PVC profile design and processing technology 【Worthable collection】
PVC profile design and processing technology 【Worthable collection】Formula design principles and characteristics of various formulas
The formulation of PVC plastic profiles is mainly composed of PVC resin and additives, which are divided into heat stabilizers, lubricants, agents, processing modifiers, impact modifiers, fillers, aging resistance agents, colorants Wait. Before designing the PVC formula, we should first understand the performance of PVC resin and various additives.
Raw materials and additives
PVC resin
The resin for producing PVC plastic profiles is polyvinyl chloride resin (PVC). Polyvinyl chloride is a polymer made by polymerizing vinyl chloride monomers, and its output is second only to PE.
PVC resin can be divided into two types of loose type (XS) and compact type (Ⅺ) due to the different dispersants in the polymerization. Loose particle size is 0.1-0.2mm, irregular surface, porous, cotton ball shape, easy to absorb plasticizer, compact particle size below 0.1mm, regular surface, solid, table tennis shape, not easy to absorb Plasticizers are currently used more loosely.
PVC can be divided into ordinary grade (toxic PVC) and sanitary grade '(non-toxic PVC). Hygienic level requires vinyl chloride (VC) content lower than lOXl0-6, can be used in food and medicine. Synthetic process is different, PVC can be divided into suspension PVC and emulsion PVC. According to the national standard GB / T5761-93 "Suspension Method General Polyvinyl Chloride Resin Inspection Standard", the suspension method PVC is divided into PVC-SGl to PVC-SG8Jk resins, where the smaller the number, the greater the degree of polymerization and the more the molecular weight The greater the strength, the higher the strength, but the more difficult the melt flow and the more difficult the processing. When making specific choices, when making soft products, generally use PVC-SGl, PVC-SG2, PVC-SG3 type, need to add a large amount of plasticizer. For example, polyvinyl chloride film uses SG-2 resin, adding 50 ~ 80 parts of plasticizer. When processing hard products, generally no or little plasticizer is added, so PVC-SG4, VC-SG5, PVC-SG6, PVC-SG7, PVC-SG8 are used. For example, PVC hard pipes use SG-4 resin, plastic door and window profiles use SG-5 resin, rigid transparent sheets use SG-6 resin, and rigid foam profiles use SG-7 and SG-8 resin. The emulsion method PVC paste is mainly used for artificial leather, wallpaper and floor leather and plastic dipped products. Some PVC resins manufactured by PVC resin manufacturers are classified according to the degree of polymerization (the degree of polymerization is the number of unit links, and the degree of polymerization is multiplied by the molecular weight of the link equal to the molecular weight of the polymer). SK-700; SK-800; SK-1000; SK-1100; SK-1200 and so on. The corresponding degree of polymerization of its SG-5 resin is 1000-1100. For physical and chemical properties of PVC resin, see Chapter 4.
PVC powder is a white powder with a density between 1.35-1.45g / cm3 and an apparent density between 0.4-0.5g / cm3. Depending on the content of the plasticizer, it can be soft and hard products. Generally, the plasticizer content is 0-5 parts for hard products, 5-25 parts for semi-hard products, and more than 25 parts for soft products.
PVC is a non-crystalline, polar polymer with high softening temperature and melting temperature. Pure PVC generally needs to be plasticized at 160-210 ~ C. Due to the polar bonds between macromolecules, PVC Shows hard and brittle performance. Moreover, the chlorine-containing groups in PVC molecules, when the temperature reaches 120 ~ C, pure PVC will begin to de-HCl reaction, which will lead to thermal degradation of PVC. Therefore, various additives must be added during processing to modify and impact modify PVC, so that it can be processed into a useful product.
PVC resin is mainly used to produce all kinds of films (such as daily printing films, industrial packaging films, agricultural greenhouse films and heat shrinkable films, etc.), all kinds of boards and sheets (their sheets can be used for plastic products), and all kinds of pipes (Such as non-toxic water supply pipes, building threading pipes, transparent hoses, etc.), various types of profiles (such as doors, windows, decorative panels), hollow blow molding (for cosmetics and beverages), cables, various injection molded products and artificial leather , Floor leather, slush plastic toys, etc.
stabilizer
Pure PVC resin is extremely sensitive to heat. When the heating temperature reaches 90Y: above, a slight thermal decomposition reaction will occur. When the temperature rises to 120C, the decomposition reaction will increase. At 150C, 10 minutes, the PVC resin will change from the original white Gradually changed to yellow-red-brown-black. The decomposition process of PVC resin is due to a series of chain reactions caused by the de-HCL reaction, which finally leads to the breakage of the macromolecular chain. The thermal stability mechanism to prevent the thermal decomposition of PVC is achieved through the following aspects.
By capturing the HCl produced by the thermal decomposition of PVC, the catalytic degradation of HCl is prevented.
Lead salts mainly act according to this mechanism, in addition to metal soaps, organic tins, phosphites, and epoxy.
· Replace the active allyl chloride atom. Metal soaps, phosphites and organic tins can act according to this mechanism.
· Reacts with free radicals and terminates the reaction of free radicals. Organotin and phosphite act according to this mechanism.
· Additional effect with conjugated double bond, restrain the growth of conjugated chain.
Organotin and epoxy act according to this mechanism.
· Decompose peroxide and reduce the number of free radicals. Organotin and phosphite act according to this mechanism.
· Passivating metal ions with catalytic HCl removal.
The same stabilizer can achieve thermal stabilization according to several different mechanisms.
