Introduction and feasibility report of SPC floor production line for stone plastic floor
Introduction and feasibility report of SPC floor production line for stone plastic floor1. Description of stone plastic floor, SPC (SCB), MCB floor:
Stone plastic floor (SPC floor) is a product made by extruding the PVC base material by an extruder, using a four-roll calendering unit to separately laminate the PVC color film + PVC wear-resistant layer + PVC base film at one time. The process is simple, the fit is completed by heat and does not contain glue. After the stone plastic floor is extruded by an extruder and the surface coating process is realized online, it is cut by a multi-saw (because the length is fixed, only a longitudinal multi-saw is needed), and then grooved in the vertical and horizontal directions, and the surface is painted with UV (Usually do two courses) Finally, pack and store. This section introduces the host and its functions.
SPC floor material uses environmentally friendly formula, does not contain heavy metals, phthalate, formaldehyde and other harmful substances, and meets EN 14372, EN 649-2011, IEC 62321, GB 4085-83 standards.
Product size range of stone plastic floor
length
950, 1220, 1850mm
width
125-200mm
thickness
4-8mm
Finished product tolerance
length
±0.25 mm
width
±0.025 mm
Straightness (banana shape)
Longitudinal ---- ±0.08 mm/ 1000 mm
Straight angle
±0.03 mm/ 205 mm (board length/board width>5)
Seam height difference (using template)
±0.03 mm
Fit tolerance
±0.05 mm
SPC floor density: 1.9~2.1 tons/m3;
SPC floor shrinkage rate: ≤1‰ (after tempering treatment);
:≤2.5‰ (without tempering treatment);
★Shrinkage rate test standard: 80℃, 6 hours standard.
SPC floor advantages: SPC floor physical indicators are stable and reliable, and chemical indicators meet international and national standards!
Disadvantages of SPC floor: SPC floor has high density, heavy weight and high transportation cost!
Comparison of production of SPC floor and WPC floor: SPC floor processing and manufacturing process are simple!
2. The process flow of producing SPC floor:
Process 1: Mixing
According to the fifth point, the raw materials are poured in according to the proportioning → high-speed mixer hot mixing (hot mixing temperature: about 125 ℃, the function is to mix all kinds of materials uniformly, eliminating the water in the materials) → enter the cold mixing (to cool the materials, Prevent agglomeration and discoloration, cold mixing temperature: about 45℃.)→Cool and mix homogeneous materials;
Process 2: Extrusion
Join the twin-screw extruder for heating and extrusion → enter the sheet die head selected by the customer for extrusion molding, the formed sheet is passed through a four-roll or five-roll calender, and the base material is fixed in thickness → color film → paste resistance Grinding layer→embossing (synchronous embossing)→cooling→cutting;
Process 3: UV
UV twice
Process 4: Slitting + Slotting + Pasting Silent Pad + Packaging
Slitting → slotting → sticking mute pad → inspection → packaging.
3. Composition and ratio of SPC floor:
4. SPC floor cost accounting (formulation cost is calculated at 2,600 yuan/ton):
1. 4mm thickness SPC floor weight: thickness 4.0mm×density 2.0=8Kg/㎡,
The formula cost is 2.6 yuan/kg×8kg=20.8 yuan/㎡
2. PVC wear-resistant layer 2 yuan/㎡+color film 4 yuan/㎡=6 yuan/㎡ (wear-resistant layer thickness: 0.3)
3. Slotting: 2-3 yuan/square;
4. Patent fee: __yuan/㎡
5. Packaging: 1.5~2 yuan/㎡
6. UV: 1 + labor 1 yuan/㎡=2 yuan/㎡
7. Comprehensive labor: 2-3 yuan//㎡
Total: 36 yuan/㎡ (excluding export lock patent fees)
5. SPC floor effect:
Six, SPC floor production equipment introduction
Serial number
model
Main motor
Yield
(Tons/day)
With 4mm thick floor, 30 wire wear-resistant layer
Daily wages of workers (2 people in 2 shifts)
Daily electricity bill
Daily screw replacement cost
Cost per square
1
SJSZ92/188 cone double stone plastic floor production line
110kw
12-14 tons
1500-1875 flats/day, with an average of 1700 flats/day,
800 yuan
Calculate the total power based on 110kw main engine
230kw*0.8*0.7*24=3091 yuan
Replace every 3 months, 75,000/75 days = 1,000 yuan
2.88 yuan / flat
2
SJSZ110/220 Cone Double Stone Plastic Floor Production Line
185kw
28-30 tons
3500-3750 flats/day, with an average of 3625 flats/day,
800 yuan
Calculate the total power based on 185kw main engine
330kw*0.8*0.7*24=4435 yuan
Replace every 2 months
150,000/50 days=3000
2.27 yuan / flat
3
SJSP115 flat double stone plastic floor production line
75kw
20-25 tons
2500-3125 flat/day, with an average of 2800 flat/day,
800 yuan
Calculate the total power based on 75kw main engine
200kw*0.8*0.65*240=2496 yuan
Replace every 6 months
110 thousand / 150 = 734 yuan
1.43 yuan / flat
Note: 1. The cost calculation is based on the cost of labor, electricity and screw replacement for a single production line to average to the final cost per square meter of floor;
