes thicker, the porosity increases, and it is generally used when the order is transferred quickly);
7. Properly reduce the weight (within the range of internal control).
8. How to reduce resistance and improve efficiency
1. While increasing the receiving distance of the meltblown cloth, appropriately increase the flow or temperature of the hot air and reduce the suction at the bottom of the net (increasing the fineness and bulkiness of the fiber);
2. Improve the fiber fineness and reduce the spinning ambient temperature (such as adding cold air device);
3. While increasing the bulkiness of the fiber, increase the electrostatic voltage (current) and increase the amount of powder added appropriately;
4. Improve the fineness of the fiber and reduce the weight (not commonly used).
Nine, how to improve both strength and elongation
1. Appropriately reduce the flow or temperature of hot air, reduce the receiving distance of the meltblown cloth, and appropriately increase the air suction at the bottom of the mesh (for the physical indicators that are not qualified due to too high ambient temperature and too high raw material melting index);
2. Properly increase the flow or temperature of the hot air, increase the receiving distance of the meltblown cloth, and appropriately reduce the air suction at the bottom of the net (used to fail the physical index caused by the low ambient temperature and the low melting index of the raw material);
3. Reduce output;
4. Increase the fiber fineness and reduce the spinning ambient temperature.
10. How to reduce the CV value of meltblown cloth
1. Correspondingly change the working temperature of each area of the die head (the gram weight is increased slightly, and vice versa);
2. When the local efficiency and resistance conflict with the CV value, a baffle can be added to the position (increasing the local spinning ambient temperature);
3. The CV value of the longitudinal grammage is mainly related to the stability of the speed of the web-forming system.
11. Reasons for the appearance of "Shot" lumpy polymer
1. Improper setting of working temperature (too high or too low, generally too high is easy to appear);
2. The raw material or masterbatch is too dirty (generally the whole cloth surface or large area appears);
3. After the die head is used, the die tip is dirty (sometimes it is a poor threading or a large area, which can be solved by scraping the die tip);
4. There are carbonized substances or dirty plugs around the die tip that cause poor wire output (usually caused by abnormal shutdown. Generally, a small amount occurs locally, which can be solved by scraping the die tip);
5. The air knife is partially dirty or has physical damage to the air knife (affects the uniformity of the normal spinning airflow, and appears locally with vertical thin grooves);
6. The output is too high or too low (generally occurs in a large area, reduce or increase the output to solve);
7. The raw material melting index is too high or too low (usually too high is easy to appear);
8. There is water in the raw materials.
12. Reasons for "Flying Flowers and Flying Catkins"
1. The flow of hot air is too large or the temperature is too high (too many broken fibers);
2. The working temperature in each area is too high (too many fiber breaks);
3. The receiving distance of the meltblown cloth is too small (the cloth is too dense, which affects the suction efficiency);
4. The spinning environment temperature is too high (same as 1);
5. When adding recycled materials, the recycling amount is too large, and the melting index of the recycled materials is uncertain;
6. The output is too low;
7. The wire is difficult to attach to the net curtain, and the receiving distance of the meltblown cloth is too small (the cloth is too dense, which affects the suction efficiency)
8. Improper setting of the suction parameters of the bottom of the net or the screen is too dirty (small suction, the fiber cannot be fully absorbed on the screen and detached from the screen);
9. There is a lack of fusion between the filaments, the spinneret holes are plugged, and the crystallization temperature is too high.
10. The raw material melting index is too high.
13. What should I do if the spinneret needs to run in?
1. The new machine must install the die-spinneret after a while. It is similar to the new car running in.
2. Many of the spinneret mold materials on the market are not standard materials, and some low-end mold steels are used instead. There will be some micro-cracks that are invisible to the eyes during the use process, the hole diameter is rough, and the accuracy is poor. Without polishing, directly on board. As a result, the spinneret is uneven, the toughness is poor, the thickness of the spinneret is different, and it is easy to produce crystals.
3. The material has large ash content and impurities
4. The spinneret hole is not smooth enough
5. Unstable material
6. No filter added
7. The barrel is not cleaned
14. The screw speed problem
1. The faster the screw speed, the greater the amount of extrusion per unit time. Under the same hot air drafting conditions, the fiber formation is thicker, the fiber content of the product with the same gram weight is reduced, and the strength of the fiber web is reduced.
15. Receiving distance and roller speed
1. The receiving distance is an important parameter that affects the performance of the fiber web. Generally, with the change of the receiving distance, the longitudinal and transverse strength of the melt-blown cloth, the bending stiffness, and the fiber diameter will also change. The larger the receiving distance, the longer the cooling time of the drawn fibers, the reduced the bonding points between the fibers, the more fluffy and soft the product, and the lower the breaking strength.
2. The rotation speed of the drum determines the orientation of the fibers in the finished cloth. The faster the rotation speed, the more the fibers are oriented in the direction of rotation of the receiving device, and the greater the difference between the vertical and horizontal directions of the finished cloth.
