The basic knowledge of PVC foam board we should understand
The basic knowledge of PVC foam board we should understand1. What is rigid PVC foam plastic?
This time should be said that the history is not long. It was developed in the 1970s and the true industrialization was also in the 1990s. As soon as this material came out, people called it "future wood", and its chemical composition was polyvinyl chloride. Because rigid PVC low foam products are widely used, it can replace almost all products made of wood. Has the ability to compete with wood.
The technology of rigid foam has also developed rapidly in recent years. The United States is very prominent in the development of rigid PVC foam technology, with large investment and high output. Many new products have been developed to make rigid PVC foam products in construction. In the field of decorative materials, furniture materials have been industrialized.
The processing technology of rigid PVC foam products has made rapid progress. Whether it is equipment, molds or formula technology, there are foaming requirements.
Wood powder or other fillers are added to the PVC foam products. By adding different fillers, the rigid PVC foam products are given different characteristics. Improve the application range of this product in replacing various building materials and decorative materials. At the same time, the surface decoration of rigid PVC foam products is good.
Compared with wood materials, rigid PVC low-foam material has the characteristics of moisture proof, anti-corrosion, insect-proof, flame-retardant, paint-free, non-toxic and odorless, etc. It also protects against termites. This kind of product can not only save wood, but also effectively improve people's living environment. It is the best indoor and outdoor building material. PVC low-foam materials can replace wood on site, and can also replace other building materials. First of all, it reduces the amount of raw materials, which in turn reduces the cost of the product; reduces the thermal conductivity, improves the thermal insulation, thermal insulation; reduces the thermal expansion.
The products currently formed by PVC foaming mainly include rigid PVC free foaming and crust foaming solid panels, hollow panels, rigid PVC foam decorative profiles, pipes, rigid PVC foamed plastic wood products, etc. In the fields of construction, packaging, furniture industry, etc., applications are becoming more and more widespread.
Second, the seven basic requirements for foam molding extrusion?
Extruders for the production of PVC low-foam extruded products can use either single-screw extruders or twin-screw extruders, which need to be determined according to the specific products and the conditions of the enterprise itself. In practice, the basic requirements for extruders for the production of PVC low foam products are summarized for reference.
The basic requirements for the extruder for extrusion foam molding are as follows:
(1) The power of the transmission system of the extruder should be sufficient to match the corresponding extrusion volume;
(2) The length-diameter ratio of the screw of the extruder should be large enough to establish a high and stable extrusion pressure;
(3) The extruder must be able to generate sufficient melt pressure to prevent premature foaming;
(4) The extruder screw mixing and plasticizing performance requirements are high to ensure that the resin and various additives are mixed evenly and the plasticization is good;
(5) The extrusion system should be wear-resistant and corrosion-resistant;
(6) The accuracy of the temperature control system of the extruder is higher than that of the ordinary extruder;
(7) The transmission of the extruder should be stable, and the speed fluctuation should be smaller than that of the ordinary extruder.
3. The difference between PVC free foam and controllable foam
PVC direct foaming method (also called directional foaming), this kind of extrusion foaming is inseparable from free foaming process and controllable foaming process (also called crust foaming method, inward foaming method)
For free-foaming, after the melt containing the blowing agent leaves the die, it begins to expand freely within a certain distance from the die, and the foaming product with the desired shape and foaming density required by the shaping device is obtained. The density of the foam product in cross section is about the same, and the periphery is surrounded by a dense but thin outer skin. Tubes, plates, and profiles can be formed by the free foam method under suitable process conditions. At present, the more consistent view is that the application of the free foam method is often limited to products with smaller cross-sections, and the cross-sectional area is generally <3000mm2, mainly thin-walled parts.
For the controllable foaming method, the shaping device is directly connected to the die opening, and its outer contour is the same as the die opening. The result of this styling form is that the melt containing the blowing agent, as soon as it leaves the die, causes the entire surface of the extrudate to be rapidly cooled, which prevents the formation of cells on the surface of the extrudate and the cross section of the extrudate Swell on any external dimensions on the At the same time, the cavity produced by the core in the die is filled with cells formed by the melt during the shaping process. The density of the foam product varies greatly in cross section, the density of the core is low, and the density of the outer surface layer is high. This method can also produce pipes, plates and profiles, and the strength structure is better than free foam, so it is often used to manufacture PVC low-foam structural materials that meet different requirements, and controllable foaming allows cross-sectional area of PVC products. >3000mm2, some more than 30,000mm2.