Commonly used stabilizer varieties:
1. Lead salts
Lead salts are the most commonly used heat stabilizers for PVC, and are also very effective heat stabilizers. Their dosage can account for more than 70% of PVC heat stabilizers.
Advantages of lead salt stabilizers: excellent thermal stability, long-term thermal stability, excellent electrical insulation performance, good weather resistance and low price.
Disadvantages of lead salt stabilizers: poor dispersion, high toxicity, initial coloring, difficult to obtain transparent products, and difficult to obtain products with bright colors, lack of lubricity, and easy to produce sulfur pollution.
Commonly used lead salt stabilizers are:
(1) Tribasic lead sulfate
The molecular formula is 3PbO. PbSO. H20, code-named TLS, referred to as tri-salt, white powder, density 6.4g / cm ’. Tribasic lead sulfate is the most commonly used type of stabilizer. It is generally used together with the dibasic lead phosphite. It needs to be equipped with a lubricant because it has no lubricity. Mainly used in PVC rigid opaque products, the dosage is generally 2 ~ 7 servings.
(2) Dibasic lead phosphite
The molecular formula is 2PbO. PbHPO3.H2O, code-named DL, abbreviated as di-salt, white powder, density 6.1g / cm3. The thermal stability of dibasic lead phosphite is slightly lower than that of tribasic lead sulfate, but the weather resistance is better than tribasic lead sulfate. Dibasic lead phosphite is often used in combination with tribasic lead sulfate, and the dosage is generally 1/2 of tribasic lead sulfate.
(3) Dibasic lead stearate
Code-named DLS, it is not as common as tribasic lead sulfate and dibasic lead phosphite and has lubricity. It is often used in combination with tribasic lead sulfate and dibasic lead phosphite in an amount of 0.5-1.5 parts.
2. Metal soaps
It is the second-largest main stabilizer whose dosage is second only to lead salts. Although its thermal stability is not as good as lead salts, it also has lubricity. The metal soaps can be metal (lead, barium, cadmium, zinc, calcium, etc.) salts of fatty acids (lauric acid, stearic acid, naphthenic acid, etc.). Among them, stearates are the most commonly used, and the order of their activeness is : Zn salt? Cd salt? Pb salt? Ca salt 7. Ba salt. Metal soaps are generally not used alone, often between metal soaps or in combination with lead salts and organic tin. Except for Gd and Pb, they are non-toxic, except Pb and Ca, which are transparent and free of sulfide pollution, so they are widely used in soft PVC, such as non-toxic and transparent products.
Commonly used metal salt stabilizers are:
(1) Zinc stearate (ZnSt) is non-toxic and transparent. After a large amount, it is easy to cause the "zinc burnt" products to turn black. It is often used together with Ba and Ca soaps.
(2) Cadmium stearate (CdSt) is an important transparent stabilizer. It has high toxicity, is not resistant to sulfide pollution, and has a large ability to inhibit initial discoloration. It is often used in combination with Ba soap.
(3) Lead stearate (PbSt) has good thermal stability and can be used as a lubricant. Disadvantages are easy precipitation, poor transparency, poisonous and serious sulfide pollution, often used with Ba and Cd soap.
(4) Calcium stearate (CaSt), good processing performance, low thermal stability, no sulfide pollution, non-toxic, often used with Zn soap.
(5) Barium stearate (BaSt), non-toxic, long-term thermal stability, anti-sulfurization pollution, transparent, often used with Pb, Ca soap. Compound varieties are commonly used: Ca / Zn (non-toxic, transparent), Ba / Zn (non-toxic, transparent), Ba / Cd (toxic, transparent) and Ba / Cd / Zn.
3. Organotin
Organotin is the most effective heat stabilizer and the most widely used in transparent and non-toxic products. Its outstanding advantages are: good thermal stability, good transparency, and most are non-toxic. The disadvantage is high price and no lubricity.
Most of the organic tins are liquid, and only a few are solid. It can be used alone or in combination with metal soaps.
Organotin heat stabilizers mainly include sulfur-containing organotin and organotin carboxylate.
(1) Sulfur-containing organotin:
It is mainly thiol organotin and organotin sulfide stabilizers. It can produce sulfur pollution when used in combination with Pb and Cd soaps. Sulfur-containing organotins have good transparency. The main varieties are:
a, Di-octyl dimercaptoacetate di-n-octyl tin (DOTTG), light yellow liquid, excellent thermal stability and transparency, non-toxic, less than 2 parts.
b. Dimethyldimercaptoacetic acid isooctyl tin (DMTFG), the appearance is a light yellow clear liquid, a non-toxic, high-efficiency, transparent stabilizer, commonly used in kink film and transparent film.
(2) Organotin carboxylate:
The stability is not as good as sulfur-containing organic tin, but no sulfur pollution, mainly including fatty acid tin salt and maleic acid tin salt. The main varieties are:
a, Di-n-butyl tin dilaurate (DBTL) light yellow liquid or semi-solid, excellent lubricity, good transparency, but toxic, often used with Cd soap, dosage 1-2 parts; with tin maleate and tin thiolate Used in combination, the dosage is 0.5-1.
b. Di-n-octyltin dilaurate (DOTL) is toxic and expensive, with excellent lubricity. It is often used in hard PVC with an amount of less than 1.5 parts. c. Di-n-butyl tin maleate (DBTM), white powder, toxic, non-lubricating, often used with tin laurate, not used with metal soaps in transparent products.
4. Organic antimony
It has excellent initial hue and hue retention, especially at low dosage, its thermal stability is better than organic tins, and it is especially suitable for PVC formulations with twin-screw extruders.
