Understand the meltblown cloth production equipment, meltblown extruder detailed explanation
Understand the meltblown cloth production equipment, meltblown extruder detailed explanationMelt-blown cloth is the use of high-speed hot air flow to draw a thin stream of polymer melt extruded from the nozzle hole of the die, thereby forming ultra-fine fibers and collecting them on the condensed screen or roller, and at the same time bonding themselves to become Meltblown nonwoven fabric.
The width of the melt-blown cloth of regular manufacturers is generally 1600mm, 2400mm, 3200mm, and the diameter of the extruder is usually 90mm, 105mm, 135mm. However, after the epidemic began, the small machines (that is, the ones used in Yangzhong family workshops) with a small width were usually only a few tens of centimeters, and the screw diameters were mostly 45mm, 50mm, and 65mm.
This kind of machine has low output and low quality, but the cost is cheap, the delivery time is fast, and the price before the epidemic was 2-3 million. Now it has risen to 200,000, but it is still much cheaper than the extruders of regular manufacturers. At present, the melt-blown extruder from the mainstream mainstream manufacturers of 1600 in the market is priced at more than 6 million, and the delivery time is more than 2 months.
The production process of meltblown cloth is mainly as follows:
1. Melt preparation
2. Filter
3. Measurement
4. Melt is extruded from the spinneret
5. Melt trickle drafting and cooling
6. Netting
Overview and principle of meltblown cloth equipment
The melt-blown method is a method for preparing fibers by blowing polymer melts with high-temperature and high-speed airflow to rapidly draw them.
After the polymer chips are heated and pressed into a molten state by a screw extruder, they reach the spinneret hole at the front end of the nozzle through the melt distribution flow channel, and after being extruded, they are refined by two converging high-speed and high-temperature air flows to refine .
The refined fibers are cooled and solidified on the screen device to form a melt-blown nonwoven fabric.
Components of meltblown cloth equipment
Meltblown heads, automatic charging system equipment components, ultrasonic cleaning machines, air heaters, centrifugal fans, screw extruders, meltblown web forming machines, meltblown offline winding machines, meltblown offline slitting machines and other key equipment.
The core components of meltblown cloth equipment
Spinneret
The spinneret for the melt spinning method is a representative spinneret for the manufacture of synthetic fibers such as polyester and nylon. The thermoplastic resin is heated and melted, extruded through the spinneret in air or water at a certain speed, and cooled The spinning method of solidification into fibers.
The most core technology is the small nozzle on the spinneret. This nozzle is not only small in size, only 0.15mm, but also needs to process a complex hole pattern on such a small nozzle, which is extremely difficult to process. The process of nozzle processing requires Months. If the processing accuracy is not high, the melt-blown cloth finally produced will not meet the corresponding technical requirements, which will affect the protective performance of the mask.
Structure of melt-blown cloth spinneret
According to the shape of the spinneret, the structure of the spinneret is divided into three forms: round, fan and rectangle. At present, round and rectangular plates are mostly used at home and abroad. To suit different chemical fiber spinning occasions, round spinnerets are divided into flat type, flange flat type, flat ring, flange ring, etc.: rectangular spinneret is divided into flange rectangle and flange groove rectangle, etc. , Mostly used for short fiber spinning with more holes.
Meltblown cloth spinneret structure
Meltblown die head
The die head includes a die head body, a spinneret plate and a gas plate. The spinneret plate and the gas plate are detachably installed in the die head body. A spinneret hole is provided in the spinneret plate. There are several gaps between the spinneret plate and the gas plate There are several gas circulation channels in the main body of the die head. The gas circulation channels communicate with the slot. The outer wall of the main body of the die head is provided with a gas pipe connection end. The gas pipe connection end is connected to the gas collecting chamber through the gas pipe Through, the one end face of the spinneret hole of the spinneret is fixedly connected with a flow stabilizing element, the other end face of the spinneret hole is fixedly connected with a pipe connection device, and the spinneret hole is connected to the discharge port of the screw extruder through the pipe connection device Connected.
In the melt-blown equipment, the melt-blown die head is one of the core components to realize the wire drawing of the polymer. The design and accuracy directly affect the length, uniformity, toughness, fineness and other aspects of the wire drawing, thus affecting the quality of the final coil. Have a decisive impact.
Meltblown die head structure
Meltblown air heater
That is, the pipeline heater is composed of a body and a control system. The heating element is made of stainless steel pipe as a protective sleeve, high-temperature resistance alloy wire, crystalline magnesium oxide powder, formed by a compression process, and the control part uses advanced digital circuits and integrated circuit triggers. , High back pressure thyristor, etc. composed of adjustable temperature measurement and constant temperature system to ensure the normal operation of the electric heater.
Meltblown air heater
Polypropylene materials are refined from petroleum. At present, enterprises such as Sinopec Corp. can mass-produce them, but the equipment for producing polypropylene as melt-blown cloth, especially the core parts spinneret, mainly depends on imports. These suppliers mainly include Japanese Carson spinneret, German Enka, Japanese spinneret and other companies. Japanese suppliers occupy the most important position. The current output of several companies is far from meeting market demand.