4. The mixing technology and feeding sequence of PVC low foam raw materials
The preparation of PVC low-foam dry mix is carried out on a standard heating and cooling mixing unit (this unit is a combination of high-speed mixer and cooling mixing unit). The mixing principle of the high-speed mixer is that the materials are rapidly dispersed along the wall of the container under the impulse of the high-speed rotating stirring blade, and fall from the center of the container to form a vortex-like movement to achieve a rapid mixing and uniform effect. During high-speed stirring, when the materials are mixed, there will be friction between the materials, that is, friction heat will be generated at the same time, there will be friction between the materials and the stirring blade and the container wall, and friction heat will also be generated, as well as the heat source outside the container. Under the combined action, various additives are quickly penetrated into the PVC resin and form a semi-gelled dry mix. The principle of the cooling mixer is to pass cooling water through the outer jacket of the container, and under the low-speed stirring of the blades, the dry mixture of about 110-120 ℃ is quickly cooled to below 45 ℃ to prevent the hot material from agglomeration, decomposition and foaming. The mixed dry mixture discharged from the mixer should be sieved to remove agglomerates and molten particles for the next step of extrusion granulation, or direct extrusion of low foam products.
In the low-foaming formula PVC compound, there are many components, and various additives such as stabilizers, modifiers, lubricants, foaming agents, foaming regulators, pigments, fillers, etc. should be added in order. This is very important. The wrong feeding sequence will seriously affect the normal production and product quality.
The normal feeding sequence is as follows:
(1) At low speed, add PVC resin to the high-speed mixing chamber;
(2) Add stabilizer and metal soap to PVC resin at 60 ℃ high speed;
(3) Add processing modifiers, internal lubricants, pigments, impact modifiers, and foaming agents to the feedstock at a high speed of 75°C;
(4) Add foaming regulator and external lubricant under high speed stirring at about 90℃;
(5) Add filler at high speed around 100℃;
(6) At about 110℃~120℃, remove the material at low speed and send it to the starting cooling mixer;
(7) In the cold mixer, the mixture is cooled to below 45℃ and discharged;
(8) Screened packaging (or sent to storage tank).
The PVC dry mix should be placed for more than 48 hours after being mixed, and then sent to the granulation process or directly sent to the extrusion molding process.
5. Six common sense of PVC foam board processing
The processing characteristics of PVC foam board are almost the same as those of wood processing. It is only necessary to avoid the scorching caused by high working temperature. In addition, the chips generated after processing can be collected, recycled and remanufactured to reduce costs. There is one thing to note when cutting hollow foam board. Because the hollow spacing is 23㎜, it is convenient to assemble. If you don’t pay attention, when cutting, most of the pieces are overlapped and cut at one time, resulting in different spacing; you can use the tool Positioning in the form of a bolt to facilitate processing, now we know a little bit about common knowledge about the surface processing of PVC foam board.
1. You can use the engraving machine to form according to the design drawing, and then select the surface to be pasted with Mena or baking paint; but the hollow foam board needs to be noted that if the surface is uneven, only the vacuum overmolding method can be used to select the 2㎜ PVC board.
2. Bending forming is only applicable to solid foam board, hollow foam board is not suitable; the processing method is to use the upper and lower molds, cover the wooden mold surface with aluminum plate and heat the solid foam board to the plasticizing temperature of 70~90℃ In the meantime, the shape of the foam board surface is directly extruded by the upper and lower dies without any change.
3. When self-adhesive PVC is extruded and manufactured, the surface can be provided with wood grains with different textures printed according to requirements, which can save unnecessary processing procedures.
4. The surface of the PVC foam board can be painted, and the general category can be divided into general baking paint, piano baking paint and ceramic baking paint according to the processing method; anti-UV components will be added during the piano baking paint processing to avoid changes in the surface color; In terms of surface hardness, ceramic baking paint is also used as an excellent anti-scratching advantage.