Organic antimony mainly includes thiol antimony salts, mercaptoacetate thiol antimony, mercaptocarboxylate antimony and carboxylate antimony. The domestic antimony stabilizers are mainly composed of isooctyl trimercaptoacetate antimony (ST) and the composite stabilizers STH-I and STH-Ⅱ with ST as the main component. Antimony pentathiol is a transparent liquid and can be used as a heat stabilizer for transparent tablets, films, and transparent pellets. STH-I can replace Jingxi C-102, can inhibit the initial coloring of PVC, good thermal stability, transparent products, bright colors, STH-Ⅱ non-toxic, mainly used in PVC water pipes.
5. Rare earth stabilizer
The materials selected are mostly rare earth oxides and rare earth chlorides, and their oxides and chlorides are mostly single bodies or mixtures of light rare earth elements such as lanthanum, cerium, praseodymium, and neodymium.
Rare earth elements have similar and unusually active chemical properties. They have many orbits that can be used as central ions to accept the lone pair electrons of the ligand. At the same time, the rare earth metal ions have a large ionic radius. Formation of ionic coordination bonds, as the central atom of the complex, often forms a complex with a coordination number of 6-12 in various hybrid forms such as d2SP3, d4dP3, f3d5Ssp3.
The excellent mechanical properties and grouping principles of rare earth elements are related to the geometric properties of rare earth elements. Because the radius of atoms and ions is an important factor that determines the physical properties of the crystal such as configuration, hardness, density and melting point, under normal temperature and pressure conditions, the rare earth metals lanthanum, praseodymium, and neodymium have a double hexagonal crystal structure, while cerium has a cubic structure. The crystal is dense (face-centered) structure, and when the temperature and pressure change, most rare earth metals undergo crystalline transformation. Due to the shrinkage of the lanthanide series, the atomic radius and atomic volume of lanthanide elements decrease with the increase of atomic number, and the density increase with the increase of atomic number. However, cerium has abnormal phenomena compared with lanthanum, praseodymium, and neodymium.
Among lanthanum, cerium, praseodymium, and neodymium, the chemical properties of lanthanum are the most active, but trivalent lanthanum and C1 can only generate RECl positive complexes, and this complex is unstable, while cerium, praseodymium, these expensive rare earth ions The ability to form complexes with Cl is stronger than trivalent lanthanum, and they can generate stable negative complex ions with Cl ligands. Therefore, the respective advantages of lanthanum, cerium, praseodymium, and neodymium should be integrated in the selection of rare earth thermal stabilizers , In different applications, use its high-purity single, mixed or reasonable mix.
Rare earth ions are typical hard cations, that is, ions that are not easily polarized and deformed, and their coordination ability with metal hard base coordination atoms, such as oxygen, is very strong. The coupling effect of rare earth compounds on CaC03, due to the strong coordination interaction between the rare earth ions and the chloride ions of the PVC chain, is conducive to the transmission of shear force so that the rare earth compounds can effectively accelerate the gelation of PVC. Promote the plasticization of PVC, and can also play the role of processing aid ACR. At the same time, the coordination of rare earth metal ions with C1 in CPE can make CPE more play its role of toughening and modification. Whether these functions are fully utilized, balanced or not, has a considerable relationship with the compounding aid in the rare earth compound. The lubricating system and processing modification system in the compound are very important, so the compounding process is good Bad directly affects the performance of rare earth multifunctional composite stabilizer. The rare earth stabilizer with excellent performance should have the following functions:
(1) Excellent thermal stability
The static and dynamic thermal stability is equivalent to that of Jingxi 8831, better than lead salts and metal soaps, three times that of lead salts and 4 times that of Ba / Zn composite stabilizer. It can be compounded to be non-toxic and transparent, and it can also be partly used instead of organotin stabilizer. The mechanism of action of the rare earth stabilizer is to capture HCl and displace allyl chloride atoms, and has a good synergistic effect with the auxiliary stabilizer of epoxy type.
(2) Coupling
It has excellent coupling effect. Compared with lead salt, it has good compatibility with PVC. For PVC-CaCO, the coupling effect of the system is better, which is beneficial to the strength of PVC plastic doors and windows. The welded corner strength of PVC profiles processed with rare earth stabilizers is higher than that of lead salt stabilizers, and the raw material prices are also higher.
(3) Toughening effect
Good compatibility with PVC resin and toughening agent CPE and coupling with CaCO3, make PVC resin plasticize evenly during processing, low plasticizing temperature, and good impact resistance of the profile.
Rare earth stabilizers have no lubricating effect and should be added together with lubricants. At present, the rare earth composite stabilizers produced in China are compounded with rare earths, heat stabilizers and lubricants, and the addition amount is generally 4-6 parts.
6. Compound lead salt stabilizer
lead
Salt stabilizers are cheap and have good thermal stability, and have been widely used. However, the powder of lead salt is fine. In the ingredients and mixing, the dust of the salt is inhaled by people and it will cause lead poisoning. Compound lead salt heat stabilizer. This composite additive uses symbiotic reaction technology to mix tri-salt, di-salt and metal soap in the reaction system with the initial ecological grain size and various lubricants to ensure the full dispersion of the heat stabilizer in the PVC system At the same time, due to co-melting with lubricant to form particles, it also avoids poisoning caused by lead dust. The compound lead salt stabilizer contains the heat stabilizer component and lubricant component required for processing, and is called the full package heat stabilizer. It has the following advantages:
(1) The various components of the composite heat stabilizer can be fully mixed during the production process, which greatly improves the uniformity of mixing and dispersion with the resin.