2. If considering the labor, electricity and screw usage per square floor, it is recommended to choose 115 flat pairs.
7. The total investment of a set of SPC floor production equipment and related auxiliary equipment and facilities:
Whole line process:
A. Substrate extruder: automatic feeder-mixer-automatic feeder-SJSZ92/188 (SJSP115 or SJSZ110/220) extruder-mold-synchronous four-roll calender or five-roller-cooling Carriage-to-roller tractor-cross-cutting machine-stacking table-crusher-mill (production line 800,000-1.8 million, blender 25-500,000, crusher 50,000, mill 80,000, total 1.2-2.4 million)
B. Paint line UV: increase abrasion resistance (usually do two) (360,000)
C. Longitudinal multi-blade saw: slitting (100,000)
D. Slotting equipment: longitudinal conveyor belt conveyor ˃ longitudinal milling ˃ longitudinal dust cleaning machine ˃ transition belt conveyor ˃ horizontal double-end milling (1.8-4 million, including dust collector and cutter)
F. Packaging equipment: sticking mute pad equipment + manual carton cover ˃ film sealing and cutting machine ˃ roller table ˃ heat shrinking machine ˃ cooling roller table (350,000) ˃ stacking with flaps (400,000)
Total price: RMB 4-6 million including tax and freight
8. Equipment power and site requirements
(1) The total power of the substrate extruder: about 300kw-500kw, the total power of the back-end supporting equipment: about 400kw.
(2) Site requirements: The substrate extrusion line has a length of 60 meters and a width of 10 meters, and the rear equipment site is 40 meters long and 15 meters wide.
(3) Operators: 12-13 people (3 people for substrate extrusion line, 4 people for slitting, 1-2 people for slotting, 2 people for packaging boxes, 2 people for stacking finished products)
9. Introduction of main equipment
1) SRL-Z800/2500 mixer, main motor 110kw, frequency conversion speed regulation;
SRL-Z1000/3000 mixer, main motor 160kw, frequency conversion speed regulation;
SRL-Z1500/4500 mixer, main motor 225kw, frequency conversion speed regulation;
2) SJSZ92/188 substrate extrusion production line, main motor 110kw, frequency conversion speed regulation, whole machine installed power 230kw;
SJSZ110/200 substrate extrusion line, main motor 200kw, frequency conversion speed regulation, whole machine installed power 350kw;
SJSP115 substrate extrusion production line, main motor 75kw, frequency conversion speed regulation, machine installed power 200kw
3) HJC-12, longitudinal multi-blade saw, feed motor power 2.2KW, speed 10-30 meters per minute, spindle motor 15KW;
Resize DSC_0403
3) DTLS6/06/10D+2G, longitudinal double-end milling, feed motor power 5.5KW, speed 40-80 meters per minute, spindle motor 8KW*6 at 1, 2, and 3 stations, 4 and 5 stations Spindle motor 5.5KW*4, scraper system installed at the sixth station;
Longitudinal double track
4) DT6/18/10D+2G, horizontal double-end milling, feeding motor power 3.7KW, speed 20-40 meters per minute, spindle motor 5.5KW*6 for the first, second and third stations, the fourth and fifth stations Spindle motor 3KW*4, scraper system installed at the sixth station;
Traverse double end tenoner DTS
5) GTP5-02, automatic film sealing and cutting machine, 6-8 packs per minute;
Automatic packing line 1
Speed and capacity of substrate extrusion, slitting, slotting and packaging:
The substrate extrusion output averages 800-1100 kg an hour; about 1.5-3m/min (950-1220mm wide slab).
The main speed and frequency of the slitting and slotting line: longitudinal milling 60-80m/min, about 60 standard boards per minute (standard boards are 6.2*150*1220, and the area of a single piece is 0.18 square meters).
Slitting section: cutting 8-10 large boards per minute, sawing the large boards into 8 small boards, a total of 64-80 small boards per minute;
Slotting section: the speed of longitudinal double-end milling is 80 meters, 60 target plates; the speed of lateral double-end milling is about 30m/min. The distance between the push hooks is 400mm, and 75 standard boards can be processed per minute at a speed of 30m/min.