5. Secondly, it is a common processing method. On the surface, a crystal plate (usually a single-sided colored acrylic plate), Mine board and Mina paper are used. In the edge-sealing part, most of the general processing is automatic edge banding machine for Mainly, the automatic edge banding machine is divided into two types: roller type and crawler type. However, when using hollow foam, it is recommended to use a color similar to the surface-mounting material to avoid obvious color difference when the paper is shrunk. .
6. Drilling can benefit the crawler edge banding machine, which is less likely to cause unevenness after surface edge banding, and pressure adjustment is also very important; the color of the foam board is also directly processed by NC machine. The material itself can reduce the density and increase the air content of the foam board itself according to the needs of the application, so as to achieve the effect of heat insulation and sound insulation and increase the cost reduction. Same weight. At present, some manufacturers have applied foam molding to tabletop molding or large machine cover using vacuum forming, but it has a disadvantage that it is not easy to wear due to poor surface mold resistance.
6. The mixing technology and feeding sequence of PVC low foaming raw materials
The preparation of PVC low-foam dry mix is carried out on a standard heating and cooling mixing unit (this unit is a combination of high-speed mixer and cooling mixing unit). The mixing principle of the high-speed mixer is that the materials are rapidly dispersed along the wall of the container under the impulse of the high-speed rotating stirring blade, and fall from the center of the container to form a vortex-like movement to achieve a rapid mixing and uniform effect. During high-speed stirring, when the materials are mixed, there will be friction between the materials, that is, friction heat will be generated at the same time, there will be friction between the materials and the stirring blade and the container wall, and friction heat will also be generated, as well as the heat source outside the container. Under the combined action, various additives are quickly penetrated into the PVC resin and form a semi-gelled dry mix. The principle of the cooling mixer is to pass cooling water through the outer jacket of the container, and under the low-speed stirring of the blades, the dry mixture of about 110-120 ℃ is quickly cooled to below 45 ℃ to prevent the hot material from agglomeration, decomposition and foaming. The mixed dry mixture discharged from the mixer should be sieved to remove agglomerates and molten particles for the next step of extrusion granulation, or direct extrusion of low foam products.
In the low-foaming formula PVC compound, there are many components, and various additives such as stabilizers, modifiers, lubricants, foaming agents, foaming regulators, pigments, fillers, etc. should be added in order. This is very important. The wrong feeding sequence will seriously affect the normal production and product quality.
The normal feeding sequence is as follows:
(1) At low speed, add PVC resin to the high-speed mixing chamber;
(2) Add stabilizer and metal soap to PVC resin at 60 ℃ high speed;
(3) Add processing modifiers, internal lubricants, pigments, impact modifiers, and foaming agents to the feedstock at a high speed of 75°C;
(4) Add foaming regulator and external lubricant under high speed stirring at about 90℃;
(5) Add filler at high speed around 100℃;
(6) At about 110℃~120℃, remove the material at low speed and send it to the starting cooling mixer;
(7) In the cold mixer, the mixture is cooled to below 45℃ and discharged;
(8) Screened packaging (or sent to storage tank).
The PVC dry mix should be placed for more than 48 hours after being mixed, and then sent to the granulation process or directly sent to the extrusion molding process.
7. The principle and application of rigid PVC foamed plastic
Foamed plastic is a type of polymer material formed by a large number of gas micropores dispersed in solid plastic, and has the characteristics of light weight, heat insulation, sound absorption, corrosion resistance, shock absorption and so on.
Compared with non-foamed plastics, foamed plastics have low density, light weight and high specific strength, and have excellent cushioning and shock absorption, sound insulation and sound absorption properties, low thermal conductivity, good thermal insulation performance, and excellent electrical insulation. , Corrosion resistance, mold resistance. Flexible foamed plastic has excellent elasticity and other properties.
Foam plastic classification
There are currently three types: classified by hardness, which can be divided into three categories: soft foam plastic, hard foam plastic and semi-rigid foam speed.
At 23 degrees Celsius and 50% relative temperature, flexible foamed plastics have an elastic modulus of less than 70 MPa; classified by density, they can be divided into low foaming plastics, medium foaming plastics, and high foaming speeds. Low-foam plastics with a density above 0.4g cubic meters, medium-foam plastics with a density of 0.1/0.4G cubic meters; classified according to the cell structure, the cells are classified into closed-cell type and open-cell type. The pores in the closed-cell type are isolated from each other and have buoyancy; the pores in the open-cell type are connected to each other without buoyancy. According to the size of the pore size, ultra-micropores are 0.1-1.0 micrometers, bit pores are 1.0-10 micrometers, and generally cell pores are more than 50 micrometers.