(2) When the formula is mixed, the measurement times are simplified, and the probability of measurement errors and the losses caused thereby are reduced.
(3) The supply and storage of auxiliary materials are simplified, which is conducive to production and quality management.
(4) The possibility of producing products without dust is provided, and the production conditions are improved.
In short, the compound heat stabilizer is conducive to large-scale production and provides a new direction for the development of lead salt heat stabilizers. An important indicator of the compound lead salt stabilizer is the lead content. The lead content of the compound lead salt stabilizer currently produced is generally 20% -60%; the amount used in the production of PVC plastic door and window profiles is 3.5-6 parts. Table 2 shows the grades and dosages of composite lead salt stabilizers used in the production of some PVC profiles.
7. Main auxiliary heat stabilizer varieties
The auxiliary pad stabilizer itself does not have a heat stabilizing effect. Only when used in combination with the main stabilizer, will the heat stabilizing effect be produced and promote the stabilizing effect of the main stabilizer. Auxiliary heat stabilizers generally do not contain metals, so they are also called non-metal heat stabilizers.
The main varieties of auxiliary heat stabilizers are:
(1) Phosphites. It is an important auxiliary heat stabilizer, and has a synergistic effect with Ba / Cd, Ba / Zn composite stabilizer and Ca / Zn composite stabilizer, etc. It is mainly used in soft PVC transparent formulations, the dosage is 0.1-1 parts .
(2) Epoxy compounds have a synergistic effect with metal soaps and have good effect when used with organotin rare earth stabilizers. The dosage is 2-5 parts. The commonly used varieties are epoxy soybean oil and epoxy grease.
(3) Polyols, mainly pentaerythritol, xylitol, mannitol, etc., can be used with Ca / Zn composite stabilizer.
Lubricant
The role of the lubricant is to reduce the friction between the materials and the surface of the materials and processing equipment, thereby reducing the flow resistance of the melt, reducing the viscosity of the melt, improving the fluidity of the melt, avoiding the adhesion of the melt to the equipment, and improving the products Surface finish, etc.
According to different molding methods, the emphasis on lubrication is different:
Calendering to prevent the melt from sticking to the roller;
Injection molding, improve flow and improve mold release;
Extrusion molding to improve flow and die separation;
Pressing and lamination are beneficial to the separation of the pressing plate and the product.
Classification of lubricants:
· Classified by lubricant ingredients, mainly saturated hydrocarbons and halogenated hydrocarbons, fatty acids, fatty acid esters, aliphatic ester amines, metal soaps, fatty alcohols and polyhydric alcohols.
· According to the role of lubricant, it is divided into internal and external lubricants.
The main distinction is based on its compatibility with the resin. The internal lubricant has a high affinity with the resin, and its role is to reduce the intermolecular force; the external lubricant has a low affinity with the resin, and its role is to reduce the friction between the resin and the metal surface.
The difference between internal and external lubricants is only relatively speaking, and there is no strict classification standard. In resins with different polarities, the role of internal and external lubricants may change. For example, stearic alcohol, stearic acid amide, butyl stearate and stearic acid monoglyceride have internal lubrication for polar resins (such as PVC and PA); but for non-polar resins (such as PE , PP), showing external lubrication. In contrast, polymer paraffin and other polar resins have poor compatibility. For example, they are used as external lubricants in polar PVC, and internal lubricants in non-polar resins such as PE and PP.
At different processing temperatures, the role of internal and external lubricants will also change. For example, stearic acid and stearyl alcohol are used in the initial stage of PVC calendering. Due to the low processing temperature and poor compatibility with PVC, they mainly play the role of external lubrication; When the temperature increases, the compatibility with PVC increases, then it acts as an internal lubricant.
According to the composition of the lubricant, it can be divided into: saturated hydrocarbons, metal soaps, aliphatic amides, fatty acids, fatty acid esters and fatty alcohols.
1. Saturated hydrocarbons
Saturated hydrocarbons can be divided into non-polar hydrocarbons (such as polyethylene wax and polypropylene wax), polar hydrocarbons (such as chlorinated paraffin, oxidized polyethylene, etc.) according to polarity. Saturated hydrocarbons can be divided according to molecular weight; liquid paraffin (C16-C21), solid paraffin (C26-C32) microcrystalline paraffin (C32-C70) and low molecular weight polyethylene (molecular weight 1000-10000), etc., mainly used for PVC Non-toxic external lubricant.
(1) Liquid paraffin: Commonly known as white oil, it is a colorless transparent liquid, which can be used as a transparent external lubricant for PVC. The dosage is about 0.5 parts. The dosage will seriously affect the strength of the welding corner.
(2) Solid paraffin, also known as natural paraffin, white solid, can be used as an external lubricant for PVC. The dosage is 0.1-1.0 parts. Too much dosage will affect transparency.
(3) Microcrystalline paraffin, also known as high-melting paraffin, has a white or light yellow solid appearance, and is called microcrystalline paraffin because of fine crystals. The lubricating effect and thermal stability are better than other paraffin waxes. The amount used in PVC is relatively small, generally 0.1 to 0.3 servings.
(4) Low molecular weight polyethylene, also known as polyethylene wax, is a white or light yellow solid powder with poor transparency. It can be used as an external lubricant for PVC extrusion and calendering. The dosage is generally less than 0.5 parts.
(5) Oxidized polyethylene wax, which is a partial oxidation product of polyethylene wax, and its appearance is white powder. It has excellent internal and external lubrication, good transparency, low price, and the dosage is 0.2-1.
