Problems and solutions of SPC floor in the production process
Problems and solutions of SPC floor in the production processSPC stone-plastic flooring is a new type of environmentally friendly flooring developed based on high technology. The extruder is combined with a T-die to extrude the PVC substrate. The three-roll or four-roll calender is used to separate the PVC wear-resistant layer, PVC color film layer PVC substrate, one-time heating and embossing products, the process is simple, the bonding is completed by heat, and no glue is required. SPC floor materials use environmentally friendly formulas and do not contain heavy metals, phthalates, formaldehyde and other harmful substances. They are mainly composed of calcium powder and polyvinyl chloride stabilizer combined to form a composite flooring material. It complies with EN 14372, EN649-2011, IEC62321 and GB 4085-83 standards. It is a new material invented in response to national emission reduction. It is very popular in the home improvement market at home and abroad. Description: SPC floor has the advantages of waterproof, moisture-proof, non-slip, formaldehyde-free, easy to recycle, soft and silent. Plate specifications generally have a thickness of 3-10mm, a width of 120-400mm, and a length of 600-1800mm. Extrusion: the production of substrates, the base material of general wood-plastic floors is foamed plastic, and the thickness of the substrate is generally 4-6mm. The floor (SPC) generally adopts online lamination, and the surface decoration PVC film is posted online. UV coating production line is mainly aimed at furniture factory, wooden door factory, cabinet factory and other panel furniture factories, producing veneer, solid wood substrate, density board and other boards for UV surface coating. The multi-function UV coating production line has less investment, quick results, and less floor space, which can greatly save operating time, improve production efficiency, reduce coating costs, and reduce VOC emissions. Glue laminating machine: After the base material is glued, the PVC board with wood grain is superimposed on it for bonding, generally the PVC board is 1.5-2.5mm. In order to improve the strength of the bonding, it is recommended to use a cold press to maintain the pressure of the bonded plate for about 4 hours.
Slotting: Through the vertical and horizontal slotting equipment, the edges of the sheet are processed to obtain the final finished floor. Customers need to choose reasonable standard specifications and button types.
The advantages of SPC environmental protection floor
(1) Waterproof and moisture-proof. It fundamentally solves the problem that wood products easily rot and swell and deform after absorbing moisture in wet and watery environments, and can be used in environments where traditional wood products cannot be used. (2) Insect-proof and termite-proof, effectively prevent insect harassment and prolong service life. (3) Colorful, with many colors to choose from. It not only has natural wood feeling and wood texture, but also can be customized according to your own personality. (4) It has strong plasticity, can easily achieve personalized modeling, and fully reflects the individual style (5) High environmental protection, no pollution, no pollution Pollution and recycling. The product does not contain benzene and formaldehyde, it is an environmentally friendly product, and it can be recycled to greatly save the amount of wood used. It is a national policy for sustainable development and benefits the society. (6) High fire resistance. It can effectively flame retardant, and its fire rating reaches B1 level. It will self-extinguish in case of fire and will not produce any toxic gas. (7) Good machinability, can be ordered, planed, sawn, drilled, and the surface can be painted. (8) The installation is simple and the construction is convenient, without complicated construction techniques, saving installation time and costs. (9) No cracking, no expansion, no deformation, no need for repair and maintenance, easy to clean, save the cost of later repair and maintenance. Good sound absorption and energy saving.