Foaming process
No matter what method is used to make the foaming process, the basic process is foaming. The foaming process changes the plastic into a liquid state, or introduces gas into the molten plastic to generate micropores (bubble), which increases the micropores to A certain volume, the microporous structure is fixed by physical or chemical methods. If you can’t fix it, the foam will burst and the foam will not form.
How to mix gas into plastic polymer materials? There are currently three methods: mechanical method, physical method, chemical method. Machinery is vigorous stirring, and the previous soapy liquid and washing machine stirring will produce foam. The physical way is to normally see the foamed material, microporous filler, low boiling point liquid gasification, and generate bubbles by heating. Chemistry is the reaction of solid blowing agent to produce gas
If you want to know more about it please do not hesitate to
contact me. WhatsApp:+86-15966835076.
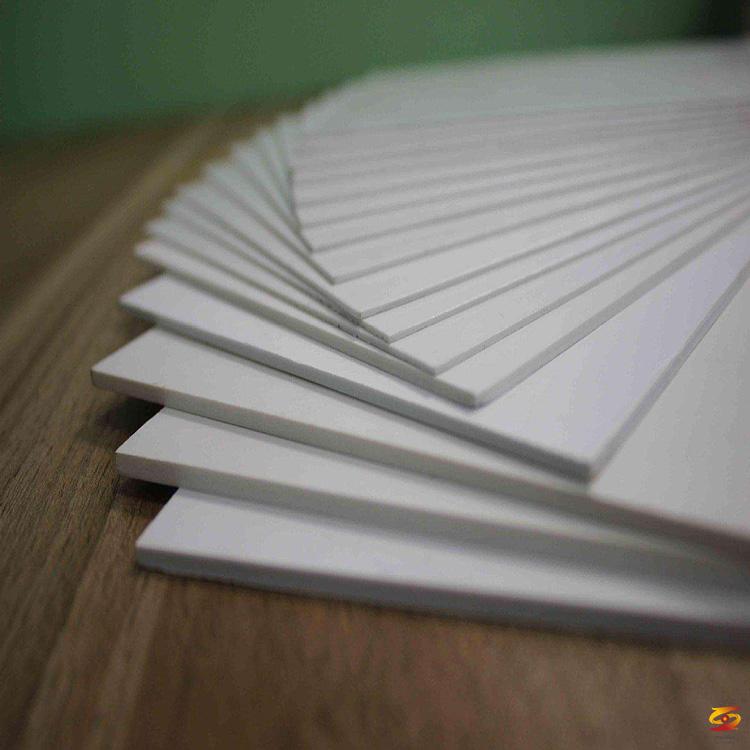
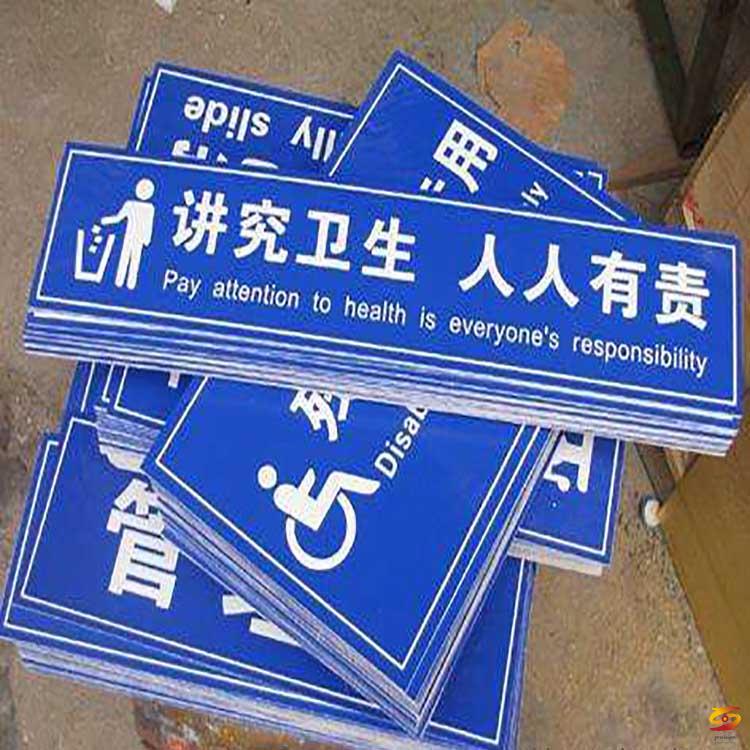
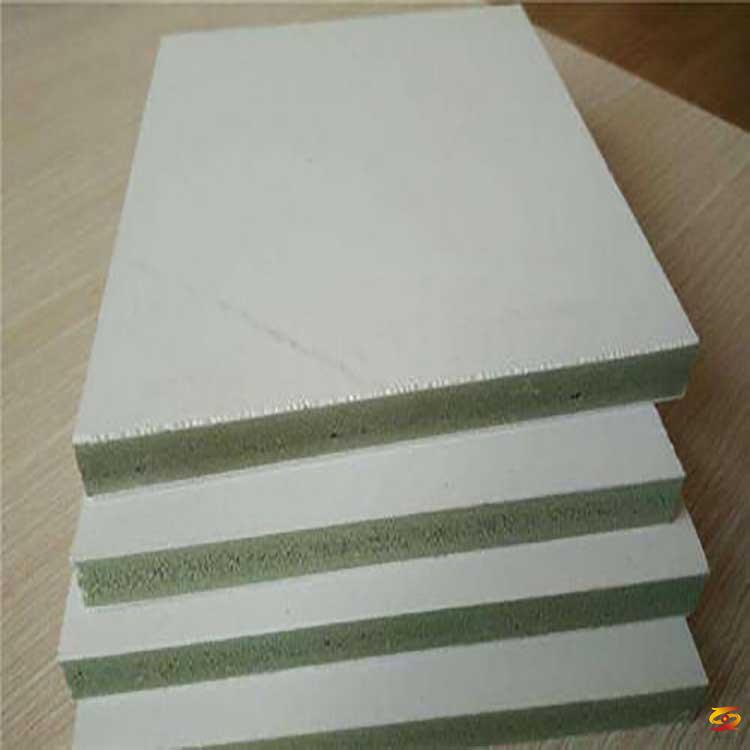
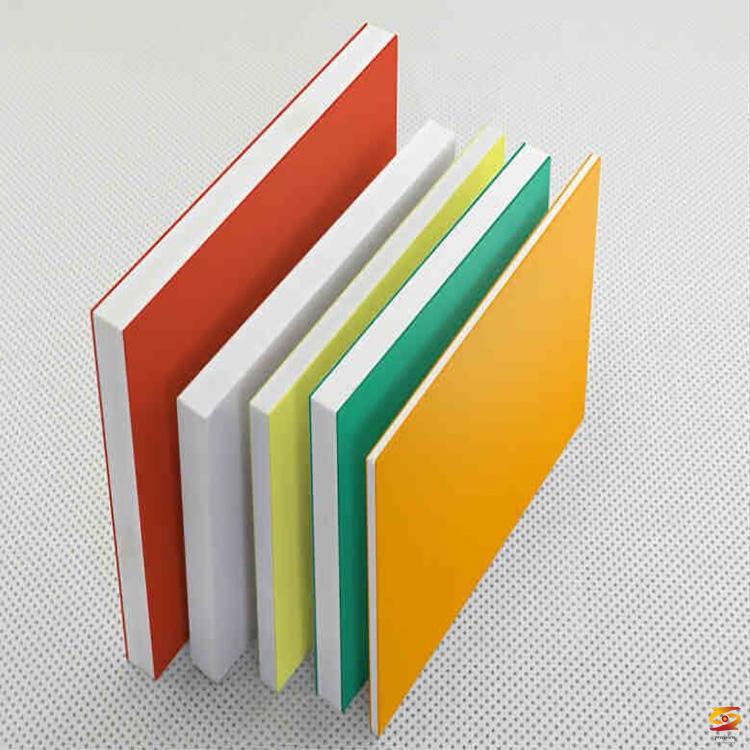