Packing section: the frequency of boxing, filming, and filming is 6-8 times per minute. (10 pieces of standard board per box)
If you want to know more about it please do not hesitate to
contact me. WhatsApp:+86-15966835076.
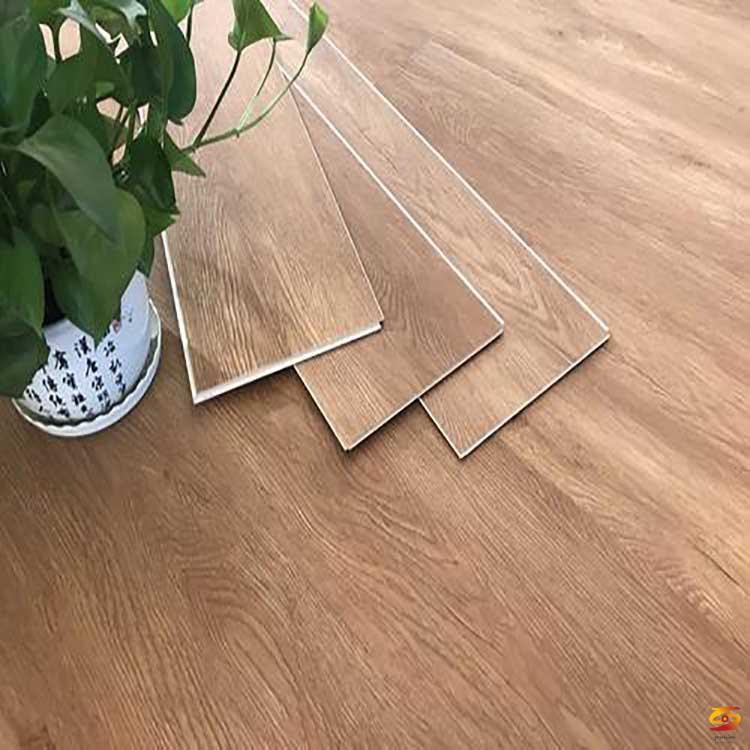
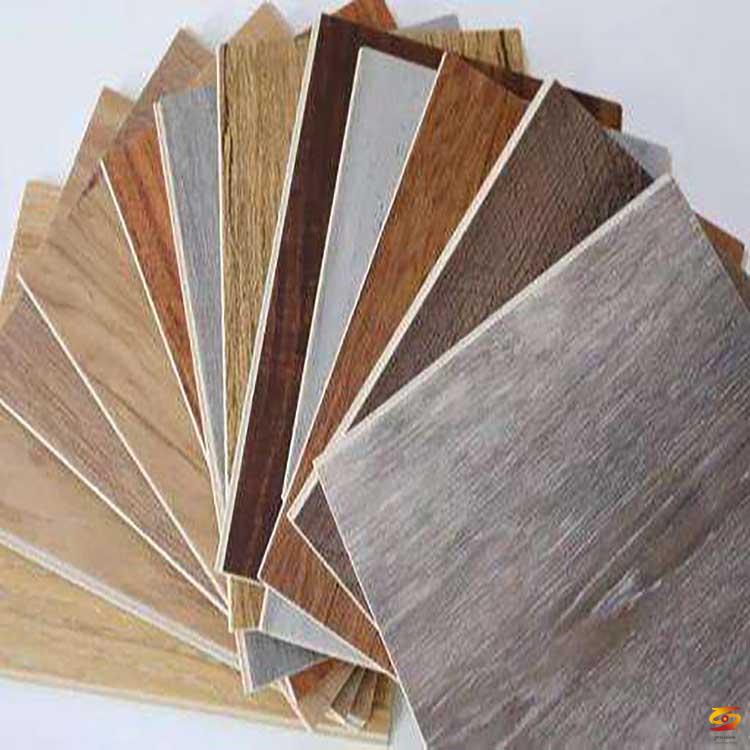
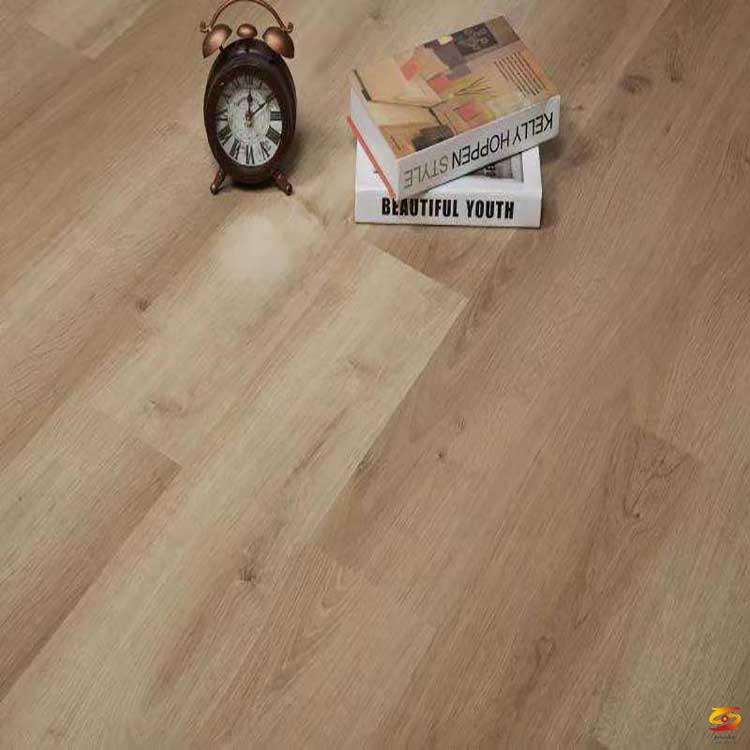
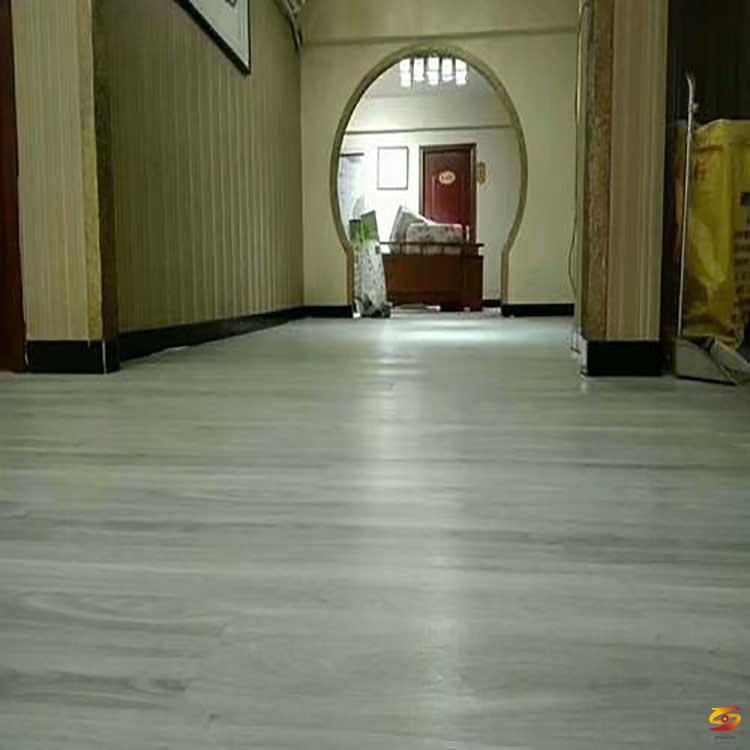
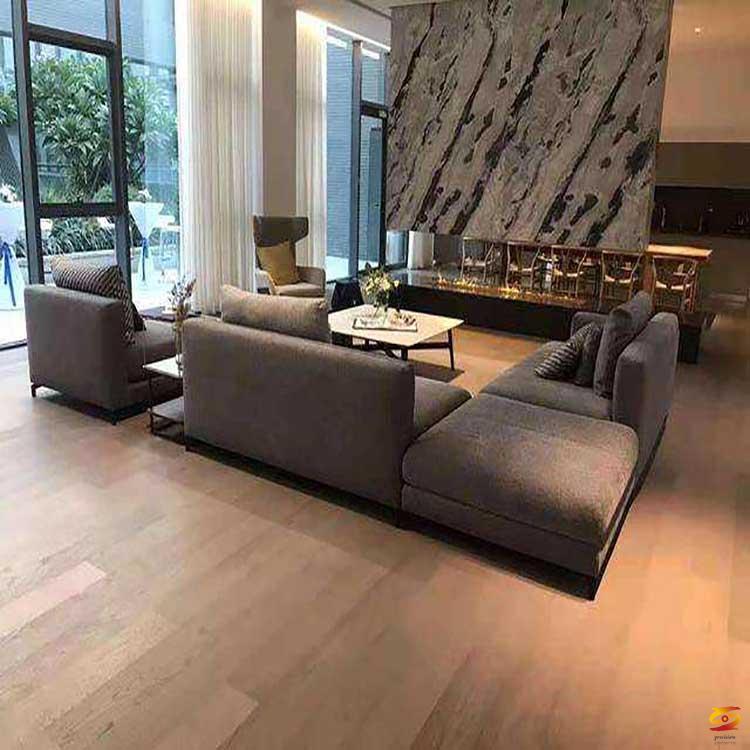