SPC floor production process
Process 1: Mix the materials according to the raw material formula ratio, pour into → high-speed mixer hot mixing (hot mixing temperature: 125 ℃, the role is to mix all materials uniformly, exclude moisture in the material) → enter cold mixing (cooling the material, preventing Agglomeration and discoloration, cold mixing temperature: 55°C.) → Mix materials uniformly by cooling; Step 2: Extrusion into a twin-screw extruder for heating and extrusion → Enter the sheet die selected by the customer for extrusion molding , The formed sheet passes through a four-roll calender, and the base material is set to a thickness → paste color film → paste wear layer → cooling → cutting; process 3: UV tempering surface UV → tempering (tempering hot water temperature: 80~120) ℃; cold water temperature: 10℃) Process 4: slitting slot + packaging
Slitting → slotting → inspection → packaging
production material
SPC flooring often encounters some problems in production:
With the market demand, traditional flooring is gradually replaced by new environmentally friendly SPC flooring, but with the explosive growth, from equipment to production, many problems are encountered. Below I will briefly list some of these problems: 1. New customers The problems encountered in the selection of equipment, there are currently many models of SPC floor equipment, from the early 80/156 cone double to the later 92/188 cone double, to the current 110/220 cone double, Nowadays, the production of Ping Shuang has risen again in the market, 115 Ping Shuang, 135 Ping Shuang. The advantages and disadvantages of these models are listed below: The 80/156 cone double extrusion production is the earliest batch. The advantage is stable production. The disadvantages are that the output is too low and the speed is slow. With the customer's order quantity and plant area and other issues, this extrusion production was quickly replaced by 92 cone double. The 92/188 cone double production line is also the main force in the early days. The advantages and output have been improved, and the disadvantages are that the service life of the screw is not long. The advantage of 110/220 cone double production is that the output is much improved, which can be 25-30 tons per hour, and the disadvantage is that the screw life is not long. The