(6) Chlorinated paraffin, good compatibility with PVC, poor transparency, good effect when used with other lubricants, the dosage is less than 0.5 parts.
2. Metal soaps
It is both an excellent heat stabilizer and a lubricant. It has both internal and external lubricating functions. Different varieties have slightly different emphasis. The lubricity is calcium stearate and lead stearate.
3. Aliphatic acid amine
Including two major categories of single fatty acid amides and double fatty acid amides, single fatty acid amines mainly exhibit internal lubrication, the main varieties include X double stearamide, N, N · sub X X ricinoleic acid amide, etc.
4. Fatty acids
For example, stearic acid is a lubricant widely used next to metal soaps. It can be used in PVC. When the amount is small, it acts as internal lubrication; when the amount is large, it acts as external lubrication. The amount of stearic acid added is less than 0.5 parts.
5. Fatty acid esters
(1) Butyl stearate, the appearance is colorless or light yellow oily liquid, which is mainly lubricated internally and externally lubricated in PVC, the dosage is 0.5-1.5 parts.
(2) Glycerol monostearate, code-named GMS, white waxy solid appearance, excellent internal lubricant for PVC, little effect on transparency, added in less than 1.5 parts, can be used with stearic acid.
(3) Ester wax and saponification wax mainly refer to the post-sequence products made with montan wax as the main raw material and bleached. Bleaching waxes include S wax and L wax, and saponified waxes include 0 wax and OP wax. Mainly used for HPVC, the dosage is 0.1-0. 3 copies.
6. Fatty alcohols
Stearyl alcohol, the appearance of white fine beads, internal lubrication, good transparency, the amount of 0.2 to 0.5 in PVC. Can also be used in PS. Such as pentaerythritol, used as PVC high temperature lubricant, the dosage is 0.2-0. 5 parts.
Processing modifier
1. The working principle of processing aids
Due to the poor ductility of the PVC melt, it is easy to cause the melt to break; the PVC melt relaxes slowly, which easily causes the surface of the product to be rough, dull, and shark skin. Therefore, PVC processing often needs to add processing aids to improve the above defects of its melt.
Processing aids are additives that can improve the processing properties of resins. There are three main modes of action: promoting resin melting, improving melt rheological properties, and imparting lubrication.
· Promote resin melting: When the PVC resin is heated and melted under a certain shear force, the processing modifier first melts and adheres to the surface of the PVC resin particles. Its compatibility with the resin and its high The molecular weight increases the viscosity and friction of PVC, which effectively transfers shear stress and heat to the entire PVC resin and accelerates the melting of PVC.
· Improve melt rheological properties: PVC melt has the disadvantages of poor strength, poor ductility and melt rupture, and processing modifiers can improve the above rheology of the melt. Its mechanism of action is to increase the viscoelasticity of the PVC melt, thereby improving the die expansion and increasing the melt strength.
· Giving lubricity: the processing modifier is compatible with the first part of PVC to melt, which promotes melting; while the part incompatible with PVC migrates out of the molten resin system, thereby improving mold release.
2. ACR, a commonly used processing modifier
ACR is a copolymer of methyl methacrylate and monomers such as acrylate and styrene. In addition to being used as a processing aid, it can also be used as an impact modifier. I. ACR in China can be divided into ACR201, ACR301 and ACR401, ACR402. Foreign brands are: K120N, K125, K175, P530, P501, P551, P700, PAl00, etc. Table 2—1-3 is a comparison of domestic and foreign ACR processing aid brands. Table 3 Comparison of domestic and foreign ACR processing aid brands.
The important role of ACR processing modifier is to promote the plasticization of PVC, shorten the plasticization time, improve the uniformity of melt plasticization, and reduce the plastic flower temperature. Table 4 shows the effect of ACR measured by BLANBENDE plasticity meter on plasticizing time and temperature.
ACR201 or ACR401 is generally used in PVC plastic door and window profiles, and the dosage is 1.5-3 parts.
Impact modifier
An important content of polymer material modification is to improve its impact resistance. PVC resin is a polar non-crystalline polymer with strong interaction between molecules. It is a hard and brittle material; impact strength Lower. After adding the impact modifier, the elastomer particles of the impact modifier can reduce the total silver streak-induced stress, and use the particle's own deformation and shear band to prevent the silver streak from expanding and growing, and absorb the impact from the body Yes, so as to achieve the purpose of anti-impact. The particles of the modifier are small, which is beneficial to increase the number of modifiers per unit weight or unit volume, and increase the effective volume fraction, thereby enhancing the ability to disperse stress. At present, organic impact modifiers are widely used.
According to the internal molecular structure of the organic impact modifier, it can be divided into the following categories.
1. Predetermined elastomer (PDE) type impact modifier, which belongs to a polymer with a core-shell structure, the core is a soft elastomer, which gives the product high impact resistance, and the shell is a polymer with a high glass transition temperature The main function of the substance is to isolate the modifier particles from each other to form free-flowing component particles, promote their uniform dispersion in the polymer, and enhance the interaction and compatibility between the modifier and the polymer. Modifiers of this structure are: MBS, ACR, MABS, MACR, etc., these are excellent impact modifiers.
2. Unscheduled elastomer type (NPDE) impact modifier, which belongs to the network polymer, and its modification mechanism is to modify the plastic by solvation (plasticization) mechanism. Therefore, NPDE must form a resin-coated network structure, which is not a very good compatibility with the resin. Modifiers of this structure are: CPE, EVA.