Therefore, the production capacity of the mask ultimately depends on the output of the melt-blown cloth production equipment, and the core nozzle of the melt-blown cloth production equipment is very difficult to produce. The processing time takes several months, and the output cannot be greatly improved in a short time. And the production capacity is very limited, which makes the mask production can only make the most of the current equipment, and increase the production by extending the working time of the production line.
Main device configuration
1. Screw extruder; 2. Metering pump; 3. Melt blowing device; 4. Receiving net; 5. Winding device; 6. Feeding device.
The equipment of the continuous production line of melt-blown nonwoven fabric is about 6m high, about 5m wide, and about 20m long.The production equipment is as follows:
(1) Screw extruder: The screw diameter is generally 100~120mm, and the length/diameter ratio is 30. Its purpose is to melt the slice.
(2) Metering pump: Its function is to accurately measure and control the output and the fineness of the fiber. It is a gear pump that continuously delivers the melt to the spinneret.
(3) Melt filter: Its function is to filter out impurities in the melt, so as not to block the spinneret holes.
(4) Conveying net curtain: Spread the melt-blown fiber evenly on the net and convey it forward. There is a suction fan below it to discharge the hot air from above.
(5) Spinning box: It is the key equipment of the melt-blowing process. It has a long strip-shaped spinneret plate, which is covered with a long row of spinneret holes. Generally, there are about 1500 nozzle holes per m length. Hot air nozzles are installed on both sides of the spinneret, and hot air nozzles are installed below it, forming a 50b angle with the nozzle holes.After the fibers are ejected, the air is stretched with high-speed hot air immediately to blow the fibers and become superfine fiber.
(6) Feeding system: It consists of 3 measuring hoppers, which are used to measure white slices, masterbatch, and additives. The three components enter the following mixer and mix evenly, that is, put into production.
(7) Hot air blower and heater: provide the temperature and pressure of the hot air used in the spinning air flow stretching, heated by electricity, and consume more electricity.
(8) The take-up machine adopts full-automatic take-up, and melt-blown cloth is packaged in rolls. The fiber characteristics of the melt-blown non-woven fabric are ultra-fine, and the fiber diameter can reach a minimum of 0.5Lm, generally between 1 and 5Lm. The finer the fiber, the better the quality of the meltblown cloth, but the output is relatively reduced. Due to the ultra-fine fiber, its large specific surface area and strong adsorption capacity are the most prominent advantages of melt-blown cloth.
If you want to know more about it please do not hesitate to
contact me. WhatsApp:+86-15966835076.
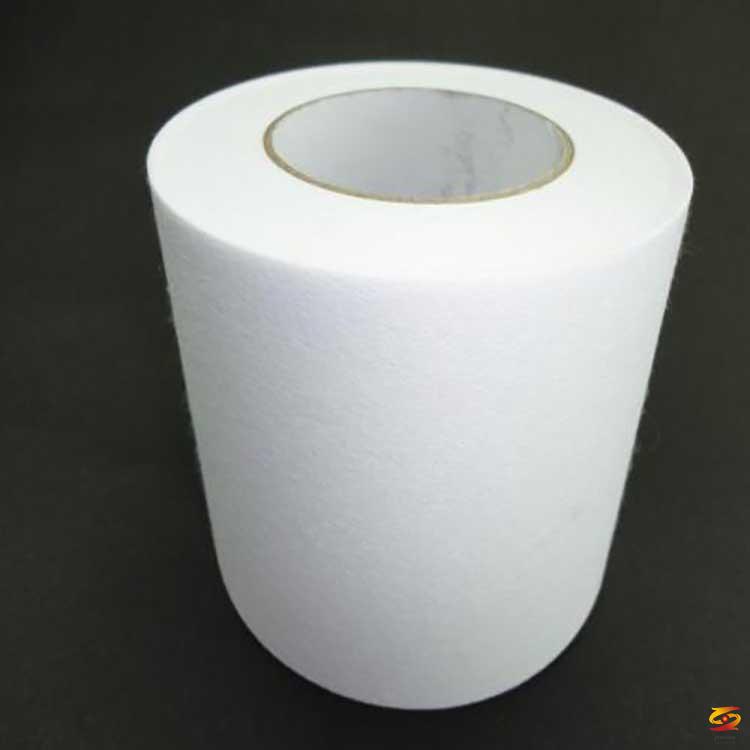
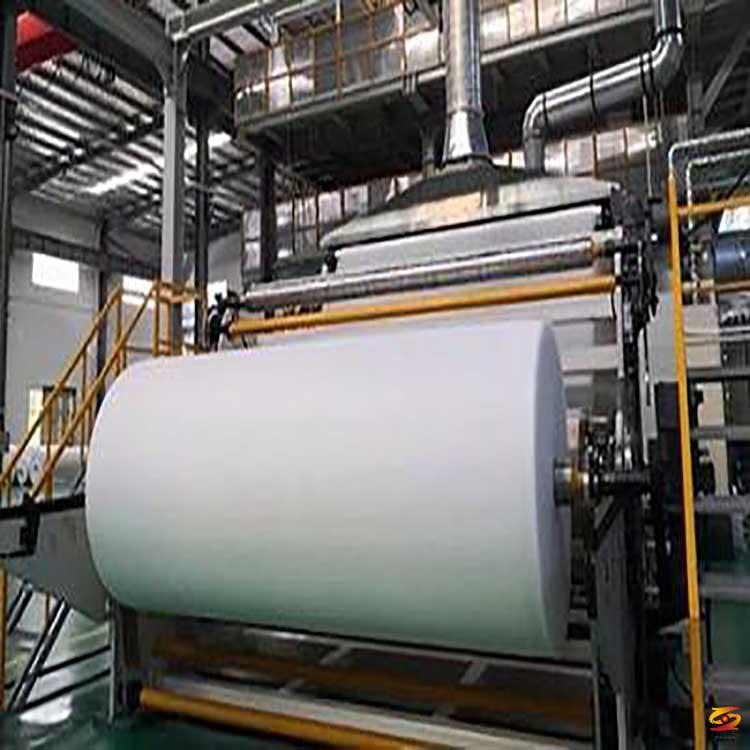
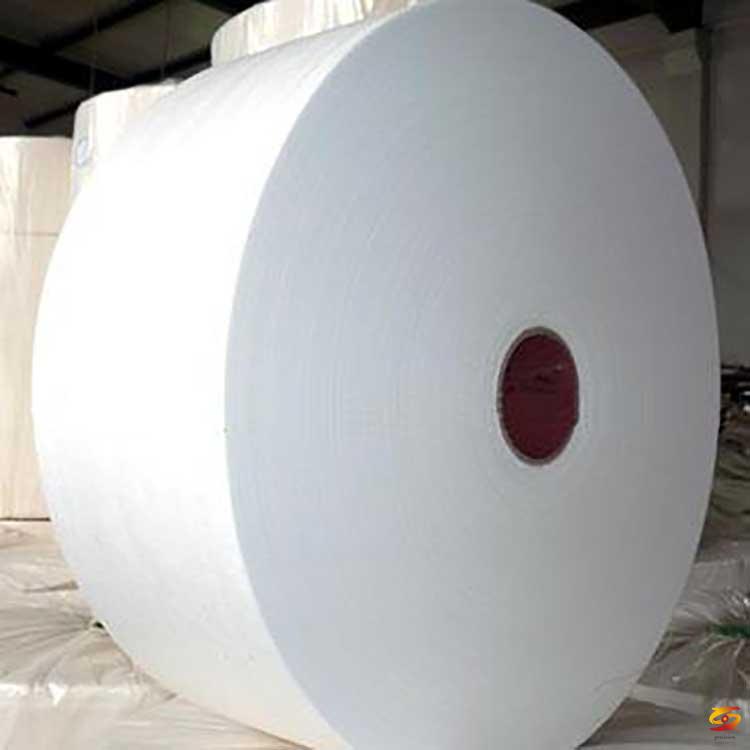
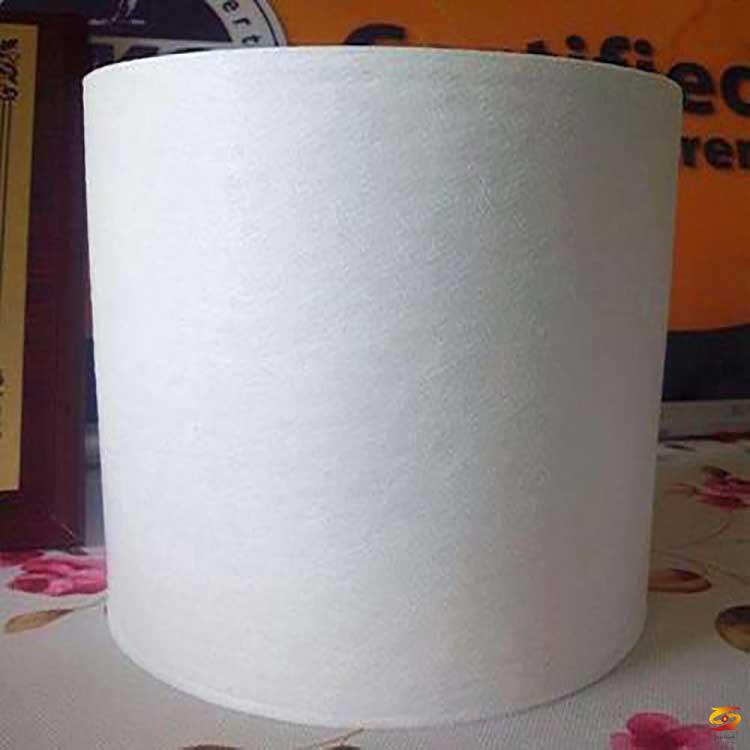