advantages of the 115 flat double production line are energy saving, the output is higher than the 92 cone double, the energy consumption is not as large as the 92 cone double, and the service life of the screw is extended. The shortcomings of the current domestic gearbox and screw production are not mature enough, and the screw is prone to death. The 135 flat double production line can also be said to be the production line with the highest output at present. At present, the domestic customer's usage is not very large. According to the design of the equipment manufacturer, the output can reach 40 tons per hour, and some equipment factories are testing 50 tons per hour. It is 160KW, which is smaller than the 200KW of the 110 cone double. According to the actual output I have contacted, it should be around 35 tons. This model is still in the experimental stage. At present, the main use is the 110/220 cone double production line. Therefore, new customers will encounter difficulties in selecting equipment manufacturers and models. At present, there is no uniform standard for domestic equipment. 2. Extrusion production models, from the early standing four rolls to the current flat four sticks and flat five sticks, can be said to have different advantages. At present, the most commonly used flat five rolls are easy to operate. 3. Introducing the configuration of the mixer, the mixer is also changing with the output of the extruder, from the early 500/100, 800/2500, 1000/3000, and now 1500/4500. It can be said The output is also gradually increasing. Due to environmental protection requirements, large factories currently use fully automatic or semi-automatic mixing methods. The main change is that the calcium powder is separately added to the discharge tank, which is easier for labor. It can be automatically measured, which also facilitates the increase and decrease of the added amount. The mixing part can also be said to be the source of the entire process, which seems to be an unimportant link, but it will affect the entire production process.
If you want to know more about it please do not hesitate to
contact me. WhatsApp:+86-15966835076.
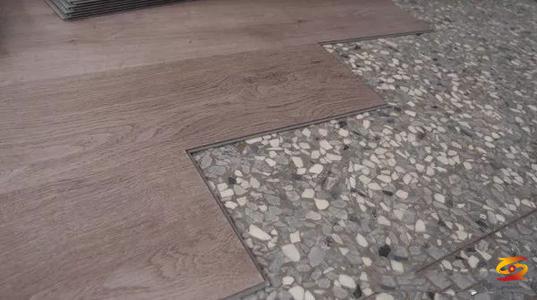
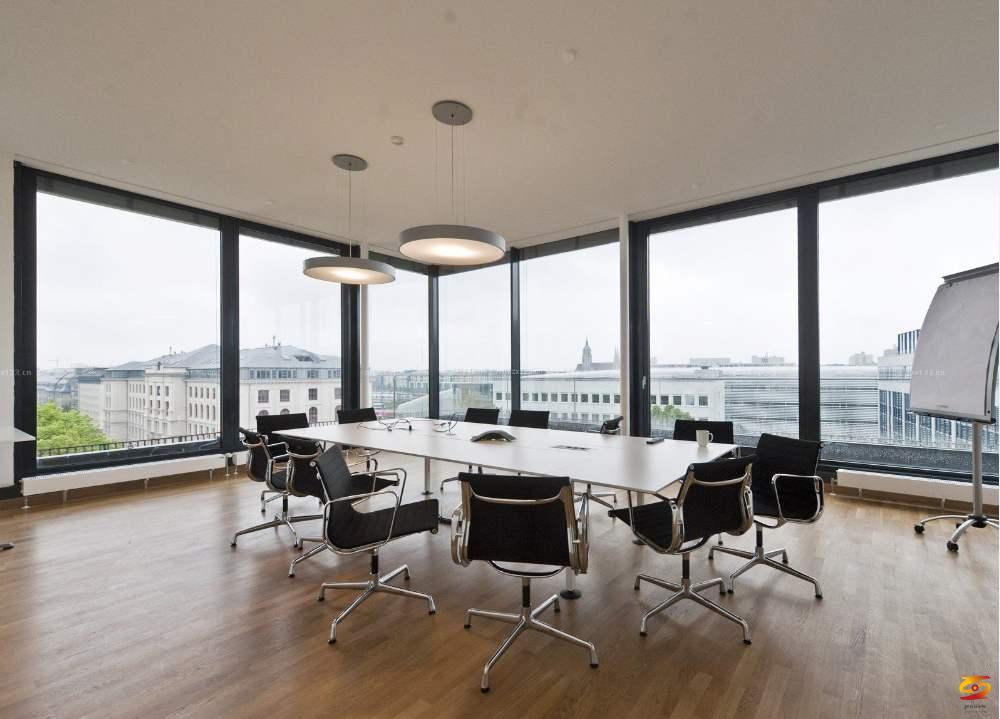
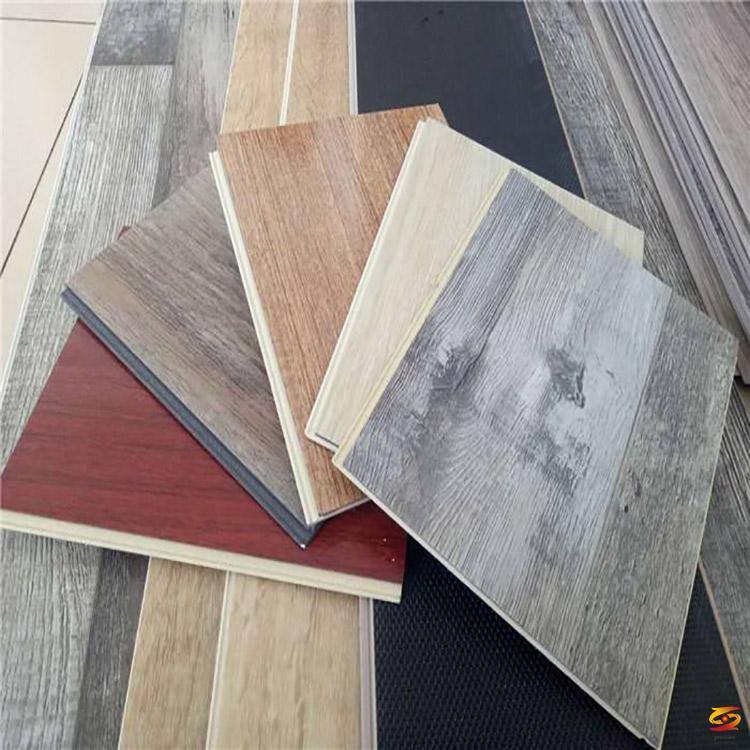
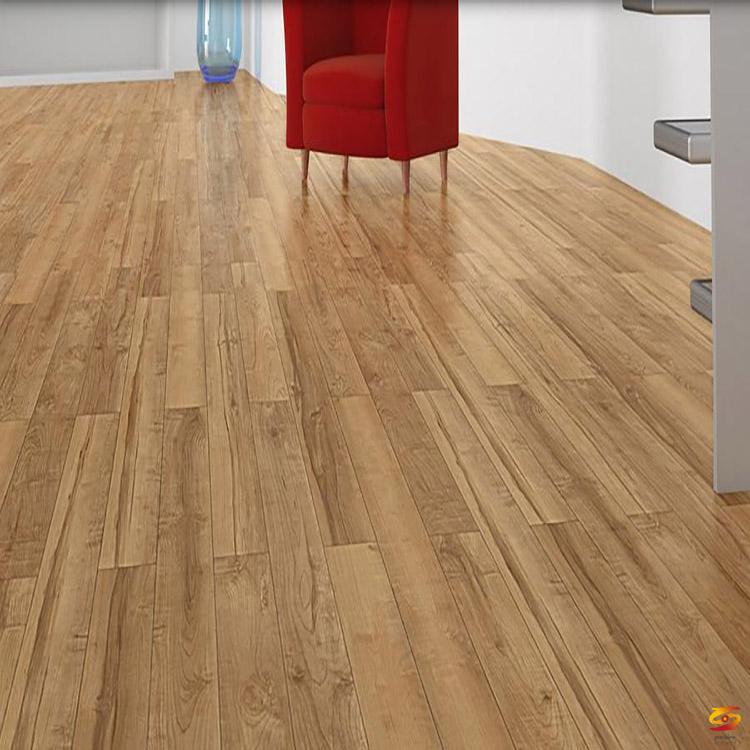