3. Excessive impact modifier, whose structure is between two structures, such as ABS. The specific varieties used for PVC resin are:
(1) Chlorinated polyethylene (CPE) is a powdered product that is suspended and chlorinated by HDPE in the aqueous phase. As the degree of chlorination increases, the originally crystallized HDPE gradually becomes a non-crystalline elastomer. C? E used as a toughener generally contains 25-45% of C1. CPE has a wide range of sources and low prices. In addition to its toughening effect, it also has cold resistance, weather resistance, flame resistance and chemical resistance. CPE is currently the dominant impact modifier in China, especially in the production of PVC pipes and profiles, most factories use CPE. The added amount is generally 5-15 parts. CPE can be used in conjunction with other toughening agents, such as rubber, EVA, etc., the effect is better, but rubber additives are not resistant to aging.
(2) ACR is a copolymer of monomers such as methyl methacrylate and acrylate. ACR is the best impact modifier developed in recent years. It can increase the impact strength of materials by several tens of times. ACR belongs to the impact modifier of the core-shell structure, the outer shell composed of methyl methacrylate-ethyl acrylate high polymer, the rubber elastomer formed by the cross-linking of butyl acrylate as the core is distributed in the inner layer of the particles. Especially suitable for impact modification of PVC plastic products used outdoors. The use of ACR as an impact modifier in PVC plastic door and window profiles has better processing performance, smooth surface, good aging resistance, and high weld angle strength compared with other modifiers. Features, but the price is about 1/3 higher than CPE. Commonly used foreign brands such as K-355, the general dosage is 6-10 copies. At present, there are fewer domestic manufacturers of ACR impact modifiers and fewer manufacturers.
(3) MBS is a copolymer of three monomers of methyl methacrylate, butadiene and styrene. The solubility parameter of MBS is between 94-9.5, which is close to the solubility parameter of PVC, so it has better compatibility with PVC. Its biggest feature is that it can be made into transparent products after adding PVC. Generally, adding 10-17 parts of PVC can increase the impact strength of PVC by 6-15 times, but when the amount of MBS added is greater than 30 parts, the impact strength of PVC decreases instead. MBS itself has good impact performance, good transparency, and light transmittance can reach more than 90%, and at the same time improve impact resistance, it has little effect on other properties of the resin, such as tensile strength and elongation at break. MBS is relatively expensive, and is often used in combination with other impact modifiers such as EAV, CPE, SBS, etc. MBS has poor heat resistance and poor weather resistance. It is not suitable for long-term outdoor use. It is generally not used as an impact modifier for plastic door and window profiles.
(4) SBS is a ternary block copolymer of styrene, butadiene, and styrene, also known as thermoplastic styrene-butadiene rubber. It is a thermoplastic elastomer, and its structure can be divided into two types: star and linear. The ratio of styrene to butadiene in SBS is mainly 30/70, 40/60, 28/72, 48/52. It is mainly used as impact modifier of HDPE, PP, PS, and its added amount is 5-15 parts. The main function of SBS is to improve its low temperature impact resistance. SBS has poor weather resistance and is not suitable for long-term outdoor use.
(5) ABS is a terpolymer of styrene (40% -50%), butadiene (25% -30%), acrylonitrile (25% -30%), mainly used as engineering plastics, but also used as PVC Impact modification is also very good for low temperature impact modification. When the amount of ABS added reaches 50 parts, the impact strength of PVC can be compared with pure AB
S is equivalent. The amount of ABS added is generally 5-20 parts. ABS has poor weather resistance and is not suitable for long-term outdoor use. It is generally not used as an impact modifier for the production of plastic door and window profiles. (6) EVA is a copolymer of ethylene and vinyl acetate. The introduction of vinyl acetate changes the crystallinity of polyethylene. The content of vinyl acetate is very poor. Moreover, the refractive index of EVA and PVC is different. It is difficult to obtain transparent products. Use EVA in combination with other impact-resistant resins. The amount of EVA added is 10 parts or less.
4. Rubber impact modifier
It is a toughening agent with excellent performance. The main varieties are: ethylene propylene rubber (EPR), EPDM (EPDM), nitrile rubber (NBR) and styrene-butadiene rubber, natural rubber, butadiene rubber, neoprene, Polyisobutylene, butadiene rubber, etc., among which EPR, EPDM, NBR are the three most commonly used. They are excellent in improving low temperature impact resistance, but are not resistant to aging. Plastic door and window profiles generally do not use such impact modifiers.
Other commonly used additives
1. Light stabilizer
Most PVC products are exposed to sunlight and other various light. Adding a certain amount of light stabilizer according to the application environment of the product can prevent and delay its decomposition and aging, and extend the service life of the product.
Light stabilizers can be roughly divided into four categories:
(1) Light shielding agent. Such as titanium white and carbon black, can block ultraviolet rays from entering the interior of the profile to prevent the photodegradation of the polymer from proceeding. For example, the aging resistance of LDPE sheet with 2% carbon black is 20 times higher than that of LDPE sheet without carbon black. Titanium white has a greater improvement in the aging resistance of the profile. Titanium white should use rutile type, and the amount used in PVC plastic door and window profiles is 3-6 parts.
(2) Ultraviolet absorbent. It can strongly absorb 280-400nm ultraviolet light and convert it into visible light or heat. Commonly used are UV-531, UV-327, UV-326, UV-p and other products, the dosage is generally 0.1-0.5%. But the price is higher.