16. How to use Yanshan Petrochemical's hydrogen-regulated melt-blown material?
1. There is no molecular weight distribution data in the inspection report of Yanshan Petrochemical. Generally, the molecular weight distribution of polymerized PP is not as narrow as CR-PP.
2. Can the powder of Yanshan Petrochemical be used?
Answer: Before mass production of Yanshan products, it was useful in Yanshan's own melt-blown cloth production line, so normal use should not be a problem. However, the general device should adjust some parameters from the pellet to the powder, and it is necessary to test the level of the master.
3. Are Yanshan Petrochemical and Basel's metallocene melt-blown materials the same process?
Answer: Yanshan did not introduce the process of Basel. The products use different catalysts. Yanshan Petrochemical’s hydrogen-conditioning melt-blown material is fine powder. Yanshan Petrochemical’s hydrogen-conditioning melt-blown material should be different from Basel metallocene melt-blown granulated powder. .
17. How to choose melt-blown materials? Is powder or pellets good?
1. The pellets have a long storage time and the powders degrade quickly, especially when the weather is hot;
2. The powder and the degrading agent are mixed more evenly, the contact surface is large, and it has more advantages;
3. If the melting index of the base material is small, add more degrading agent; if the melting index is larger, add less.
4. Select polypropylene melt-blown material with concentrated molecular weight distribution
5. It is the key technology to find a way to eliminate the impact of unstable base materials.
18. How to handle the electret and how to buy the equipment?