(3) Quenching agent. The main purpose is to destroy the energy of the excited polymer molecules and bring them back to the ground state. The specific varieties are nickel and cobalt complexes. The varieties include light stabilizer 2002 and light stabilizer 1084. Generally used in conjunction with other light stabilizers, the dosage is 0.1-0.5%.
(4) Free radical scavenger. It is an efficient light stabilizer, which captures free radicals decomposed by photodegradation and stops the degradation reaction. Generally used in LDPE agricultural film. The main varieties are: light stabilizers GW-540, GW-544, CW-310, BW-10LD, light stabilizer 744, light stabilizer 622, light stabilizer 944, etc., the amount of 0.02-0.5%.
2. Filler
The main purpose of using fillers is to occupy space to reduce costs. Of course, some fillers also give the material some special properties, such as flame retardancy, electrical conductivity, thermal conductivity, and rigidity.
The main indicators of fillers are: whiteness, particle size, particle shape and particle surface activity.
Its main varieties are:
(1) Carbonates are mainly heavy calcium carbonate, light calcium carbonate and activated calcium carbonate. Generally, activated light calcium carbonate is used in PVC plastic profiles with a particle size of 300 mesh to 700 mesh.
(2) Carbon black such as natural gas channel black, gas mixing channel black, high wear-resistant furnace black, thermal cracking method black, acetylene carbon black, etc. The main function is to reinforce rubber, and some varieties are also used as fillers, such as used in conductive and antistatic polymer materials.
(3) Sulfates There are barium sulfate, calcium sulfate, zinc barium white (lead powder), etc., which are mainly used as fillers and also have a coloring effect. Barium sulfate can reduce the X-ray transmittance.
(4) Metal oxides such as alumina, iron oxide, manganese oxide, zinc oxide, antimony oxide, magnesium oxide, iron oxide, magnetic powder, etc., are used as fillers and colorants.
(5) Metal powders such as aluminum, bronze, zinc, copper, lead and other powders are used for decoration and to improve thermal conductivity. In the production of plastic profiles, copper powder and aluminum powder are sometimes used to produce aluminum window profiles.
(6) Silicon-containing compound The most commonly used clay is kaolin clay as a filler. Hard clay has a reinforcing effect. Talc powder is used as a filler.
(7) Fibers, such as glass fiber, boron fiber, carbon fiber, etc., are used as reinforcing agents.
Profile design
Principles of formula design for PVC plastic profiles
1. The resin should choose PVC-SC5 resin or PVC-SG4 resin, that is, polyvinyl chloride resin with a polymerization degree of 1200-1000.
2. The thermal stability system must be added. Choose according to the actual requirements of production, pay attention to the synergistic effect and confrontation effect between heat stabilizers. The characteristics of different thermal stability systems are described in the table above:
3. Impact modifier must be added. CPE and ACR impact modifiers can be selected. According to the other components in the formula and the plasticizing ability of the extruder, the addition amount is 8-12 parts. The price of CPE is low and the sources are wide; ACR has the ability to resist aging and the strength of the welding angle is high.
4. Add a proper amount to the lubrication system. The lubricating system can reduce the processing machinery load and make the product smooth, but excessive strength will cause the weld corner strength to decrease.
5. Adding processing modifiers can improve the quality of plasticization and improve the appearance of products. Generally, ACR processing modifier is added in an amount of 1-2 parts.
6. The addition of fillers can reduce the cost, increase the rigidity of the profile but has a greater impact on the low-temperature impact strength. The active fine calcium carbonate with a higher fineness should be selected and added in an amount of 5-15 parts.
7. A certain amount of titanium white must be added to shield the ultraviolet rays. Titanium white should choose rutile type, and the added amount is 4-6 parts. When necessary, ultraviolet absorbers UV-531, UV327, etc. can be added to increase the aging resistance of the profile.
8. Adding blue and fluorescent whitening agent in proper amount can obviously improve the color of the profile.
9. The design formula should be simplified as much as possible, and no liquid additives should be added, and the formula should be divided into batches No. I, No. II, and No. III according to the mixing process requirements (see mixing problems) in batches in the order of addition.
Examples and characteristics of various formulas
Classification from the heat stabilizer used:
1. Formula of organic tin stabilizer
PVCSG-5 100 copies
Tin thiolate (Jing Tin 8113) 2-3 servings
Calcium stearate 1-2 servings
ACR401 1-2 copies
CPE (35%) 8-10 copies
Active light calcium 6-8 servings
Titanium white (rutile) 4-6 parts
PE wax 0.5-1 copies
The characteristics of the formula: non-toxic, little dust pollution, high welding strength of the profile. Disadvantages: high price, odor during production, can not be mixed with PVC materials using lead salt stabilizers.
2. Formula of rare earth stabilizer
PVC-SG5 100 copies
Rare earth composite stabilizer 4-6 parts
ACR401 1-2 copies
CPE (35%) 8-10 copies
Active light calcium 6-8 servings
Titanium white (rutile) 4-6 parts
PE wax 0.2-0.5 copies
The characteristics of the formula: non-toxic, high welding strength of the profile. Disadvantages: higher prices.
3. Compound lead salt stabilizer formula 1
PVC (K66-68) 100 copies
5 parts of composite lead SMS50011FP
Baerorapid 10F 1 serving
Baerodur EST-3 8 servings
Active Light Calcium 5 servings
Titanium white (rutile) 5 servings
4. Compound lead salt stabilizer formulation 2
PVC-SG5 100 copies
Compound lead (HJ-301) 5 parts
Stearic acid 0.3 servings
ACR401 2 copies
CPE (35%) 10 copies
Active light calcium 6 servings
Titanium white (rutile) 4 parts
The characteristics of the formula: little lead pollution in production, good processing fluidity, easy operation and moderate price.
5. Formula of lead salt stabilizer
PVC-SG5 100 copies
3 servings of salt
1.5 salt
Calcium stearate 0.5 servings
Barium stearate 0.5 servings
Lead stearate 0.5 servings
Stearic acid 0.5 servings
ACR401 2 copies
CPE (35%) 10 copies
Active light calcium 8 servings
Titanium white (rutile) 4 parts
Oxidized PE wax 0.3 parts
Paraffin 0.3 parts
The characteristics of the formula: low cost and good stability. Disadvantages: Lead pollution is easy to occur in production, and the batching operation is troublesome.
The impact modifiers used are CPE and ACR. The above listed are all CPE formulations. There are many factories in China that produce CPE and the price is lower. The ACR impact modifier is used more abroad, characterized by good processing performance, good welding properties of profiles, good aging resistance, and a slightly higher price than CPE. The following example is a formula using ACR impact modifier:
6. ACR impact modifier formula
PVC (K65) 100 copies
3 servings of salt
Calcium stearate 0.5 servings
Barium stearate 0.5 servings
Lead stearate 0.5 servings
Stearic acid 0.5 servings
ACR K125P 0.8 copies
ACR K175 0.5 copies
6 copies of ACRKM355P
Active light calcium 6 servings
Titanium white (rutile) 4 parts
PE wax 0.2 copies
The formulas listed above are for reference only. When determining the production formula of an enterprise, the enterprise should also determine it according to the enterprise's equipment capabilities, the sources of various additives, the quality stability and the price and cost. Once the formula is determined, do not change the formula often to stabilize production. Changes in formulations often cause changes in material flow properties, affecting mold and extrusion process control.
If you want to know more about it please do not hesitate to
contact me. WhatsApp:+86-15966835076.
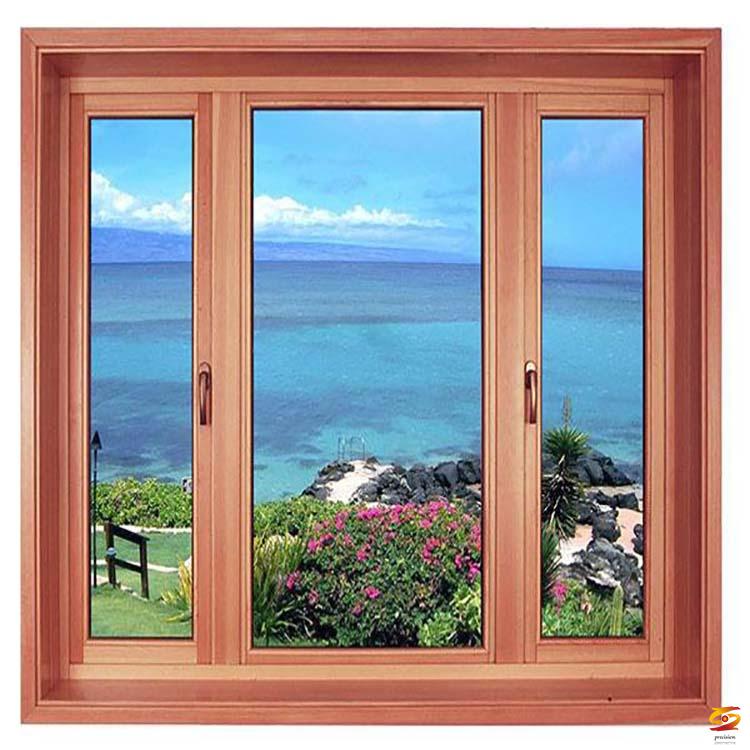
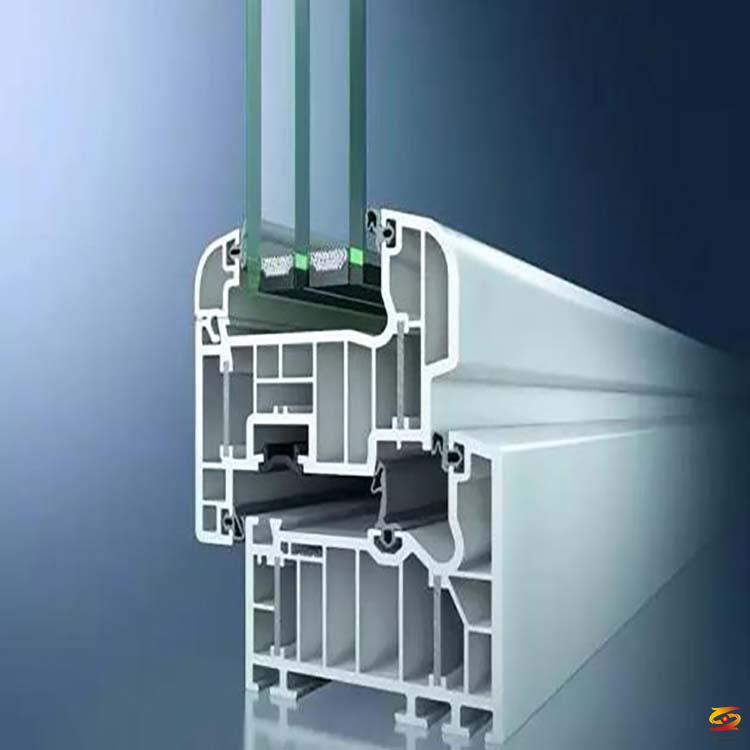