1. The electret time, electret voltage and electret distance are the three important process parameters that affect the electret effect. As the electret time increases, the equivalent surface charge density of the deposit increases and the potential of the electret surface rises. High, which enhances the adsorption and polarization of the electret, but with the increase of the electret time, when the surface potential of the filter material is sufficiently high, the charge under the needle tip will be repelled to move to other places with lower charge density. When the electret ends, its charge surface density reaches saturation, so when the electret time increases again, the filtration efficiency of the filter material does not change significantly.
2. Electret equipment should be bought with positive electricity, not negative electricity. Because there is a positive charge on the cloth, it can absorb the negative charge in the air. When the meltblown cloth contacts the skin, negative charges are more likely to be consumed. If they are positively charged, they will be consumed more slowly.
3. Dust, bacteria and viruses in the air are attached to the particles, mainly negatively charged, and the meltblown cloth is positively charged, which is easy to adsorb these negatively charged particles.
4. The electret masterbatch has little ability to increase static electricity, mainly to store charge, which makes the decay slower
If you want to know more about it please do not hesitate to
contact me. WhatsApp:+86-15966835076.
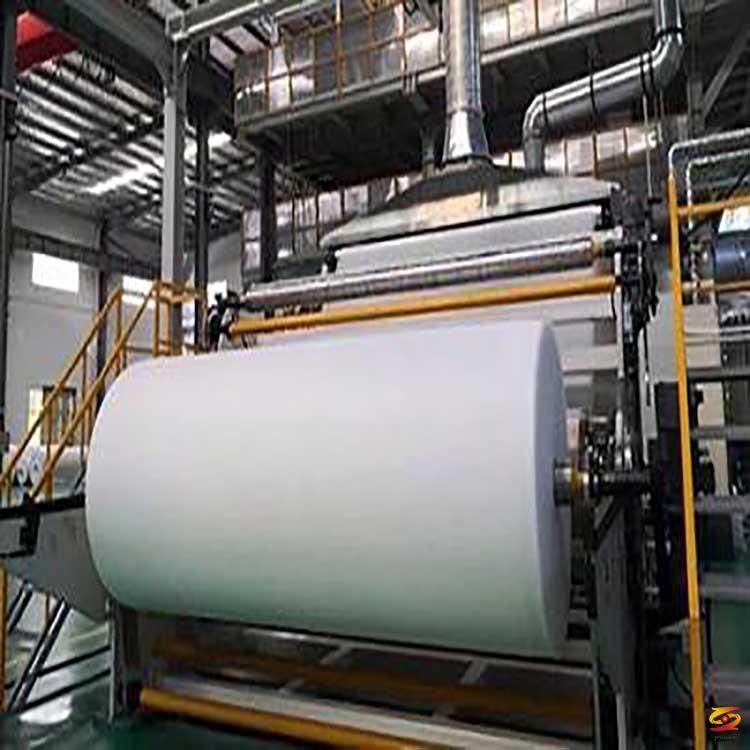
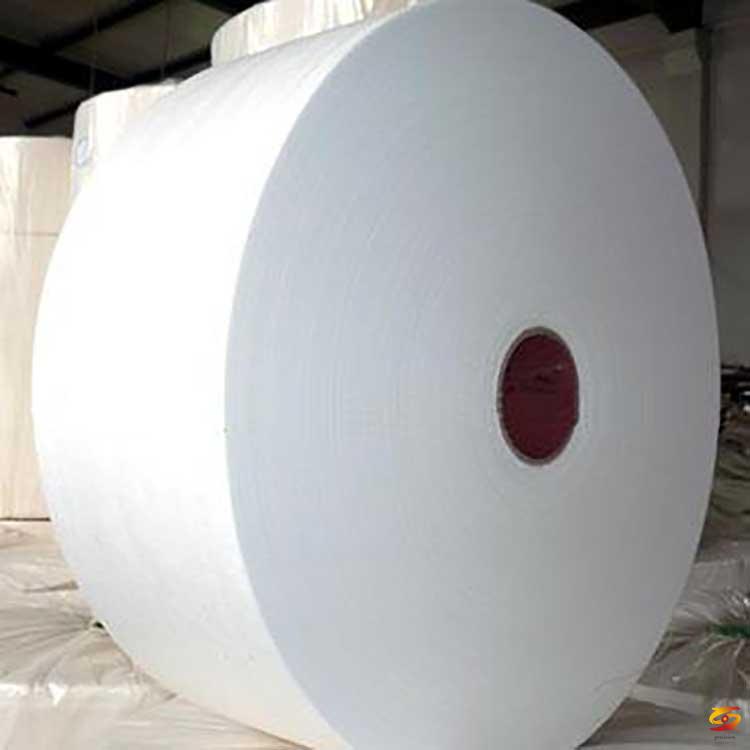
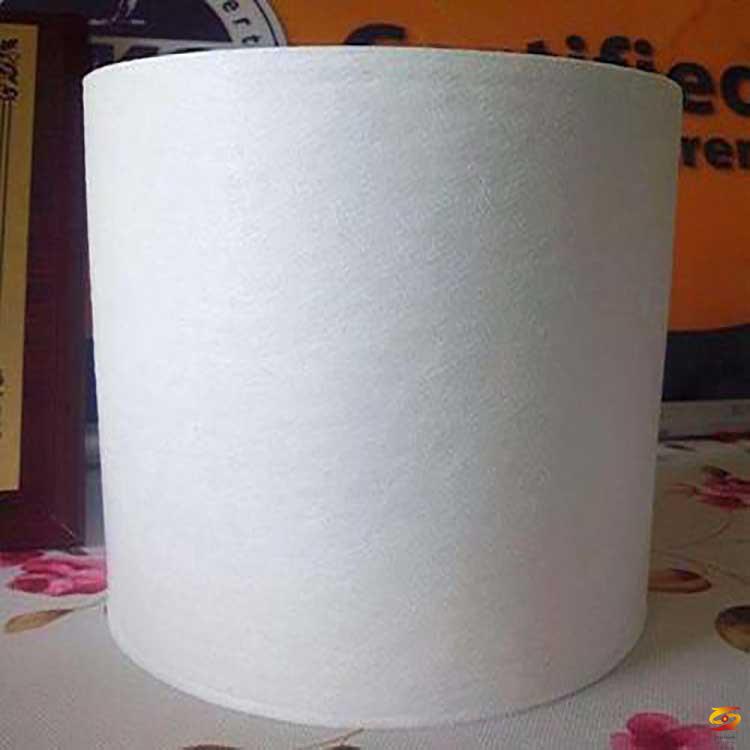
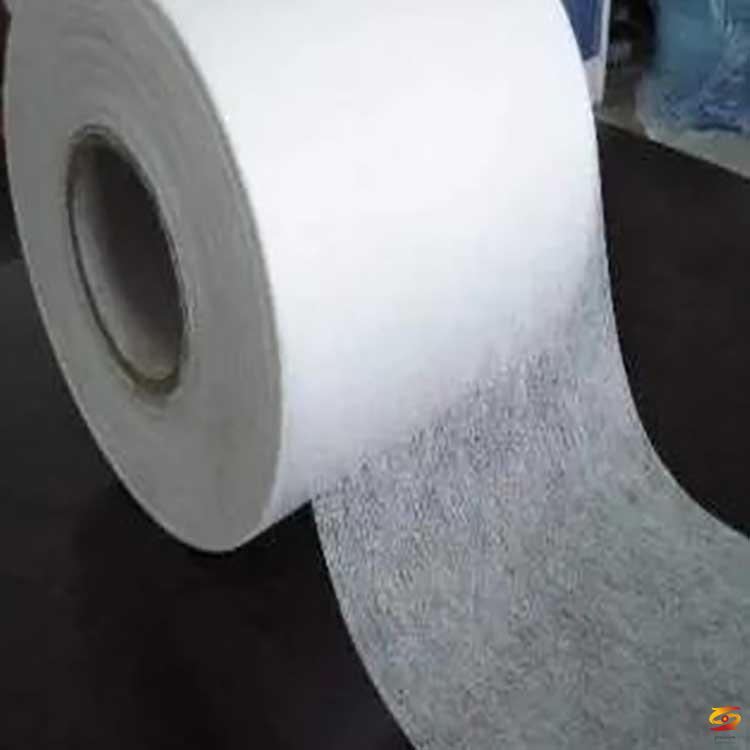